Michela Bon
Head of Controlling Italy at Wittur Group- Claim this Profile
Click to upgrade to our gold package
for the full feature experience.
Topline Score
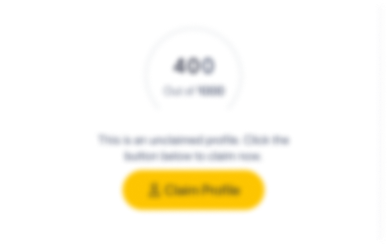
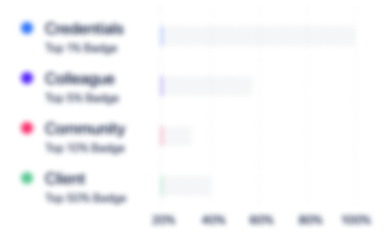
Bio


Experience
-
Wittur Group
-
Germany
-
Industrial Machinery Manufacturing
-
700 & Above Employee
-
Head of Controlling Italy
-
Dec 2020 - Present
Parma, Emilia-Romagna, Italy
-
-
-
CNH Industrial
-
Machinery Manufacturing
-
700 & Above Employee
-
Plant Controller | CNH Industrial - Modena Plant
-
Jul 2018 - Nov 2020
Modena Plant is part of CNH Indutrial and manufactures drivelines and other components for tractors. Number of employees is 1.000 Responsible for Controlling for the plant. 3 direct reports. The role reports to the PT EMEA Manufacturing Controller. Part of the local management team. Main responsibilities: - preparation of plant P/L and reconciliation actual vs budget, and actual vs forecast - supervision of the reporting activities to CNH Industrial - coordination of the… Show more Modena Plant is part of CNH Indutrial and manufactures drivelines and other components for tractors. Number of employees is 1.000 Responsible for Controlling for the plant. 3 direct reports. The role reports to the PT EMEA Manufacturing Controller. Part of the local management team. Main responsibilities: - preparation of plant P/L and reconciliation actual vs budget, and actual vs forecast - supervision of the reporting activities to CNH Industrial - coordination of the budget and forecast processes with all the Departments involved - definition and management of the product standard costs in all his aspects (Material, variable and fixed costs) - management of relationships with Group auditors and external auditors on Controlling topics Cost deployment pillar leader for WCM
-
-
Plant Controller | Iveco Astra - Piacenza Plant
-
Jul 2016 - Jun 2018
Piacenza Area, Italy Iveco Astra is part of CNH Indutrial and manufactures trucks of-road and military vehicles. Number of employees is 300 Responsible for Controlling for the plant. 3 direct reports. The role reported to the Iveco EMEA Manufacturing Controller. Part of the local management team. Main responsibilities: - preparation of plant P/L and reconciliation actual vs budget, and actual vs forecast - supervision of the reporting activities to CNH Industrial - coordination of the budget… Show more Iveco Astra is part of CNH Indutrial and manufactures trucks of-road and military vehicles. Number of employees is 300 Responsible for Controlling for the plant. 3 direct reports. The role reported to the Iveco EMEA Manufacturing Controller. Part of the local management team. Main responsibilities: - preparation of plant P/L and reconciliation actual vs budget, and actual vs forecast - supervision of the reporting activities to CNH Industrial - coordination of the budget and forecast processes with all the Departments involved - definition and management of the product standard costs in all his aspects (Material, variable and fixed costs) - management of relationships with Group auditors and external auditors on Controlling topics Cost deployment pillar leader for WCM
-
-
Controller – Cost deployment Pillar Leader | Iveco - Brescia Plant
-
Nov 2012 - Jun 2016
Brescia Area, Italy From November 2012 to Jun 2016 I worked as Cost deployment Pillar Leader in the IVECO Brescia plant (2.500 employees – production of EUROCARGO trucks – annual pieces 25.000) of Fiat Industrial. My main responsibilities included: - evaluation of the plant losses - elaboration of metodologies to eliminate losses and calcualtion of the expected savings. - preparation of the yearly budget (expected savings) and monthly monitoring of the actions launched - evaluation and control… Show more From November 2012 to Jun 2016 I worked as Cost deployment Pillar Leader in the IVECO Brescia plant (2.500 employees – production of EUROCARGO trucks – annual pieces 25.000) of Fiat Industrial. My main responsibilities included: - evaluation of the plant losses - elaboration of metodologies to eliminate losses and calcualtion of the expected savings. - preparation of the yearly budget (expected savings) and monthly monitoring of the actions launched - evaluation and control of all investments submitted to Group. Verification of payback and related expected savings - reporting activities (actual and budget) on investments - preparation of World Class Manufacturing yearly audits and management of relationships with Group auditors
-
-
-
Medtronic
-
United States
-
Medical Equipment Manufacturing
-
700 & Above Employee
-
Manufacturing Controller | Brescia Plant
-
Apr 2011 - Oct 2012
Brescia Area, Italy From April 2011 to October 2012 I’ve worked as Manufacturing Controller in the Brescia plant of Medtronic Spa (500 employees – production of stents for hearts diseaes – annual sales 70Mil.€). Medtronic is an American multinational company that produces biomedical products. My main responsibilities included: - preparation of monthly reporting (including forecast) submitted to the European headquarter in Ireland. The reporting includes: variances analysis actual vs budget on material,… Show more From April 2011 to October 2012 I’ve worked as Manufacturing Controller in the Brescia plant of Medtronic Spa (500 employees – production of stents for hearts diseaes – annual sales 70Mil.€). Medtronic is an American multinational company that produces biomedical products. My main responsibilities included: - preparation of monthly reporting (including forecast) submitted to the European headquarter in Ireland. The reporting includes: variances analysis actual vs budget on material, labour and fixed cost and analysis of FTE - elaboration of monthly reporting per Cost Center. - calculation of the Product Standard Costs for all the items manufactured in the plant - intercompany profit elimination - monthly analysis of Purchase Price Variances vs budget - monthly analysis of freight costs - support to Finance Manager (on the Manufacturing areas) for the preparation of the annual financial statement US GAAP - preparation of the Annual Budget per cost center of the italian plants (and the related reports submitted to the headquarter). This activity included: 1) cooperation with Cost Center Managers on the definition and verification of the budget; 2) analysis of direct material consumption 3) definition of personnel costs; 4) calculation of budget standard costs In 2011, together with IT department, I’ve carried out the following projects: - implementation of SAP – FINANCE MODULE - creation of the finance data interfaces between AX Microsoft (ERP system used by Italian plants) and SAP Show less
-
-
-
CIAT
-
Industrial Machinery Manufacturing
-
300 - 400 Employee
-
Financial Plant Controller | Verona Plant
-
Nov 2008 - Apr 2011
Verona Area, Italy From November 2008 to April 2011 I’ve worked as Financial Plant Controller in the Pescantina (VR) plant of Ciat Italia (40 employees – production of heat exchanger – distribution of air cooling system machines, annual sales 15Mil.€) The Pescantina site has been taken over by CIAT in 2007. When I’ve started working for CIAT in 2008, there was the need from the headquarter to develop an internal Controlling Department (this activity was in fact previously managed by external… Show more From November 2008 to April 2011 I’ve worked as Financial Plant Controller in the Pescantina (VR) plant of Ciat Italia (40 employees – production of heat exchanger – distribution of air cooling system machines, annual sales 15Mil.€) The Pescantina site has been taken over by CIAT in 2007. When I’ve started working for CIAT in 2008, there was the need from the headquarter to develop an internal Controlling Department (this activity was in fact previously managed by external consultants). My first task was to obtain all the necessary information in order to start managing and validating all the data and the reports submitted to the French headquarter. Afterwards I’ve implemented and executed different projects, in order to align all the internal procedures and financial processes to the headquarter requirements and standards. Main responsibilities covered: - preparation of Profit and Loss account and Balance Sheet for budget, actual and quarterly forecast. For the quarterly forecast I simulated a year-end closing - elaboration of all month end reports related to Sales, Orders, Overdue and all information related to the performance of the plant. - preparation of the monthly report presented to Ciat board. This included the reconciliation actual vs budget (and vs last year) and the causal factor analysis with the explanation of the main variances - stock evaluation weekly, monthly and at year end, with the elaboration of all related reports (i.e. Inventory turnover) - management of rotational stock counts to control the inventories - introduction of production standard times by product. I’ve also carried out the following projects: - introduction of the standard costs by product, according the rules made by the headquarter - implementation of a procedure to calculate the gross margin by product, product line and customer - mapping and creation of the Work Centers to introduce Cost Accounting Show less
-
-
-
Electrolux Group
-
Sweden
-
Manufacturing
-
700 & Above Employee
-
Controller | Firenze Plant
-
Apr 2002 - Nov 2008
Florence Area, Italy Based in the Electrolux Florence Plant (500 employees, production of fridges and freezers). The main responsibilities covered: - preparation of Commercial Profit and Loss account for Florence and Treviso Factories. - preparation of all reports (actual, quarterly and budget) for central administration; preparation of the Operating Profit for Florence Factory including the consolidation of Factory costs, Commercial costs and central allocations; - elaboration of Plant Capital… Show more Based in the Electrolux Florence Plant (500 employees, production of fridges and freezers). The main responsibilities covered: - preparation of Commercial Profit and Loss account for Florence and Treviso Factories. - preparation of all reports (actual, quarterly and budget) for central administration; preparation of the Operating Profit for Florence Factory including the consolidation of Factory costs, Commercial costs and central allocations; - elaboration of Plant Capital Expenditure (actual, quarterly and budget); - calculation of Stock Value Adjustments and involvement in all Supply Chain and Warehousing cost issues. - Monitoring and coordination of Investment Proposals and Job order. - approval of purchase requests; - compounding of factory Assets - calculation of Depreciation From 2005, as a consequence of a job rotation request, the main responsibilities included: - calculation of the Product Standard Costing (fridges and freezers) for all the items manufactured in the plant - calculation of product and purchasing price efficiencies; - elaboration of Cost reduction Project reports for the Florence plant products; presented to and used by Local and Divisional management team, as well as Central R&D - preparation of Factory Information for Florence and Treviso factory (actual, quarterly and budget level). - Preparation of make or buy analysis - Preparation of all reports to be electronically sent to the Group - Implementation of Sarbanes Oxley Law (SOX) for Florence and Treviso factories. Show less
-
-
-
Diners World Travel
-
Singapore
-
Travel Arrangements
-
1 - 100 Employee
-
Marketing Department
-
Oct 1998 - Mar 2002
Florence Area, Italy Based in Diners Travel in the Marketing department the main responsibilities covered: - research of new sectors and customers in order to develop the commercial activity of the office which followed international fairs related to the leather and underwear trades. This role involved visiting international fairs (i.e. Drupa in Dusseldorf, Plast in Milan)
-
-
Education
-
Università degli Studi di Firenze
Law -
Electrolux Home Products
Community
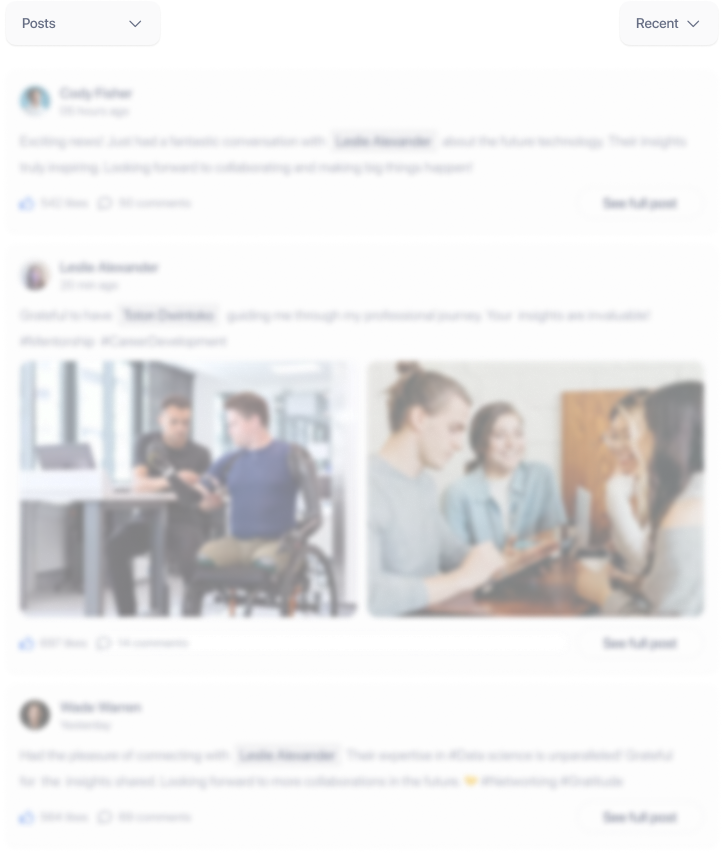