Matt Marstaller
IT Manager at artcobell- Claim this Profile
Click to upgrade to our gold package
for the full feature experience.
Topline Score
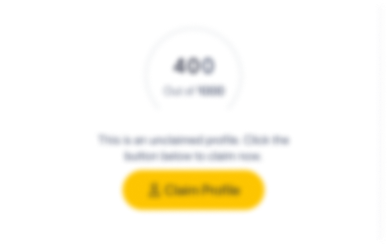
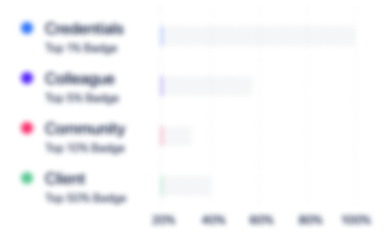
Bio


Experience
-
artcobell
-
Furniture and Home Furnishings Manufacturing
-
100 - 200 Employee
-
IT Manager
-
Jan 2022 - Present
-
-
Business Analyst
-
Aug 2020 - Jan 2022
-
-
-
TransTech Energy
-
United States
-
Oil and Gas
-
1 - 100 Employee
-
Production Planning Manager
-
Jun 2018 - Jun 2020
-
-
-
Texas Hydraulics, Inc.
-
United States
-
Machinery Manufacturing
-
100 - 200 Employee
-
Master Scheduler
-
Jul 2016 - Jun 2018
Previously: Production Supervisor, Value Stream Manager Previously: Production Supervisor, Value Stream Manager
-
-
-
L3 Technologies
-
United States
-
Defense and Space Manufacturing
-
700 & Above Employee
-
Supply Chain Manager
-
Jan 2013 - Mar 2015
Managed supply chain for the USAF/Big Safari Compass Call C-130 Program and Navy P-3 Program. • Implemented “controlled aircraft parts at point of service” staging areas where all kitting/staging was done to prepare for planned/unplanned aircraft installations. • While working together with the scheduling, planning, and operations teams, we were able to reduce late kit deliveries to six sigma levels. • Overhauled and revitalized the “aircraft strip” process using handheld mobile computer technology which has eliminated $100K annual loss pertaining to lost parts. Show less
-
-
-
Zodiac Aerospace
-
France
-
Aviation and Aerospace Component Manufacturing
-
700 & Above Employee
-
Supply Chain Director, Manufacturing Engineering Manager
-
Aug 2011 - Jan 2013
Managed supply chain and master scheduling for Zodiac Seats US (formerly Weber Aircraft), the largest commercial aircraft seat manufacturer in the world, with $500M in annual revenue to foreign and domestic customers. • Led the team which successfully implemented Thruput ERP with finite capacity master scheduling and the most detailed, accurate, and efficient demand management process in the company’s history which produced the following results: • Successfully combined the efforts of the supply chain and the operations team. This project was an IT type implementation that was completely driven and successful because of the cooperation and buy-in of the operations management team. We built a succinct, measurable, attainable schedule which left no excuse for non-performance for any member of the integrated supply chain. • Improved the global integrated supply chain metric for on-time delivery from 78% to 97% in 2-month’s time. • Implemented project during the most rapid period of growth in company history as revenue rose from $375M (2011) - $510M (2012). • Set daily, weekly, monthly, and annual production records as the demand management process was rolled out to the operations team. • Rolled out demand planning process over the course of 2 months of time spent in Chihuahua, Mexico. Show less
-
-
-
Multi Packaging Solutions (MPS)
-
Printing Services
-
700 & Above Employee
-
Regional Lean Coordinator
-
Dec 2010 - Aug 2011
Managed lean initiatives across 4 packaging facilities for MPS, a leading manufacturer of print, packaging, labels, and inserts, with 18 manufacturing facilities in the US and Europe. • Led multiple teams which accomplished all of the following: • 4 TPM events, 7 5S events, and full 5S implementation in 2 facilities. • 2 SMED events which both produced greater than 40% reduction in changeover time. • Implementation of “Sustained Employee Engagement” program in 1 facility. • 5 VSM events, first of which has led to total product lead time of less than 2 hours in 1 facility. Show less
-
-
-
Zodiac Aerospace
-
France
-
Aviation and Aerospace Component Manufacturing
-
700 & Above Employee
-
Production Manager
-
Dec 2007 - Dec 2010
As Production Manager, rotated through three departments (sheet metal, foam, plastics), 100 direct/indirect reports. As Manager of Production Control, scheduled daily tasks for entire Fabrication Division, consisting of 8 departments, totaling 800 employees. • Led the Team which created a Lean Model Cell in the Plastics Area in 2 month’s time by: • Reducing weekly assembly line stoppage time from an average of 540 minutes to less than 10 minutes • Reducing turnaround time from 8 days to 2 days • Creating a visual pull system from Assembly through Plastics • Creating and then level-loading standard work across the entire department • Establishing multiple point-of-use Kanbans for common details • Providing succinct planning requirements to each supplier in order to insure elimination of flow interrupters • Created an original manufacturing planning system for the entire facility which resulted in an average $85K monthly savings over its first year in use by: • Eliminating subjectivity through the use of a fully automated system that relied on visual signals • Reducing Work in Progress (WIP) by 40% • Creating uninterrupted flow of material throughout the facility • Creating multiple point of use Kanbans for fabricated and purchased parts • Implementing heijunka box systems to control flow of material through problematic processes • Created 40+ applications primarily focused on process automation and enterprise-wide analysis & planning Show less
-
-
-
Eminence Speaker, LLC
-
United States
-
Music
-
1 - 100 Employee
-
Lean Champion
-
Jul 2006 - Dec 2007
Managed plant-wide continuous improvement strategy for Eminence Speaker, the largest loudspeaker manufacturer in the United States, with $40M in annual revenue including wholesale distribution and OEM sales to customers such as Yamaha, Fender, Community, Telex, Peavey, Marshall, and Gibson. • Led Lean Steering Committee responsible for making lean transformation proposals directly to the President. • Developed and maintained productivity standards for all production lines and personnel. • Managed factory-wide 5S implementation by conducting training courses for all personnel, coaching supervisors and managers, and performing audits for each of the 18 departments. • Created metered adhesive dispense device that has increased consistency of the bond at the most vital joint of loudspeakers by 98% and reduced operating cost by $50K in its first year. • Created $2K poka yoke device that reduced scrap by more than $100K in its first year. • Wrote numerous standard work instructions in compliance with ISO:9001 certification. Show less
-
-
Education
-
Texas A&M University
Bachelor of Arts, Chemistry -
The Southern Baptist Theological Seminary
Community
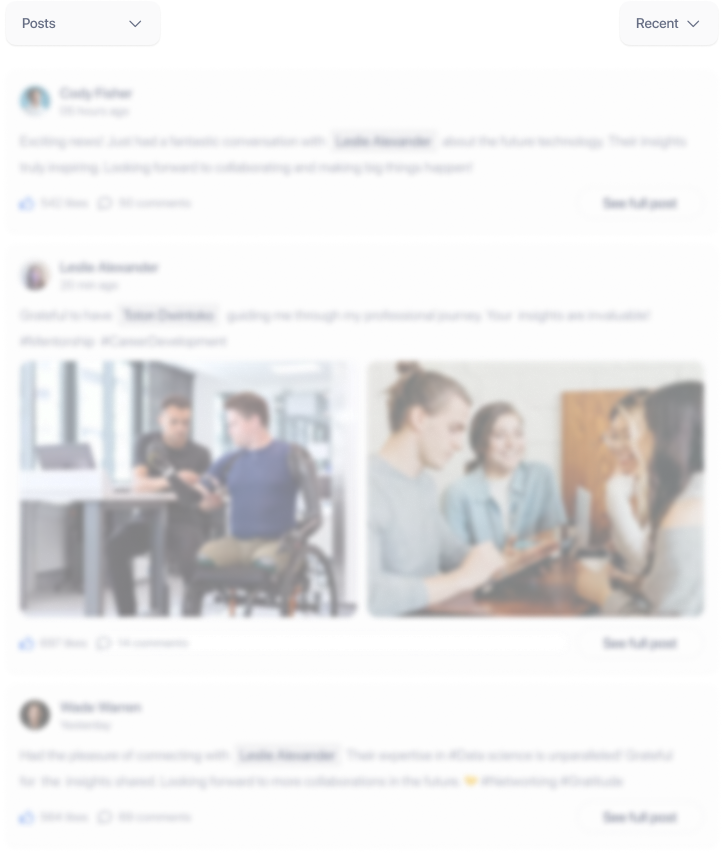