Matthew Markland
Senior Validation Engineer at Hughes Engineering, PLLC- Claim this Profile
Click to upgrade to our gold package
for the full feature experience.
-
English Native or bilingual proficiency
Topline Score
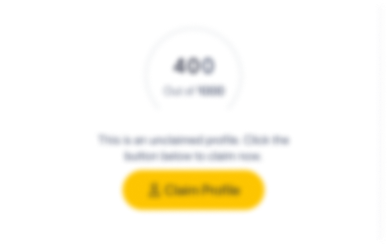
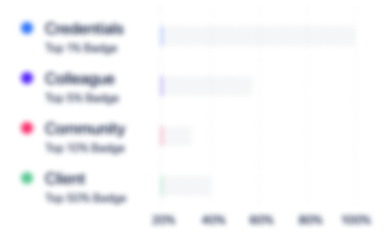
Bio


Experience
-
Hughes Engineering, PLLC
-
United States
-
Business Consulting and Services
-
1 - 100 Employee
-
Senior Validation Engineer
-
Dec 2022 - Present
Senior Validation Engineering Consultant working on various Client projects in the North Carolina / Virginia Area. Senior Validation Engineering Consultant working on various Client projects in the North Carolina / Virginia Area.
-
-
-
AMPAC Fine Chemicals
-
United States
-
Pharmaceutical Manufacturing
-
300 - 400 Employee
-
Senior Quality Engineer
-
Jan 2019 - Nov 2022
● Lead Equipment and Automation Qualification Efforts for Multiple Building reactivations from idled state ● Site Performance Process Validation Engineer for API Manufacturing ● Assisted with Process Engineering for Equipment and Process Reactivations ● Main site contact for Document Management System (MasterControl) ● Responsible for System Documentation for Control System (DeltaV) Upgrades and Modifications ● Participated in Greenfield Construction project Qualification Documentation and Review Show less
-
-
-
Tate Engineering Systems, Inc
-
United States
-
Mechanical Or Industrial Engineering
-
1 - 100 Employee
-
Project Manager
-
Nov 2018 - Jan 2019
Project/Construction manager for boiler installation at a client's site. Project/Construction manager for boiler installation at a client's site.
-
-
-
Abbott
-
United States
-
Hospitals and Health Care
-
700 & Above Employee
-
Project Manager
-
Aug 2017 - Oct 2018
+Manager and Engineer over multiple projects to determine and increase capacity and operational efficiency at SAMHSA certified Drug Toxicology Labs. +Managed site’s safety and environmental programs +Managed multi-site safety programs and data acquisitions for corporate reporting +Developed divisional contractor safety program and associated safety documentation. +Manager of division’s Business Continuity plan, including a easing the use of the current documentation +Manager of key client transferring of business which lead to demand increase of 10% Show less
-
-
-
Sun Chemical
-
United States
-
Chemical Manufacturing
-
700 & Above Employee
-
Production Supervisor
-
Mar 2016 - Aug 2017
+Supervisor of 15 employees at a batch ink manufacturing facility. Majority of the production is for tobacco product packaging and associated printing applications. Production is a mixture of same day shipments and bulk intermediates for internal and external customers. +Developed and updated operating procedures for production employees. +Process optimization for simple liquid blending applications. +Supervisor of 15 employees at a batch ink manufacturing facility. Majority of the production is for tobacco product packaging and associated printing applications. Production is a mixture of same day shipments and bulk intermediates for internal and external customers. +Developed and updated operating procedures for production employees. +Process optimization for simple liquid blending applications.
-
-
-
Ashland Inc
-
United States
-
1 - 100 Employee
-
Production Supervisor
-
Feb 2015 - Nov 2015
CMC Dryside SupervisorFocus on managing 9 employees on finished product blending and packaging for 24/7 production line and maintaining same production line. The production line produces a viscosity modifier for multiple applications under cGMP certifications. Worked with quality system teams and operations to ensure on specification product throughout the process.
-
-
Process Engineer
-
Nov 2011 - Nov 2015
+Support and process engineer for 4 production lines at the facility. Work incorporated troubleshooting and process improvements for each production facility. Each production facility covers different polymer based chemistry. Finished products included powders and liquids for shipment.+Support new product scale up from pilot scale to production facilities within current site and external tolling facilities. +2 Capital Expansion Projects: Lead process engineer of $15 Million new process in a brownfield location Lead process engineer during early stages of $50 Million project to expand a current facility by 50% within processing and building constraints. Both processes are for food and pharma applications, covered by cGMP protocols. Show less
-
-
-
Henkel
-
Germany
-
Manufacturing
-
700 & Above Employee
-
Operations Engineer
-
May 2008 - Nov 2011
Part of Project “MFO” (November 2008-present). +Lead 2 transfer streams from four closing sites, bringing in silver inks and solder paste. Assisted in three additional transfer streams of product from closing sites. Transfer Lead consisted of managing operators in making qualification batches, statistical analysis of batch results versus historical batches from sister plant, and writing white papers for transfer streams. +Project Lead on expansion of Quality Control Lab Building that doubled the building footprint from 3,500 square feet to 7,000 square feet. Work consisted of construction design, consulting with quality department to determine proper layout for equipment and General Contractor on the design and building process. +Process Engineer of equipment transfer from sister sites. Assisted in start up and initial training of operators. Lead writer of equipment operating procedures for new equipment (twenty-eight mixers, four reactors, two Three Roll Mills). +Process Engineer for initial start up of silver inks after qualification period. Assisted operators in early production of batches to meet required specifications. +Process Engineer for Epoxy and Urethane products from sending site. Majority of products are PPAP controlled or UL certified. Work includes basic troubleshooting of Siemens PCS7 control system. Milling and Classifying Engineer +Process Engineer for Milling and Classifying. Responsibilities include troubleshooting specification batches and equipment support. Products consist of powders milled to under 20 microns by use of a jet mill or screened via a vibrating screener. Production occurs 24/5. +Lead transfer of two new products to area requiring start up of new equipment, training operators, and writing equipment operating procedures. Show less
-
-
-
-
Engineering Co-op
-
Aug 2005 - Aug 2008
+Participated in commissioning of plant expansion (EManate) by bringing on line various utility machines. Equipment consisted of 200 ton water chiller, cooling towers, and auxiliary equipment. Wrote and verified operating procedures for equipment. Basic Siemens PCS7 troubleshooting occurred with programming of VFDs installed for the plant expansion. +Assigned as Milling and Classifying Engineer for six months in 2007 with responsibility for assisting in mechanical aspects of equipment (Hosokawa Milling System and Kosher Screeners). Main contributor to two separate Six Sigma projects. Assisted in bringing four new products to the Milling and Classifying area and improved one additional product output capacity by 50% and yield by 33%. +Assisted in routine engineering of resin plant systems, focusing on safety, ergonomics and piping design. Show less
-
-
Education
-
North Carolina State University
B.S., Chemical Engineering -
North Carolina State University
B.S., Chemistry
Community
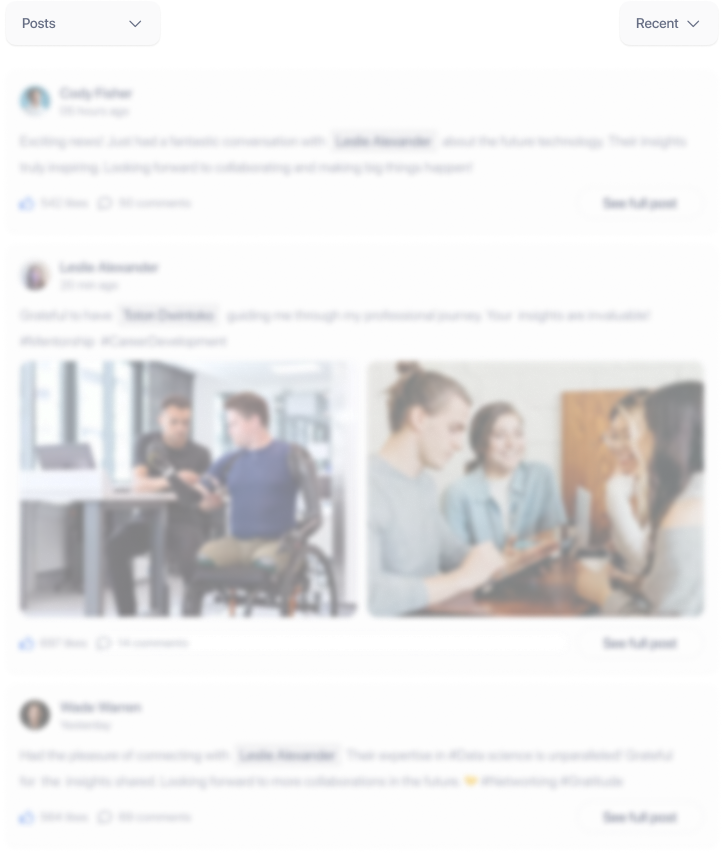