Megan LeBaker
Production Supervisor at Elemental LED Inc.- Claim this Profile
Click to upgrade to our gold package
for the full feature experience.
-
English Native or bilingual proficiency
Topline Score
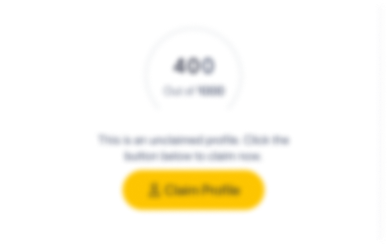
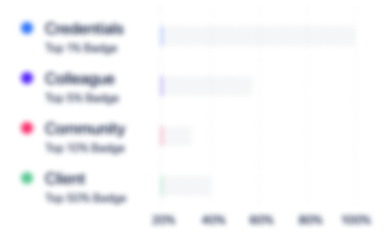
Bio


Experience
-
Elemental LED Inc.
-
United States
-
Appliances, Electrical, and Electronics Manufacturing
-
1 - 100 Employee
-
Production Supervisor
-
Jul 2021 - Present
• Work cross functionally to successfully manage large and special projects, driving new divisions of the business forward. • Set up cross training and employee training schedules making sure the department has coverage and growth for all areas. • Created metrics measuring employee productivity, on time delivery, and supply chain impacts. Allowing for better analysis of areas needing improvement in the department. • Manage a team of 30 direct reports, ensuring a culture of efficiency and positivity. resulting in improved on time delivery and transparency across the business. • Overhauled Manufacturing inventory resulting in accurate stock levels and furthering efficiency targets for material pickin Show less
-
-
-
Elemental LED Inc.
-
United States
-
Appliances, Electrical, and Electronics Manufacturing
-
1 - 100 Employee
-
Production Scheduler
-
Dec 2020 - Apr 2021
• Created workcells to promote improved quality, productivity, and streamlined processes. • Created a scheduling process including daily schedules that could be flowed down to work cells and used cross functionally resulting in improved on time delivery and transparency across the business. • Overhauled Manufacturing inventory resulting in accurate stock levels and furthering efficiency targets for material pickin • Created workcells to promote improved quality, productivity, and streamlined processes. • Created a scheduling process including daily schedules that could be flowed down to work cells and used cross functionally resulting in improved on time delivery and transparency across the business. • Overhauled Manufacturing inventory resulting in accurate stock levels and furthering efficiency targets for material pickin
-
-
-
IGT
-
United Kingdom
-
Software Development
-
700 & Above Employee
-
Production Master Scheduler III
-
Oct 2019 - Dec 2020
• Ensure new customer and product integration is successful through leading cross functional project teams.• Work alongside international teams to plan and schedule their forecasted demand and ensure flexibility to maintain OTD.• Reduce inventory values and labor resources utilizing uncommitted inventory.• Modernized the shipment process for Electronic Table Games, resulting in fewer errors and a more efficient audit process.
-
-
Master Scheduler II
-
Mar 2018 - Oct 2019
• Have been able to work closely with cross function teams to reduce software Inventory by $130k. This was done by more regular cycle counts, recovering scrap, and review data to clear old stock.• By working underutilized reports and employing support teams we ensured more accurate and on releases of future demand, resulting in an increase of OTD by 5%.• Streamlined several processes for a more concise and effective way of managing business processes.
-
-
-
Ebara International Corporation, Cryodynamics Division
-
United States
-
Oil and Gas
-
1 - 100 Employee
-
Supply Chain Manager
-
Feb 2016 - Mar 2018
• Exceeded YoY goal in cost and lead time reductions by initiating negotiations with key suppliers. • Reduced inventory levels 40% by utilizing forecast data to determine obsolescence and future consumptions. • Conduct data analysis to interpret areas for cost savings, productivity improvements, and inventory reductions. • After a reduction in force, acquired responsibility of customer service and sales. Resulting in a 13% gross profit improvement • Exceeded YoY goal in cost and lead time reductions by initiating negotiations with key suppliers. • Reduced inventory levels 40% by utilizing forecast data to determine obsolescence and future consumptions. • Conduct data analysis to interpret areas for cost savings, productivity improvements, and inventory reductions. • After a reduction in force, acquired responsibility of customer service and sales. Resulting in a 13% gross profit improvement
-
-
-
PCC Structurals, Inc.
-
United States
-
Aviation and Aerospace Component Manufacturing
-
700 & Above Employee
-
Front End Operations Manager
-
Aug 2015 - Feb 2016
• Oversaw all daily operations, P&L management, inventory management and process improvements of 3 departments while managing 80 direct reports over two shifts.• Implemented lean inventory procedures, and reduced inventory discrepancies by 40%.• Reduced overtime by 15%, resulting in a monthly savings of $20K, by conducting hands on training and process improvement initiatives.
-
-
Area Manager
-
Jun 2014 - Aug 2015
• Successfully implemented and streamlined work processes that increased department productivity by 16%.• Directly responsible for a 12% reduction in department operating costs after enhancing operational efficiencies. • Consistently achieve daily, monthly and quarterly targets by effectively outlining targets and budgets with management.
-
-
-
Arconic
-
United States
-
Manufacturing
-
700 & Above Employee
-
Operations Manager
-
Feb 2013 - Jun 2014
• Oversaw a $90M annual ship plan with a consistent commitment to achieve sales goals.• Managed all purchasing and inventory while overseeing the daily work of four departments and 16 direct reports. • Launched innovative process improvement guidelines and meetings that reduced waste by 20% in five high-volume areas.
-
-
Production Control Supervisor
-
Sep 2011 - Feb 2013
• Oversaw production control including order releases, raw materials purchasing and outside processing positions. • Saved over $20K annually by implementing leasing and consignment contracts with key suppliers.• Led the company through two consecutive years of yearly inventory with no write-offs by successfully initiating an increased cycle count program for high dollar inventory.
-
-
Production Control Coordinator
-
Jul 2007 - Sep 2011
• Oversaw all logistics between plants in Nevada and California, and movement within each state, including the negotiating of transportation agreements and pricing and the scheduling of all transportation to and from each plant. • Created templates for shipping and receiving to use to verify products were shipped and received as needed. • Successfully managed supplier matrix's to ensure on-time delivery to customers, resulting in an 85% on-time delivery rate.
-
-
Education
-
University of Phoenix, Reno, NV
Bachelor of Science (BS), Business Administration and Management, General
Community
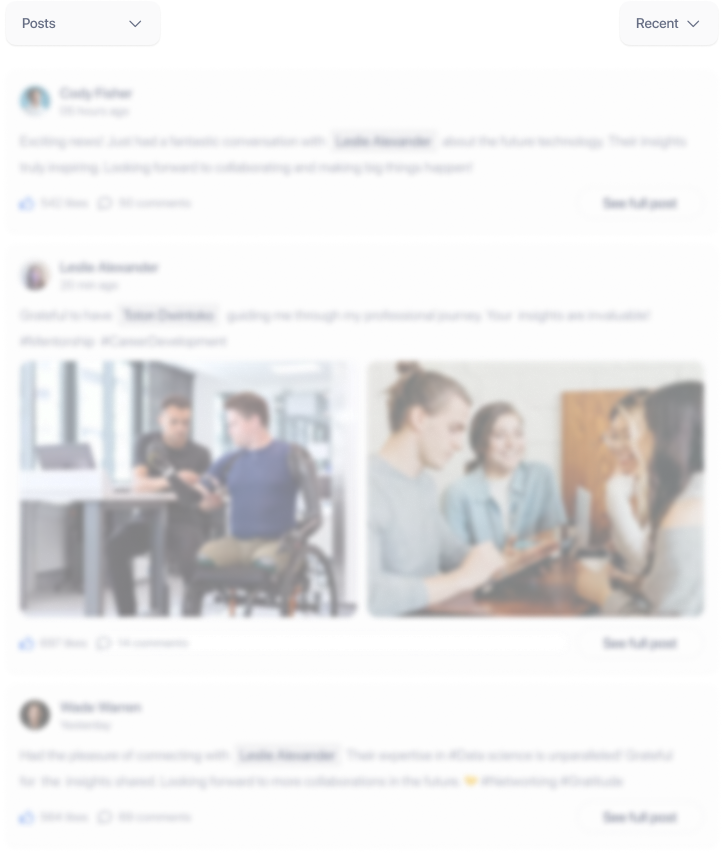