Michael Olson
Expeditor/ Cost Estimator/Continuous Improvement Officer at ECS- Claim this Profile
Click to upgrade to our gold package
for the full feature experience.
-
English Native or bilingual proficiency
Topline Score
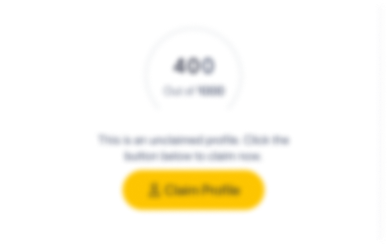
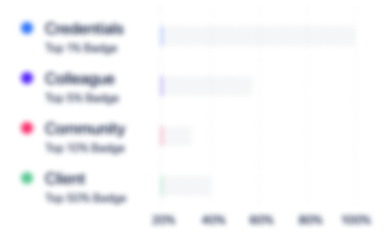
Bio


Credentials
-
Business Process Improvement
LinkedInMay, 2021- Nov, 2024 -
Lean Six Sigma White Belt Certification
lean
Experience
-
ECS Composites
-
United States
-
Packaging & Containers
-
1 - 100 Employee
-
Expeditor/ Cost Estimator/Continuous Improvement Officer
-
Feb 2021 - Present
-
-
Buyer
-
Aug 2020 - Jan 2021
-
-
-
The Home Depot
-
United States
-
Retail
-
700 & Above Employee
-
Sales Associate
-
Aug 2020 - Aug 2020
-
-
Hardware Sales Associate
-
Aug 2019 - Aug 2020
-
-
-
-
Expeditor/Purchaser/Continuous Improvement
-
Sep 2018 - May 2020
Involved with all aspects of business, from procurement, through manufacturing and billing. Once customer gives us a PO to commence work on their project, I order all material and components needed to manufacture and complete the job, sending out Rfq's for best price and lead time from current suppliers. Also set up in Sage, new suppliers I find that provide competitive price, product and lead time. Once work begins, work with our machine shop and outside vendors who perform services integral for the completion of the order. Familiar with the steps involved with all outside processes, including Machining, Turning, OD/ID Grinding, Double Disc Grind, Blanchard Grind, Wire and Conventional EDM, Passivation, Finishing, including Cerakote, Black Oxide, Chemical Film (Clear and Gold), Anodize, Chromate, Zinc, Laser and Chemical Etching. Kept in constant contact with outside processes to ensure deadlines maintained, due to each step determining completion date of next one. Deliver material, PO and design blueprints for what's expected of them. Communicated with service vendors on tolerances/limits to hold on their process. Used my working knowledge of GD&T and blueprint reading to interpret details to these same vendors. Expedite order through each step of manufacture, through all processes, ensuring high level of quality and completion.Utilized Excel and VBA to build a program for the company that has automated the quoting, ordering and tracking of historical data, including labor and invoicing. Have taken the company from manual entry of records to one that utilizes dashboards displaying kpi's, knows and can quickly recall records and quotes for future orders, and can see a snapshot of the current fiscal health for reporting to stockholders. I've utilized Excel to create an automatic scheduler that lets us know even before a job is started, when it'll be finished, and how long each step in the order should take.
-
-
-
-
Purchaser/Continuous Improvement Officer
-
May 2012 - Sep 2018
Consistently follow best practices to accurately forecast and project stock levels and review tenders and bids. Overhaul several purchasing aspects; order placement timing, supply/demand alignment, material replenishment, and diligently working and renegotiating with suppliers to decrease company spending. Involved in equipment purchases, site improvement, OSHA compliance and process improvement. Contacted multiple contractors and opened bidding on planned projects, reviewed bids and awarded based on price and projected completion of their timeline. Managed multiple aspects in regard to projects, coordinating schedules and deadlines with current and next step in completion as benchmarks. Review technical documents, process diagrams, blueprints, P&ID to compile a Request For Quote from suppliers.Conduct extensive research to identify alternative items to adopt standardization, match specification, quality and lead time; decreasing the number of vendors from 150 down to 27.Establish VMI programs with vendors that are able to meet our requirements for stocking and availability.Work with OEM suppliers for contract pricing via vendors willing to stock inventory applicable to company's needsPurchased equipment, consumables and services from vendors and suppliers.Negotiated best price and lead time for repair parts, repairs and other services as needed.Chose vendors to manage inventory and received special pricing, to save the company money by installing point of use machines to vend consumables and safety products.Started a program with motor supplier to provide vibration analysis on our most crucial equipment, to get advanced notice of failure, allowing for more cost effective repairs during downtime vs replacing motors due to failures.Eliminated Maverick spending plantwide by researching and adopting a uniform selection of products that represented the most traceable production and sanitation tools for documentable recall.
-
-
-
Andes Candies, LLC
-
United States
-
Food and Beverage Manufacturing
-
1 - 100 Employee
-
Maintenance Planner
-
Apr 2008 - Apr 2012
As a Maintenance Planner, I focused on tracking repair of parts and managing PM schedules. I also managed inventory levels as well as coordinated with vendors to secure the best products for the best price and quality. During my time here, I made several noteworthy contributions: ♦ Decreased downtime by strategically scheduling equipment repairs to restore operations. ♦ Secured a 35% decrease in downtime by ensuring that the PM had all specific tools, parts and lubricants that will be needed to complete tasks. ♦ Optimized operations by analyzing PM processes and decreasing the number of PM's needed by 30%. ♦ Reclaimed $25K in company savings in new tooling equipment through expanding the pm system to encompass tools and shop equipment, and maintaining their life and performance. ♦ Maintained productivity by analyzing the availability of PM schedule to coordinate repairs that impacted operations with minimal interruption. ♦ Increased movement accuracy; formulated a smart part numbering system for internal tracking of parts usage.♦ Categorized parts in an ABC usage system, taking into account not only the loss of production time of failing parts, but historical data and graphs to determine categories.
-
-
Purchaser
-
Mar 2010 - Apr 2011
To ensure smooth work flow, I collaborated with the Project Manager to support and expedite timelines as well as oversaw the accuracy and quality of materials and products. Major accomplishments are: ♦ Shortened the number of vendors by 7 in a two week time frame by bringing on 3. ♦ Redeemed $3K in savings by liquidating old and obsoleted inventory. ♦ Evaluated the distance of current vendors and identified others in closer proximity; saved the company $3K. ♦ Oversaw the movement and timely delivery of products; communicated effectively with suppliers, vendors, PM's contractors, and personnel to provide status and any changes on delivery timetables. ♦ Accurately completed and maintained documentation to keep for records. ♦ Proactively prepared for issues that could impede delivery time.
-
-
Education
-
Galena High School
Community
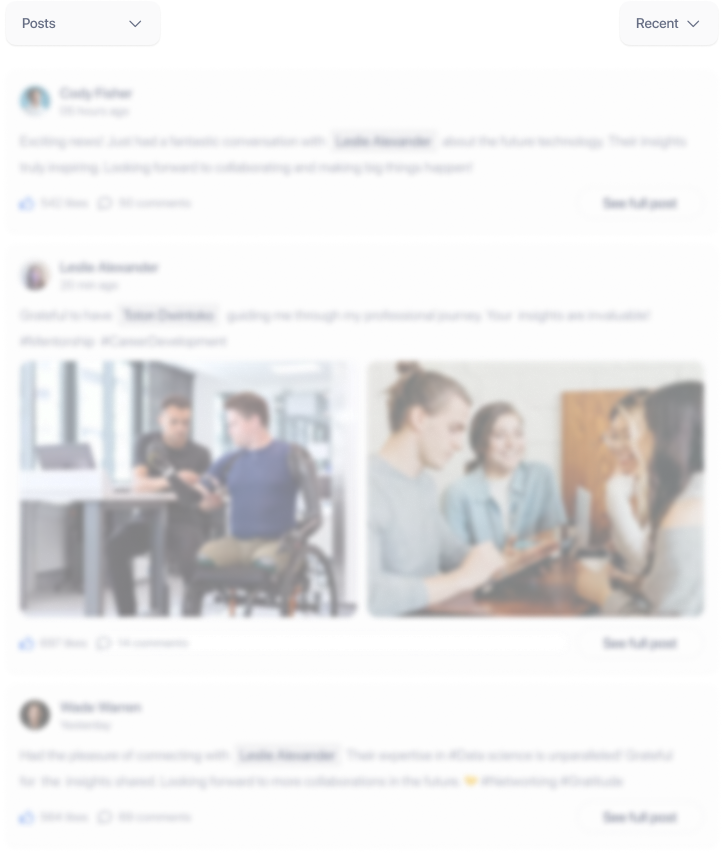