Matthew Cook
Toolmaker at CHALLENGE MANUFACTURING COMPANY PRIVATE LIMITED- Claim this Profile
Click to upgrade to our gold package
for the full feature experience.
Topline Score
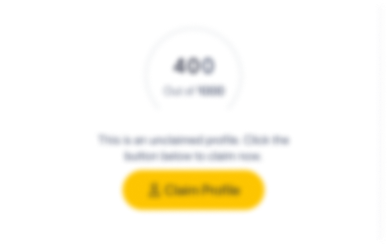
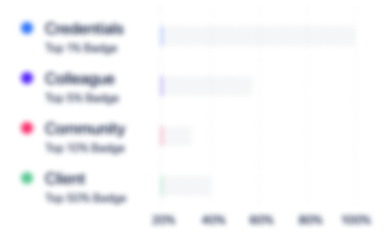
Bio

Jes Salmons
Matt has a strong will to succeed and strives to be the best at every project he works on. He also is very able to self manage and prioritize each project he is working on Simultaneously. I worked directly with Matt in Draw die training and he was always willing to learn something new and try something outside the box to produce a quality product without increasing cost of the product.

Jes Salmons
Matt has a strong will to succeed and strives to be the best at every project he works on. He also is very able to self manage and prioritize each project he is working on Simultaneously. I worked directly with Matt in Draw die training and he was always willing to learn something new and try something outside the box to produce a quality product without increasing cost of the product.

Jes Salmons
Matt has a strong will to succeed and strives to be the best at every project he works on. He also is very able to self manage and prioritize each project he is working on Simultaneously. I worked directly with Matt in Draw die training and he was always willing to learn something new and try something outside the box to produce a quality product without increasing cost of the product.

Jes Salmons
Matt has a strong will to succeed and strives to be the best at every project he works on. He also is very able to self manage and prioritize each project he is working on Simultaneously. I worked directly with Matt in Draw die training and he was always willing to learn something new and try something outside the box to produce a quality product without increasing cost of the product.

Experience
-
CHALLENGE MANUFACTURING COMPANY PRIVATE LIMITED
-
India
-
1 - 100 Employee
-
Toolmaker
-
Oct 2015 - Present
Reported to the Tool Room Supervisor for the proper functioning and repair dies and production of stampings for the automotive industry. Served as lead for second shift and lead other toolmakers in repairing and troubleshooting. Responsible for maintenance of dies and equipment, troubleshooting, press set-up, machine work, and welding. Trained employees in tool repair. Reported to the Tool Room Supervisor for the proper functioning and repair dies and production of stampings for the automotive industry. Served as lead for second shift and lead other toolmakers in repairing and troubleshooting. Responsible for maintenance of dies and equipment, troubleshooting, press set-up, machine work, and welding. Trained employees in tool repair.
-
-
-
Trans-matic
-
United States
-
Individual and Family Services
-
Toolmaker
-
Apr 2010 - Oct 2019
Small deep draw stampings. Small deep draw stampings.
-
-
-
Eden Cryogenics
-
Railroad Equipment Manufacturing
-
1 - 100 Employee
-
Machinist
-
Jul 2009 - Jun 2010
Machine welded pipe assemblies for aerospce industry Machine welded pipe assemblies for aerospce industry
-
-
-
Spartanburg Steel Products
-
United States
-
Motor Vehicle Manufacturing
-
100 - 200 Employee
-
Tooling Engineer
-
May 2008 - Feb 2009
Reported to the Tooling Engineering Manager for the oversight of maintenance and repair for automated tandem press line with a strong focus on dies, tool inspection, blank reduction and all other manufacturing improvements and safety. Directly involved with troubleshooting die issues in production and outside of the press. Press line produced high volume OEM parts for automotive and lawn and garden industries. Worked directly with customers. Implemented preventative maintenance program to reduce customer rejects on exposed automotive panels. Reduced customer rejection to zero for four months. Significantly reduced splits issues on all parts in the press line. Worked with all other departments to resolve press line issues as needed. This included maintenance issues, automated equipment and quality follow up documentation. Worked extensively with Quality Assurance. Increased overall line rate by 25%, creating enough free press time to bring outsourced work back into the press line for significant savings. Led press line improvement team consisting of up to 8 members and organized weekly team meeting to support quality and production requirements focusing on quality, team work, process tracking, tool work, maintenance and inspections. Led by example in all processes. Managed engineering changes for all stamping related issues in the press line, including “hands on” work when necessary. Assisted with the design and manufacture of new tooling including dies and automation tooling. Ensured staff completed all assigned functions correctly and in accordance with policies, procedures, and regulations. Worked with Quality Assurance to meet Customer documentation Requirements. Worked on blank size reduction project to reduce raw material costs for parts. Wrote job instructions for new processes and updated instructions for existing processes. Ensured all proper maintenance (PMs) and tool work were continued on schedule, reducing downtime. Show less
-
-
-
-
Process Engineer
-
Mar 2004 - Apr 2008
Reported to the Engineering Manager for the manufacturing of exposed and unexposed stampings and assemblies for the automotive industry including inspection of new tooling, design of new tooling, design of blanks and blanking processes, creation of packaging processes, and creation of manufacturing processes for stamping, assembly, and shipping operations. Maintained records of production processes and managed all incoming CAD data. Utilized Lean Manufacturing techniques. Worked with sales to create new business. Created manufacturing processes for all incoming stamping jobs in all company facilities. Also responsible for up to 25 %of all assembly and some packaging jobs. Created and maintained blank process sheets, stamping process sheets, assembly process sheets, job instructions and flow charts for over 3000 parts. Created other records as required including Quality Assurance documentation. Collaborated with sales and program coordinators on quoting new work. This included press line choices, die issues, and labor and rate estimation. Traveled to customers to examine new work and evaluate it for suitabilityto the company. Examined dies and assembly processes. Designed and ordered new fixtures and equipment when needed for stampings and assemblies. Worked with Quality and Manufacturing to verify completed fixtures would meet Customer requirements Reduced blank size issues to a minimum Developed blank size and shape when required. Worked with steel purchasing to reduce blank issues. Worked with service and OEM parts and tools from almost every major automotive manufacturer for high volume, low volume and extremely low volume parts. Created a new packing process for overseas shipping of automotive stampings and assemblies in disposable packaging. Monitored and updated production records including all blanking process sheets, flow charts, and assembly process sheets. Maintained and created routes for an MRP system. Show less
-
-
Journeyperson Tool and Die/Repair
-
Feb 1995 - Mar 2004
Reported to the Die Maintenance Supervisor for the repair and maintenance of dies and equipment, troubleshooting, line set-up, machine work and welding. Assisted in training new employees. Completed apprenticeship training in die repair and tryout and became the first graduate of the apprentice program at The Gerstenslager Company. Worked directly with a wide variety of dies including blanking, draw, trim pierce, flange and progressive dies for both exposed and unexposed panels from most major automotive manufacturers. Performed all work necessary to repair dies and associated equipment, including, welding, grinding, machining, surface condition repair and in-line press work. Built fixtures as required. Promoted to Process Engineer. Show less
-
-
-
-
Quality Assurance Technician
-
Jan 1994 - Jan 1995
Responsible to the Supervisor for the proper function of water deionization systems and parts. Tested systems, components and supported production and engineering. Responsible to the Supervisor for the proper function of water deionization systems and parts. Tested systems, components and supported production and engineering.
-
-
-
Lenscrafters
-
United States
-
Retail Apparel and Fashion
-
700 & Above Employee
-
Apprentice Optician
-
Jan 1993 - Jan 1994
Responsible to the Store Manager for selling, repairing, fitting and adjusting eyeglasses Responsible to the Store Manager for selling, repairing, fitting and adjusting eyeglasses
-
-
-
Emro Marketing - Speedway
-
United States
-
Individual and Family Services
-
chain
-
Jan 1992 - Jan 1993
Assistant Manager Assistant Manager
-
-
Education
-
The University of Akron
Mechanical Engineering -
State of Ohio
Journeyprerson Tool and Die -
Wayne County Schools Career Center
Welding,
Community
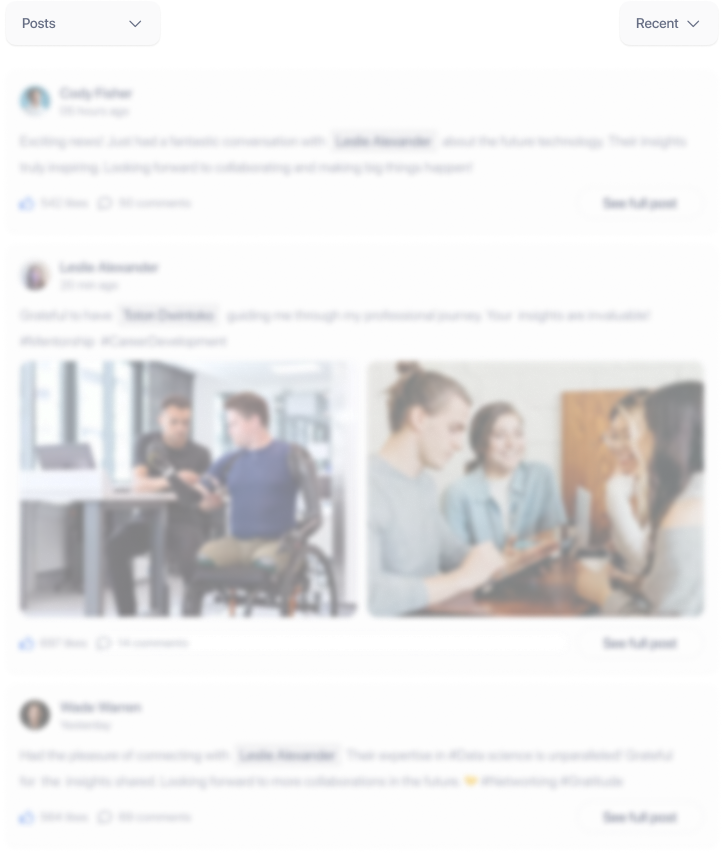