Matt Walker
Director of Supply Chain at APG- Claim this Profile
Click to upgrade to our gold package
for the full feature experience.
Topline Score
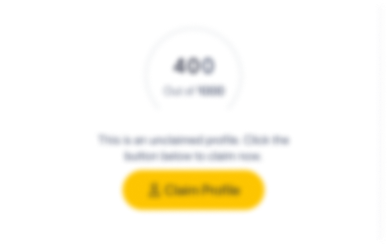
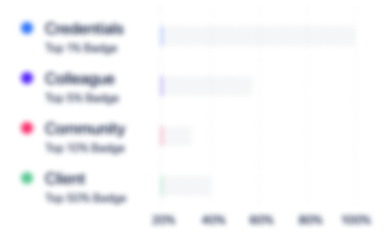
Bio
0
/5.0 / Based on 0 ratingsFilter reviews by:
Experience
-
APG
-
United Kingdom
-
Media Production
-
Director of Supply Chain
-
Jun 2022 - Present
-
-
-
Weatherford
-
Ireland
-
Oil and Gas
-
700 & Above Employee
-
Materials Manager
-
Aug 2021 - Jun 2022
Lead and oversee the Supply Chain departments: Planning, Procurement, Warehouse, and Shipping for Weatherford's West Gulf Bank manufacturing facility. Lead and oversee the Supply Chain departments: Planning, Procurement, Warehouse, and Shipping for Weatherford's West Gulf Bank manufacturing facility.
-
-
-
Black Horse LLC
-
United States
-
Oil and Gas
-
1 - 100 Employee
-
Supply Chain Director
-
May 2018 - Jul 2021
Black Horse LLC is a wholly owned subsidiary of Caterpillar Inc. I oversee execution of overall supply chain and logistics functions, including procurement, demand planning, supplier development, strategic sourcing, inventory management, warehousing, distribution, and transport of products. I develop processes and operational instruction documentation in adherence with ISO 9001:2015. I supervise implementation of supplier development and supplier changes to improve quality, delivery, and cost. I aid Caterpillar sales team and engineers in execution of targeted finished good inventory strategy and integration of new product and new technology initiatives respectively. • Drove major improvement in cost and lead time on key direct components by up to 35% and by 12 weeks respectively. • Enhanced outputs to reduce headcount by creating, leading, and coaching team. • Spearheaded major reduction in total slow-moving inventory by overseeing excess inventory reduction reviews. • Improved cost on indirect materials by up to 15%.
-
-
-
KWI (KW International, LLC)
-
United States
-
Oil and Gas
-
1 - 100 Employee
-
Director of Supply Chain
-
Dec 2015 - May 2018
I created, documented, and standardized purchasing operating procedures for corporate procurement. I conducted statistical analysis for development of corporate excess requirements and reporting activities. I headed execution of excess inventory control to minimize dead inventory and total inventory values company wide. I chaired meetings for ERP and Microsoft Navision conversion for operations side of the business. I led implementation of multiple key functions, including data mapping and cleanup of product file, and replenishment settings from existing operating systems.• Enhanced material cost by up to 20% and added labor saving for manufacturing by leading various product group sourcing reviews in compliance with approved vendor list consolidation.• Oversaw creation and execution of corporate approved vendor lists for quotations and purchasing groups for consolidation of spend, lower material costs, control quality, and improved vendor services.• Upheld concurrent responsibility over standardization of entire products by group to enhance vendor consolidation savings and minimize inventory.• Evaluated and developed new vendors to support high-mix of engineered products within varying degrees of volumes.
-
-
Director of Manufacturing
-
Jun 2015 - Nov 2015
I steered optimum management of manufacturing activities in adherence with KPIs to ensure improved labor absorption, direct labor utilization, customer deliveries, rework hours, and safety record of zero recordable injuries. I strategically reviewed and managed facility P&L statement.• Headed development of KPIs with key focus on safety, quality, delivery, and cost for Houston manufacturing site, further utilized corporately across overall manufacturing locations.• Maximized capacity with existing labor by redesigning Houston facility and overseeing implementation of manufacturing mixed model flow line.• Improved job hour performance and decreased rework through defined standards by integration of model flow lines.
-
-
Corporate Materials Manager
-
Feb 2015 - May 2015
I developed and documented SOPs for material management and control as well as executed new SOPs service to manufacturing through timely and accurate delivery of kitted materials. I performed multiple key functions, including conducting corporate sourcing review of transportation providers.• Directed consolidation of complete company transactions to single 3Pl and realized 20% reduction of company-wide transportation spend.• Collaborated with operating system programs for development and documentation of corporate cycle count and physical inventory programs.• Escalated physical inventory performance from minus 5% variance during previous year to 0.3% variance within current year.
-
-
-
Gexpro
-
Appliances, Electrical, and Electronics Manufacturing
-
700 & Above Employee
-
Operations Manager
-
Dec 2012 - Jan 2015
As Operations Manager to Gexpro, I steered sales growth by providing strong leadership to Inside Sales team and excellent customer service and operational support to Outside Sales group. I reviewed and managed Houston and Beaumont expenses of P&L statements. The following are highlights of the value I brought to Gexpro: • Proved mentor consistently focused on staff development through setting clear goals to support company objectives, stable and frequent communication, and support of training and advancement. • Established rapport between sales associates and Gexpro shared services (Sourcing, Pricing, Credit, etc.) initiatives to continuously enhance the service and support delivered to both customers and employees.
-
-
-
Exterran
-
Canada
-
Oil and Gas
-
700 & Above Employee
-
Area Manager - Materials
-
Dec 2011 - Dec 2012
I defined strategy to capitalize on holistic view for supervising inventories of $40 million. ($25m raw materials $15m finished goods). I conducted core operations in compliance with company policies and SOX standards. The following are highlights of the value I brought to Exterran: • Utilized key analytical skills to develop new operations processes/policies for warehouse and improved job order material visibility, receiving put away time, and overall improved customer service for manufacturing. • Formulated, synthesized and documented standard operating policies for warehouse, shipping, and material handling and track compliance through established KPIs and goals.
-
-
-
Ferguson Enterprises
-
United States
-
Operations Manager
-
Nov 2005 - Dec 2011
With Ferguson Enterprises, I controlled all endeavors and ensured accuracy, timely completion of every task with adherence to company’s goals and initiatives. I built synergy between warehouse and sales teams, ensuring all functions communicate effectively.The following are highlights of the value I brought to Ferguson Enterprises:• Reviewed and measured expenses on a monthly/yearly basis and oversaw Accounts Payable, expertly assessed business’s monthly/yearly P&L statement and corporate budget, implemented ISO 9001:2008 registration.• Managed inventory levels of $28 million annually and reviewed product mix to maximize sales and cash flow.• Pursued initiatives leading to reduce dead inventory from 20% to 5%; improved service levels from 83% to 98%.
-
-
Operations Management Trainee
-
Jul 2004 - Nov 2005
• Rotational training program in Warehouse, Counter Sales, Inside Sales, Shared Purchasing Center, Distribution Center, and corporate Accounting Center.• Program aimed at developing leadership, problem solving, time management, and managerial skills through accelerated learning and mentor-ship program.
-
-
Education
-
University of Oklahoma
Bachelor of Business Administration (B.B.A.), Finance, General
Community
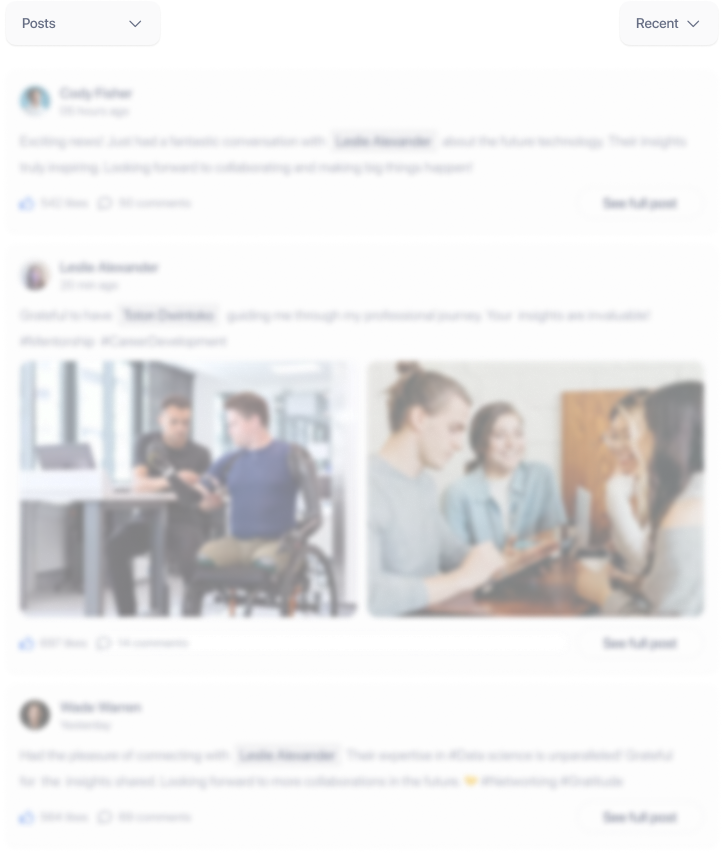