
Martin Pilko
Quality Manager at SPPP Slovakia- Claim this Profile
Click to upgrade to our gold package
for the full feature experience.
-
german Full professional proficiency
-
english Professional working proficiency
Topline Score
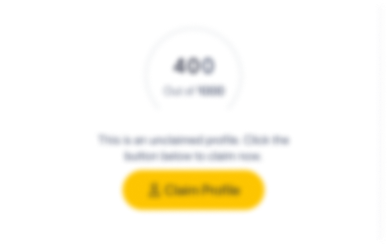
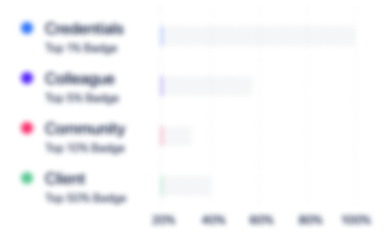
Bio


Credentials
-
VDA 6.3 - Upgrade Training
VDA QMC , TQMDec, 2017- Nov, 2024 -
IATF 16 949 - Upgrade training for 1st / 2nd party auditors
VDA QMC , TQMJun, 2017- Nov, 2024 -
IATF 16 949 - Implemntation within the organisation
VDA QMC , TQMMay, 2017- Nov, 2024 -
Module B II - Process audit VDA 6.3 - product life cycle
VDA QMC , TQMOct, 2015- Nov, 2024
Experience
-
SPPP Slovakia
-
Slovakia
-
Motor Vehicle Manufacturing
-
1 - 100 Employee
-
Quality Manager
-
Jun 2019 - Present
-
-
-
-
Quality Manager plant Súčany
-
Nov 2018 - May 2019
-managing of Q-department, laboratory, technicians for measure automats (22 employees)-Q-department – 3 quality engineers focused on customers, 4 quality auditors, 1 incoming inspection-technicians for measure automats for check holes, threads, dynamic control of dimensions-calibration laboratory and measuring laboratory with metalografy and evaluation of hardening-coordination and supervision of certification acc. IATF 16 949 and ISO 14 001 -managing of IMS system and documentation in plant-managing and approval of schedules internal system, process and product audits-communication with customers f.e. during visits, complaints-monitoring and analysis of quality costs, coordination and implementation preventive and corrective actions, monitoring KPIs, evaluation of the product and process using quality tools-reporting KPIs to headquarters-preparing budget for all departments together with controlling-managing of dep. SHE (safety, health, environment)
-
-
-
-
Quality and Safety Manager
-
Nov 2006 - Apr 2018
managing of 5 Q-departments for production segments and 4 central Q-departments (app. 60 employees)-5 Q-departments (business units) focused on customers, managing of quality group leaders-4 central Q-departments – Q-central dep., calibration laboratory and measuring laboratory, incoming inspection-coordination and supervision of certification acc. IATF 16 949 and ISO 14 001-managing of IMS system and information intranet in the plant-managing and approval of schedules internal system, process and product audits-communication with customers f.e. during visits, significant complaints, visits at customers-escalation meetings with suppliers-monitoring and analysis of quality costs, coordination and implemetation preventive and corrective actions, monitoring KPIs, evaluation of the product and process using quality tools-reporting KPIs to headquarters-preparing budget for all departments together with controling-managing of dep. SHE (safety, healty, enviroment)-concluding contracts with external suppliers (f. e. SHE)-managing of competence center for headquarters (15 empl. -multifunctional team)-hiring sutaible employees for the teams
-
-
-
-
Director, executive manager
-
Jan 2002 - Nov 2006
managing of plant Púchov and Žilina-leadership of staff, departments, commnication with the authorithies-preparing of budget for both plants-cooperation on new projects together with central departments-secure the communication with central functions as sales, logistic, purchasing, R&D in Austria-communication and coordination finance with controling in Austria
-
-
Quality Manager
-
Sep 2001 - Dec 2001
-managing of 4 quality group leaders-coordination of certification acc. ISO TS 16 949-monitoring of quality costs-managing of internal audits-contact with the customers, communication with customers f.e. during visits, complaints and visits atcustomers
-
-
-
-
Quality group leader
-
Aug 1994 - Aug 2001
-coordination and creating of 8D reports for the customers, ceating of FMEA, CP, MSA-managing of quality employees – engineers, technicians, inspectors-visits and contact with customers, preparing of presentations-coordination and implemetation preventive and corrective actions for internal processes and complaints-monitoring and managing of claims-monitoring of quality costs -coordination and creating of 8D reports for the customers, ceating of FMEA, CP, MSA-managing of quality employees – engineers, technicians, inspectors-visits and contact with customers, preparing of presentations-coordination and implemetation preventive and corrective actions for internal processes and complaints-monitoring and managing of claims-monitoring of quality costs
-
-
Education
-
TU Košice – Faculty of Mechanical Engineering
Dipl. Ing., Manufactoring Engineering
Community
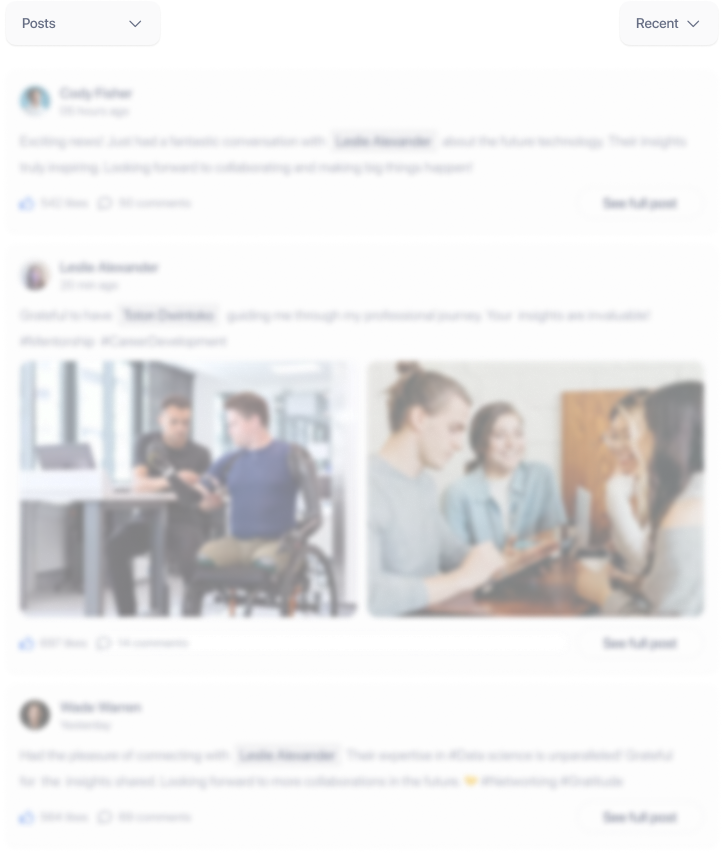