Michael Borowicz
Quality Assurance / Quality Control Specialist at Quincy Bioscience- Claim this Profile
Click to upgrade to our gold package
for the full feature experience.
Topline Score
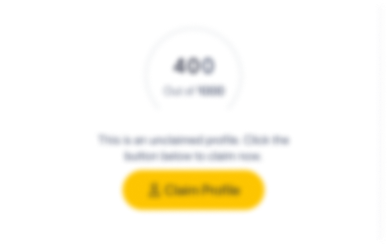
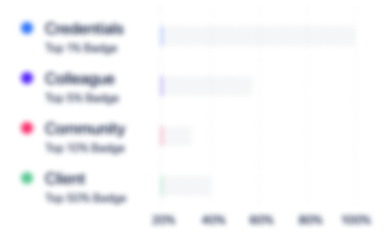
Bio


Experience
-
Quincy Bioscience
-
United States
-
Biotechnology Research
-
1 - 100 Employee
-
Quality Assurance / Quality Control Specialist
-
Aug 2012 - Present
- Ensures that our products are being manufactured in compliance with the cGMP's by maintaining an on-site presence during the manufacturing process. - Maintains and enhances our internal quality systems. - Partners with CMO's to facilitate effective communications and maintain continued compliance with the cGMP's. - Compliance review of batch records/discrepancy resolution. - Release of product for distribution. - Author, review and approve Quality Systems Documentation including but not limited to SOP's, product specifications, CAPA's, and discrepancy reports. - Implementation and presentation of internal GMP training programs for both new employee orientation as well as annual company-wide training.
-
-
-
-
Sr. Compliance Specialist
-
Aug 2000 - Nov 2008
Monitor the manufacturing and packaging of pharmaceutical products at contract facilities, to ensure GMP compliance. Additional responsibilities included: - On-site expert for the product specific manufacturing processes. - Compliance review of batch records/discrepancy resolution. - Work with the CMO staff to resolve any compliance issues. - Recommend release of product for distribution. - Review and approval of new documents for submission into the change control system. Monitor the manufacturing and packaging of pharmaceutical products at contract facilities, to ensure GMP compliance. Additional responsibilities included: - On-site expert for the product specific manufacturing processes. - Compliance review of batch records/discrepancy resolution. - Work with the CMO staff to resolve any compliance issues. - Recommend release of product for distribution. - Review and approval of new documents for submission into the change control system.
-
-
-
-
Scientist
-
May 1999 - Aug 2000
Primary responsibility was to work with outside contractors, during the construction of a new pharmaceutical development and manufacturing facility, to ensure that the materials of construction, HVAC, building services, and manufacturing equipment were cGMP compliant. Some additional responsibilities included: - Investigate new manufacturing equipment capabilities and justify their purchase. - The preperation and manufacture of parenteral dosage forms at both their original facility located in the Medical University of South Carolina School of Pharmacy, and at their new Faber Place facility. - Train and supervise operators on on the proper techniques required, to manufacture GMP-compliant pharmaceutical products.
-
-
-
-
Scientist II - Product Development
-
1997 - 1998
As a Product Development Scientist II, I was responsible for the technology transfer of manufacturing processes from Product Development into Production. Some of the responsibilities of this position included: - Coordinate and Orchestrate the manufacturing of pharmaceutical demonstration batches. - Laison between the Product Development, Engineering, Quality Assurance, and Manufacturing Departments. - Ensure that all process steps were GMP compliant. - Verify that all equipment and processes have been calibrated and/or validated. - Train production personel to perform any non-routine process steps.
-
-
-
-
A number of positions held
-
1973 - 1997
Held a number of positions during my career at Searle. I was hired in the Shipping Dept. as a Packer and worked my way up through the ranks until my last position with the company, as a Sr. Pharmaceutical Technical Assistant. In that capacity I was responsible for the day-to-day operation of a Parenteral Product Pilot facility used to scale-up lab-size batches into pilot batches, and untimately manufacture clinical supplies. A major function of that position was to coordinate the twice annual facility shut-down. This shut-down provided a means to accomplish the manditory preventative maintenance requirements, on the equipment and the facility.
-
-
Education
-
Madison College
Certificate, Quality Management
Community
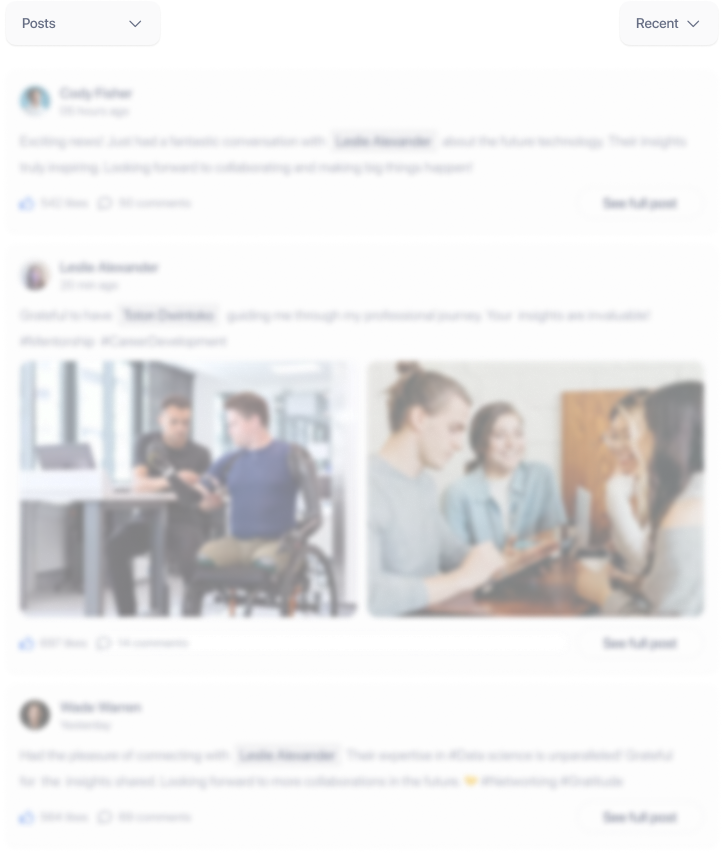