Michal Kulczynski
Supply Chain Director at ecowipes- Claim this Profile
Click to upgrade to our gold package
for the full feature experience.
-
English -
Topline Score
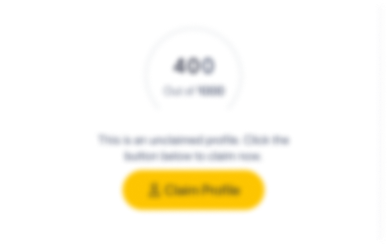
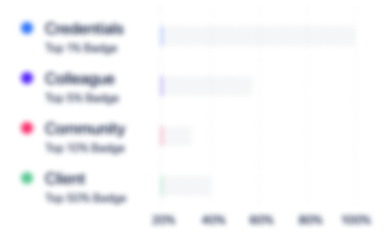
Bio


Experience
-
ecowipes
-
Poland
-
Manufacturing
-
1 - 100 Employee
-
Supply Chain Director
-
Jun 2020 - Present
Strategically plan and manage planning, warehouse, purchasing, transportation and customer services. Liaise and negotiate with suppliers and partners. Keeping track of quality, quantity, stock levels, delivery times, transport costs and efficiency. Management and improvement of processes related to logistics and warehousing of goods. Maintain metrics and analyze data to assess performance and implement improvements. Implementation of the company's personnel policy in the logistics department, including motivating, accounting for subordinate employees, training and supervising their development in terms of logistics skills. Comply with laws, regulations and ISO requirements. Show less
-
-
-
Procter & Gamble
-
United States
-
Manufacturing
-
700 & Above Employee
-
Planning Manager
-
Nov 2018 - Jun 2020
-
-
Project Coordinator
-
Jan 2017 - Nov 2018
Member of Project team coordinating transition of Planning Processes, supporting new system setup.• Manage transitions with 0 business impact and minimal cost. • Provide timely project status updates to the Leadership. • Identify and work to remove barriers to successful completion of the overall project, with particular emphasis on resolving issues with subcontractors. • Plan and facilitate project review meetings to expedite requirements and resolution of project issues. • Guide the team on resource requirements, methodologies, tasks, dependencies, deliverables, risks, and other issues through the life of the project. • Create business process and procedures to ensure compliance with the business processes. • Develop and deliver role-based process and system training. Show less
-
-
Site Integrated Planner
-
Apr 2012 - Dec 2016
Enforced, coordinated and guided production management and manufacturing personnel in detailed production planning and scheduling. Worked with Operations and Manufacturing management to ensure that products were produced efficiently according to internal procedures at lowest cost, of requisite quality and on time.• Responsible for scheduling three production departments with a total of 50 machines in a 24/7 operation.• Implemented daily production schedules for all work centers.• Worked with plant to overcome temporary bottlenecks in plant throughput caused by machine, tool and labor issues.• Developed weekly production plans. Also, responsible for managing inventory and meeting service objectives for those products.• Ability to prioritize conflicting tasks and make timely decisions, as well as identifying critical supply constrains and developing action plans to avoid service impacts. Show less
-
-
Business Process Owner
-
Jul 2009 - Mar 2012
• Performed ad hoc deep dive analyses for specific business problems.• Developed business cases, presentations, and reports for senior management.• Developed and implemented various improvement plans (management of partial pallets and product shelf time in warehouse, improved the tool for efficient container utilization resulting increased Vehicle Fill Rate, introduced setup process for new product eliminating business disruption, daily management system for proactive issue resolution) • Designed and implemented monthly metrics, tracking and data collection tools resulting in improved productivity • Improved profitability by 10% -15% by significantly reducing the full-time employee (FTE) hours by maximizing the efficiency of WMS and gaps elimination in day to day operation (Improved layout of warehouse considering product segmentation, Stackablity factor for FG, setup secondary WMS system to control inventory for rented space)• Managed 2 direct reports Show less
-
-
SAP (WM, SD) & WMS Key User
-
Mar 2006 - Jun 2009
SAP Support Specialists provided functional support with the SAP product to help resolve users' issues, developed system and processes:• Developed SAP knowledge and capability in others, shares knowledge, skills and experienceto raise SAP competence level,• Assisted in the implementation of new SAP ERP system• Performed systems processes analyses• Providing SAP process improvement recommendations in the IM/WM area, and creating post launch support plans (setup process for external WH, developed return process for obsoletes from Markets, Implemented Claim process of over/underdelivery)• Able to learn and implement new skills within a short period of time.• Ability to handle stressful situations and unexpected errors in a calm and efficient manner• Perform testing in the UAT Environment • Coordinate and participate in the test status meetings, Defect Triage and program level meetings with development and test (Direct Plant Shipments) Show less
-
-
Inventory Analyst
-
Oct 2005 - Feb 2006
Established effective communication with 3PL's. Aggressively collaborated with internal/external contacts to assure timely and accurate reporting of inventory activities. Implemented standardized data flow to facilitate inventory reconciliations process. Performed daily inventory reconciliations for finished goods. Coordinated and performed cycle and annual physical inventory counts. Work with cross-functional departments to assure a high level of inventory integrity and customer service.• Processed daily activities in SAP. Reviewed and resolved daily EDI exceptions for inventory transactions. • Responsible for researching discrepancies between inventory reports for over 1,500 items . • Processed adjustments to inventory warehouse. • Problem solved and analyzed inventory reports and numbers• Prepared reports, such as inventory balance, price lists and shortages Show less
-
-
Education
-
University of Life Science in Lublin
BS, Production Engineering -
Technical University of Lodz
Postgraduate Diploma, Logistics management -
Kozminski University
Executive MBA
Community
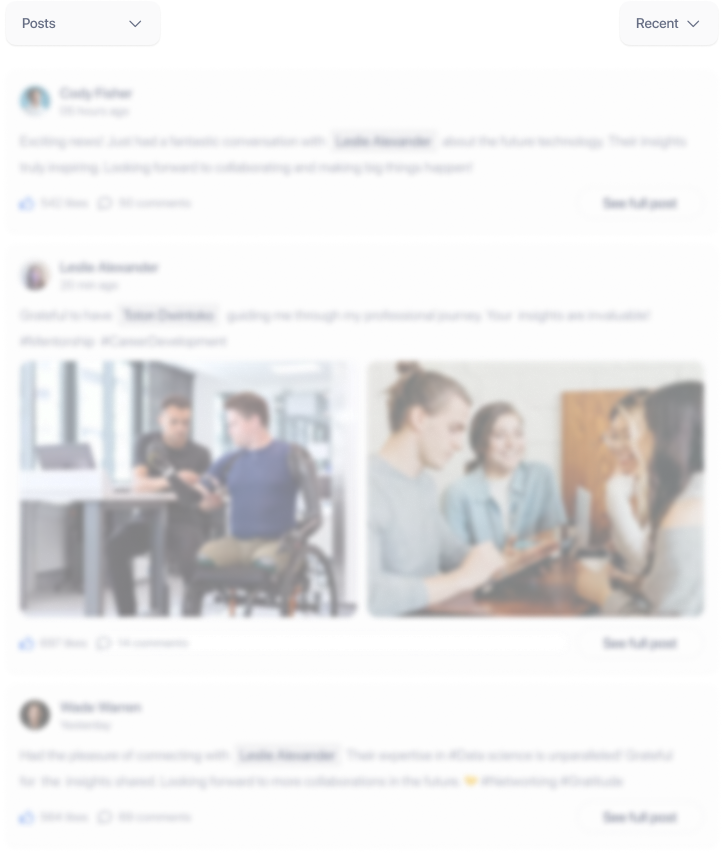