Michael Millard, MBA, CPIM, LSSGB
Director of Operations at Wagner Logistics- Claim this Profile
Click to upgrade to our gold package
for the full feature experience.
Topline Score
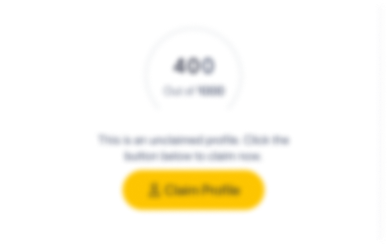
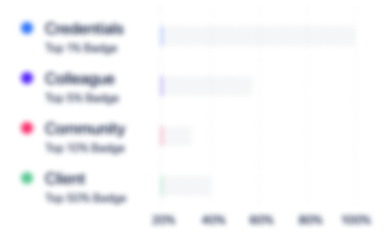
Bio

Ryan Farnsworth
Micheal has a clear focus on big picture planning and has the drive to achieve desired results. I learned a great deal form him during the time that he was my production manager.

Ryan Farnsworth
Micheal has a clear focus on big picture planning and has the drive to achieve desired results. I learned a great deal form him during the time that he was my production manager.

Ryan Farnsworth
Micheal has a clear focus on big picture planning and has the drive to achieve desired results. I learned a great deal form him during the time that he was my production manager.

Ryan Farnsworth
Micheal has a clear focus on big picture planning and has the drive to achieve desired results. I learned a great deal form him during the time that he was my production manager.

Credentials
-
CPIM I Certified in Production and Inventory Management
APICSJan, 2015- Oct, 2024 -
Lean Six Sigma
-Jan, 2013- Oct, 2024 -
Lean Six Sigma Green Belt
-Jan, 2013- Oct, 2024
Experience
-
Wagner Logistics
-
United States
-
Transportation, Logistics, Supply Chain and Storage
-
100 - 200 Employee
-
Director of Operations
-
Jan 2023 - Present
-
-
-
SCD Probiotics, LLC
-
United States
-
Biotechnology Research
-
1 - 100 Employee
-
Director of Operations at SCD Probiotics, LLC
-
Jan 2022 - Jan 2023
-
-
Senior Manager of Operations at SCD Probiotics, LLC
-
Feb 2021 - Jan 2022
• Operations master planning and implementation including production schedule planning and forecasting, and create/implement policies and procedures as necessary for effective plant operations. • Personnel management: Ensure that personnel have proper qualifications, are properly trained, and motivated to work productivity both as part of a team and individual. The candidate will lead the development of team goals and ensuring that these are communicated and understood by other team… Show more • Operations master planning and implementation including production schedule planning and forecasting, and create/implement policies and procedures as necessary for effective plant operations. • Personnel management: Ensure that personnel have proper qualifications, are properly trained, and motivated to work productivity both as part of a team and individual. The candidate will lead the development of team goals and ensuring that these are communicated and understood by other team members. • Ensure compliance with established standards/certifications and procedures involving safety, sanitation, good manufacturing policies, lean manufacturing and other plant programs. Analyze operational problems. Identify probable root cause. Implement opportunities for continuous improvement. Recommends changes when needed and assists in implementation of new processes. • Manage and utilize KPIs to improve company business. • Manage and provide leadership to operations, fulfillment and warehouse staffs in solving complex problems. • Demonstrate and develops operational experience to understand and ultimately provide robust process solutions as well as project capacity planning for continuing production and its expansion. • Manage inventory for both supplies and products manufactured by the company. • Oversee and maintain production equipment as well as physical facility and the equipment in good working conditions. • Review and approves all major projects. Exercises authority to implement and initiate projects. • Participates with senior management in developing and establishing organizational and company policies. Receives strategic guidance only. • Responsible for the career growth of employees.
-
-
-
Neovia Logistics
-
Transportation, Logistics, Supply Chain and Storage
-
700 & Above Employee
-
Operations Manager
-
Oct 2017 - Feb 2021
Responsible for all operations of a seven days per week, multi-shift 3PL. Oversee approximately 125 employees including Supervisors and Leads. Responsible for ensuring product is received accurately and in a timely manner. Also ensures adequate order cycle and delivery times to meet customer’s KPI's. Develops, monitors and coaches performance at the employee and department level. Directly and/or indirectly supervises all employees within the facility. Plans, organizes and controls all… Show more Responsible for all operations of a seven days per week, multi-shift 3PL. Oversee approximately 125 employees including Supervisors and Leads. Responsible for ensuring product is received accurately and in a timely manner. Also ensures adequate order cycle and delivery times to meet customer’s KPI's. Develops, monitors and coaches performance at the employee and department level. Directly and/or indirectly supervises all employees within the facility. Plans, organizes and controls all activities of the departments. Participates in developing department goals, objectives and systems. Acts as an integral part of the site’s Management team, works together with team to focus on current issues and opportunities, as well as long-term strategies. Works to establish a high degree of mutual trust and respect between employees, shifts, and departments by resolving conflicts consistently and objectively. Encourages collaboration and teamwork. Plans/schedules the efficient use of manpower and equipment to accomplish objectives. Maintains contact with carriers to ensure delivery schedules are met and load quality meets customer requirements Ensures disciplinary actions are being handled promptly and consistently by all supervisors on each shift. Plans and continuously monitors departmental operations to ensure that all work requirements and customer needs are being met. Works closely with Facilities and Maintenance staff to ensure all equipment is in safe, working order. Maintains a highly motivated workforce by timely communications, displaying an attitude of safety, consistency, fairness, focused recognition for good work and ideas, customer commitment, teamwork, and outcomes.. Leads continuous improvement processes throughout the facility. Develops and provides key performance metrics and countermeasures on a regular basis to all levels of the organization. Oversees all departmental budgets of shift. Responsible for each department’s annual budgetary performance. Show less Responsible for all operations of a seven days per week, multi-shift 3PL. Oversee approximately 125 employees including Supervisors and Leads. Responsible for ensuring product is received accurately and in a timely manner. Also ensures adequate order cycle and delivery times to meet customer’s KPI's. Develops, monitors and coaches performance at the employee and department level. Directly and/or indirectly supervises all employees within the facility. Plans, organizes and controls all… Show more Responsible for all operations of a seven days per week, multi-shift 3PL. Oversee approximately 125 employees including Supervisors and Leads. Responsible for ensuring product is received accurately and in a timely manner. Also ensures adequate order cycle and delivery times to meet customer’s KPI's. Develops, monitors and coaches performance at the employee and department level. Directly and/or indirectly supervises all employees within the facility. Plans, organizes and controls all activities of the departments. Participates in developing department goals, objectives and systems. Acts as an integral part of the site’s Management team, works together with team to focus on current issues and opportunities, as well as long-term strategies. Works to establish a high degree of mutual trust and respect between employees, shifts, and departments by resolving conflicts consistently and objectively. Encourages collaboration and teamwork. Plans/schedules the efficient use of manpower and equipment to accomplish objectives. Maintains contact with carriers to ensure delivery schedules are met and load quality meets customer requirements Ensures disciplinary actions are being handled promptly and consistently by all supervisors on each shift. Plans and continuously monitors departmental operations to ensure that all work requirements and customer needs are being met. Works closely with Facilities and Maintenance staff to ensure all equipment is in safe, working order. Maintains a highly motivated workforce by timely communications, displaying an attitude of safety, consistency, fairness, focused recognition for good work and ideas, customer commitment, teamwork, and outcomes.. Leads continuous improvement processes throughout the facility. Develops and provides key performance metrics and countermeasures on a regular basis to all levels of the organization. Oversees all departmental budgets of shift. Responsible for each department’s annual budgetary performance. Show less
-
-
-
-
Operations Manager Pursuing Opportunities
-
Apr 2017 - Sep 2017
-
-
-
Amazon
-
United States
-
Software Development
-
700 & Above Employee
-
Operations Manager
-
Apr 2016 - Mar 2017
Job Description The Operations Manager has complete responsibility for inbound operations, outbound operations or a functional process responsibility within the fulfillment center on a specified shift or across multiple shifts. Responsibilities: • Lead and supervise a team of Area Managers (2-5 front-line supervisors depending on location) and 100-300 hourly associates in outbound or inbound operations within the Fulfillment Center. • Responsible for the overall safety, quality… Show more Job Description The Operations Manager has complete responsibility for inbound operations, outbound operations or a functional process responsibility within the fulfillment center on a specified shift or across multiple shifts. Responsibilities: • Lead and supervise a team of Area Managers (2-5 front-line supervisors depending on location) and 100-300 hourly associates in outbound or inbound operations within the Fulfillment Center. • Responsible for the overall safety, quality and performance and customer experience of the shift. • Carry out supervisory responsibilities in accordance with the organization’s policies and procedures. • Accountability for meeting and exceeding operational goals. • Strategic planning and forecasting; appraise performance; reward and discipline employees; resolve problems; and address staffing needs. • Mentor, train and develop teammates for career progression and learning • Ability to develop and share best practices across the shifts and network. Show less Job Description The Operations Manager has complete responsibility for inbound operations, outbound operations or a functional process responsibility within the fulfillment center on a specified shift or across multiple shifts. Responsibilities: • Lead and supervise a team of Area Managers (2-5 front-line supervisors depending on location) and 100-300 hourly associates in outbound or inbound operations within the Fulfillment Center. • Responsible for the overall safety, quality… Show more Job Description The Operations Manager has complete responsibility for inbound operations, outbound operations or a functional process responsibility within the fulfillment center on a specified shift or across multiple shifts. Responsibilities: • Lead and supervise a team of Area Managers (2-5 front-line supervisors depending on location) and 100-300 hourly associates in outbound or inbound operations within the Fulfillment Center. • Responsible for the overall safety, quality and performance and customer experience of the shift. • Carry out supervisory responsibilities in accordance with the organization’s policies and procedures. • Accountability for meeting and exceeding operational goals. • Strategic planning and forecasting; appraise performance; reward and discipline employees; resolve problems; and address staffing needs. • Mentor, train and develop teammates for career progression and learning • Ability to develop and share best practices across the shifts and network. Show less
-
-
-
-
Operations Manager Pursuing Opportunities
-
Dec 2015 - Mar 2016
I believe as managers we should be active leaders and engage in the activities on the floor leading teams on a regular basis. Managers must exude positive energy and motivate others. Managers have complete responsibility of the functional processes within the departments. As leaders we must be able to inspire more efficient ideas, gather data and execute continuous process improvements.As managers we are responsible for making safety not only a priority, but a culture. I believe as managers we should be active leaders and engage in the activities on the floor leading teams on a regular basis. Managers must exude positive energy and motivate others. Managers have complete responsibility of the functional processes within the departments. As leaders we must be able to inspire more efficient ideas, gather data and execute continuous process improvements.As managers we are responsible for making safety not only a priority, but a culture.
-
-
-
PaperWorks
-
United States
-
Paper and Forest Product Manufacturing
-
300 - 400 Employee
-
Plant Manager
-
Apr 2015 - Nov 2015
*Responsible for the overall safe operations of the manufacturing facility to include, but not limited to, safety, personnel, housekeeping, maintenance, production, customer requirements/interface, planning and scheduling. *Manage material flow to insure inventory is maintained to the optimum levels to support on time customer deliveries. *Served as a key member of the management leadership team reporting back to the corporate office. *Assisted in development and… Show more *Responsible for the overall safe operations of the manufacturing facility to include, but not limited to, safety, personnel, housekeeping, maintenance, production, customer requirements/interface, planning and scheduling. *Manage material flow to insure inventory is maintained to the optimum levels to support on time customer deliveries. *Served as a key member of the management leadership team reporting back to the corporate office. *Assisted in development and evaluation of data, and made process improvements. *Manage employees to include schedules, training, productivity, and discipline when necessary. *Create and oversee the daily production schedule. *Address unplanned and scheduled maintenance issues. *Manage and solve maintenance issues as they arise. *Responsible for ensuring quality systems are in place and comply with customer specifications. *Manage production of customer product on a timely basis per schedule. *Oversee logistics for the shipping and receiving of raw materials. *Oversight of major projects and capital purchases. *Oversight of plant purchases – production supplies *Create and maintain a strong safety culture. *Oversee the organization of the work space and machines to increase efficiency *Review and analyze production reports (OEE, downtime, waste, etc.) to determine causes of nonconformity with product specifications, and/or operating or production problems. Show less *Responsible for the overall safe operations of the manufacturing facility to include, but not limited to, safety, personnel, housekeeping, maintenance, production, customer requirements/interface, planning and scheduling. *Manage material flow to insure inventory is maintained to the optimum levels to support on time customer deliveries. *Served as a key member of the management leadership team reporting back to the corporate office. *Assisted in development and… Show more *Responsible for the overall safe operations of the manufacturing facility to include, but not limited to, safety, personnel, housekeeping, maintenance, production, customer requirements/interface, planning and scheduling. *Manage material flow to insure inventory is maintained to the optimum levels to support on time customer deliveries. *Served as a key member of the management leadership team reporting back to the corporate office. *Assisted in development and evaluation of data, and made process improvements. *Manage employees to include schedules, training, productivity, and discipline when necessary. *Create and oversee the daily production schedule. *Address unplanned and scheduled maintenance issues. *Manage and solve maintenance issues as they arise. *Responsible for ensuring quality systems are in place and comply with customer specifications. *Manage production of customer product on a timely basis per schedule. *Oversee logistics for the shipping and receiving of raw materials. *Oversight of major projects and capital purchases. *Oversight of plant purchases – production supplies *Create and maintain a strong safety culture. *Oversee the organization of the work space and machines to increase efficiency *Review and analyze production reports (OEE, downtime, waste, etc.) to determine causes of nonconformity with product specifications, and/or operating or production problems. Show less
-
-
-
-
Materials Operations Manager
-
Oct 2006 - Apr 2015
Responsible for: *Effective execution of the monthly demand planning process, Monthly Demand Review Meetings and support of the Joint S&OP Decision meetings. *Prepare annual sales planning tools and facilitate the joint planning process between commercial, customer service and finance. *Develop seasonal indices to be used in the extrapolation of the inputs to generate a monthly item/ship to financial plan in units & dollars. Coordinate the upload of the annual plan into the… Show more Responsible for: *Effective execution of the monthly demand planning process, Monthly Demand Review Meetings and support of the Joint S&OP Decision meetings. *Prepare annual sales planning tools and facilitate the joint planning process between commercial, customer service and finance. *Develop seasonal indices to be used in the extrapolation of the inputs to generate a monthly item/ship to financial plan in units & dollars. Coordinate the upload of the annual plan into the wIntegrate (ERP) system. *Lead organization within the scope of the all procurement processes to limit cost of the supply chain by managing the following: Commodity and negotiation strategies including Terms and Conditions Supplier selection, evaluation and rationalization of Supply chain solutions, including vendor managed inventory (VMI), supplier consignment and safety stock levels. *Manage the wIntegrate system, ensuring accuracy of the variables that make up a demand forecasting unit (Customer, Sales Region, Brand). Ensure data cleanliness removing duplicates, managing changes in the network. *Facilitate the monthly upload process into wIntegrate (ERP), troubleshoot and facilitate resolution of issues. *Ensure that effective forecasting tools & process are in place to provide an accurate view of demand as an input into the S&OP Process, Production Planning, Inventory targets & Financial planning. *Identify appropriate routing and MRP/DRP relationships for all new items, establishing relationship in wIntegrate and auditing monthly to ensure accuracy and alignment to the annual load plan and the most recent S&OP load plan. *In support of capacity and inventory planning, the Materials Manager is responsible to set inventory & safety stock policies to optimize service levels. *Responsible for master data management process and management of the specifications coordinator executing item and bill of material (BOM) set ups.
-
-
Manufacturing Production Operations Manager
-
Dec 2012 - May 2014
*Plan, direct and coordinate production work flow; prepare production schedule and set deadlines to ensure timely completion of work *Maintain daily contact with, supervisors, production team leaders, set-up team, and temporary staffing agency to assure production requirements are met *Coordinate production activities with the related activities of other departments *Ensure training of plant production personnel; update and maintain training documentation pertaining to production… Show more *Plan, direct and coordinate production work flow; prepare production schedule and set deadlines to ensure timely completion of work *Maintain daily contact with, supervisors, production team leaders, set-up team, and temporary staffing agency to assure production requirements are met *Coordinate production activities with the related activities of other departments *Ensure training of plant production personnel; update and maintain training documentation pertaining to production efficiency, safety, GMP’s , SOP’s, and quality procedures *Establish and control conditions in production to achieve maximum efficiency; troubleshoot and resolve problems related to design, production, and quality issues *Develop and maintain cost effective efficiency and quality improvements *Promote innovation to achieve increased quality and productivity with Assembly Line Leaders *Direct supervision of Production Team Leaders and Support Team Leaders *Evaluate and review employee performance for both salaried and hourly employees *Maintain appropriate staffing levels; assist as needed in resolving employee issues and discipline *Comply with all safety and environmental rules and regulations; create and maintain a safe and secure work environment *Liaise with vendors and contractors *Participate in the budget process *Assist Plant Manager with executing operating strategies and plans, and achieving company goals and objectives
-
-
Distribution Manager, NA
-
Oct 2006 - Nov 2012
Inventory Planning / Scheduling: *Prioritization of orders and adjusting of schedules to ensure customer priority requirement are met, raw material utilization is maximized, and raw material upgrades minimized. *Ensure efficient scheduling and routing to and from plants and their customers to achieve lowest total costs and on-time in-full (OTIF) delivery *Schedule shipping to successfully meet customer requirements and ensure effective delivery of services to internal and external… Show more Inventory Planning / Scheduling: *Prioritization of orders and adjusting of schedules to ensure customer priority requirement are met, raw material utilization is maximized, and raw material upgrades minimized. *Ensure efficient scheduling and routing to and from plants and their customers to achieve lowest total costs and on-time in-full (OTIF) delivery *Schedule shipping to successfully meet customer requirements and ensure effective delivery of services to internal and external customers with lowest total cost fulfillment *Oversee cost estimating process performed and coordination of orders with Corporate Procurement and distributors. *Ensure proper inventory procedures are being followed and margin improvements obtained *Work with production to resolve raw material utilization and manufacturing issues and eliminate raw material upgrades, substitutions *Work with Operations Managers in conducting capacity planning. Logistics / Fleet Management: *Identify transportation synergies between Business Units, Plants, Warehouse to meet demands and reduce costs *Develop and implement transportation initiatives in support of the organization’s service objectives *Manage day-to-day Warehouse, employees, equipment, budget and external vendor and 3PL’s over-site. *Monitor and report results against established key performance indicators including clear weekly reporting metrics
-
-
Education
-
Baker University
Master of Business Administration (MBA), Business Administration, Management and Operations -
Park University
Bachelor of Science (B.S.), Business Administration and Management, General -
APICS
CPIM, APICS Certified in Production and Inventory Management
Community
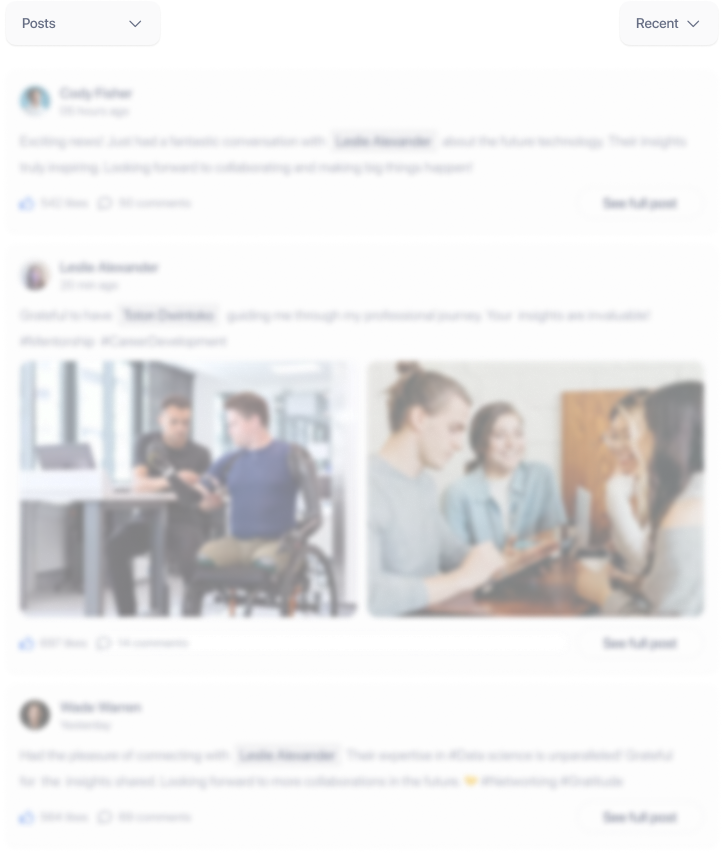