Michel Gour
Building Condition Assessment Engineer and Reserve Fund Planner at Keller Engineering Associates- Claim this Profile
Click to upgrade to our gold package
for the full feature experience.
-
English Full professional proficiency
-
French Full professional proficiency
Topline Score
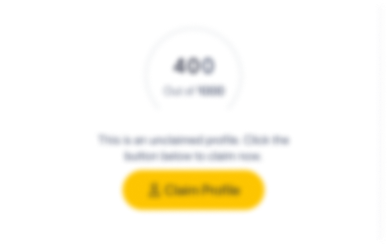
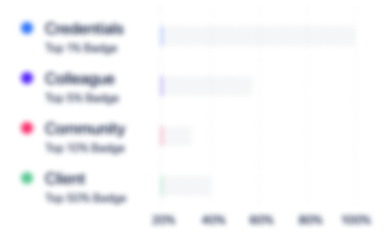
Bio
0
/5.0 / Based on 0 ratingsFilter reviews by:
Credentials
-
Professional Engineer
Professional Engineer of OntarioDec, 2001- Sep, 2024
Experience
-
Keller Engineering Associates
-
Canada
-
Civil Engineering
-
1 - 100 Employee
-
Building Condition Assessment Engineer and Reserve Fund Planner
-
Oct 2022 - Present
Perform reserve fund studies / building condition surveys and prepare reports. Perform property condition assessments and prepare reports. Perform investigations required to diagnose problems related to building systems and recommend repair options. Provide status reporting regarding project milestones, deliverables, dependencies, risks and issues, communications across leadership. Discuss and review engineering products with clients. Participate in team accountability efforts to meet project goals, adhering to their responsibilities and project milestones. Update and modify existing report styles. Coach, mentor, and motivate junior engineers. Develop project strategies with junior engineers prior to project initiation. Review and provide constructive feedback on written draft reports. Show less
-
-
-
-
Facility Condition Assessor/Technical Reviewer
-
Jan 2018 - Oct 2022
Conduct independently Mechanical & Electrical, Roof, Envelope, Structural & Architectural building systems onsite visual assessments, and investigations using various field data collection software tools and tablets. Independently review drawings for quantity take-offs and prepare multi-discipline building condition assessments (BCAs), reserve fund studies, capital planning projects, technical/building audits or other investigative reports complete with observations, conclusions, recommendations and repair budgets. Assist and/or manage field measurements and data collection and preparation of AODA (Accessibility for Ontarians with Disabilities Act) audits complete with observations, conclusions, non-compliances, recommendations, and budgets. Provide technical peer review of reports and feedback to technical staff. Assist and/or manage project activities through to completion, including time allocation and project tracking/scheduling of project deliverables. Assist with the development/improvement of company service delivery processes (i.e. standard reports, standard cost tables, reporting and data collection tools/processes, etc.). Provide French-language translation services for technical reports and proposals. Assist with business development by maintain and developing client relationships, exploring new market opportunities, and promoting/marketing FCAPX services through conferences, proposals, presentations, etc. Show less
-
-
-
VFA
-
Brazil
-
Legal Services
-
1 - 100 Employee
-
Building Condition Assessment Consultant
-
Jan 2014 - Jan 2018
Conducted Building Condition Assessments (BCAs) that included the review of drawings and documents provided by clients, and onsite evaluation of the age and condition of building systems (HVAC/mechanical, electrical/life safety, building envelope/structural and roofing, and service utilities). Reviewed technical reports provided by environmental services consultants for the determination of capital replacement costs of building components that required asbestos abatement activities in the planning and implementation of building demolition/construction projects. Prepared and reviewed Building Condition Assessment (BCA) reports in both English and French that included recommendations and capital replacement cost estimates, using various proprietary software applications to assist clients (school boards, colleges/universities, hospitals/medical centres) with expert capital budget planning of their portfolio. Show less
-
-
-
Stantec
-
Civil Engineering
-
1 - 100 Employee
-
Environmental and Building Condition Assessor
-
Jun 2011 - Jun 2013
Supervised contractors and conducted onsite inspections of enclosed work areas during asbestos abatement projects that included asbestos removal/repair operations, air quality monitoring and asbestos fibre concentrations analysis in conformance with the Ontario Occupational Health & Safety Act and Regulations. Conducted onsite Building Condition Assessments (BCAs) that included the review of drawings and documents provided by clients, onsite evaluation of the age and condition of building systems (HVAC/mechanical, electrical/life safety, building envelope/structural and roofing) for school boards, commercial retailers, financial institutions, and recreational establishments. Reviewed technical reports provided by environmental services consultants for the determination of capital replacement costs of building components that required asbestos abatement activities in the planning and implementation of building demolition/construction projects. Prepared and reviewed technical reports in both English and French for Designated Substances & Hazardous Materials, Asbestos Abatement projects, and Building Condition Assessments. Show less
-
-
-
PWGSC
-
South Africa
-
Construction
-
1 - 100 Employee
-
Environmental Analyst
-
May 2010 - May 2011
Improved the existing national PCB Management Program by reviewing both the PCB Regulations (SOR/2008-273) and the latest Regulations Amending the PCB Regulations (SOR/2010-57), and conducting a non-compliance gap/risk analysis to develop a revised national PCB Management program with a response action plan in compliance with the regulations. Collaborated with Regional PCB Coordinators and the AFD (Alternate Form of Delivery) service provider to update the PCB-containing equipment inventory for all Asset categories within the PWGSC portfolio, and update the PCB Management Program documentation/staff training package pertaining to the regulatory requirements associated with the use, labelling, reporting, and disposal of PCB-containing equipment. Collected and submitted samples of suspect hazardous building materials for laboratory analysis and evaluated the analytical results for the preparation of Designated Substances Reports that included recommendations for worker protection during demolition/construction project activities for various government clients in compliance with the Canada Labour Code and the Occupational Health and Safety Act of the applicable provincial jurisdictions. Assisted with project management activities that included the preparation of Request for Proposals (RFPs), planning and management of budgeting, scheduling, scope, safety review, and procurement for the completion of large-scale Designated Substances/Hazardous Materials (HAZMAT) assessment projects valued at up to $100K through direct interaction with environmental services consultants. Show less
-
-
-
Iogen Corporation
-
Canada
-
Chemical Manufacturing
-
Plant Process Engineer
-
Apr 2007 - Sep 2009
Provided plant engineering and operation support with all aspects of environmental health & safety, industrial plant practices, process monitoring, optimization, and troubleshooting for a 1,000 gallons/day ethanol distillation area, including HAZOP reviews. Created and improved standard operating procedures and troubleshooting user guides to assist plant personnel. Developed and implemented a training program for plant operation staff in the operation and troubleshooting of a continuous ethanol distillation system, which also included the safe handling of ethanol and emergency response procedures. Served as an employee representative on the company’s joint health & safety committee and provided technical support to the plant’s emergency response team in the safe handling and mitigation of environmental releases resulting from accidental spills. Provided weekly and monthly unit operation reports to management that included mass & energy balances, ethanol product quality, and overall distillation area performance. Managed the development, procurement and implementation of continuous process improvement projects to improve plant reliability and productivity in collaboration with various cross-functional groups of the plant and outside contractors. Collaborated with management and the engineering and maintenance departments on the development of a preventative maintenance program for the distillation area of the plant. Show less
-
-
-
Radient Technologies Inc.
-
Canada
-
Biotechnology Research
-
1 - 100 Employee
-
Pilot Plant Engineer
-
Jan 2001 - Apr 2007
Assisted with the project development, scheduling, procurement, and implementation associated with the pilot plant commissioning activities. Conducted the planning, initial equipment set-up & calibration, and completion of laboratory and pilot-scale testing for the purification of pharmaceutical ingredients and other naturally-derived additives by chemical extraction of different feedstock in support of greenhouse gas emissions reduction initiatives. Developed and implemented a training program for pilot plant personnel in the safe operation and troubleshooting of a batch processing facility. Developed, procured and implemented continuous improvement projects which included the selection, installation, and commissioning of pilot plant equipment. Served as the company’s health & safety employee representative, responsible for the safety orientation of new employees, monthly health & safety inspections, and to ensure pilot plant activities conform to the company’s policies and procedures on health & safety. Responsible for all hazardous waste management activities that included the online registry, handling and disposal of hazardous wastes through the Hazardous Waste Information Network (HWIN) with the Ontario Ministry of the Environment. Created and implemented a preventative maintenance program for the pilot plant facility. Prepared weekly progress reports and delivered oral presentations to senior management and partners. Show less
-
-
-
-
Sales Applications / Project Engineer
-
Aug 1998 - Jan 2001
Supported business development by soliciting potential clients through cold calling and courtesy plant visits. Completed cost analysis and feasibility studies of corrosion protection systems along with detailed engineering proposals and quotations for prospective clients. Designed, commissioned, and conducted onsite inspections of electrochemical corrosion protection systems for over 20 pulp & paper and mining clients throughout North America. Provided onsite training and technical support to plant personnel on the operation and maintenance of corrosion protection systems valued up to $100K. Delivered after-sale customer service and technical support with the implementation of corrective actions to resolve any system malfunctions. Show less
-
-
-
Multipak Ltd
-
Packaging and Containers Manufacturing
-
1 - 100 Employee
-
Quality Assurance Laboratory Technician
-
Apr 1994 - Aug 1998
Responsible for the approval of preliminary printed specimen samples generated by flexographic printing press operators to ensure that quality conformance standards are fully met. Assisted with troubleshooting of both printing and adhesive/extruding lamination plant processes. Conducted quality assurance tests of both printed and laminated web samples (bond & heat seal strength, slip coefficient, residual solvent & basis weight determination, repeat length consistency). Prepared certificates of analysis of final products for clients. Show less
-
-
-
-
Research Assistant / Technologist
-
May 1985 - Feb 1994
Responsible for the daily operation of up to eight (8) hydrotreating/hydrocracking pilot plant units, with throughputs ranging from 10 g/hr to 1,500 g/hr, which included start-ups, shutdowns, solvent flushing, catalyst preparation, unit monitoring and troubleshooting, and optimization of process control variables. Completed daily operation summary logs and conducted mass balance test runs to evaluate unit performance and product quality. Completed bench-scale batch distillations of in-house refinery intermediate oil samples from the pilot plants and other departments of the research facility. Conducted crude oil assay distillations of external samples by established ASTM methods to quantify boiling range fractions. Show less
-
-
Education
-
University of Toronto School of Continuing Studies
Building Science Practice Certificate, Architectural and Building Sciences/Technology -
Ryerson University
Bachelor of Engineering (B.Eng.), Chemical Engineering -
Ryerson University
Diploma, Chemical Engineering Technology/Technician
Community
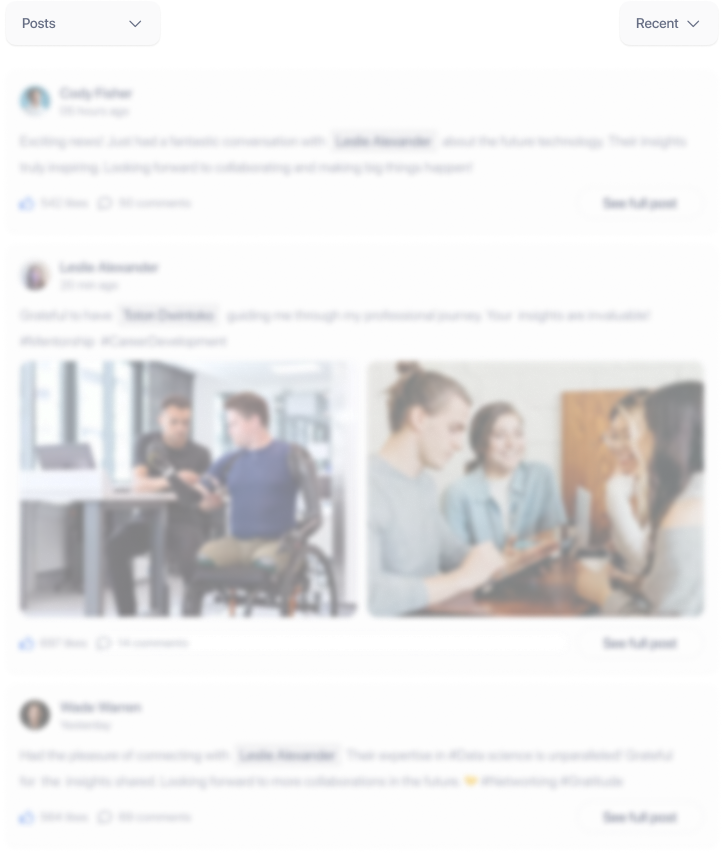