Mehmet Irmak
Supply Chain Executive at doremusic- Claim this Profile
Click to upgrade to our gold package
for the full feature experience.
-
English Full professional proficiency
-
German Professional working proficiency
Topline Score
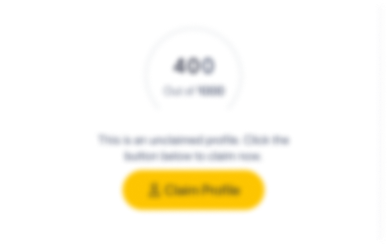
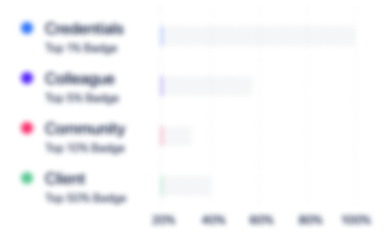
Bio


Experience
-
doremusic
-
Türkiye
-
Music
-
1 - 100 Employee
-
Supply Chain Executive
-
Aug 2015 - Present
-
-
-
-
Managing Partner
-
Oct 2012 - Jul 2015
-
-
-
Arzum
-
Türkiye
-
Retail
-
Supply Chain Director
-
Mar 2011 - May 2012
Turkish Small Domestic Appliances Brand operating in 4 countries (Turkey, Hong Kong, Germany, Macedonia), Market Leader in Unit, #4 in Value in the Turkish SDA Market. Supply Chain Director Responsible from Logistics, Purchasing and Quality Assurance Direct Reports: Logistics Manager, Purchasing Manager – Turkey & Europe, Purchasing Manager Far East , Quality Assurance Manager Logistics Management of demand planning & supply planning. Organization of Customs Clearance, Import & Export Operations. Management & Organization of inbound & outbound logistics Planned & implemented distribution project to achieve a % 17 saving with minimum negative effect on service level Implemented new KPI’s & reporting procedure. Purchasing Managing the Purchasing Teams in İstanbul & Hong Kong Organizing purchasing activities with 70 suppliers in Far East and 18 Suppliers in Turkey & Europe. Organization of Sourcing activities according to Sales & Marketing needs Initiated the Supplier Consolidation Project, to increase purchasing power and decrease complexity and inefficient workload of the purchasing team. Initiated the Supplier Evaluation Project to prepare a quarterly “objective – measurable” supplier evaluation report. Quality Assurance Managing a Quality Team of 6 people (4 Turkey, 2 Hong Kong) Implemented the Registration & Technical Documentation Process to improve the customs clearance process. Made agreements with 3’rd party test organizations to conduct audit and inspection activities. Organized the preparation of the quality handbook and supplier handbook. Improved the test labs of Turkey and Hong Kong to match the test capacity needed. Show less
-
-
-
-
•Asst.Gen.Manager, Operations
-
Aug 2010 - Mar 2011
Turkish Intercity Coach Operator serving 12,000,000 passengers annually with a fleet of 400 busses.. Assistant General Manager (Operations) Responsible from Operations Direct Reports: Area Operations Managers, Operations Support, Quality &Audit Manager , Maintenance Manager, Purchasing Manager, Network Planning & Reporting Specialist Fleet Planning & Management Planning the seasonal fleet capacity. Managing the own fleet & arranging contracted busses. Organization of bus scheduling and micro planning Network Planning Making the yearly plans for network expansion and new routes Organization of terminals, sales offices and busses for new routes prior to launch. Purchasing Organization of the fleet purchases, catering purchases and maintenance purchases. Using the purchasing power, changed the purchasing function from a cost center to a profit center by selling catering and maintenance supplies not only to contracted busses, also to other coach companies. Operations Support, Quality & Audit Organized preparation of the New Quality Operations Manual. Launched trainings and audits according this handbook. Planned and implemented GPS System to the whole fleet (including transfer shuttles) and created a GPS based Operations Center. Maintenance Organized yearly maintenance plans for the own fleet. Made maintenance agreements with bus producers and decreased maintenance costs by 20% with periodical maintenance and high volume spare parts procurement. Show less
-
-
-
Horoz Logistics
-
Türkiye
-
Transportation, Logistics, Supply Chain and Storage
-
700 & Above Employee
-
Sales Director Warehousing & Distribution (3.PL)
-
Jan 2010 - Aug 2010
Turkish Integrated Logistics Solution Provider with a yearly revenue of $370,000,000 Sales Director Responsible from the Sales of Warehousing, Customs Brokerage, Inland Distribution (Micro Distribution, FTL distribution) Direct Reports: Key Accounts Manager, Warehousing Sales Manager, Inland Micro Distribution Sales Manager, Inland FTL Distribution Sales Manager, Customs Brokerage and Bonded Warehousing Sales Manager, Project Manager. Show less
-
-
-
Oriflame Cosmetics
-
Switzerland
-
Personal Care Product Manufacturing
-
700 & Above Employee
-
Operations Director
-
Feb 2003 - Feb 2009
Swedish Cosmetics Company selling direct, present in 61 countries. Responsible from Supply Chain Management. Direct Reports: Warehouse Manager, Customer Service Manager, Distribution Supervisor, Stock Control Supervisor, Imports & Purchasing Specialist. Inventory control Decreased inventory from 145 days to 62 days in an environment of more than 2000 SKU’s and monthly 20 launches and discontinuations on average. Imports planning and implementation Responsible from imports operations and close coordination with registration processes. Outsourced bonded warehouse, which led to an annual saving of €18,000 and created additional 800 pallet space in the warehouse without any additional cost. Warehousing and Pick & Pack operations Decreased the delivery lead time to max 48 hours after order without cost increase through implementation of a new shift & control system. Distribution Planning & Distribution Increased home delivery percentage from 12% to 53% of orders, while maintaining the same cost/net sales ratio. Customer price for home delivery decreased by 25% and the order limit for free delivery decreased by 50%. Negotiated a new price scheme, which helped decrease courier prices dramatically. Purchasing & third party relations Mainly concentrated on replacing of centrally sourced accessories and local production of printed materials. Additionally is responsible from all purchasing activities of the company. On-line project (Website & on-line ordering) - Implemented in Nov’03 Orders via internet reached 85% of total orders in a country with only ~20% internet penetration. Credit card payment solution implemented in March 2006 (first market in Oriflame world). Show less
-
-
-
FHP
-
Germany
-
Industrial Machinery Manufacturing
-
1 - 100 Employee
-
Operations Manager
-
1998 - 2003
German cleaning & household products company known for its “Vileda”, “Wettex” brands. Responsible from Supply Chain Management Direct Reports: Warehouse Manager (3PL), Distribution Supervisor (3PL), Stock Control, Imports & Purchasing Specialist. Developed and implemented the outsourcing project: Converting and distribution operations have been outsourced to a third party logistics company. As a result of this project, the cost of goods sold declined by 6 percent and the project was presented as “best practice” among the FHP Group. Lead and managed “Sponge Production Localization” project, which resulted in €110,000 savings annually in 2003. The project stages were; searching for local producers, price negotiations, preparing technical specifications, sample production, and testing, qualification, approval and signing of the contract. Responsible from the supply chain management: Planning and management of production and distribution operations Materials Requirement Planning: Preparation and implementation of procurement plans for raw materials/finished goods; inventory management Management of imports activities Managing registration processes and relationships with government authorities (Ministry of Health, Customs Authorities…) Negotiations with the suppliers of raw materials/finished goods. Management of relationships with sub-contractors Managing implementation of quality assurance system Regular update of the supplier database Also responsible for management of IT operations Reduced the average operation cycle from 167 days in 1998 to 52 days by the beginning of 2000 while increasing the customer service level from 40% to 97% within the same period, which contributed to the success of The Company in achieving market leadership position for the first time ever since its establishment Show less
-
-
-
General Electric
-
Canada
-
Machinery Manufacturing
-
1 - 100 Employee
-
Logistics Supervisor
-
1995 - 1998
Preparation of monthly & annual production and material requirement plans in coordination with the Sales and Production Departments. Determination of weekly production and import levels based on monthly plans, the on-going sales performance and current inventory levels. Evaluation of current suppliers with regard to their past performance in terms of timeliness, quality and price; selection of the optimum set of material suppliers. Preparation and implementation of the annual purchasing agreements with major suppliers. - Bar-Code Project: Adapted a bar-code system for warehousing operations. The system reduced the number of incorrect shipments from 15% to 0% - Warehouse Layout Plan: Designed new layout plan of the warehouse. The new plan resulted in a 20% increase in storage capacity and provided easier access to the required inventory. ISO-9002 Quality Assurance Project: Leader of the Logistics Team of ISO-9002 Project. Show less
-
-
-
Gölcük Naval Shipyard
-
Appliances, Electrical, and Electronics Manufacturing
-
1 - 100 Employee
-
Submarine Planning Corporal
-
1994 - 1995
-
-
Education
-
Orta Doğu Teknik Üniversitesi / Middle East Technical University
BS, Industrial Engineering -
Orta Doğu Teknik Üniversitesi / Middle East Technical University
BS, Industrial Engineering
Community
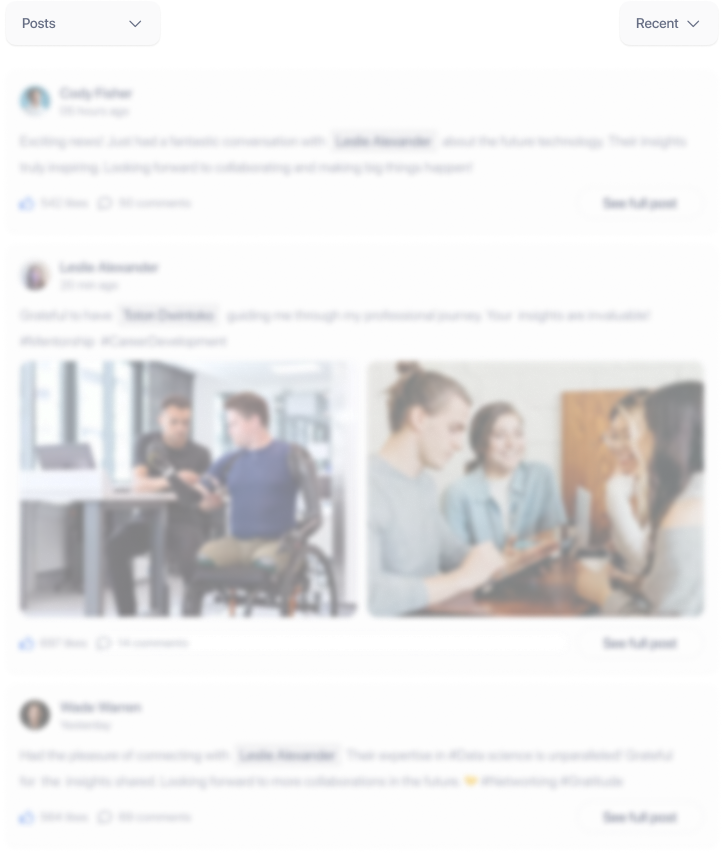