Matt Lord
Site Operations Manager at Cormar Carpets- Claim this Profile
Click to upgrade to our gold package
for the full feature experience.
Topline Score
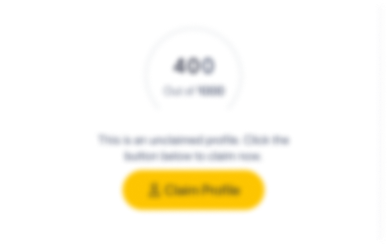
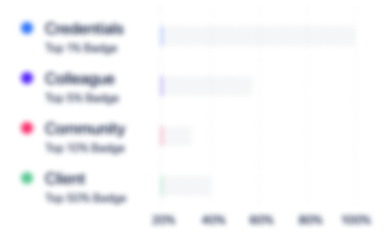
Bio
0
/5.0 / Based on 0 ratingsFilter reviews by:
Experience
-
Cormar Carpets
-
United Kingdom
-
Construction
-
1 - 100 Employee
-
Site Operations Manager
-
Dec 2017 - Present
-
-
-
Countrystyle Foods
-
United Kingdom
-
Food Production
-
200 - 300 Employee
-
General Manager
-
May 2017 - Dec 2017
FMCG Food manufacturer producing frozen bakery products such as fruit and savoury pies, crumbles, sausage rolls, turnovers, slices, etc. Direct Reports: 3 Department/3 Production Managers; In-Direct: 9 Team Leaders/70 Team Members; Total: 85 • Overall responsibility for entire site • Managing and leading all aspects of Production, Engineering, Technical, Quality, NPD, Hygiene and Warehousing • Setting and maintaining the site leadership strategy • Setting and managing department KPI’s and budgets • Overseeing the introduction of new and innovative products • Liaising with commercial teams on new and existing customer contacts/business
-
-
-
Warburtons
-
United Kingdom
-
Food and Beverage Manufacturing
-
700 & Above Employee
-
Bakery Production Manager
-
Feb 2016 - May 2017
Direct Reports: 3 Team Mangers/1 Production Planner; In-Direct: 9 Team Leaders/96 Team Members; Total: 109• Managed and took responsibility for site in when Unit Manufacturing Manger was off site• Established a CI mentality into everyday life via SIC, Daily and Weekly Meetings, that ensured robust and sustainable improvements within departments• Encouraged and led the manufacturing, maintenance and other departments to improve KPI’s and plant reliability through robust root cause analysis; by holding people to account and driving consistency of behaviours• Provided a stable and consistent message when dealing with all people performance issues from Team Members, Team Leaders and Team Managers, i.e. Absence, Disciplinary and Grievance procedures• Performance management of Team Managers and Team Leaders via use of 121’s, End of Year Appraisals, PiP’s• Nurtured and developed talent across departments through robust Training, Talent and Succession Planning• Ensured Employee Relationship and Engagement was improved via briefings and action plans being delivered by Team Managers, Team Leaders, other department heads and myself• The above resulted in the site achieving a ‘One Star’ rating from Best Companies, second highest score in the bakery group, and gaining the highest internal survey employee engagement score in the group for 2016/7
-
-
Bakery Production Manager
-
Jan 2014 - Feb 2016
Direct Reports: 4 Team Mangers/1 Production Planner; In-Direct: 9 Team Leaders/72 Team Members; Total: 86• Commissioned a new £22 million Sheet and Cut Plant three weeks ahead of schedule• Established and standardized the implementation of GMP, Housekeeping, machinery SOP’s/procedures and Quality standards throughout the new operation• Led the recruitment and induction of two Team Managers, four Team Leaders and developed four internal members of the team into Secondment Team Leaders and Team Managers• Organised and managed the recruitment, induction and training of 24 Fixed Term Contract and Agency workers to restart a ‘moth balled’ plant• Managed the site through 6 shift changes of working patterns without a single grievance• Embedded a culture of self managed teams to drive change led by Team Managers and Team Leaders• Influenced and encouraged cross department working by challenging teams to constructively challenge and hold each other accountable to achieve the goal of ‘Unbeatable Quality’
-
-
-
United Biscuits
-
United Kingdom
-
Food Production
-
700 & Above Employee
-
Manufacturing Plant Manager
-
Feb 2010 - Dec 2013
Direct Reports: 1 Team Leader/20-39 Team Members; Total: 40 • Implementing and leading the CI action plans to improve throughput and quality standards of the plant • Responsible for the development of team via coaching, mentoring and multi-skill training programme • Reviewed KPI’s to ensure they where communicated and understood, i.e. Safety, Quality, Output, Waste, GMP • People performance management via the ‘Absence’ and ‘Disciplinary and Grievance’ procedures Direct Reports: 1 Team Leader/20-39 Team Members; Total: 40 • Implementing and leading the CI action plans to improve throughput and quality standards of the plant • Responsible for the development of team via coaching, mentoring and multi-skill training programme • Reviewed KPI’s to ensure they where communicated and understood, i.e. Safety, Quality, Output, Waste, GMP • People performance management via the ‘Absence’ and ‘Disciplinary and Grievance’ procedures
-
-
-
Betts Group
-
United States
-
Business Consulting and Services
-
General Manager
-
Sep 2007 - Jul 2009
FMCG Packaging company producing tubes for toothpaste and personal care market, flexograph printing and plastic injection moulding.Direct Reports: 4 Department Managers; In-Direct: 5 Team Managers/5 Team Leaders/120 Technicians; Total: 134• Responsible for the management and leadership of Manufacturing, Maintenance and Warehousing departments• Performance Management and Development of site via coaching, mentoring and training programme• Established the Operational Excellence initiative by creating cross-functional CI teams• Managed the site through a six month closure/redundancy process with zero employee grievances
-
-
Site Business Manager
-
Aug 2006 - Sep 2007
Direct Reports: 2 Production Managers/4 Day Managers; In-Direct: 5 Team Managers/60 Technicians; Total: 71• Overall responsibility for Production, Maintenance, Supply Chain, Quality and Warehousing departments• Managed the site through a two year closure/redundancy with zero employee relation issues or grievances• Maintained compliance of all business and HR procedures, without loss of Quality or Customer Service levels
-
-
Production Manager
-
May 2004 - Aug 2006
• Managed teams with the objective of achieving a best in class manufacturing environment for site and customer• Team Work and Skill Development of Team Managers and Operators via training, coaching, performance reviews• Ownership and improvement of KPI’s including; Safety, Quality, GMP, efficiency, damage, planning, stock levels
-
-
Quality and Improvement Manager
-
Oct 2001 - May 2004
• Facilitated customer relationship via site visits, audits, presentations, Quality performance/Improvement plans• Organised and hosted external body audits and major customer audits, i.e. GSK, P&G, Colgate, Unilever• Implemented quality standards, GMP audits, SPC, In Process Quality Checks, internal audits, managed the QMS
-
-
-
Fresh Bake
-
South Africa
-
Food and Beverage Manufacturing
-
1 - 100 Employee
-
Area Team Leader
-
Sep 1997 - Oct 2001
-
-
-
-
Management Trainee
-
Aug 1994 - Sep 1997
-
-
Community
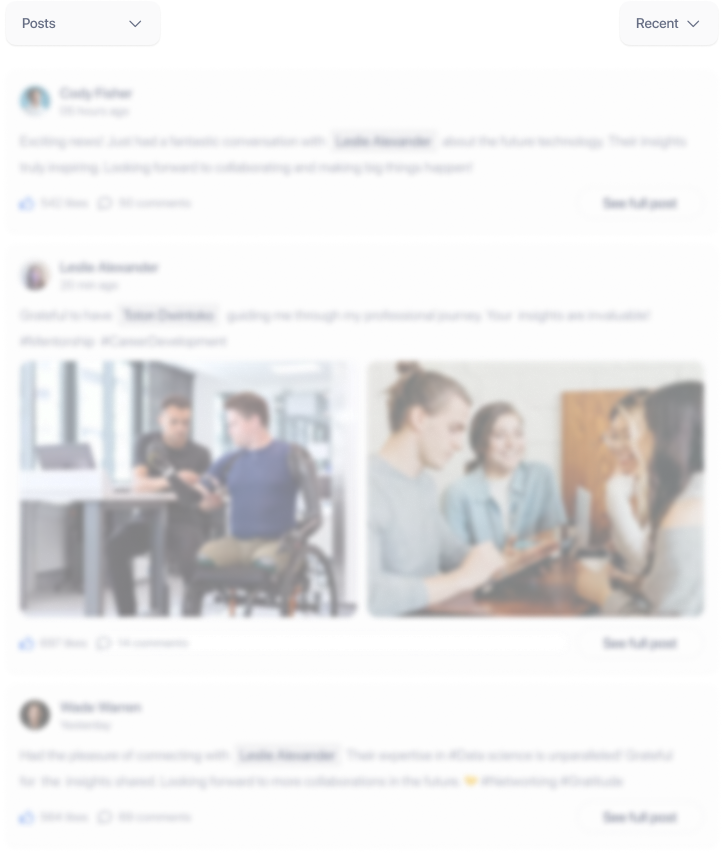