Michael Hoerner
Warehouse/Shipping Supervisor at WENDT CORPORATION- Claim this Profile
Click to upgrade to our gold package
for the full feature experience.
Topline Score
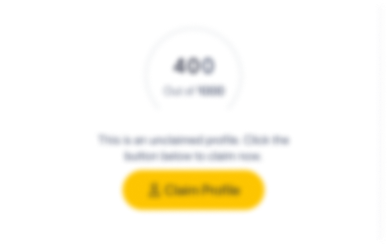
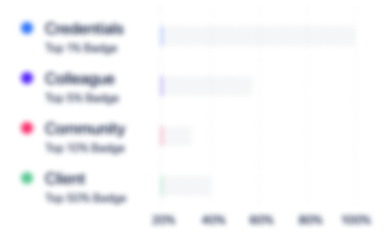
Bio


Experience
-
WENDT CORPORATION
-
United States
-
Machinery Manufacturing
-
1 - 100 Employee
-
Warehouse/Shipping Supervisor
-
Feb 2017 - Present
• Identify where VISION Systems can be improved to be better utilized • Changed warehouse floor plan for better efficiency. • International Shipping • Harmonized tariff code classification • Efficient work order flow • Maintain timely receiving practices • Daily accuracy and shipping of customer orders • Safely monitor the handling of exceptionally heavy product within the facility • Safety committee member • Identify where VISION Systems can be improved to be better utilized • Changed warehouse floor plan for better efficiency. • International Shipping • Harmonized tariff code classification • Efficient work order flow • Maintain timely receiving practices • Daily accuracy and shipping of customer orders • Safely monitor the handling of exceptionally heavy product within the facility • Safety committee member
-
-
-
Chart Industries, Inc.
-
United States
-
Industrial Machinery Manufacturing
-
700 & Above Employee
-
Warehouse Supervisor
-
Jan 2015 - Feb 2017
• Defined where JD Edwards, E1 Oracle system needs to be examined for productivity improvements. • Changed warehouse floor plan for better efficiency. o The shipping and the receiving departments were separated to utilize different dock doors. o Receiving was moved to the intake side of the warehouse to reduce travel time through the warehouse to materials storage. o The shipping department was move to the finished goods of the plant to increase productivity for order selection and shorter travel distance to the shipping dock staging area. • Actively involved with Safety Committee and have been trained in DuPont Stop for safety. • Actively worked with shipping department and identified computer short-cuts that were necessary to be implemented to increase productivity of the department. • Established SOP’s for the Receiving department to eliminate receiving errors. • Distributed workload utilizing a staff of 36 employees across 2 shifts, including 4 leads across Shipping, Receiving, and Materials. • Forklift in-house certified trainer of powered walkie jacks, sit-down forklifts and stand-up reach trucks. • Established mentoring program with the shipping lead for further advancement. • Reviews and coaching to advise my staff and continue their growth within the organization. • Followed strict FDA, ISO9001, and ISO13485 quality programs/regulations.
-
-
-
Canon Business Process Services
-
United States
-
Outsourcing and Offshoring Consulting
-
700 & Above Employee
-
Site Manager
-
May 2009 - Jan 2015
* I was selected as the Site Supervisor and progressed into a site Manager is a 6 month period. * Implemented Six Sigma 5-S program to improve efficiency and optimization * Reduced and controlled company expenses by taking control of Office supplies and internal use materials. * Prepared program operating budgets, budget reports and other financial performance reports. * Assumed ownership over team productivity and managed work flow to meet or exceed quality service goals. * Produced monthly reports using advanced Excel spreadsheet functions.
-
-
-
ITT Inc.
-
United States
-
Industrial Machinery Manufacturing
-
700 & Above Employee
-
Warehouse Logistics Manager
-
Jun 2006 - Apr 2009
* Managed a 60-thousand square foot warehouse space employing 30 workers. * Using Six Sigma and OSHA Best Practices I designed and implemented a New 60 thousand square foot Warehouse within a Manufacturing facility. * Oracle Driven WMS System used for inventory control and order fulfillment. * Supervised a team of 2 area managers and 28 associates. * Led warehouse improvement initiatives to advance operational efficiencies. * Coordinated with freight forwarders to expedite international shipments.
-
-
-
Russell A. Farrow (U.S.) Inc
-
Amherst, NY
-
Warehouse Manager
-
Jan 2006 - Jun 2006
* Cross Docking operation from Toronto, Ontario to United States businesses * Determined the most cost-effective procedures and routes for shipments. * Translated business needs and priorities into actionable logistics strategies. * Reported carrier-performance metrics and monthly costs reports to executive team. * Redirected shipments en route in response to customer requests. * Maintained accurate stock records and schedules. * Established long-term customer relationships through prompt and courteous service.
-
-
-
Skulogix Incorporated
-
Depew, NY
-
Warehouse Manager
-
Sep 2002 - Jan 2006
* Managed a 120-thousand square foot 3PL warehouse space employing 125 workers utilizing a 3 shift operation. * This was a Highly Automated warehouse with RF readers on conveyor, hand-held RF units and Picker truck RF units. * Multiple Carousel, WMS Operated system used for high volume order selection * Bar code set-up warehouse on all slot positions, product and internal transportation equipment. * Direct shipping to big box companies. WalMart, Target, JC Penny's, Bed, Bath and Beyond and e-commerce. * Cross Docking of mixed trailers of apparel from Toronto, Ontario
-
-
-
Carquest Auto Parts
-
United States
-
Motor Vehicle Manufacturing
-
700 & Above Employee
-
Warehouse Manager
-
Jan 1981 - Sep 2002
* Steady progression through Warehouse Operations and into Warehouse Management role. * Managed a 100-thousand square foot warehouse space employing 48 workers. * Managed private WMS computer system from Cooperative Computing Inc. * Management responsibilities for Order Fulfillment, Warehouse to Warehouse transfers, Inventory control variance, Returned Product to Manufacturers. * Managed 14 fleet trucks with drivers. Maintenance of all DOT records and compliance for drivers. Maintained all DOT maintenance with leasing agent to ensure DOT compliance. * Planning all aspects of the annual inventory for accuracy and efficiency. RESULTS: Preparations for inventory completed, and a timely inventory with less than a 1% deviation of a 10 million-dollar inventory.
-
-
Education
-
Cornell University
2 year Certificate, Supervisory Studies
Community
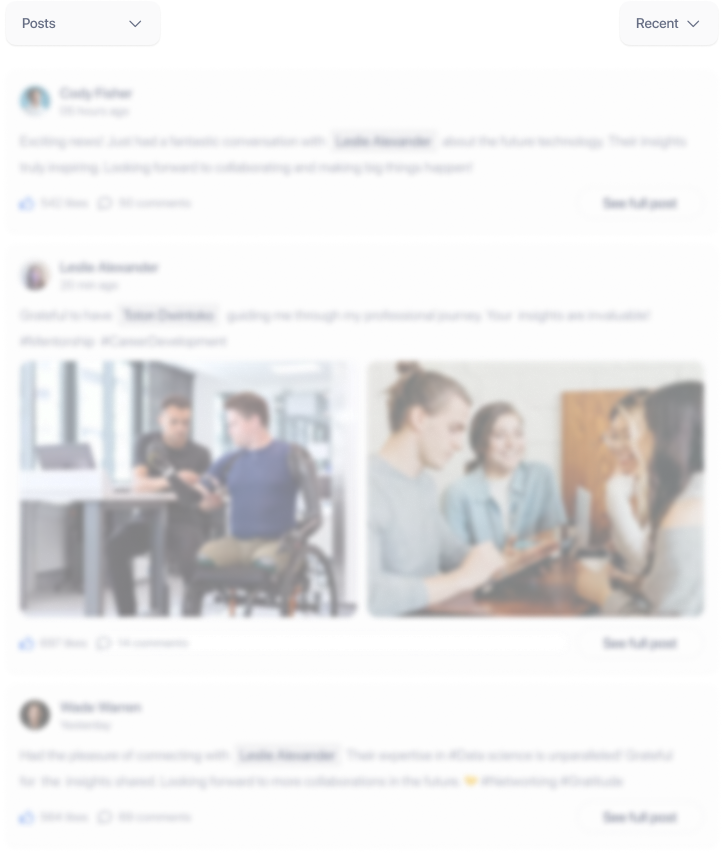