Marty Brett
General Manager at Crystal Engineering Co- Claim this Profile
Click to upgrade to our gold package
for the full feature experience.
Topline Score
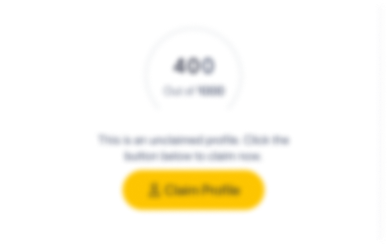
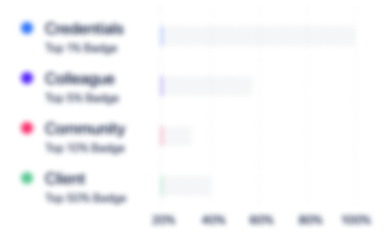
Bio

Jason Hamilton
Marty is the best individual I have ever met with organization. I have worked on the same team many years and also reported to him for a period of time. He thinks of both Company and the Employees. Marty would be a great asset to any team!

Jason Hamilton
Marty is the best individual I have ever met with organization. I have worked on the same team many years and also reported to him for a period of time. He thinks of both Company and the Employees. Marty would be a great asset to any team!

Jason Hamilton
Marty is the best individual I have ever met with organization. I have worked on the same team many years and also reported to him for a period of time. He thinks of both Company and the Employees. Marty would be a great asset to any team!

Jason Hamilton
Marty is the best individual I have ever met with organization. I have worked on the same team many years and also reported to him for a period of time. He thinks of both Company and the Employees. Marty would be a great asset to any team!

Credentials
-
Certified Continuous Improvement Manager
Management & Strategy InstituteSep, 2020- Nov, 2024
Experience
-
Crystal Engineering Co
-
United States
-
Machinery Manufacturing
-
1 - 100 Employee
-
General Manager
-
Apr 2021 - Present
-
-
-
World Washer & Stamping
-
Addison, Illinois, United States
-
General Manager
-
Apr 2021 - Jan 2022
-
-
-
Agrati Group
-
Italy
-
Motor Vehicle Parts Manufacturing
-
500 - 600 Employee
-
Group Industrial Engineering Manager
-
Feb 2019 - Jul 2020
• Directed team responsible for the annual $10M CapEx spend, continuous improvement projects and Agrati Production System (APS) standardization at four US locations • Slashed $500K+ annually in operational improvements and savings and increased focus of all employees to see impact that eliminating waste had on company’s bottom line, utilizing kaizen and SMED activities • Improved overall effectiveness by 4%–7%; enhanced throughput by 7%–10% and quality of production areas • Led team to champion the implementation of Agrati standard forms in areas throughout the organization from operations to quality to HR to EH&S
-
-
-
Taubensee Steel & Wire Company
-
United States
-
Mining
-
1 - 100 Employee
-
General Manager - Chicago District
-
2017 - Feb 2019
• Led two divisions with $80M in annual revenue and union employees • Improved financial performance of operations due to a concerted effort to reduce costs • Managed organizational certification of ISO 9001:2015 quality system • Led two divisions with $80M in annual revenue and union employees • Improved financial performance of operations due to a concerted effort to reduce costs • Managed organizational certification of ISO 9001:2015 quality system
-
-
-
Agrati Group
-
Italy
-
Motor Vehicle Parts Manufacturing
-
500 - 600 Employee
-
General Manager
-
Mar 2015 - Nov 2017
• Improved Customer On-Time Delivery; improved Cost of Quality from high 7% down to 4% of revenue; and reduced scrap reduction from a high 3.5% to 2% of revenue• Led projects that improved operations of $101M automotive supplier at two locations, including 5-S program implementation, efficiency improvements within the direct labor manufacturing departments, SMED activity, more-efficient changeovers and streamlined warehouse shipping, receiving and inventory control• Improved EBITDA performance by 65% in 18 months, reduced overtime 15% and improved OEE 15% • Drove operational improvements through Kaizen events focused on setup reduction and streamlining of processes• Executed efforts that achieved certifications of quality systems and safety systems: ISO/TS 16949 Management System, ISO17025 Quality Lab Accreditation, ISO14001 Environmental Management System, MMOG/LE Materials Management Operations Guidelines and Ford Q1 Supplier Certification
-
-
Director of Materials Management
-
Apr 2004 - Mar 2015
• Achieved 2% savings YOY while negotiating and managing a $56M raw materials and process contracting budget• Improved Supplier On-time Delivery from 74% to 88%• Identified KPI’s, collaborated with department managers on trends and course corrected when necessary• Subject Matter Expert: Corporate ERP system: Plex• Produced planning process from raw materials and production tooling through WIP to finished goods inventory• Upheld on-time delivery performance 99.5%+ with direct oversight of Customer Service and Warehouse Operations• Improved visibility for customer service group, developed cycle count program and created portal access in ERP system • Ensured quality system compliance: TS16949, ISO14001• Managed 52 employees and 4 departments: Purchasing, Customer Service, Production Control, Warehouse (shipping, receiving, inventory control and sorting)
-
-
-
ATF Inc.
-
United States
-
Motor Vehicle Manufacturing
-
100 - 200 Employee
-
Purchasing Manager
-
2001 - 2004
• Managed $15M raw materials and process contracting budgets and 10 employees in Purchasing and Raw Materials Receiving departments • Formalized monthly supplier scorecard system of suppliers that improved delivery and quality levels • Led daily Material Review Board for supplier-related issues • Ensured quality system compliance: TS16949, QS9000, ISO9002, ISO14001 • Managed $15M raw materials and process contracting budgets and 10 employees in Purchasing and Raw Materials Receiving departments • Formalized monthly supplier scorecard system of suppliers that improved delivery and quality levels • Led daily Material Review Board for supplier-related issues • Ensured quality system compliance: TS16949, QS9000, ISO9002, ISO14001
-
-
-
ATF Inc.
-
United States
-
Motor Vehicle Manufacturing
-
100 - 200 Employee
-
Plant Controller/Operations Analyst
-
1997 - 2000
• Prepared financial review packages, supported Controller in forecasting and managed 5-person Accounts Payable and Accounts Receivable departments • Monitored manufacturing production activity, prepared monthly financials and monthly labor and burden efficiency analyses and upheld A/S 400-based standard cost system in Unisys and CMS software • Prepared cost analyses from new product ventures to monthly expenses • Prepared financial review packages, supported Controller in forecasting and managed 5-person Accounts Payable and Accounts Receivable departments • Monitored manufacturing production activity, prepared monthly financials and monthly labor and burden efficiency analyses and upheld A/S 400-based standard cost system in Unisys and CMS software • Prepared cost analyses from new product ventures to monthly expenses
-
-
Education
-
St. Xavier University
Master of Business Administration (MBA), Information Systems -
Marquette University
Bachelor's degree, Accounting
Community
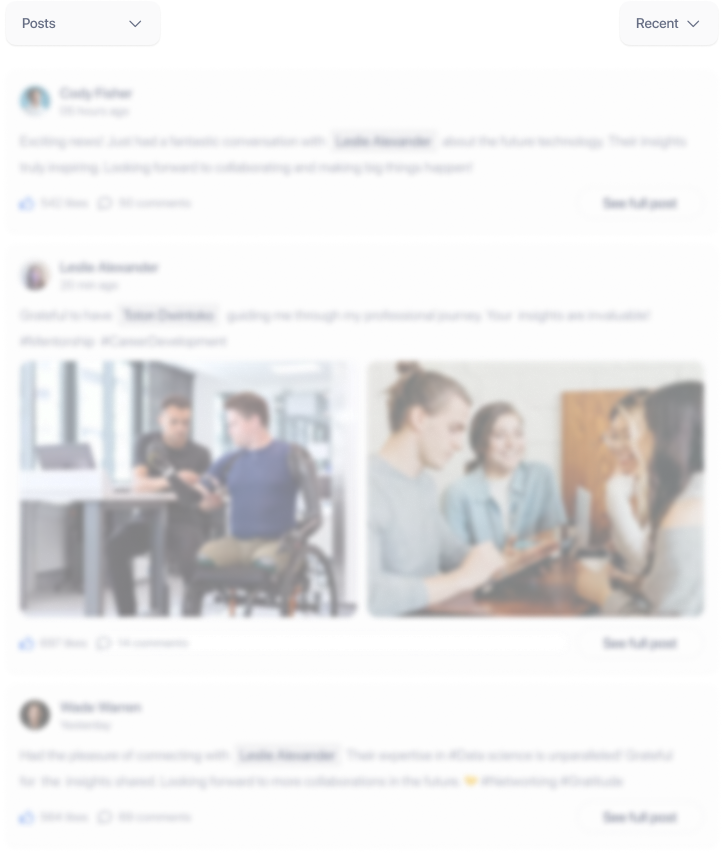