Michael Johnson
Principal NPI Engineer, R&D at Canary Medical Inc.- Claim this Profile
Click to upgrade to our gold package
for the full feature experience.
Topline Score
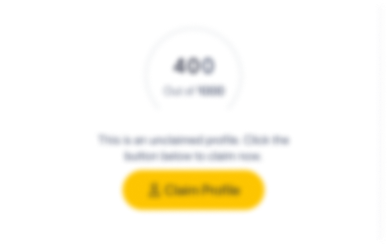
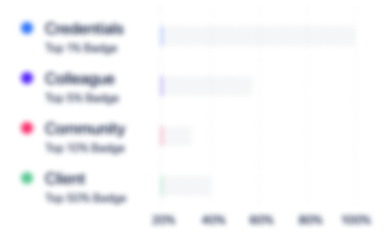
Bio

Amanda Tian
Michael’s extensive technical expertise, passion for learning, and effective problem solving strategies were valued assets on our team’s project. After working with him for over two and a half years, I observed Michael lead our team through countless tasks such as designing for manufacturing and meeting customer needs, performing root cause analysis, and determining effective test plans. Aside from being a valuable technical lead, Michael was a tremendous resource for educating and mentoring his peers on materials, manufacturing processes, CAD, and GD&T.

Eitan Nudel
Michael was always my go-to when I had a technical question while working at Breg. His knowledge and problem-solving capabilities were always what pushed the product development team in the right direction, every single time. Michael always asked the right questions and challenged our designs, while providing constructive feedback and technical help. Michael is a great team player and I'm confident he will succeed in all of his future projects.

Amanda Tian
Michael’s extensive technical expertise, passion for learning, and effective problem solving strategies were valued assets on our team’s project. After working with him for over two and a half years, I observed Michael lead our team through countless tasks such as designing for manufacturing and meeting customer needs, performing root cause analysis, and determining effective test plans. Aside from being a valuable technical lead, Michael was a tremendous resource for educating and mentoring his peers on materials, manufacturing processes, CAD, and GD&T.

Eitan Nudel
Michael was always my go-to when I had a technical question while working at Breg. His knowledge and problem-solving capabilities were always what pushed the product development team in the right direction, every single time. Michael always asked the right questions and challenged our designs, while providing constructive feedback and technical help. Michael is a great team player and I'm confident he will succeed in all of his future projects.

Amanda Tian
Michael’s extensive technical expertise, passion for learning, and effective problem solving strategies were valued assets on our team’s project. After working with him for over two and a half years, I observed Michael lead our team through countless tasks such as designing for manufacturing and meeting customer needs, performing root cause analysis, and determining effective test plans. Aside from being a valuable technical lead, Michael was a tremendous resource for educating and mentoring his peers on materials, manufacturing processes, CAD, and GD&T.

Eitan Nudel
Michael was always my go-to when I had a technical question while working at Breg. His knowledge and problem-solving capabilities were always what pushed the product development team in the right direction, every single time. Michael always asked the right questions and challenged our designs, while providing constructive feedback and technical help. Michael is a great team player and I'm confident he will succeed in all of his future projects.

Amanda Tian
Michael’s extensive technical expertise, passion for learning, and effective problem solving strategies were valued assets on our team’s project. After working with him for over two and a half years, I observed Michael lead our team through countless tasks such as designing for manufacturing and meeting customer needs, performing root cause analysis, and determining effective test plans. Aside from being a valuable technical lead, Michael was a tremendous resource for educating and mentoring his peers on materials, manufacturing processes, CAD, and GD&T.

Eitan Nudel
Michael was always my go-to when I had a technical question while working at Breg. His knowledge and problem-solving capabilities were always what pushed the product development team in the right direction, every single time. Michael always asked the right questions and challenged our designs, while providing constructive feedback and technical help. Michael is a great team player and I'm confident he will succeed in all of his future projects.

Experience
-
Canary Medical Inc.
-
Canada
-
Medical Equipment Manufacturing
-
1 - 100 Employee
-
Principal NPI Engineer, R&D
-
Aug 2022 - Present
-
-
-
Ra Medical Systems
-
United States
-
Medical Equipment Manufacturing
-
1 - 100 Employee
-
Staff R&D Engineer
-
Feb 2022 - Jun 2022
Optimized the energy and working life of the 308nm Excimer Laser used in the dermatology and vascular intervention industry. Identified production issues and design improvements to produce a more stable laser. Made design changes to the laser to solve existing problems and improved catheter production by identifying problems, building fixtures, and modifying procedures to improve a repeatable process. Created solid models, assemblies, and drawings for the entire laser system. Led Process and Component FMEA’s for the Pharos dermatology and DABRA vascular laser. Completed Verification and Validation of production equipment for both laser and catheter production. Served as the lead designer of a new application device for the dermatology laser including drawings, manufacturing instructions, and Verification and Validation. Developed test studies for lifetime (dynamic / static) use cases and designed in line test fixtures and methods for the catheter DABRA 101. Lead designer of new catheter attachment to vascular laser, including drawings, manufacturing instructions, and Verification and Validation. - Rebuilt high vacuum pump stations replacing pumps, gauges, and timers; added automated heating of system to drive out contaminates. - Utilized additive manufacturing (3D printing), mills, and lathes to build production and test fixtures. Advised other engineers in designing parts to optimize 3D printing. Improved catheter production by identifying problems, building fixtures, and modifying procedures to improve a repeatable process. Show less
-
-
Sr Manufacturing Engineer
-
Feb 2020 - Feb 2022
-
-
-
Breg
-
United States
-
Medical Equipment Manufacturing
-
500 - 600 Employee
-
Principal Product Engineer
-
Jan 2016 - Nov 2019
-
-
Senior Product Development Engineer
-
Mar 2010 - Jan 2016
-
-
Product Engineer
-
Nov 2007 - Feb 2010
-
-
-
Plastic Engineering & Development, Inc..
-
United States
-
Plastics Manufacturing
-
1 - 100 Employee
-
Project Engineer
-
Apr 2004 - Oct 2007
Assisted customers with product design and development for injection molding. Recommended materials for parts, type of tooling needed, and cavitation requirements. Worked with the Tool Builder on behalf of the customer to ensure a quality tool. Developed testing and documentation in accordance with FDA requirements. Assisted customers with product design and development for injection molding. Recommended materials for parts, type of tooling needed, and cavitation requirements. Worked with the Tool Builder on behalf of the customer to ensure a quality tool. Developed testing and documentation in accordance with FDA requirements.
-
-
-
IDEX Optical Technologies B.V.
-
Netherlands
-
Appliances, Electrical, and Electronics Manufacturing
-
1 - 100 Employee
-
Mechanical Engineer
-
Mar 2000 - Apr 2004
Designed components, jigs, and fixtures for Micro Lasers focusing on material selection, electrical shorting, and thermal paths. Wrote and processed Engineering Change Orders (ECO), tracked inventory and purchasing, and created process instructions for manufacturing. Designed components, jigs, and fixtures for Micro Lasers focusing on material selection, electrical shorting, and thermal paths. Wrote and processed Engineering Change Orders (ECO), tracked inventory and purchasing, and created process instructions for manufacturing.
-
-
Education
-
San Diego State University-California State University
Community
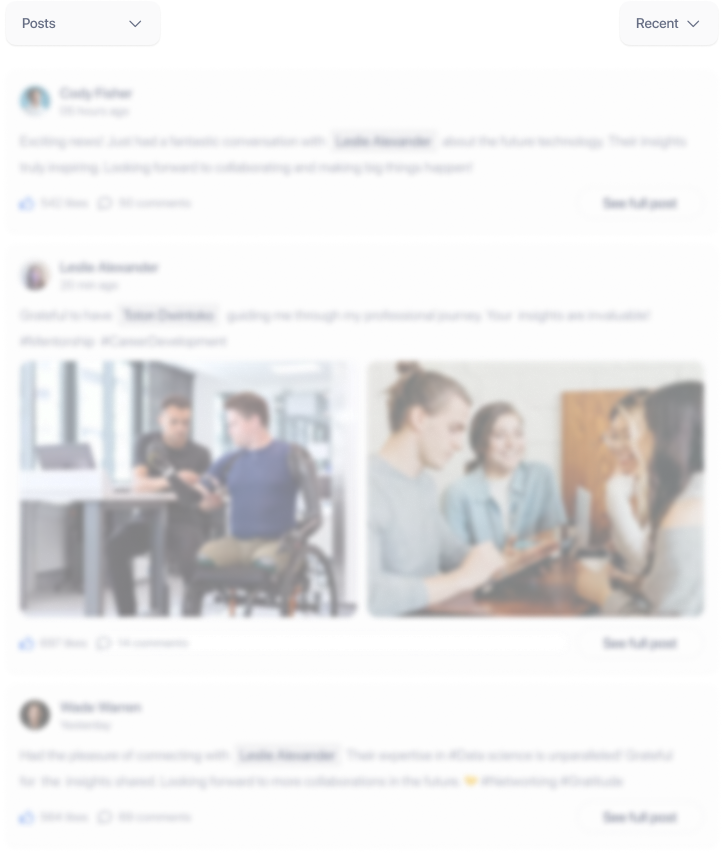