Matthew Grimes
Project Coordinator at Workbox Staffing- Claim this Profile
Click to upgrade to our gold package
for the full feature experience.
Topline Score
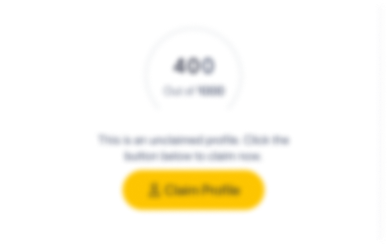
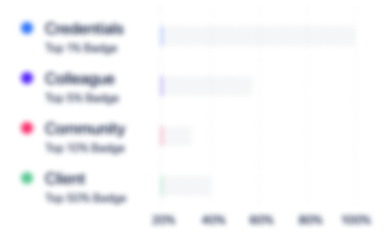
Bio


Experience
-
Workbox Staffing
-
United States
-
Staffing and Recruiting
-
100 - 200 Employee
-
Project Coordinator
-
Jan 2020 - Present
-
-
Payroll/Billing Administrator
-
Oct 2019 - Jan 2020
Collecting timesheet data and payroll information.Entering data into payroll and administrative databases and software programs.Calculating wages, benefits, tax deductions, commissions, etc.Preparing and processing paychecks and cash deposits.Maintaining accurate records of payroll documentation and transactions.Preparing and distributing income statements.Responding to payroll-related inquiries and resolving concerns.Performing account balance and payroll reconciliations.Preparing financial reports for accounting and auditing purposes.Preparing periodic payroll reports for review by management. Show less
-
-
-
Grand Rapids City Hall
-
Grand Rapids
-
Customer Support
-
Jun 2018 - Oct 2019
• Specialized customer support for municipal services • Educated in all city departments including; purchasing, engineering, development, code compliance, water, refuse, fire, environmental, etc. • Scheduling city work for applicable departments • Specialized customer support for municipal services • Educated in all city departments including; purchasing, engineering, development, code compliance, water, refuse, fire, environmental, etc. • Scheduling city work for applicable departments
-
-
-
Gentex Corporation
-
United States
-
Appliances, Electrical, and Electronics Manufacturing
-
700 & Above Employee
-
Cost Analyst
-
Sep 2016 - Oct 2019
Support Commercial Finance team by developing accurate product cost models.Work closely with Sales, Manufacturing, and Program Management.
-
-
Internal Scheduler
-
Mar 2015 - Oct 2019
Construct and manage effective short term capacity plans and inventory sizing for internally supplied components. These actions create production schedules for internal processes which maximize capital equipment efficiency while minimizing system inventory.• Manage conflicting priorities between manufacturing and marketing.• Ensure that Gentex production schedules are pull-based and reflect true customer demand.• Create and maintain a realistic and valid master schedule within the constraints of the production plan and factory capacity through lot-making and inventory management, convert customer pull into a logical production instruction for upstream processes.• Maintain accurate and effective communication with downstream master Schedulers as to product availability and potential shortages.• Prepare and update the sales and operations plan for monthly review by senior management to accurately represent production's role in the strategic business plan for the company.• Create the master production schedule from the marketing forecast and customer orders with a minimum planning horizon of 52 weeks of weekly buckets.• Coordinate with the Production Control Customer Support Specialists to ensure customer orders are shipped on time with a minimum of premium freight expense.• Monitor actual performance against the MPS and production plan and provide status for QMS reporting and improvement.• Drive to root cause of all part shortages and provide/implement corrective actions.• Drive continuous improvement activities for areas of responsibility. Continued focus on customer delivery, product quality and pursuit of ‘One-Piece Flow'. Show less
-
-
MEA Change Coordinator
-
Feb 2014 - Oct 2019
oCoordinate weekly with Schedulers, Program Managers, and Material Manager to ensure knowledge of E-Build events. oCoordinate with Industrial Engineer on any ECO trial parts needed for PPAP builds. oReview TTP orders to ensure timely execution of build requirements and coordination between areas. oPhysically manage and quarantine inventory during launch and engineering changes oResponsible for verifying the presence of all build materials within required manufacturing lead time prior to schedule build; if material is not present, responsible for escalation to cancel builds. oSupport weekly build review meetings with program management team and communicate exceptions. Show less
-
-
Education
-
Grand Rapids Community College
Business Administration, Management and Operations
Community
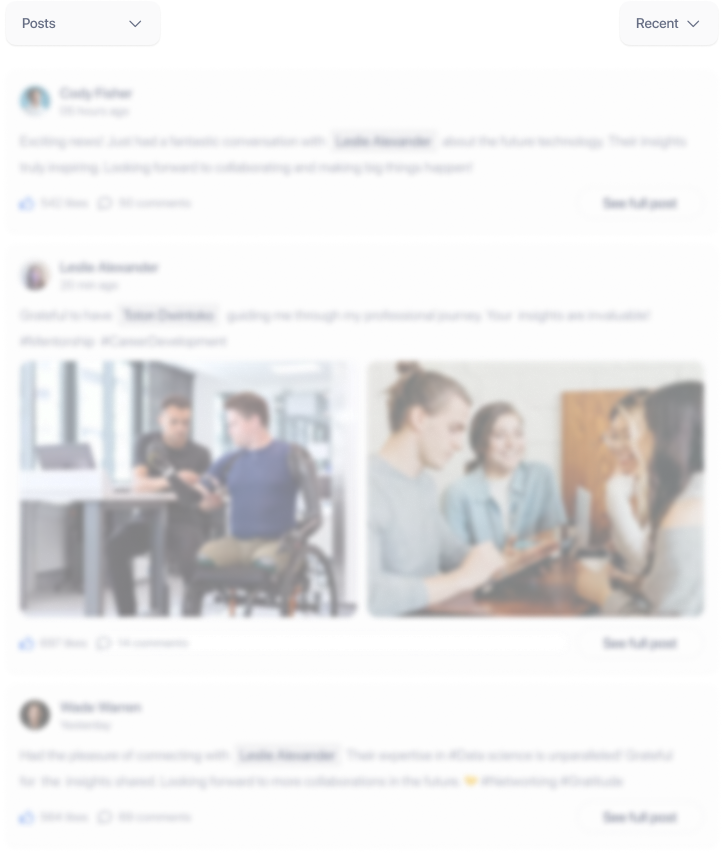