Michael Parsey
Vice President Process Engineering, Automation & Design at Shambaugh & Son, L.P.- Claim this Profile
Click to upgrade to our gold package
for the full feature experience.
Topline Score
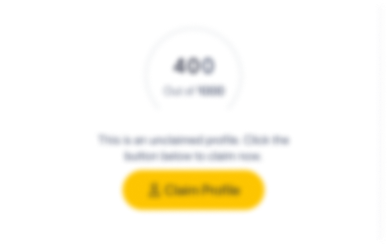
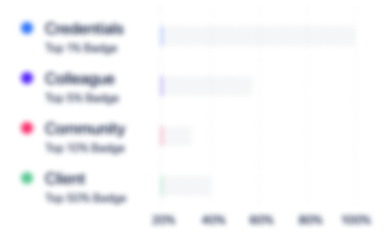
Bio


Experience
-
Shambaugh & Son, L.P.
-
United States
-
Construction
-
500 - 600 Employee
-
Vice President Process Engineering, Automation & Design
-
Jan 2018 - Present
Provide leadership and direction to over 50 engineers and designers. Specifically oversee: Design Operations which includes 3D plant modeling, BIM development and fabrication drawing creation for shop fabrication. Automation Engineering - PLC HMI automation engineering programming, electrical panel design, sales and marketing Process Engineering - Food process engineering design activities, plant design from mass balance / block flow through P&ID's, plan view layouts / 3d modeling to construction and start up.. Leadership and direction includes: technical peer reviews of plant / system designs, manufacturing plant block flow diagram conception, manufacturing plant mass and utility balance creation, equipment plan view drawing development, generation of P&ID drawings, design build project estimating for engineering and construction services, company sales and marketing with client presentations and trade show attendance, new client development and client sales proposal and estimation creation, employee group development and improvement activities, and employee mentoring.
-
-
Vice President Process Engineering & Design
-
Oct 2015 - Jan 2018
-
-
Food Process Engineering Manager
-
May 2007 - Oct 2015
Responsible for project capital budget development, project detailed estimate review, process engineering standards development, peer review of process designs, customer marketing presentations, assigning engineering project work, professional recruiting for the group, and peer development.Accomplishments:• Developed formal process design peer review process for conceptual and final design criteria.• Created standard process and instrument diagram symbols and drawing methods.• Implemented consistent design basis criteria for large scale project designs to better define project criteria to clients; mass balance, process block flow, utility balance, water usage balance and process scope narrative • Created standard equipment tagging matrix for process flow sheets.• Performed bi annual performance and wage reviews for processing engineering staff including, performance improvement suggestions and wage adjustment recommendations• Recruited eight new process engineers, doubling the engineering staff size• Working department manager o Engineering project management, lead process design, detailed plant utility consumption requirements, daily water use and waste water discharge volume needs, process cost analysis and budgeting – 14 month project duration - $40 Million Milk Condensing Plant in Michigan o Produced mass balance and production time line requirements, process design evaluation, detailed plant utility consumption requirements, daily water use and waste water discharge volume needs, process improvement cost analysis and budgeting, – 12 month project duration - $30 Million Yogurt Process Plant in Vermont. o Engineering project management, process design, equipment sizing and specification, process improvement cost analysis and budgeting, – 14 month project duration - $62 Million Milk Evaporation and Drying Process Plant Capacity Expansion in Michigan. o Developed numerous capital budgets for greenfield process facilities for capital planning
-
-
Sr. Food Process Engineer
-
May 2000 - May 2007
Process system designs that include the following: Evaporation (steam and mechanical vapor recompression), spray drying systems, bulk powder handling systems, HTST systems (dairy and food),CIP systems, ultrafiltration, nano-filtration, reverse osmosis, process tank farms, liquid/powder blend systems, refrigeration equipment, batching systems, clarifiers, separators, and decanters. Food and dairy process system designs for domestic markets.Accomplishments:• Existing plant capacity and process evaluation, process design, equipment specification, process improvement cost analysis and budgeting, site installation management, start-up and operator training– 9 month project duration - $14 Million Renovated Mozzarella Cheese Plant in Wisconsin.• Lead process design, site installation management, and start-up of two milk HTST systems – 6 month project duration - $1.5 Million Fluid Milk Plant in Indiana.• Existing plant capacity and process evaluation, process design, equipment sizing and specification, process improvement cost analysis and budgeting, site installation management, start-up and operator training – 9 month project duration - $20 Million Renovated Ice Cream Plant in Arizona.• Existing plant capacity and process evaluation, process design, equipment sizing and specification, process improvement cost analysis and budgeting, overall project management and start-up – 10 month project duration - $12 Million Renovated Ricotta Cheese Plant in Wisconsin.• Engineering project management, existing plant capacity and process evaluation, process design, equipment sizing and specification, process improvement cost analysis and budgeting – 9 month project duration - $32 Million MPC/Milk Powder Process Expansion in New Mexico.• Site installation management, start-up and operator training of egg pasteurization system – 2 month project duration - $1.0 Million Egg Processing Plant Expansion in Indiana.
-
-
-
Waukesha Cherry-Burrell
-
Louisville, Kentucky Area
-
Applications Engineer
-
Nov 1997 - May 2000
Aseptic and ESL process systems, aseptic surge vessels, hot fill systems and standard pasteurizing systems for sanitary applications. Waukesha Cherry-Burrell Votators and Votator II scraped surface heat exchangers, corrugated tubular heat exchangers, plate heat exchangers, positive displacement pumps, centrifugal pumps, and sanitary valves. Food and dairy process system designs for domestic and international markets. Applications Engineer Accomplishments: • Self trained in the design/application of all heat exchange lines offer by Waukesha Cherry-Burrell. • Created standard technical filing database for customer product tests for equipment specifications. • Designed/Implemented standard technical budget processing standards for various core applications. • Able to individually create complete processing system proposals, including equipment sizing, pricing, documentation and flow schematic preparation.
-
-
-
Ionics / SeparaTech
-
St. Paul, MN
-
Project Engineer
-
Feb 1996 - Oct 1997
Ultrafiltration, nano-filtration and reverse osmosis system designs for sanitary and industrial filtration applications. Sized and specified variety of sanitary pump manufacturers for high and low pressure applications (Standard and European). Sized and specified a variety of sanitary valves. Food and dairy process system designs for domestic and international markets. Project Engineer Accomplishments: • Design/Installation and Start-up of $1.4 Million Whey processing plant in California. • Involved in evaluation of existing filtration designs for build cost improvements. • Successful start-up of (7) separate membrane systems. • Design of $1.0 Million Milk Whey processing plant in Southern California.
-
-
-
APV Crepaco
-
Rosemont, IL
-
Project Engineer
-
Dec 1993 - Feb 1996
Process system designs that include the following: CIP systems, rotary drum filters (sanitary and industrial), acid preparation equipment, ultrafiltration, nano-filtration, reverse osmosis, process tank farms, dematiaceous earth filters, press filters, gas fired dryer, recirculated air belt dryer, 2-effect evaporator, pasteurizers, liquid/powder blend system, refrigeration equipment, clarifiers, separators, and decanters. Food and dairy process system designs for domestic markets. Project Engineer Accomplishments: • Design, installation and start-up of $14 Million Gelatin processing plant. • Designed, installed, and started-up Sake pasteurization process. ($500,000) • Installed raw milk receiving bay, including two silos. ($350,000) • Involved in the preparation of process design PID’s for three separate ice cream plants. • Created mechanical and sanitary bid specifications for (3) green field processing plants.
-
-
-
International Paper
-
United States
-
Paper and Forest Product Manufacturing
-
700 & Above Employee
-
Plant Engineer
-
Jul 1992 - Dec 1993
Industrial Hygiene coordinator, plant safety coordinator, environmental compliance coordinator, maintenance manager, shift supervisor, capital equipment specification and procurement corrugating equipment. Corrugated box industry Plant Engineer Accomplishments: • Installed $2.5 Million in production capital improvements. • Implemented Lockout/Tagout plan for plant operators. • Involved in the creation of SOP’s (Standard Operating Procedures) for converting operations. • Managed installation and start-up of computerized production reporting system in numerous IP plants.
-
-
Education
-
Michigan State University
Engineering
Community
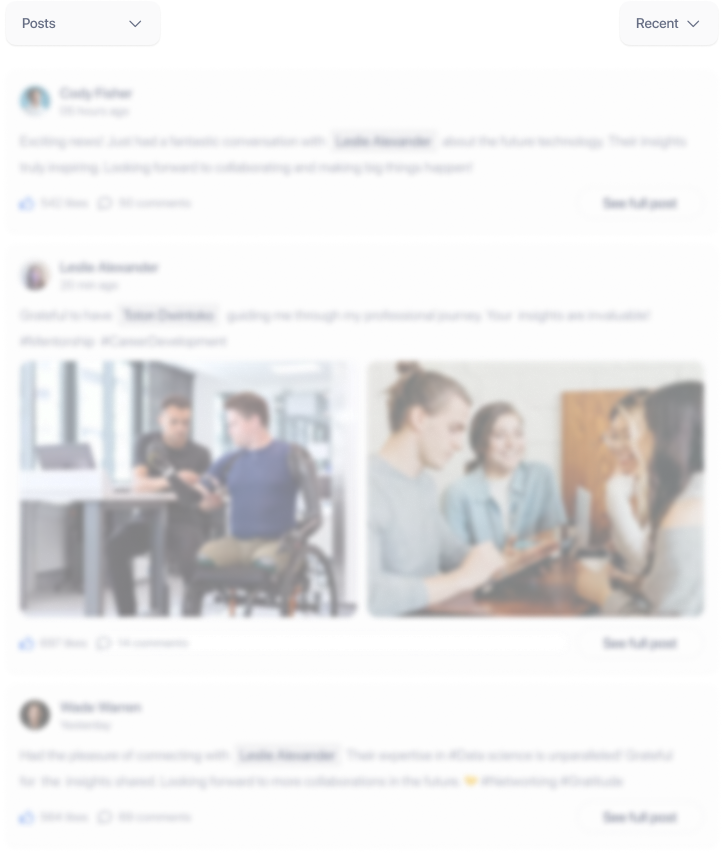