Meagan Bellinger
QA/QC Manager at Zazula Process Equipment Ltd- Claim this Profile
Click to upgrade to our gold package
for the full feature experience.
Topline Score
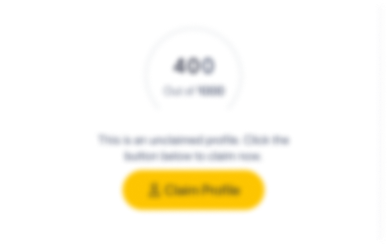
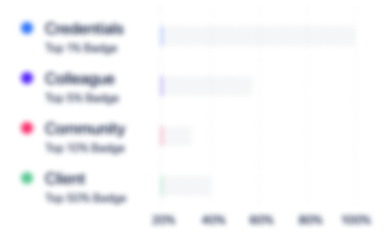
Bio


Experience
-
Zazula Process Equipment Ltd
-
Canada
-
Industrial Machinery Manufacturing
-
1 - 100 Employee
-
QA/QC Manager
-
Jan 2019 - Present
• Support Project Managers in dealing with Clients for all Quality related matters. • Prepare, obtain approval, issue and implement company quality control (assurance) program manual in compliance with owner contract and company requirements • Assess the implementation of the Quality Control Plans for each awarded job. • Manage and direct activities and resources of the quality control department to meet company objective of producing highest quality product within established budget. • Ensure product is manufactured in accordance with contract/client specifications and codes • Supervise/Conduct inspections, reports and documentation and file the required Quality Records. • Review all NDE reports and film for any code discrepancies and to ensure accuracy • Review MTR’s and ensure code compliance for all job-related materials received. • Evaluate the qualifications of welders and Non-Destructive Test-NDT technicians with regard to the activities assigned. • Evaluate the qualifications of inspection personnel. • Support the construction roles in the management and control of subcontractors. • Support and participate in all the internal/external audits. • Coordinate the relevant Tracking Systems for correct identification of materials. • Maintain materials equipment and instruments related to manufacturing and testing of product in conformance with all regulatory codes and specifications; Ensure up to date calibration certs/logs. • Support the Welding & Non-Destructive Test-NDT qualification activities. • Review/Implement all new Welding Procedures approved by governing authorities. • Address and implement resolution for all non-conformities. • Supervise/Inspect repaired weld defects and ensure proper testing is complete. Show less
-
-
-
Startec Compression & Process and Startec Service
-
Canada
-
Oil and Gas
-
100 - 200 Employee
-
QA/QC Administrator / Inspector
-
Feb 2018 - Jan 2019
• Support site supervisors, project managers, foreman, Trades personnel and other project personnel with quality assurance/control requirements and documentation • Visual inspections/Final Dimensional checks of Pressure Vessels/piping prior to PWHT/Hydrotest • Prepare manufacturer’s Data Record (MDR) for ASME Stamped Vessels and AB-83 for piping. • Review of relevant documents, procedures, vendor Specs to ensure they comply to Client Specs., Codes, Standards • Implementation of QC Manual & ITP and maintenance of standards procedures, WPSand welders qualification. • Ensure compliance with QA Standards & procedures including proper QC document control • Co-ordinate and qualify required WPS’s and Welders for the assigned projects. • Witness hydro testing of pressure vessel, pipe spool and valve as per approved hydrotest procedure • Witnessing/Monitoring of NDT, PWHT, calibration of Instruments as well as interpret welds/drawings, and review of other NDT & PWHT Reports inquisitive • Identify and report non-conformities to specified requirements. • Consolidate punch list for plant system exception lists and provide tracking to ensure that all punch list items are captured and signed off for mechanical completion • Full Review of Final Hand-Over Documentation such as Quality Assurance Record Book-Site records, Mechanical Catalogue Book, Manual/Data Book, to ensure they comply to Client Requirements and Contract. Show less
-
-
-
-
QA/QC Administrative Manager
-
Jan 2016 - Jan 2018
• Managed multimillion dollar projects with staff of ten or more people for each assigned project • Performed quality assurance functions to accomplish project coordination, monitoring, and reporting • Liaised, established and maintained open and continuous lines of communication between project management, owner, contractors, and other project participants. • Assigned, reviewed, and evaluated the work of professional, technical, and clerical staff • Interpreted and implemented quality assurance standards, and client requirements • Ensured that all projects were delivered on-time, within scope and within budget • Developed project scopes and objectives, involving all relevant stakeholders and ensured technical viability • Developed a detailed project plan to track progress and ensure resource availability and allocation • Used appropriate verification techniques to manage changes in project scope, schedule and costs • Measured project performance using appropriate systems, tools and techniques • Recruited specialists and sub-contractors • Generated marketing strategies to promote products and services • Procured project materials and inspected and verified materials upon delivery • Established, maintained and managed relationships with clients, vendors and all stakeholders • Created and maintained comprehensive project documentation Show less
-
-
-
WSP in Canada
-
Canada
-
Professional Services
-
700 & Above Employee
-
Supply QA/QC Coordinator
-
Oct 2013 - Nov 2015
• Managed projects with staff of twenty or more people • Performed quality assurance functions to accomplish project coordination, monitoring, and reporting • Assigned, reviewed, and evaluated the work of professional, technical, and clerical staff • Interpreted and implemented quality assurance standards, and client requirements • Performed cost benefit analysis through monitoring unusual occurrences or budget variances and reported on results to determine and implement actions where necessary • Reported follow-up procedures, researched and compiled statistical data, and provided narrative reports summarizing quality assurance findings for each client and project lead • Reviewed testing, QC documents, and other NDE examination reports for accuracy, completeness and compliance to ensure that QA standards, codes and regulatory requirements were met • Provided administrative assistance to all clients, vendors and internal departments • Conducted client/vendor meetings to ensure compliance to client purchase agreements and requested end of job documentation as well as issued, monitored and closed out all NCR’s • Maintained all project quality records as well as detailed budgeting costs • Compiled spreadsheets for each completed project and managed the company database • Recruited vendors and inspectors and assigned to appropriate client projects • Completed routine inspections of vendor shops, project materials/consumables and final assembled Packages prior to shipping • Managed all assigned projects and liaised between inspectors, vendors and clients to ensure accuracy and thorough completion on all projects Show less
-
-
Education
-
CWB Welding Institute
Welding Inspectors Level 1 Certification, welding
Community
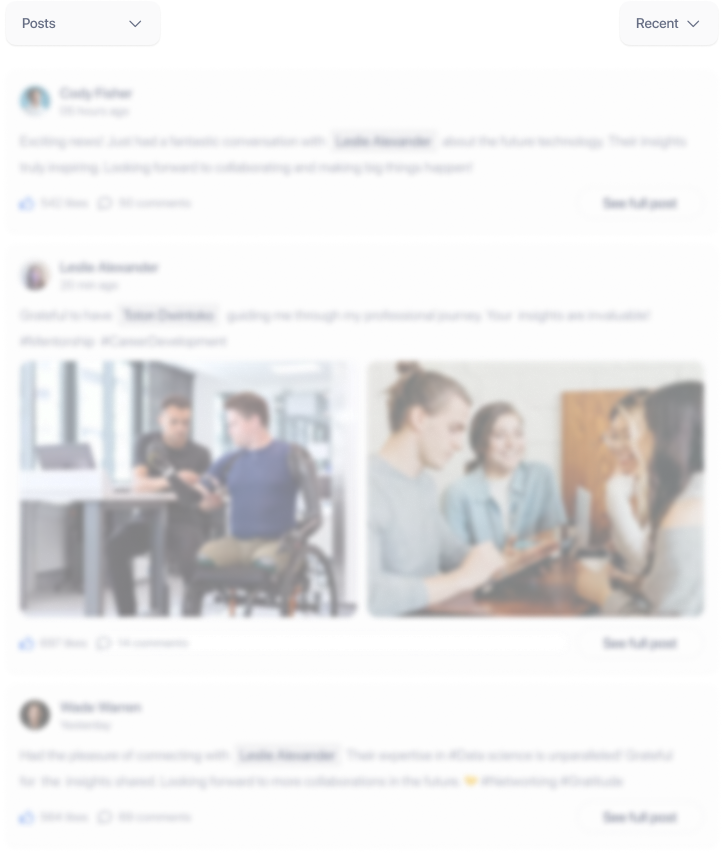