Mette Larsen
Production Manager at CC Plast A/S- Claim this Profile
Click to upgrade to our gold package
for the full feature experience.
-
Danish -
-
English -
Topline Score
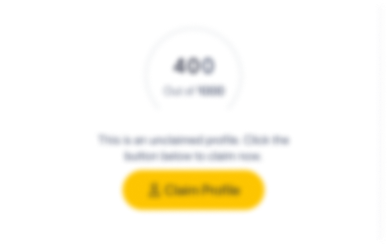
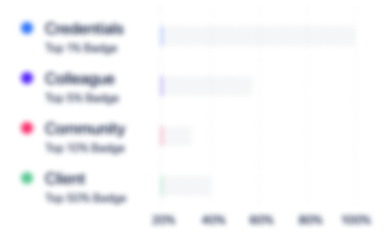
Bio


Credentials
-
ISO 13485 Lead Auditor
The Knowledge AcademySep, 2022- Nov, 2024 -
ISO 9001 Lead Auditor
The Knowledge AcademyFeb, 2022- Nov, 2024 -
Lean Navigator in Production
Teknologisk InstitutDec, 2011- Nov, 2024
Experience
-
CC Plast A/S
-
Denmark
-
Plastics Manufacturing
-
1 - 100 Employee
-
Production Manager
-
Nov 2022 - Present
-
-
-
Qlife
-
Denmark
-
Medical Equipment Manufacturing
-
1 - 100 Employee
-
Production Manager - Capsule
-
Mar 2022 - Nov 2022
Qlife has developed and now produces the Egoo health system, for biomarker testing at home. My primary responsibilities are: • Daily management of operators, lab technicians and bioanalytic • Responsible for production of capsules including QC test • Responsible for production equipment and maintenance • Responsible for personnel, competency, and employee development • Ensure production quality processes are implemented in a manner that fulfils all regulatory requirements while at the same time are optimal in terms of cost/benefit for the company. • Review and approval of documents concerning the department • Budget responsible • Responsible for coaching team members • Cooperation with R&D, QA and PS, regarding upscaling and readiness for production for new assays Show less
-
-
-
J. Krebs & Co. A/S - Plastics Processing
-
Denmark
-
Plastics Manufacturing
-
1 - 100 Employee
-
Quality Manager
-
Apr 2019 - Mar 2022
J. Krebs & Co. is a Danish-owned company that advises on and produces plastic items, primarily technical components, medico, and packaging. My primary responsibilities: • Day-to-day management of 10 machine operators and 2 QC employees • Update of current quality management system. The objective was better quality assurance of the processes, with generally higher quality and lower cost of the products as a result. • Preparation of documentation, primarily related to production, for certification ISO 13485, as well as practical implementation of processes and procedures. • Review of batch documentation, DQ, IQ, OQ, PQ, preparation of COA, COC, handling of CAPA, SCAR and internal deviations in collaboration with engineers, operators, and technicians • Customer contact regarding quality and documentation • Preparation and conduct of internal audits • Preparation and approval of validations on plastic components manufactured in accordance with ISO 13485 Result: My best and most exciting result was to secure an ISO 13485 certificate by building QMS in relation to purchasing, production, traceability, personnel and deviation handling. In addition, I have achieved great recognition from customers and management for coordination, communication and collaboration with both customers and colleagues. Show less
-
-
-
Gerresheimer Værløse
-
Værløse, Region Hovedstaden, Danmark
-
Technical Support Plastic
-
Jun 2017 - Mar 2019
Gerresheimer is a global company whose factory in Værløse primarily produces plastic packaging for the pharmaceutical market. My primary responsibilities: • Daily support and problem solving for the production regarding injection moulding, machines and equipment • Test runs and validations of new and old tools • Test, approval and commissioning of new peripherals, conveyor belts, robots, heat regulators etc. • Preparation of URS for new machines and equipment in collaboration with the departments • Contribute to FAT of new machines and tools • Coordination of service and repair machines in /out Show less
-
-
-
Novo Nordisk
-
Denmark
-
Pharmaceutical Manufacturing
-
700 & Above Employee
-
Team coordinator, Operator
-
May 2014 - May 2017
I am working in a cGMP and FDA regulated environment 24/5, three shifts. The most important task, together with my teammates, is to keep the assembly lines running by: adding materials, clean the line, correct minor errors and restart the line, change batches. During a shift there are some standard tasks for me as a coordinator: *OEE reviews and follow up on issues *Plan corrective actions with the technicians and stop the line in case of quality issues or low OEE. *Performance board meetings, escalate bigger issues to the next level *Continuous Improvements *Training SOPs Show less
-
-
-
ReSound
-
Denmark
-
Medical Equipment Manufacturing
-
700 & Above Employee
-
Process Engineer Plastic
-
Jun 2012 - May 2014
I was hired to be a technical assistent 60 percent of the working hours and LEAN Navigator the rest of the time. But after about six month, due to organizational changes I was offered a role as responsible for some procesces in the injection moulding department and day to day management of the QC-Team * IQ, OQ and PQ * Implementing and maintain new MES System (ALS Arburg), including training of technicians and colleagues * Review the MES data and report OEE to the management together with proposals for optimizations * Deal with costumer complaints B2B in accordance with FDA and ISO 13485, systematic problem solving and documentation * Smaller projects related to injection moulding and technology * Optimization of the processes regarding plast parts for hearing aids * Readiness for audits Show less
-
-
-
Berlin Packaging Denmark A/S
-
Denmark
-
Packaging and Containers Manufacturing
-
1 - 100 Employee
-
Injection moulding technician/ LEAN Navigator
-
2010 - Apr 2012
I was employed 3 days a week to do injection moulding, and 2 days for implementing LEAN. * Setting up tools and related equipment for production * Correct errors on running production * Optimize on running production * Was educated in LEAN *Started up 5S * VSM on several products * SMED projects * Focused on OEE and KPIs I was employed 3 days a week to do injection moulding, and 2 days for implementing LEAN. * Setting up tools and related equipment for production * Correct errors on running production * Optimize on running production * Was educated in LEAN *Started up 5S * VSM on several products * SMED projects * Focused on OEE and KPIs
-
-
-
Ulstrup Plast A/S
-
Denmark
-
Plastics Manufacturing
-
1 - 100 Employee
-
Lærling plastmager
-
Apr 2006 - Apr 2010
-
-
Education
-
Den Jyske håndværker skole i Hadsten
Vocational, Plastic Injection Moulding -
Teknologisk Institut Århus
LEAN Navigator - Production -
Copenhagen Business Academy
Project Management, Project Management -
Teknologisk Institut Tåstrup
Project Management, 3 days of training, theory and assignments based on cases
Community
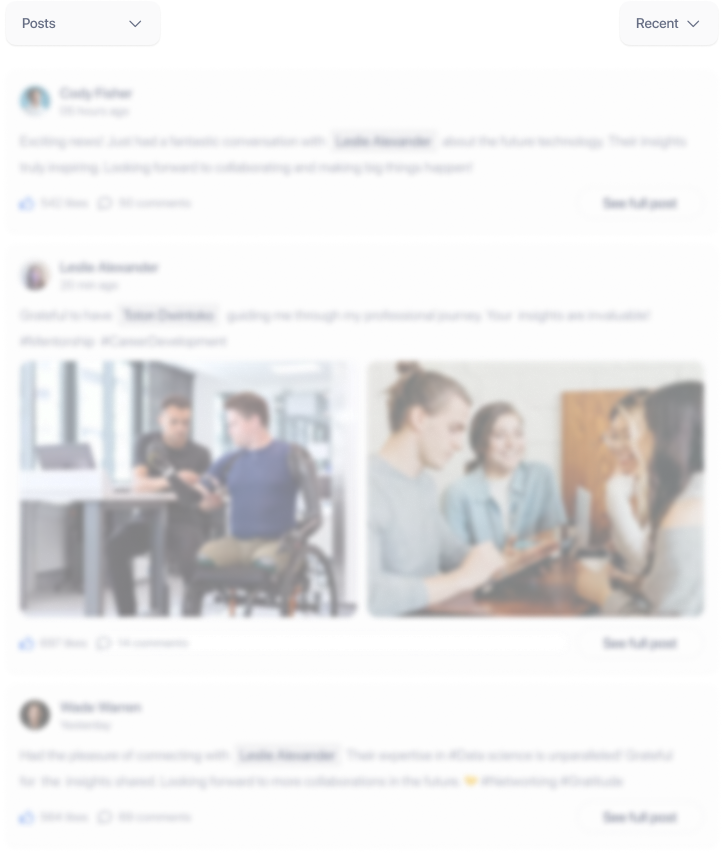