Michael Rayburn
Materials Manager at Bryan Electric, Inc.- Claim this Profile
Click to upgrade to our gold package
for the full feature experience.
Topline Score
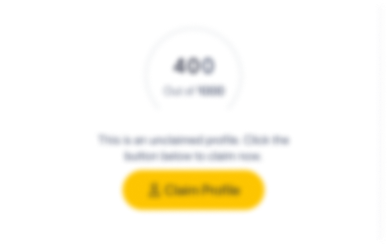
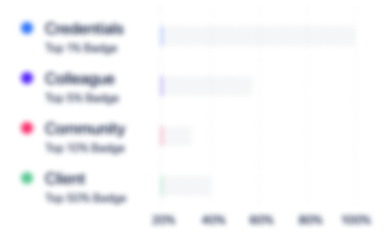
Bio


Experience
-
Bryan Electric, Inc.
-
Appliances, Electrical, and Electronics Manufacturing
-
1 - 100 Employee
-
Materials Manager
-
May 2021 - Present
Denver, Colorado, United States Tracking material shipments & addressing logistics issues w/vendors & carriers. Worked closely w/purchasing team, leveraging power of commodities & materials in outlining trade & distribution agreements. Track KPI's for project materials Negotiated pricing & terms w/vendors to secure best value for company. Cultivated strong relationships w/vendors to maintain & improve levels of customer service. Maintained material control & information systems, supporting manufacturing &… Show more Tracking material shipments & addressing logistics issues w/vendors & carriers. Worked closely w/purchasing team, leveraging power of commodities & materials in outlining trade & distribution agreements. Track KPI's for project materials Negotiated pricing & terms w/vendors to secure best value for company. Cultivated strong relationships w/vendors to maintain & improve levels of customer service. Maintained material control & information systems, supporting manufacturing & balancing inventory surpluses w/customer demand. Monitored safety stock levels & established order policies to balance inventory availability w/minimal investment. Managed direct reports & gave directives, drafted schedules & comprehensively evaluated performance. Coordinating w/project managers & contractors to determine the specific material requirements for each project. Communicated regularly w/suppliers to uphold accountability for quality standards & timely delivery of goods. Reviewed & approved purchase orders & invoices for accuracy and completeness. Generated reports on purchasing activities to support management decisions. Scrutinized purchasing data to identify areas for improvement & cost savings. Analyzed market & delivery systems to assess present & future materials availability. Reduced costs by streamlining contract bidding & procurement processes to assure best prices for materials and services. Developed & tracked metrics to measure supplier performance & cost savings. Developing & implementing strategies to optimize material usage and minimize waste. Implemented requisition forms & email templates to create accountability for workers requesting project materials. Maintaining accurate records of all material transactions, including receipt, storage, & issuance. Monitoring inventory levels & forecasting material needs for upcoming projects. Conducting regular audits of inventory to identify any discrepancies or potential issues. Created & kept inventory spreadsheets. Show less
-
-
-
-
Warehouse/Fleet Manager
-
Sep 2019 - Aug 2020
Denver, Colorado, United States Work w/Project Managers at the start of all projects to do a material & equipment takeoff Create orders for project materials & work w/vendors to ensure they are received as needed at the project without delay Manage & distribute shipments & materials to projects as needed maintaining tracking and contact w/vendors to ensure there were no delays. Hauling equipment to & from project locations Picking up orders at supply hours & dropping them off to job locations Manage inventory… Show more Work w/Project Managers at the start of all projects to do a material & equipment takeoff Create orders for project materials & work w/vendors to ensure they are received as needed at the project without delay Manage & distribute shipments & materials to projects as needed maintaining tracking and contact w/vendors to ensure there were no delays. Hauling equipment to & from project locations Picking up orders at supply hours & dropping them off to job locations Manage inventory levels in the warehouse Support project personnel w/equipment damage claims & RTV processes for vendor returns. Communicate with project management team to ensure a proactive approach to material, equipment delivery schedule & delays In constant communication w/project managers & superintendents to continuously monitor material & equipment needs at each project Oversees inventory at multiple projects at any given time Constantly looking for ways to reduce waste & increase productivity in both the warehouse & fleet management departments Implement LEAN initiates into daily work practices to increase productivity & reduce waste Run weekly reports to manage fuel card & toll road usage. Manage vehicle service schedule & coordinated w/techs & dispatch to schedule time for vehicle service as well as setting a threshold of what the vehicle maintenance vendors could do w/o prior approval. Act as the main point of contact for anything vehicle related for company employees, fleet management company & vendors Make sure that vehicle information is up-to-date for fleet management & created Excel spreadsheet to track all fleet vehicles important information like VIN, registration, & most recent vehicle maintenance (oil change, etc.) & mileage. Install GPS units on new vehicles, track techs going outside of work areas & any tracking and driving irregularities (speeding, hard braking, etc.) Approve all vehicle related expenses Build out, order and approve new vehicles for employees as needed Show less
-
-
-
Blattner Energy
-
United States
-
Construction
-
700 & Above Employee
-
Material Control Specialist (Contract)
-
Jan 2019 - Jul 2019
Avon, Minnesota, United States Manage the materials for $65M solar farm Manage the delivery of $100M of owner supplied solar panels Oversee an offload crew for shipping and receiving all materials Work closely with Superintendents and offload crew to ensure that all materials were staged in specific work zones to optimize productivity and eliminate time waste. Receive all shipments from the BOL and cross reference for proper counts Create a tracking system to ensure suppliers are delivering materials in… Show more Manage the materials for $65M solar farm Manage the delivery of $100M of owner supplied solar panels Oversee an offload crew for shipping and receiving all materials Work closely with Superintendents and offload crew to ensure that all materials were staged in specific work zones to optimize productivity and eliminate time waste. Receive all shipments from the BOL and cross reference for proper counts Create a tracking system to ensure suppliers are delivering materials in accordance with contract requirements Attend weekly three-week look ahead meetings with Project Manager, Site Manager and Superintendents to forecast what materials were needed for the coming weeks and to update them on any delays on materials so they could adjust the project timeline if necessary. Send daily reports to Superintendents on that day's deliver counts. Coordinate with all trades on the job site to ensure that all materials are allocated to the correct locations Work with suppliers to assure that all materials are being delivered on time and if there are delays to report them to the relevant supervisors in a timely manner Work with third party shipping companies who deliver materials to the job site Oversee offload crew in the field and work with offload foreman to make sure that daily material deliveries are being received during their scheduled time with maximum efficiency. Act as a liaison between the job site, corporate office, materials suppliers and project owners Trained in LEAN Initiatives Adopt and implement LEAN training techniques into day to day operations Trained C.A.T.S observer - C.A.T.S. was a Blattner created program designed to ensure every person on the job site was working safely and efficiently.
-
-
Material Manager - Electrical (Contract)
-
Jul 2018 - Dec 2018
Avon, Minnesota, United States Oversee the receiving of all electrical materials Check all BOL's for accuracy and proper counts and take account of any discrepancies or damage. Build requisitions for the different electrical crews and bring them out to each crew Oversaw a crew of people in the material yard, assigned daily projects so that time was maximized. Main point of contact for any material issues Receive material deliveries, count in material and report counts to superintendents with accuracy. Keep… Show more Oversee the receiving of all electrical materials Check all BOL's for accuracy and proper counts and take account of any discrepancies or damage. Build requisitions for the different electrical crews and bring them out to each crew Oversaw a crew of people in the material yard, assigned daily projects so that time was maximized. Main point of contact for any material issues Receive material deliveries, count in material and report counts to superintendents with accuracy. Keep superintendents up to date on inventory counts by sending Excel spreadsheets daily of all accounted materials for that day. Build out tool and material kits and deliver to crews on job site, implemented process to hold crews accountable to returning tools daily and in good condition to prevent waste. Offload trucks when needed Tool logging Notify superintendents when more tools are need as crew sizes increase by keeping an inventory of on hand tools and PPE. Account for material going out throughout the day. At the end of each day walk crew areas to make sure assets or materials are not being left behind and were collected and inventoried. Work with MCS on orders coming in and get all packing slips to her daily Maintain connexes and organized so that materials are quickly and easily accessible and inventory counts are streamlined. Keep the yard clean and orderly, free of debris and safety hazards.
-
-
-
Tile Design
-
United Kingdom
-
1 - 100 Employee
-
Residential Renovation Project Manager
-
Dec 2012 - Jul 2019
Littleton, Colorado, United States Project Planning: Developing a comprehensive project plan, including timelines, budgets, and resource allocation. Budgeting and Cost Management: Creating and managing the project budget, ensuring expenditures are within the allocated budget and making necessary adjustments as needed. Resource Management: Procuring and managing resources, such as manpower, equipment, and materials, required for the project. Vendor and Subcontractor Management: Sourcing, selecting, and managing vendors… Show more Project Planning: Developing a comprehensive project plan, including timelines, budgets, and resource allocation. Budgeting and Cost Management: Creating and managing the project budget, ensuring expenditures are within the allocated budget and making necessary adjustments as needed. Resource Management: Procuring and managing resources, such as manpower, equipment, and materials, required for the project. Vendor and Subcontractor Management: Sourcing, selecting, and managing vendors and subcontractors for various construction tasks, including plumbing, electrical, painting, and carpentry. Scheduling and Timeline Management: Creating and maintaining project schedules, ensuring that tasks are completed on time, and coordinating with different trades to avoid delays. Quality Control: Ensuring that construction work meets quality standards and adheres to building codes and regulations. Risk Management: Identifying potential risks and developing strategies to mitigate them, ensuring the safety of workers and minimizing the impact on the project timeline and budget. Client Communication: Regularly updating clients on the progress of the project, addressing any concerns or issues, and obtaining their approval for design changes or additional work. Team Leadership: Supervising and coordinating the work of project team members, including architects, engineers, designers, and construction workers, to ensure effective collaboration. Documentation and Reporting: Maintaining accurate project documentation, such as contracts, permits, change orders, and progress reports, for record-keeping and reporting purposes. Quality Assurance: Conducting regular inspections to ensure that work is progressing according to plans and specifications, and taking corrective actions as necessary. Completion and Handover: Overseeing the final stages of the project, ensuring all finishing touches are completed, coordinating inspections, and managing the handover process to the client. Show less
-
-
-
The Home Depot
-
United States
-
Retail
-
700 & Above Employee
-
Flooring Supervisor
-
Apr 2016 - May 2018
Aurora, Colorado, United States Managed department of 5 associates Managed inventory and appearance of entire tile department Assisted clients in tile selection and design Managed redesign of displays and layout of product Measure and cut blinds for customers Trained staff members on proper use of tools and equipment used during flooring installations. Engaged in sales, inventory-taking, reconciling cash receipts, and in performing services for customers. Implemented cost-saving strategies to maximize… Show more Managed department of 5 associates Managed inventory and appearance of entire tile department Assisted clients in tile selection and design Managed redesign of displays and layout of product Measure and cut blinds for customers Trained staff members on proper use of tools and equipment used during flooring installations. Engaged in sales, inventory-taking, reconciling cash receipts, and in performing services for customers. Implemented cost-saving strategies to maximize profits while minimizing expenses related to labor, materials, and equipment rental costs. Established clear performance goals for workers in order to motivate them towards maximum productivity. Prioritized tasks according to importance in order to meet tight deadlines without compromising quality standards. Monitored inventory levels of necessary tools, hardware, and flooring materials in order to maintain adequate stock levels at all times. Show less
-
-
-
Floor & Decor
-
Australia
-
1 - 100 Employee
-
Warehouse Manager
-
Apr 2012 - Mar 2016
Highlands Ranch, Colorado, United States Oversaw warehouse team of 10-12 employees Managed warehouse inventory and customer orders Managed order selection for store, tracked inventory sales and made recommendations to store manager to make adjustments based on popular products sales and to decrease inventory for products that were not selling in our market. Organized and received inventory trucks and shipments Communicated with shipping and trucking companies to schedule and reschedule deliveries Identified and… Show more Oversaw warehouse team of 10-12 employees Managed warehouse inventory and customer orders Managed order selection for store, tracked inventory sales and made recommendations to store manager to make adjustments based on popular products sales and to decrease inventory for products that were not selling in our market. Organized and received inventory trucks and shipments Communicated with shipping and trucking companies to schedule and reschedule deliveries Identified and accounted for missing or damaged inventory Created a tracking system to keep track of inventory and account for missing and damaged material Maintained safe and orderly work environment Tracked inventory sales and made recommendations to store manager to make adjustments based on popular products sales and to decrease inventory for products that are not selling Trained employees on forklift Managed restocking of inventory throughout the store Completed all necessary paperwork and reported inventory receipts nightly. Hiring and onboarding, training and managing of new store personnel Worked with corporate leadership to create guidelines for onboarding new personnel Show less
-
-
-
Tareni, Inc
-
United States
-
Store Supervisor
-
Nov 2011 - Mar 2012
Littleton, Colorado, United States Managed the day to day operations of 1 – 3 Shell gas stations. Managed inventory of convenience store and managed ordering. Maintained the interior and exterior of the stores Stocked shelves, cashiered as needed Submitted reporting to Suncor Scheduled all trucks and oversaw gasoline delivery.
-
-
-
Frontier Airlines
-
United States
-
Airlines and Aviation
-
700 & Above Employee
-
Ramp Agent
-
Sep 2008 - Sep 2010
Denver, Colorado, United States Loaded luggage and all other cargo onto commercial airplanes using various pieces of equipment such as baggage carts and conveyors. Manage baggage for flight changes to ensure it made it to its final destination. Worked varying shifts in all weather conditions. Able to manage the physical demands easily. Extreme awareness and caution of surroundings due to the various types of equipment being used and the necessity to maintain safety of self and others at all times.
-
-
Education
-
Southern New Hampshire University
Bachelor's degree, Construction Management -
STRASBURG HIGH SCHOOL
High School Diploma
Community
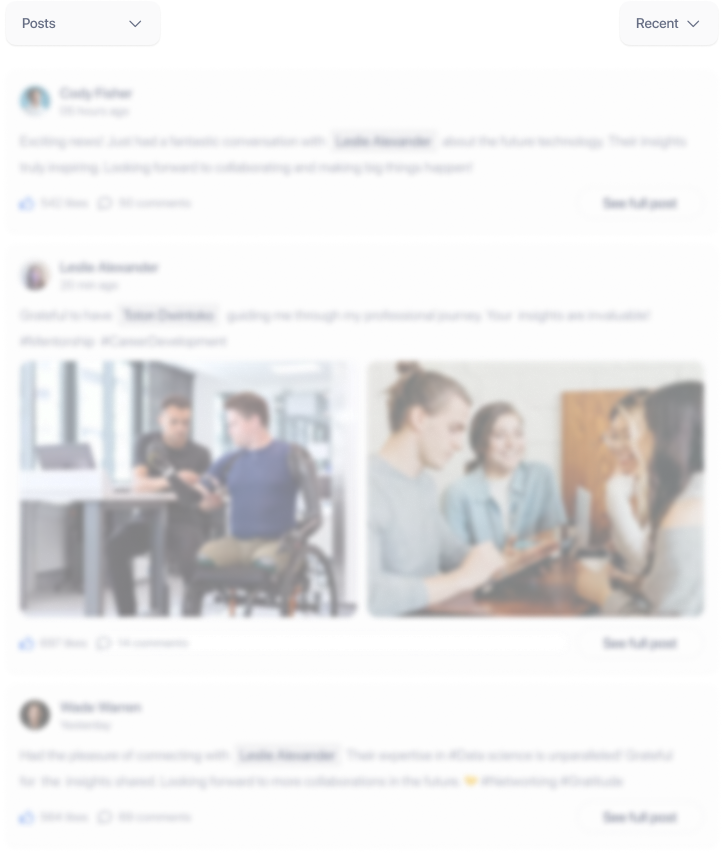