Martin Gembala
Chief Operation Officer at HERN- Claim this Profile
Click to upgrade to our gold package
for the full feature experience.
-
English -
-
Czech -
-
Polish -
Topline Score
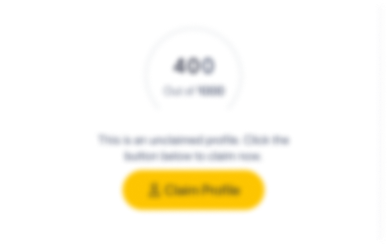
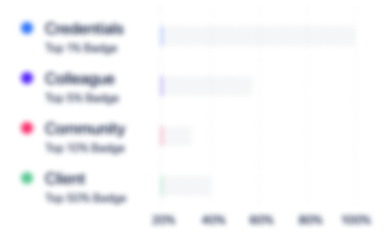
Bio


Experience
-
HERN
-
Slovakia
-
Machinery Manufacturing
-
1 - 100 Employee
-
Chief Operation Officer
-
Jan 2021 - Present
Production Director Production Director
-
-
-
self-employed
-
Trstena - Slovakia
-
Logistics advisor and consultant
-
Aug 2014 - Present
• Strategic Consulting, including business plan & sales strategy development. • Projects cooperation - standardization and optimization of logistics processes, warehouse layout proposals, stock levels set up • Supply chain coordination, 3PL analyzes, participation in strategic projects • Strategic Consulting, including business plan & sales strategy development. • Projects cooperation - standardization and optimization of logistics processes, warehouse layout proposals, stock levels set up • Supply chain coordination, 3PL analyzes, participation in strategic projects
-
-
-
Visteon Corporation
-
United States
-
Motor Vehicle Manufacturing
-
700 & Above Employee
-
Senior MP&L Manager
-
Apr 2017 - Jan 2021
• Oversight for the overall MP&L operations of a corporation or business • Responsible for supply chain of corporation customers OEM groups : German ( BMW, VW, Daimler ) French ( PSA, RSA ) and FORD • Managing MP&L team - approx. 140 people (7 direct reports): CS - customer service, RFU - Supplier release and follow up, ECN - New model and engineering change, warehouse, process and leadership dept. • Direct reporting to plant manager and corporate Vice Presidents levels • Budget preparation, CAPEX, KPI monitoring, Delivery performance • Implementer of best practice MP&L vision for instrument clusters & body controller modules production, strategy, policies, processes and procedures according the customer requirements, ISO norms, IATF 16949 standards Show less
-
-
-
XPS bv
-
Netherlands
-
Printing Services
-
1 - 100 Employee
-
Logistics Manager
-
Apr 2006 - Aug 2014
Responsible for : • Logistics and customer service team - approx. 50 people • Yearly budget • coordination of the customer's orders with the other departments ( sales, production, engineering ) • Transport ( inbound/outbound ) , land/sea/air mode, contracts , delivery analyses, monitor quality of deliveries, damage ratio ( C.A.R reports ) • KPI reporting ( CRDD,OTIF, MOS- stock coverage,VMI, inventory value raw material, empties and finish products, vendor delivery performance, ... ) • Managing stock levels in Nizna ( Slovakia ), Venray ( Netherland ), Macedon ( U.S.A ), for express bussiness in Rhiem ( Germany ), calculating safety stock levels, MIN/MAX levels • Operative of XPS distribution centrum in Macedon ( U.S.A ) • Administrative support for division MTG in XYTECH Suzhou ( China ) • Operative of XICLADO - empties collection unit in Nizna ( Slovakia ) • Sourcing activities - tender footprint, ROI analyzes, negotiations with the suppliers • approval and monitoring of the purchase orders ( direct / indirect material and services ) • Setting objectives to achieve budget Implementator of : • 5S lean methodology • Logistics structure ( warehouse, inbound/outbound, customer service , purchasing, Xpress bussiness ) • Transport schedule and network • Lean processes in customization unit ( Xpress bussiness ), private label bussiness to improve flexibility, one piece flow, Owner of : • ISO documentation for logistics • Raw material stock levels • Non binding vendor's forecast • Counting procedures ( spot check, balance sheets, delta analyzes ) Show less
-
-
-
PUNCH CAMPUS
-
Namestovo - Slovakia
-
Buyer
-
Feb 2005 - Mar 2006
• Purchasing material for Philips project as power supplies for DVD, Satellite, Subwoofer, LCD etc.; electrical materials; consumable material as tin, glues, flux, packing etc. and for Baumatic project as robot milking solution, Tecan – medicine production, Gotive – GPS systems from European as well as Asian suppliers, by land, sea and air transport • Responsible for alternatives in case of missing parts for production using distributors from Europe and America, mainly by air • Management of stock including working on the improvement of the efficiency of stock material • Management and optimization of consignment stock, reporting, administration • Evaluation of suppliers • Organizing tenders and initial purchasing for new suitable suppliers and forwarders, including negotiations • Communication with the customer about availability and timing of production and deliveries • 5S auditor • SAP trainer for purchasing module • Experience with SAP logistics module, English version Show less
-
-
-
Panasonic
-
Japan
-
Appliances, Electrical, and Electronics Manufacturing
-
700 & Above Employee
-
Purchase Agent
-
Jan 2003 - Jan 2005
Purchasing material from Asian and European countries for production of transformers and line filters • Controlling stock of the materials and placing Direct Material Purchase orders needed for production • monitoring EDI orders • Directly responsible for material availability as per production request and solving any shortages • Monitoring changes in planning and managing reschedule in, out and cancellation based on changes • Window person for suppliers • Managing of transport by land, sea and air forwarders • Arranging and tracking deliveries from world wide suppliers and dealing with those suppliers having correct shipping documents • Evaluating suppliers based on internal rules • Planning material and production availability where stock is only held for production for less then 3 weeks • SAP logistics module experience Show less
-
-
-
DUKOL s.r.o
-
Trstena - Slovakia
-
Junior Sales Representative
-
Nov 1996 - Oct 1997
Responsible for : • customer requirements on electronic department • Managing customers orders of company O.V.P ( Company Store ) • Orderings of spare parts • Handling the claims, administration • Monthly and annual counting reporting Responsible for : • customer requirements on electronic department • Managing customers orders of company O.V.P ( Company Store ) • Orderings of spare parts • Handling the claims, administration • Monthly and annual counting reporting
-
-
Education
-
SPS Tvrdosin
Oznamovacia technika
Community
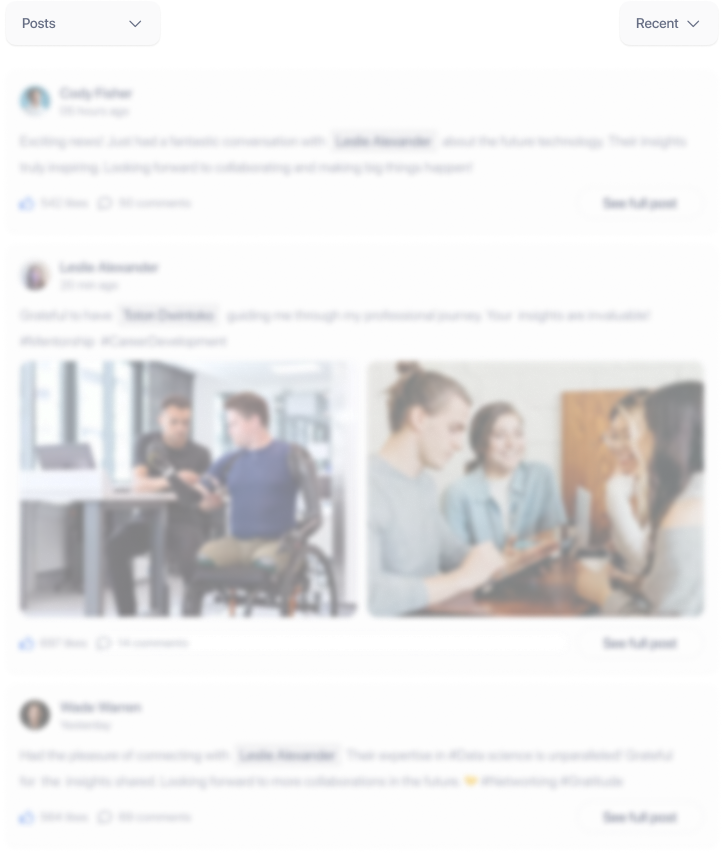