Marvi Dashi
Team Lead Inventory at Base Camp Data Solutions- Claim this Profile
Click to upgrade to our gold package
for the full feature experience.
-
English Professional working proficiency
-
Urdu Native or bilingual proficiency
-
Siraiki Professional working proficiency
Topline Score
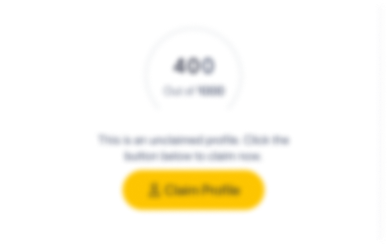
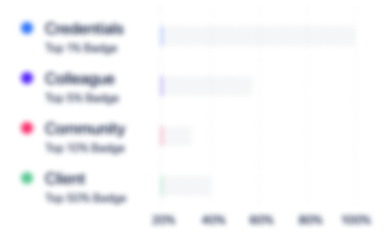
Bio
0
/5.0 / Based on 0 ratingsFilter reviews by:
Credentials
-
IELTS General (Over All 7.5 - C1 Level)
AEO PakistanAug, 2020- Sep, 2024 -
2. Paper presented in Conference -Tayyab din Memon, Imtiaz Kalwar, Bhavani Shankar ,Marvi Deshi “SWL Algorithms Optimization Using Alternative Adder Module in FPGA “, Feb 11 – 13, 2015, 4th International Conference IMTIC’15, Jamshoro, Pakistan
4th International Conference IMTIC’15
Experience
-
Base Camp Data Solutions
-
Pakistan
-
Information Technology & Services
-
100 - 200 Employee
-
Team Lead Inventory
-
Jan 2021 - Present
Manage Inventory for Client, Inspect the levels of business supplies and raw material to identify shortages.● Ensure product stock is adequate for all distribution channels.● Ensure Proper & timely closures of Masters Tickets from client stores.● Managing inventory team, assigning Projects and ensure systematic approach.● ZOHO Inventory & CRM module implementation and replicate team tasks in their respective Project.● Place orders to replenish stock avoiding insufficiencies or excessive surplus● Evaluate suppliers to achieve cost-effective deals and maintain trust relationships● Report to upper management on stock levels, issues, Products with less demand / Low sales etc
-
-
-
NADRA
-
Bangladesh
-
Retail
-
Supervisor- NSER (National Social Economic Registration) Project
-
Sep 2020 - Jan 2021
● Managing a team of Junior executives and accountable for one full-fledged Nadra Site Operation.● Ensuring proper data logging, timely submission and closure of data and tasks in the system. ● Managing Petty Cash, day-to-day purchasing and miscellaneous procurement of site.● Ensuring seamless coordination with Central Technical Networking team for system bugs and their resolution. ● Ensuring direct coordination with the Central team for proper equipment functioning & Maintenance related issues.● Floor management,Forms update and Process appointments for New applicant.● Escalating the high priority issues and ambiguity to Additional Director District and Project Team.
-
-
-
Philip Morris International
-
Switzerland
-
Tobacco Manufacturing
-
700 & Above Employee
-
Procurement Executive
-
Nov 2017 - Mar 2019
● Lead sourcing of inventoried items with respect to corresponding categories for the assigned purchasing perimeter.● Design procurement plans incorporated with business opportunities to achieve operational & Procurement objectives.● Stakeholder management and relation-building with suppliers to negotiate the conditions of the delivery, cost and lead times of the technical materials and services.● Liaison with Customs, Treasury and Accounts Payable representatives for OEM shipments, LC and their payments ● Arrange supplier and their services based on proposals provided by the end users to select best available suppliers and services in line with PMI procedures and policies.● Co-ordinate and Implement cross regional synergies, optimization programs & projects to streamline and standardize production equipment and technical procurement process, policies, standards that will generate implementation of best practices across PMI and potential Vendors development from current vendor’s pool.
-
-
Maintenance Planner
-
Nov 2015 - Nov 2017
-
-
Controls Engineer
-
Mar 2014 - Nov 2015
● Remained part of the factory hazard closure team from the Maintenance Department.● Managing Spares & Material critical part & commissioning with Vendors.● Maintenance of Production Machine (Processing).● Propose improvement to Process, efficiency & automation projects● Calibration of Instruments as per OEM recommendation.● Planning & Implementation of preventive maintenance.● Internal & Self audits lead for maintenance audits.● Procurement of Spares & services related to maintenance.
-
-
Quality Assurance Specilist
-
Feb 2012 - Mar 2014
● Part of the Team that led to the certifications of ISO-9001, 14001 and 18001● Reporting and Result analyzing of CPQI, GENESIS system admin & its reporting.● Compile PMI local Document related to Physical Quality.● Reviewing and Preparing Daily & Weekly Reports. ● Reviewing & control on floor Physical Quality check sheets, taking corrective & preventive Actions.● Instrument is Verification/calibration in QA, Daily or Monthly.● Statically comparison of instruments verification & other Physical test.● Presenting the issue of Physical test & their corrective actions in weekly QA Meeting.● EHS coordinator for QA department, Supporting ERT Team and other related activities.
-
-
Education
-
Mehran University of Engineering and Technology
Masters of Engineering, Electronic Systems Engineering -
Mehran University of Engineering & Technology Jamshoro
Bachelor's degree, Electrical, Electronics and Communications Engineering
Community
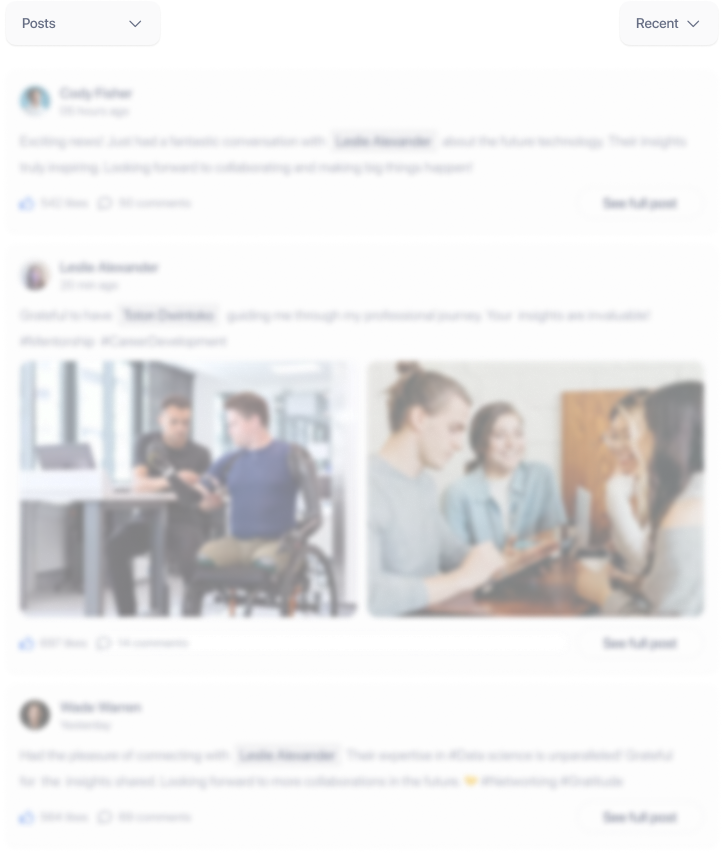