Matt Cancellieri
Senior Executive Search Consultant at Lucas Group- Claim this Profile
Click to upgrade to our gold package
for the full feature experience.
Topline Score
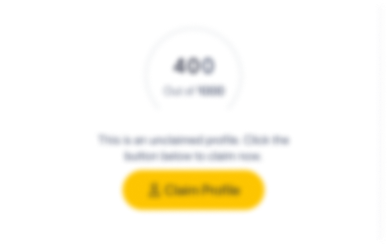
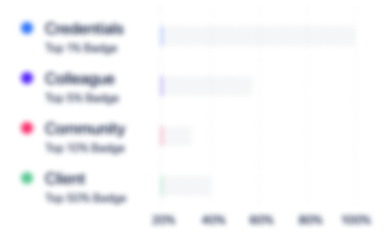
Bio

Gail Bailey
A positive, results-driven leader, describes Matt. Not only is he a focused leader, but he is also an effective coach and mentor who has the unique ability to challenge and teach in a completely constructive way. I reported to Matt for the past two years while he was the Value Stream Manager and I was the Sr. Quality Specialist for our Value Stream. Matt utilizes the SMART (Specific/Measureable/Achievable/Relevant/Time bound) approach to Project Management and Employee Performance/Development. He uses this tool effectively to maintain focus on projects and actions and engages his subordinates to employ this as technique as well. Other effective tools that Matt utilized were Visual Metrics boards to post Value Stream metrics, track progress, and provide visibility to all. Another hallmark of Matt’s leadership ability is that he effectively collaborates across functional areas to support production, quality, and maintenance. For example, he supported corrective actions for customer complaints and encouraged me to use Gemba skills to look at a more proactive approach to customer complaints. Matt is also the type of manager that has an open door and an open ear. He is great at listening, offering constructive feedback, and coaching to effect resolution. One of Matt’s strengths is his intrinsic understanding of costing and efficiency as well as his ability to communicate it effectively to others. One of the best attributes Matt has is his positivity. He has the ability to both work on the challenges of the day and also take the time to highlight what went well and call out the contributions of others. Matt is a solid and effective leader and I would wholeheartedly recommend him for any management position.

John Hall, Global Operations and Manufacturing
I worked directly and indirectly with Matt over many years and he is always pulling together his team to achieve results. Matt is an arranger, as he approaches a challenge he will identify the right resources to collaborate and engage as he grasps the situation to develop a game plan. This was a main reason I selected Matt to be a key leader as we transformed the flagship plant for Energizer in NC. Matt was successful in developing a strategy and supported execution with daily coaching of his team as he turned around the 9V manufacturing area and significantly improved delivery while at same time reducing the COGS. Matt is also a deep strategic thinker. He effectively collaborated with plant leadership peers, cross functional partners, suppliers, and executive leaders in developing a plan to outsource a significant product line while at same time develop a plan to restructure the flow of the entire plant to position for future growth opportunities. While a challenging assignment, Matt approached with a positive yes we can attitude. Matt was successful in engaging and inspiring the right people in developing and leading execution of the plan. Matt believes in working closely with his team to accomplish objectives. He is very practiced in Continuous Improvement approach. Matt has been challenged and been an excellent leader in many different roles. His experience in manufacturing operations is very valuable for any business. I would highly recommend Matt for challenging Operational Leadership positions.

Gail Bailey
A positive, results-driven leader, describes Matt. Not only is he a focused leader, but he is also an effective coach and mentor who has the unique ability to challenge and teach in a completely constructive way. I reported to Matt for the past two years while he was the Value Stream Manager and I was the Sr. Quality Specialist for our Value Stream. Matt utilizes the SMART (Specific/Measureable/Achievable/Relevant/Time bound) approach to Project Management and Employee Performance/Development. He uses this tool effectively to maintain focus on projects and actions and engages his subordinates to employ this as technique as well. Other effective tools that Matt utilized were Visual Metrics boards to post Value Stream metrics, track progress, and provide visibility to all. Another hallmark of Matt’s leadership ability is that he effectively collaborates across functional areas to support production, quality, and maintenance. For example, he supported corrective actions for customer complaints and encouraged me to use Gemba skills to look at a more proactive approach to customer complaints. Matt is also the type of manager that has an open door and an open ear. He is great at listening, offering constructive feedback, and coaching to effect resolution. One of Matt’s strengths is his intrinsic understanding of costing and efficiency as well as his ability to communicate it effectively to others. One of the best attributes Matt has is his positivity. He has the ability to both work on the challenges of the day and also take the time to highlight what went well and call out the contributions of others. Matt is a solid and effective leader and I would wholeheartedly recommend him for any management position.

John Hall, Global Operations and Manufacturing
I worked directly and indirectly with Matt over many years and he is always pulling together his team to achieve results. Matt is an arranger, as he approaches a challenge he will identify the right resources to collaborate and engage as he grasps the situation to develop a game plan. This was a main reason I selected Matt to be a key leader as we transformed the flagship plant for Energizer in NC. Matt was successful in developing a strategy and supported execution with daily coaching of his team as he turned around the 9V manufacturing area and significantly improved delivery while at same time reducing the COGS. Matt is also a deep strategic thinker. He effectively collaborated with plant leadership peers, cross functional partners, suppliers, and executive leaders in developing a plan to outsource a significant product line while at same time develop a plan to restructure the flow of the entire plant to position for future growth opportunities. While a challenging assignment, Matt approached with a positive yes we can attitude. Matt was successful in engaging and inspiring the right people in developing and leading execution of the plan. Matt believes in working closely with his team to accomplish objectives. He is very practiced in Continuous Improvement approach. Matt has been challenged and been an excellent leader in many different roles. His experience in manufacturing operations is very valuable for any business. I would highly recommend Matt for challenging Operational Leadership positions.

Gail Bailey
A positive, results-driven leader, describes Matt. Not only is he a focused leader, but he is also an effective coach and mentor who has the unique ability to challenge and teach in a completely constructive way. I reported to Matt for the past two years while he was the Value Stream Manager and I was the Sr. Quality Specialist for our Value Stream. Matt utilizes the SMART (Specific/Measureable/Achievable/Relevant/Time bound) approach to Project Management and Employee Performance/Development. He uses this tool effectively to maintain focus on projects and actions and engages his subordinates to employ this as technique as well. Other effective tools that Matt utilized were Visual Metrics boards to post Value Stream metrics, track progress, and provide visibility to all. Another hallmark of Matt’s leadership ability is that he effectively collaborates across functional areas to support production, quality, and maintenance. For example, he supported corrective actions for customer complaints and encouraged me to use Gemba skills to look at a more proactive approach to customer complaints. Matt is also the type of manager that has an open door and an open ear. He is great at listening, offering constructive feedback, and coaching to effect resolution. One of Matt’s strengths is his intrinsic understanding of costing and efficiency as well as his ability to communicate it effectively to others. One of the best attributes Matt has is his positivity. He has the ability to both work on the challenges of the day and also take the time to highlight what went well and call out the contributions of others. Matt is a solid and effective leader and I would wholeheartedly recommend him for any management position.

John Hall, Global Operations and Manufacturing
I worked directly and indirectly with Matt over many years and he is always pulling together his team to achieve results. Matt is an arranger, as he approaches a challenge he will identify the right resources to collaborate and engage as he grasps the situation to develop a game plan. This was a main reason I selected Matt to be a key leader as we transformed the flagship plant for Energizer in NC. Matt was successful in developing a strategy and supported execution with daily coaching of his team as he turned around the 9V manufacturing area and significantly improved delivery while at same time reducing the COGS. Matt is also a deep strategic thinker. He effectively collaborated with plant leadership peers, cross functional partners, suppliers, and executive leaders in developing a plan to outsource a significant product line while at same time develop a plan to restructure the flow of the entire plant to position for future growth opportunities. While a challenging assignment, Matt approached with a positive yes we can attitude. Matt was successful in engaging and inspiring the right people in developing and leading execution of the plan. Matt believes in working closely with his team to accomplish objectives. He is very practiced in Continuous Improvement approach. Matt has been challenged and been an excellent leader in many different roles. His experience in manufacturing operations is very valuable for any business. I would highly recommend Matt for challenging Operational Leadership positions.

Gail Bailey
A positive, results-driven leader, describes Matt. Not only is he a focused leader, but he is also an effective coach and mentor who has the unique ability to challenge and teach in a completely constructive way. I reported to Matt for the past two years while he was the Value Stream Manager and I was the Sr. Quality Specialist for our Value Stream. Matt utilizes the SMART (Specific/Measureable/Achievable/Relevant/Time bound) approach to Project Management and Employee Performance/Development. He uses this tool effectively to maintain focus on projects and actions and engages his subordinates to employ this as technique as well. Other effective tools that Matt utilized were Visual Metrics boards to post Value Stream metrics, track progress, and provide visibility to all. Another hallmark of Matt’s leadership ability is that he effectively collaborates across functional areas to support production, quality, and maintenance. For example, he supported corrective actions for customer complaints and encouraged me to use Gemba skills to look at a more proactive approach to customer complaints. Matt is also the type of manager that has an open door and an open ear. He is great at listening, offering constructive feedback, and coaching to effect resolution. One of Matt’s strengths is his intrinsic understanding of costing and efficiency as well as his ability to communicate it effectively to others. One of the best attributes Matt has is his positivity. He has the ability to both work on the challenges of the day and also take the time to highlight what went well and call out the contributions of others. Matt is a solid and effective leader and I would wholeheartedly recommend him for any management position.

John Hall, Global Operations and Manufacturing
I worked directly and indirectly with Matt over many years and he is always pulling together his team to achieve results. Matt is an arranger, as he approaches a challenge he will identify the right resources to collaborate and engage as he grasps the situation to develop a game plan. This was a main reason I selected Matt to be a key leader as we transformed the flagship plant for Energizer in NC. Matt was successful in developing a strategy and supported execution with daily coaching of his team as he turned around the 9V manufacturing area and significantly improved delivery while at same time reducing the COGS. Matt is also a deep strategic thinker. He effectively collaborated with plant leadership peers, cross functional partners, suppliers, and executive leaders in developing a plan to outsource a significant product line while at same time develop a plan to restructure the flow of the entire plant to position for future growth opportunities. While a challenging assignment, Matt approached with a positive yes we can attitude. Matt was successful in engaging and inspiring the right people in developing and leading execution of the plan. Matt believes in working closely with his team to accomplish objectives. He is very practiced in Continuous Improvement approach. Matt has been challenged and been an excellent leader in many different roles. His experience in manufacturing operations is very valuable for any business. I would highly recommend Matt for challenging Operational Leadership positions.

Experience
-
Lucas Group, A Korn Ferry Company
-
United States
-
Staffing and Recruiting
-
400 - 500 Employee
-
Senior Executive Search Consultant
-
Sep 2021 - Present
-
-
-
Armstrong Fluid Technology
-
Canada
-
Industrial Machinery Manufacturing
-
700 & Above Employee
-
Production Manager
-
Nov 2020 - Sep 2021
Change agent accountable for leading the facility’s Lean transformation focused on delivering Customer satisfaction through delivering quality products on time. Active coach to manufacturing team consisting of 3 Supervisors and 70 production colleagues accountable for producing $100M in revenue annually. Change agent accountable for leading the facility’s Lean transformation focused on delivering Customer satisfaction through delivering quality products on time. Active coach to manufacturing team consisting of 3 Supervisors and 70 production colleagues accountable for producing $100M in revenue annually.
-
-
-
Boyd
-
United States
-
Appliances, Electrical, and Electronics Manufacturing
-
700 & Above Employee
-
Operations Manager
-
Oct 2019 - Nov 2020
Provide operational leadership within Aerospace & Defense facility including Safety, Production, Manufacturing Engineering, Maintenance, Shipping and Receiving. Active coach to plant team consisting of ~130 colleagues on a 524 schedule producing $35M in annual revenue. Provide operational leadership within Aerospace & Defense facility including Safety, Production, Manufacturing Engineering, Maintenance, Shipping and Receiving. Active coach to plant team consisting of ~130 colleagues on a 524 schedule producing $35M in annual revenue.
-
-
-
Materion Corporation
-
United States
-
Manufacturing
-
700 & Above Employee
-
Plant Manager
-
Oct 2017 - Oct 2019
Provide plant leadership to all aspects of manufacturing including Safety & Health, Operations, Process Engineering, Production Scheduling, Inventory Management, and Maintenance in an ISO 9000:1 and 1400:1 certified facility. Through hands on leadership developed team and manufacturing systems to identify waste and drive problem solving in real time. Direct P&L accountability for $55M annual revenue and a team of 85 colleagues across two manufacturing sites. Provide plant leadership to all aspects of manufacturing including Safety & Health, Operations, Process Engineering, Production Scheduling, Inventory Management, and Maintenance in an ISO 9000:1 and 1400:1 certified facility. Through hands on leadership developed team and manufacturing systems to identify waste and drive problem solving in real time. Direct P&L accountability for $55M annual revenue and a team of 85 colleagues across two manufacturing sites.
-
-
-
Energizer Holdings
-
United States
-
Manufacturing
-
700 & Above Employee
-
Operations Manager
-
Apr 2015 - Oct 2019
Manage all aspects of safety, quality, cost, and delivery of the manufacturing of C, D, and 9V batteries with $7.4M absorption budget. Deliver solutions to remain cost competitive in a mature product line with receding global volumes. Assume direct accountability for 10 of the 24 salaried colleagues that support the business; 14 acre battery plant with annual volume of 1.6 billion batteries with 300 production, 100 maintenance, and up to 300 contract colleagues.• Lead restructuring of salaried resources and operations to align with corporate restructuring, due to spinoff of Personal Care division.• Facilitate process mapping events across multiple disciplines to establish standards under new corporate strategy.• Lead plant strategic planning to deliver $2M in Cost of Goods Sold reductions.• Implement staffing changes to offset volume losses of 25% or $1M in direct labor absorption.• Pursue new business opportunities to leverage key competencies, including evaluation of global manufacturing footprint, make vs. buy raw material sourcing strategies, and contract staffing.• Manage contract labor execution with budget of $5M annually.• Assist in new hire selection and development of hourly production, maintenance, and salaried colleagues, including interviewing and new hire appraisals.
-
-
Technical Services Manager
-
Sep 2013 - Apr 2015
Assumed responsibility for engineering and maintenance support of a high speed automated battery packing plant. Accountable for plant safety program. Direct accountability for 6 engineers, 1 Maintenance Supervisor and 1 Safety Coordinator. Led Maintenance organization consisting of 22 skilled trade indirect reports.• Led plant strategic planned to deliver $1.5M in Cost of Goods Sold budget to budget reductions.• Led development of seasonal core contract staffing model to control costs during seasonal demand swings, yielding $300k in annual savings.• Managed engineering projects to improve efficiency, to reduce material over usage, and to reduce inventory.• Effectively developed and managed fiscal year Capital and Expense Budget of $1.7M and Major Maintenance Budget of $600k.• Developed 3 year strategic maintenance improvement plan centered on shifting culture from a reactive to a preventative culture. • Reduced variable expense labor and materials by $300k annually through improved effectiveness of planned and reactive resources. • Developed highly functioning safety committee to drive improvements at the hourly level with specific areas of expertise.• Provided leadership to become certified as a NC Safety Star manufacturing facility.
-
-
Operations Manager
-
Oct 2010 - Sep 2013
Assumed full responsibility for managing plant operations, including manufacturing, production scheduling, materials management, and engineering. Provided leadership to 150 colleagues with the support of 10 salaried direct reports to meet safety, quality, cost, and delivery goals. • Led startup of AA Lithium battery expansion to increase plant capacity by 50% to 250M batteries annually including process validation, shift conversion from 524 to 724 operations, and hiring/training of additional production and salaried staff. • Worked with Technology, Engineering, and Supply Chain to deliver Product Cycle Plans to improve AA battery performance to maintain the ‘World’s Longest Lasting’ marketing claim, while minimizing conversion costs.• Determined fiscal year direct labor, material, and variable expense budgets to meet product cost goals.• Led the training of production operators, engineers, and operations managers to support the global expansion of Lithium manufacturing in Energizer’s Singapore facility. • Championed Lean cultural changes including Daily Continuous Improvement, Small K, Total Productive Maintenance, Single Piece Flow, Visual Factory and Leader Standard Work.• Developed Lean Daily Management structure to provide linkage between day to day operation, process support, and strategic change.• Provided leadership to transition all Lithium battery manufacturing to Singapore through the closure of the Saint Albans facility with zero quality complaints or impacts to the supply chain.
-
-
-
Energizer Holdings
-
United States
-
Manufacturing
-
700 & Above Employee
-
Senior Operations Supervisor
-
Apr 2007 - Jul 2008
• Determined plant labor requirements to meet fluctuations in monthly customer demand.• Analyzed monthly closing results (Labor /Material /Variable Expense) and put countermeasures in place to address usage variances. • Provided direct leadership to three Operations Supervisors with accountability for up to 150 hourly production colleagues.• Developed an Operations Supervision training program, including a time-based training curriculum, standard operating procedures, and skill validations that became the global standard for all facilities. • Drove finite scheduling improvements to align production scheduling and material planning to avoid material shortages, while minimizing inventory. • Established raw material inventory supermarkets to facilitate decision making without management oversight.
-
-
Operations Supervisor
-
Apr 2007 - Jul 2008
• Supervised 50 production colleagues to achieve established goals.• Mentored hourly production team leaders in facilitation skills, interpersonal dynamics, and the ability to eliminate waste within the operation.• Created cross training plan to increased flexibility of value stream resources to meet productions schedules.• Established staffing ramp up /ramp down plans to allocate labor between departments to efficiently react to fluctuations in volume.• Taught principles of 5S tools to improve flow and shop floor organization. • Participated in a kaizen event to develop standard work and improve line efficiency.
-
-
Education
-
The Ohio State University Fisher College of Business
Bachelors of Science, Business Administration, Management and Operations -
Bond University
Study Abroad -
Kent State University
Lean Six Sigma Black Belt
Community
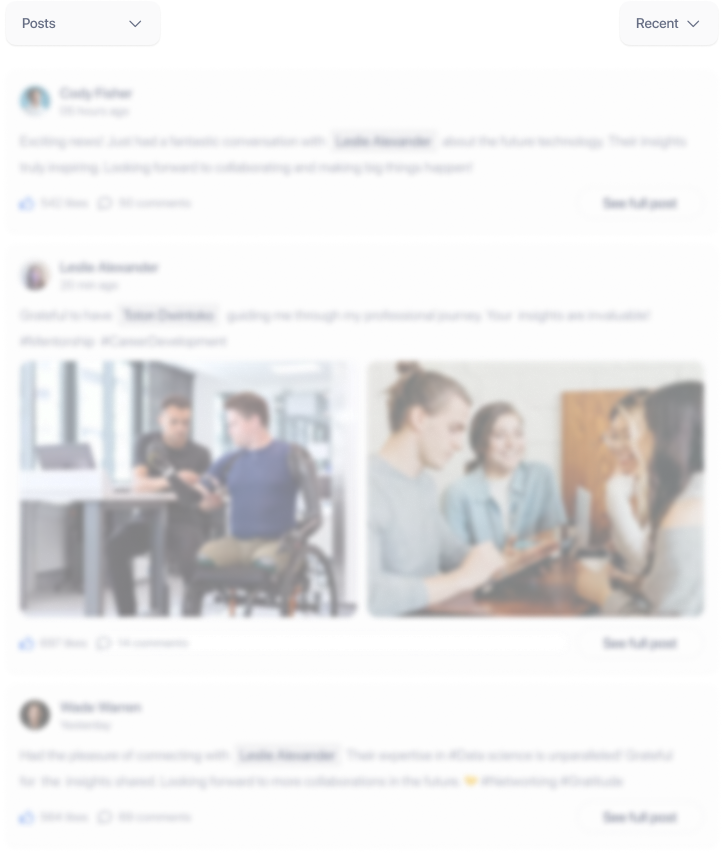