Matthew Bischof
Operations and Service Manager at Vesta Sleep- Claim this Profile
Click to upgrade to our gold package
for the full feature experience.
Topline Score
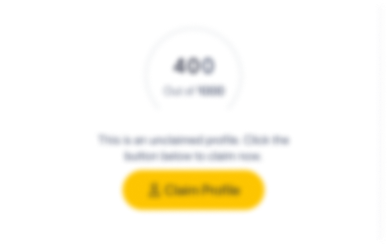
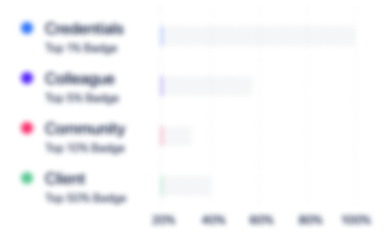
Bio


Experience
-
Vesta
-
United States
-
Manufacturing
-
1 - 100 Employee
-
Operations and Service Manager
-
Feb 2021 - Present
-Manage all daily warehouse personal and assign work activities -Interview and hire new employees -Manage all product distribution in North America and Europe region -Help customers with support issues -Find vendors and create business relationships -Manage inventory and make sure warehouse is stocked on all items for daily functionally -Track business trends and capitalize on business opportunities -Manage all daily warehouse personal and assign work activities -Interview and hire new employees -Manage all product distribution in North America and Europe region -Help customers with support issues -Find vendors and create business relationships -Manage inventory and make sure warehouse is stocked on all items for daily functionally -Track business trends and capitalize on business opportunities
-
-
-
Vincross
-
China
-
Consumer Electronics
-
1 - 100 Employee
-
US Support and Logistics Manager
-
Dec 2017 - Mar 2022
• Manage USA Office for China based company that creates and manufacturers robots for research and educational purposes • Solely managed the HEXA launch into US market which consisted in the distribution and support for over 300+ units • Provide international technical support • Physically repair all robots in North American Region • Create engineering documentation to explain technical procedures • Present robots at marketing events • Interact with engineering teams, upper management, sales, and customers on a daily basis • Hire contract workers when required • Interact with customers and suggest design changes based on customer feedback Show less
-
-
-
Graftek Imaging
-
United States
-
Software Development
-
1 - 100 Employee
-
Product Support Engineer
-
Jun 2020 - Jun 2021
• Perform pre-release functional testing of all systems shipped by Graftek. • Develop user-facing documentation for all systems developed by Graftek. • Provide timely response to incoming issues for systems supported by Graftek. • Collect all relevant information, including version numbers and logs supporting the customers’ use case and reported issues. • Diagnose, update, and fix customer issues remotely via SSH, RDP, or other remote access protocols, along with providing phone, email support, and guidance. • Provide guidance to customers through corrective steps by identifying proper configurations, software/hardware versioning, and researching reported issues. • Document all communications with customers and report any root cause issues identified. • Update product documentation as needed. • Ensure customer requests are documented, tracked, and resolved in a timely manner to maintain customer satisfaction and escalate urgent problems requiring more expertise. • Providing on-site or online technical training to end-users for Graftek solutions. • Assisting with pre-sale engineering review of large projects. Show less
-
-
-
AutoMate Scientific
-
United States
-
Appliances, Electrical, and Electronics Manufacturing
-
1 - 100 Employee
-
Operations Manager / Manufacturing Technician
-
Oct 2017 - Jun 2020
• Manage Manufacturing Floor where we assemble precision biomedical equipment for neuroscience and pharmaceutical research • Organize work schedules based on orders and client urgency • Assemble 50+ different products for neuroscience and pharmaceutical research • Troubleshoot biomedical equipment failures and create company test procedures to fix new issues • Interact with customers and help with technical issues • Track company inventory and order supplies based on stock • Create custom biomedical equipment based on client's research expectations • Constant interaction with upper management, sales, and assembly teams to manage daily manufacturing needs • Proficient with Multimeters, Oscilloscopes, Soldering Irons, Wire Strippers, and Drills. • Cut company manufacturing time from 1 week to 1 day Show less
-
-
-
Dresser-Rand - A Siemens Business
-
United States
-
Machinery Manufacturing
-
700 & Above Employee
-
Project and Commissioning Engineer
-
Sep 2010 - May 2015
• Lead teams that designed and manufactured custom oil & gas equipment for off-shore, pipeline, refinery, and industrial projects • Singular technical point of contact between customers, suppliers, and colleagues consisting of roughly 70 interactions per day • Contributed to the design of custom centrifugal compressors • Lead 10+ million-dollar projects at a time and had the responsibility of keeping projects with hard deadlines on schedule • Created engineering documentation via in-house software that satisfactorily explained how to use/install equipment • Read client specifications to ensure that project requirements were fulfilled and consistent with established price and delivery • Modified engineering documentation based on client feedback • Worked on off-shore, pipeline, refinery, and industrial projects that each called for custom regulation requirements • Gave final approval of Operation and Maintenance Manuals before presenting to client • Managed Package, Controls, Rotordynamic, Electrical, and Mechanical Engineering teams throughout the duration of projects Show less
-
-
-
University at Buffalo
-
United States
-
Higher Education
-
700 & Above Employee
-
Resident Advisor
-
Aug 2008 - May 2010
• Counseled and mentored a floor of 50 Freshmen students to ensure a positive living environment • Implemented community engagement activities based on community interest • Keep activities within allocated budget and partnered with other RAs when bigger activities were desired • Always on call in case of emergency. Worked with energy services on multiple crisis in my building • Counseled and mentored a floor of 50 Freshmen students to ensure a positive living environment • Implemented community engagement activities based on community interest • Keep activities within allocated budget and partnered with other RAs when bigger activities were desired • Always on call in case of emergency. Worked with energy services on multiple crisis in my building
-
-
-
Dresser-Rand - A Siemens Business
-
United States
-
Machinery Manufacturing
-
700 & Above Employee
-
Summer Intern
-
May 2008 - Aug 2008
•Worked on a cost analysis project involving axial compressors. •Became familiar with the system of the company and obtained all the past transactions that the company made with axial compressors. •Inputted all the data into Excel spreadsheets and interacted with both accountants and engineers. •Made a presentation to the company on whether or not the company should make axial compressors again. •Worked on a cost analysis project involving axial compressors. •Became familiar with the system of the company and obtained all the past transactions that the company made with axial compressors. •Inputted all the data into Excel spreadsheets and interacted with both accountants and engineers. •Made a presentation to the company on whether or not the company should make axial compressors again.
-
-
Education
-
University at Buffalo
Bachelor’s Degree, Electrical and Electronics Engineering -
Allegany-Limestone Middle-High School
Community
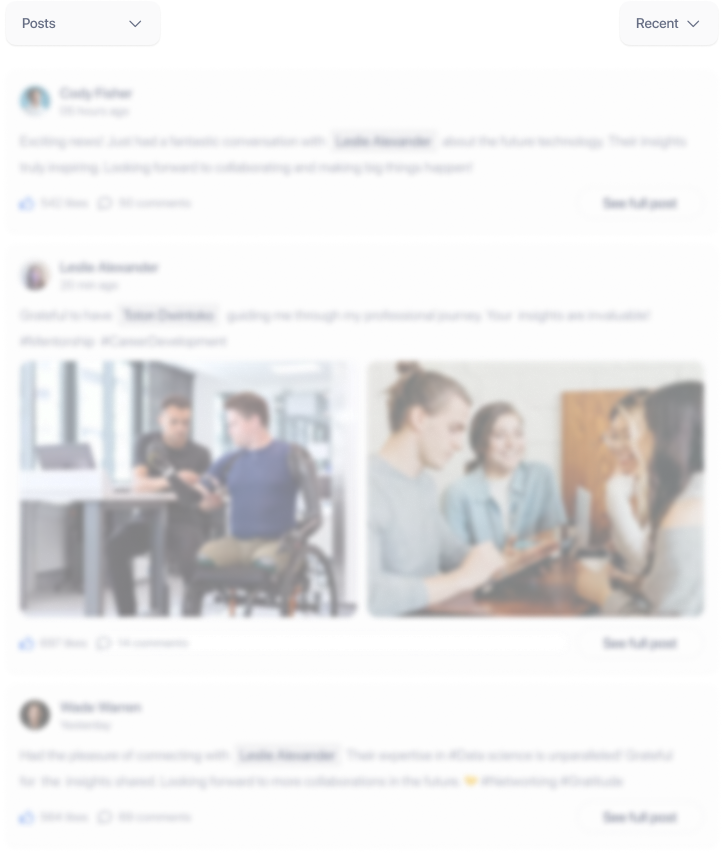