Melvin Sanabria
Senior Supply Chain Manager at Red Collar Pet Foods- Claim this Profile
Click to upgrade to our gold package
for the full feature experience.
-
Spanish -
Topline Score
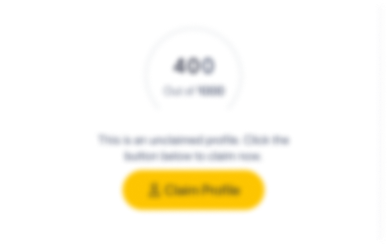
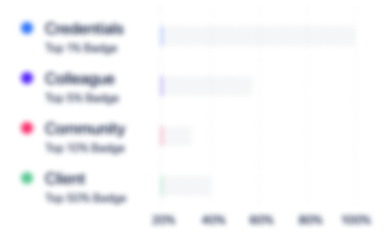
Bio


Credentials
-
Engineer Intern
Florida Board of Professional EngineersMar, 2010- Oct, 2024
Experience
-
Red Collar Pet Foods
-
United States
-
Food and Beverage Manufacturing
-
1 - 100 Employee
-
Senior Supply Chain Manager
-
Dec 2018 - Present
-
-
-
Mars
-
United States
-
Design Services
-
1 - 100 Employee
-
International Supply Chain Operations Manager
-
Jul 2015 - Nov 2018
Responsible for team of professional associates responsible for our international affiliate business valued at $306 million dollars in annual sales, shipping over 1200 skus across 11 brands to 54 different countries. Responsibilities include associate coaching and development, team building, innovation/change project management, international demand planning, supply chain operations, ocean freight transportation set-up, affiliate specific inventory, customs clearance documentation, and inter-company invoicing processes. Show less
-
-
Affiliate Activity Manger
-
Jan 2015 - Jul 2015
Manage international affiliate projects for products sold in export markets but produced on US production assets. Included leading cross-functional teams to work through all supply chain and export set-ups and challenges to ensure a timely product launch to help export markets achieve targeted growth rates. The cross-functional team includes members from in-country marketing, export analysts, commercial buyers, operations planners, and financial experts. Established and nurtured customer relationships with international Mars affiliate businesses to grow our affiliates’ in-country businesses. Also hold regular connection meetings to create efficiencies and ensure mutual treatment of each business units that compete for product with other US customers. Responsible to proactively communicate and work through all product portfolio changes that impact Mars international affiliate businesses across all Mars brands from Pedigree all the way to recently acquired Iams and Eukanuba brands. Mars international affiliates stretch as far North to Canada, as far South to Argentina and as far East as Australia. Promoted to team manager within 6 months in role. Show less
-
-
Shift Manager
-
Feb 2012 - Jan 2015
Currently coach and manage a 20 associate team in daily operations in 4-shift 7 days/week operation with primary focus on safety, food safety, quality, efficiencies, development, and team engagement. Led team over a two year transitional period where the plant capacity doubled from 7k to 14k tonnes/period, from a 3 shift, 5 day/week operation into the current state.
-
-
-
Tropicana
-
Retail Apparel and Fashion
-
Packaging Operations Supervisor
-
Mar 2010 - Feb 2012
•Supervised a 31 person crew of union operator mechanics which included 5 union stewards•Executed the launch of 3 new Trop 50 + Tea juice flavors adding an additional 20M cases/week capacity•Led a changeover parts project that expanded the capacity of UFO line 4 by 20%. •Assumed the duties of the department manager in his absence for extended periods of time for 110 employees•Responsible for department sanitation schedule of all 4 department production lines•Organized and managed union shift bump season transition that impacted all 3 shifts and 25 employees Show less
-
-
Supply Chain Associate
-
Feb 2009 - Mar 2010
Responsible for identifying and driving out operational inefficiencies through three different packaging departments and varying technologies; from cartons, PET plastics to clear blow-modeled plastics.•Saved $80,000/year savings by reducing true efficiency (TE) losses due to minor stops from 12.5% to 9.7% across the plant•Saved $10,000/year by leading CB3 line drumbeat team to reduce minor stops from 15% down to 7%•Saved $10,000 worth of pulp by rearranging scheduling needs while communicating across processing and warehouse functions during an off shift•Implemented electronic centerline (review and response) process on 8 production lines and trained hourly team members on data entry to provide an additional autonomous maintenance (AM) tool Show less
-
-
-
Procter & Gamble
-
United States
-
Manufacturing
-
700 & Above Employee
-
Packaging Operations Intern
-
Jun 2008 - Aug 2008
•Led quality rework procedures to determine the disposition of $60,000 worth of product •Reduced filler standard deviation from 2.0 g to 1.0 g using statistical capability analysis tools during start-up of a recently relocated production line •Documented 7 critical validation processes for packaging with agreement from quality group •Led quality rework procedures to determine the disposition of $60,000 worth of product •Reduced filler standard deviation from 2.0 g to 1.0 g using statistical capability analysis tools during start-up of a recently relocated production line •Documented 7 critical validation processes for packaging with agreement from quality group
-
-
-
-
Packaging Operations Intern
-
Jun 2007 - Aug 2007
• Reduced filler changeover time by 30% resulting in a $14,000 a year cost savings by leading a Rapid Improvement Event (RIE) •Trained 15 technicians on 3 shift on new rapid changeover procedures •Reduced scrap and waste by 22% by introducing a new pump and reducing unnecessary hosing length for a concealer make-up production line. • Reduced filler changeover time by 30% resulting in a $14,000 a year cost savings by leading a Rapid Improvement Event (RIE) •Trained 15 technicians on 3 shift on new rapid changeover procedures •Reduced scrap and waste by 22% by introducing a new pump and reducing unnecessary hosing length for a concealer make-up production line.
-
-
-
Pratt & Whitney
-
United States
-
Aviation and Aerospace Component Manufacturing
-
700 & Above Employee
-
Overhaul and Repair Co-Op
-
Jan 2007 - May 2007
-
-
-
-
Distribution Summer Intern
-
May 2006 - Aug 2006
•Created and implemented a semi-automated results metric database system for management daily KPI review using Microsoft access database software •Trained 15 people on the results metrics database operation and data entry •Corrected inventory discrepancy and reduced rework by 5% using Focused Improvement (FI) tools to discover a procedural discrepancy •Created and implemented a semi-automated results metric database system for management daily KPI review using Microsoft access database software •Trained 15 people on the results metrics database operation and data entry •Corrected inventory discrepancy and reduced rework by 5% using Focused Improvement (FI) tools to discover a procedural discrepancy
-
-
Education
-
University of Florida - Warrington College of Business
Master of Business Administration (M.B.A.), General Business -
University of Florida
BS, Mechanical Engineering
Community
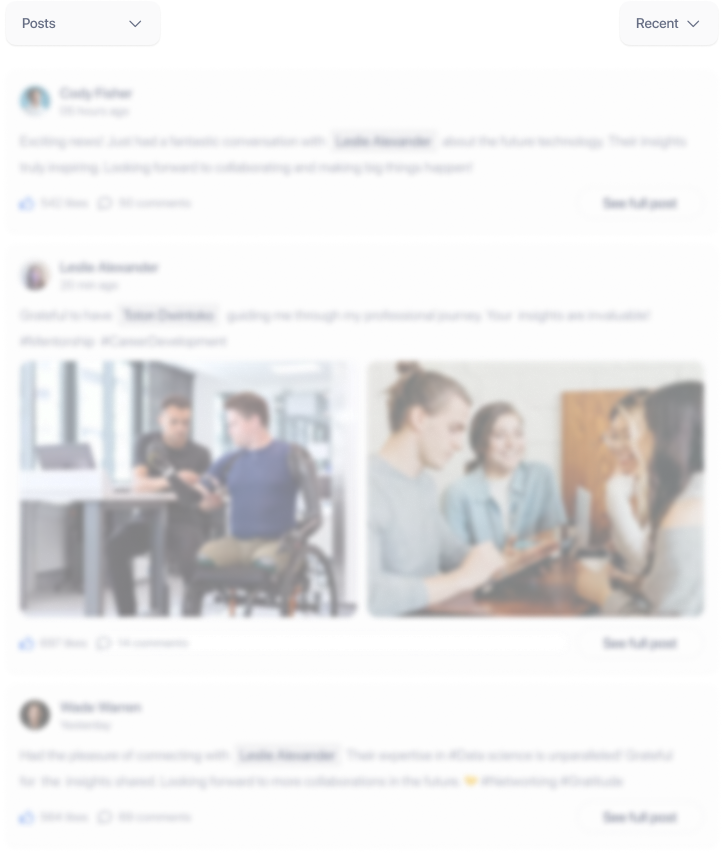