
Michael Hurd
Customer Success Manager at L2L- Claim this Profile
Click to upgrade to our gold package
for the full feature experience.
Topline Score
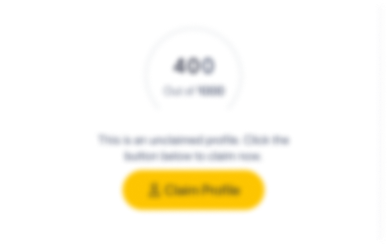
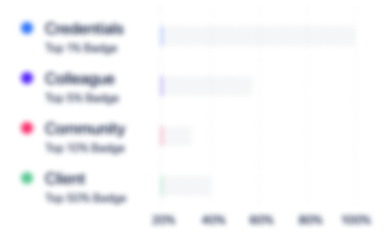
Bio


Credentials
-
Inventory Management Foundations
LinkedInMay, 2020- Nov, 2024 -
Learning SAP MM (Materials Management)
LinkedInMay, 2020- Nov, 2024
Experience
-
L2L
-
United States
-
Software Development
-
1 - 100 Employee
-
Customer Success Manager
-
Jul 2022 - Present
-
-
-
Daily's Premium Meats
-
United States
-
Food and Beverage Manufacturing
-
100 - 200 Employee
-
Maintenance Planner/Scheduler
-
May 2020 - Jul 2022
Hired to develop and implement new PM program using either existing software or introduce new methods to the company. Methods introduced were used to bridge the gap between ERP and CMMS systems where necessary, utilizing spreadsheets and Microsoft Project. When a primary CMMS was selected (Leading2lean) to replace current systems (spreadsheets, M3 and eMaint), I led the department project and installation for our team and built a new database for the maintenance department. This included new asset management strategy, asset naming convention, parent child asset relationships, industry standard preventive maintenance practices, tooling, and inventory management. Within 90 days, Daily’s effectively drove equipment downtime to well below 5% and now maintains between 1.5-3% each week. Through preventative maintenance adherence, we also were credited with increasing production capacity to an additional $60 Million without purchasing any new equipment.
-
-
-
Westinghouse Electric Company
-
Nuclear Electric Power Generation
-
700 & Above Employee
-
Facilities Maintenance Planner
-
Jan 2018 - Apr 2020
Primarily manage contractors as contact liaison and procurement of services both related to planned work and/or scheduled preventive maintenance. Organized PM schedule for technicians of various trades while managing the same schedule to fit with contractor scheduled PM’s and general planned work. All scheduled work is managed through various systems with most planned work utilizing Leading 2 Lean as the primary CMMS, SAP PM/MM, and Corrigo are used in various support functions. I managed emergent work requests as parts procurement support and scheduled our team to react as necessary to effectively adjust the schedule and remove items from our backlog and recycle them back in for scheduling. Our outage planning requires assisting the other planners in our group with their assigned maintenance area where facilities work is being performed or needed in support of another projects taking place. I also maintain support roles for implementation and development of Leading 2 Lean as our CMMS. and I also maintain the maintenance SharePoint page as the site owner.
-
-
Materials Coordinator
-
Jan 2018 - Apr 2020
Baseline duties include working closely with maintenance personnel, ordering parts for aging critical machinery used to produce zirconium based nuclear fuel product for the fabrication side of the facility, including central maintenance staff. Participated in the planning phase of the plant site shutdown each summer and winter. Worked closely with planning to ensure all aspects of the maintenance backlog in each department of my charge are executed on time and supplied the correct parts to the craftsmen. I managed inventory in satellite store rooms, utilized SAP or Leading2Lean to transact data for bills of material, historical inventory consumption, reporting effective and relevant status to supervision and department managers, and labor costs for machinery on the plant site. My tertiary responsibilities include the implementation of fresh plans and ideas that further improve the on-site processes for inventory management, planning, and maintenance. An example includes writing simple reports that have decreased research time for the craftsmen on spare parts. Those efforts in my first year have resulted in significant cost savings for machinery that I’ve been able to focus on in a short amount of time.
-
-
-
TCR Composites
-
United States
-
Plastics Manufacturing
-
1 - 100 Employee
-
Tow Line Operator/Shift Lead
-
Feb 2017 - Dec 2017
Prework inspection and machine set up, maintaining, and monitoring flow of production through assigned tow line. Tasked with identifying quality builds, potential scrap, and improper aesthetics of prepreg fiber production as it is built on each spool. Required to control documentation throughout each aspect of the line, be it correct material weights, timing of resin production, and accurate data entry to the work order. In August of 2017 I was assigned Temporary Lead Specialist due to organizational changes, where I performed oversight of the production floor, mechanical adjustments of line functions to improve prepreg fiber builds, and general personnel. Secondary responsibilities include inventory management at times of order changes, accurate work order reporting, and conducting shift meetings prior to the workday.
-
-
-
TRIUMPH
-
United States
-
Aviation and Aerospace Component Manufacturing
-
700 & Above Employee
-
Calibration Technician
-
Aug 2013 - Oct 2016
Responsibilities included: check and maintain various instrumentation for calibration, handle all electrical and mechanical calibrations for test stands and multiple smaller instruments, such as pressure gauges, timers, multimeters and other types of equipment. Calibrations are controlled by a recall system ranging from 90 to 180 and 365 day periods.● Initiated collaborations to address lack of training for a new software implementation. Worked with individuals from other departments to evaluate each area of the program and input mock parts to test various aspects of the tool management / calibration system. Discovered many useful tools to reduce time and work for data entry down to a minimum.● Wrote and published manuals for the calibration processes.● Stayed current on intercompany procedures as and industry standards.
-
-
Outside Process Expediter
-
Aug 2008 - Aug 2013
Coordinate outside processing aspect for internal customers.● Created a detailed Excel report that tracked parts with relevant information that could customized by the user to search by part, program, vendor, or due date. It was so well received that IT connected it to theMRP system and made it a simple query report that updated automatically. This decreased wait time for internal customers to get updates, improved communication between the Planning, Program Management, and Quality departments.● Took initiative to research alternatives for a specific costly brake housing part. Researched and shopped vendors. Negotiated pricing to save $350,000/year based on future unit forecast.
-
-
Education
-
University of Phoenix
Bachelor's degree, Bachelor of Science in Business, Project Management Certificate -
Ogden-Weber Technical College
Certified Technical Diploma, Cabinetmaking and Millwork
Community
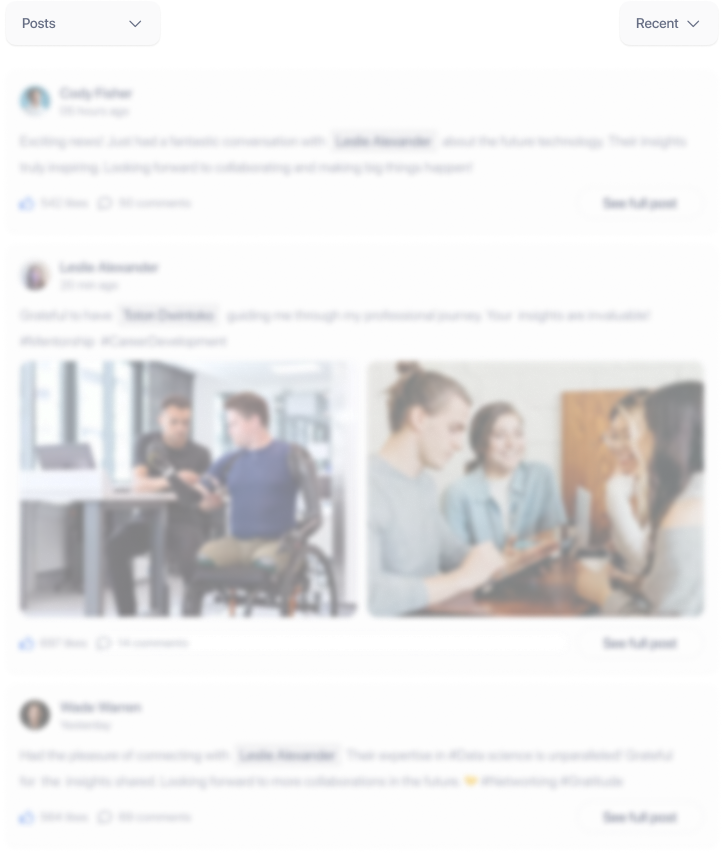