Martha C.
Quality Coordinator at Teckro- Claim this Profile
Click to upgrade to our gold package
for the full feature experience.
Topline Score
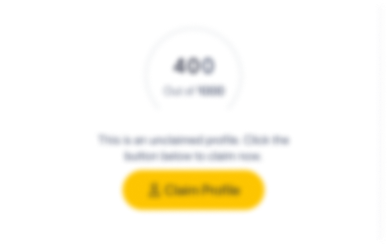
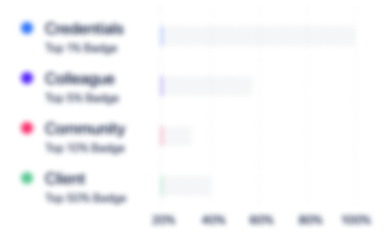
Bio


Credentials
-
Six Sigma Certification in Green belt
SigmaPro - Business Transformation SpecialistsAug, 2017- Nov, 2024 -
Certificate in the Basic Methodology for Project Management (PMBOK)
ITera Process EspañaApr, 2017- Nov, 2024 -
Internal Quality Auditor Certificate ISO 9001 2015
Applied Quality Process Consultors (AQP)Nov, 2016- Nov, 2024
Experience
-
Teckro
-
Ireland
-
Software Development
-
100 - 200 Employee
-
Quality Coordinator
-
Oct 2022 - Present
-
-
-
Be Independent Home Care Ltd
-
Ireland
-
Hospitals and Health Care
-
1 - 100 Employee
-
Healthcare Assistant
-
Sep 2021 - Oct 2022
• Organized and maintained medication closets and first aid supplies. • Assisted with patient hygiene, physical comfort, eating and drinking and mobility while observing and reporting specific changes. • Delivered high standard of holistic care to patients to promote equality and dignity. • Organized and maintained medication closets and first aid supplies. • Assisted with patient hygiene, physical comfort, eating and drinking and mobility while observing and reporting specific changes. • Delivered high standard of holistic care to patients to promote equality and dignity.
-
-
-
Servicios de Agua y Drenaje de Monterrey IPD
-
Mexico
-
Utilities
-
100 - 200 Employee
-
Compliance & Quality Operations Analyst
-
Mar 2014 - Mar 2020
• Recorded findings of inspection process, collaborating with quality team to implement corrective actions. • Provided regular updates to team leadership on quality metrics by communicating consistency problems or production deficiencies. • Routinely tested products to align temperature, specifications and ingredient levels with best practices and quality standards. • Fixed identified issues to improve workflows. • Monitored product standards and quality-control programs. • Educated employees on specific QA standards and confirmed maintenance of standards. • Created and collaborated in implementation and maintenance of customer complaint log. • Updated inspection journals and daily summary logs with quality-related data. • Developed monthly, end-of-quarter and other statistical reports for leadership team and quality improvement programs. • Collaborated with management to provide training on improved processes and assisted with creation and maintenance of quality training. • Interpreted test results by comparing to established specifications and control limits, making recommendations on appropriateness of data for release. • Implemented Six sigma studies which led to the reduction the Energy consumption from 54Kwh to 50Kwh. • Completed supporting documentation for testing procedures, data capture forms, equipment logbooks and inventory forms. • Drove corrective actions to accomplish project closure and recurrence control. • Recommended revisions to internal controls and operational and management policies and procedures. • Developed training protocols in alignment with company quality standards and ISO 9000 regulations. • Developed action plan for company certification using ISO 9000 standard knowledge. and engineering specifications to meet contract compliance regulations of the Maintenance Management headquarters, following the ISO 9001-2015 process, to be approved by the AVL (Approved Vendor List). Show less
-
-
-
Essity
-
Sweden
-
Manufacturing
-
700 & Above Employee
-
Quality Control Inspector
-
Jul 2013 - Feb 2014
Kronos System Management. -Responsible for the Quality Management System. -Project 5 in the Quality Department. -Include 5 minute security talks. -Parets and comparative analysis of quality defects. -Attention to customer and supplier claims. -In charge of the calibration requirements of the measuring equipment. -Support to the Auditor of Materials with the update of Characteristics of New Products. -Support to the TPM team supervised by the auditors of the Quality Department. Show less
-
-
-
SCA
-
Sweden
-
Paper and Forest Product Manufacturing
-
700 & Above Employee
-
Quality Control Analyst
-
Jul 2011 - Jun 2013
• Conducted data review and followed standard practices to find solutions. • Provided regular updates to team leadership on quality metrics by communicating consistency problems or production deficiencies. • Developed monthly, end-of-quarter and other statistical reports for leadership team and quality improvement programs. • Inspected incoming products for adherence to labeling laws and company quality standards. • Inspected raw materials and finished products to verify quality and disposed items that did not meet safety requirements. • Planned and implemented performance improvement and quality assurance programs. • Reviewed and validated quality requirements for manufacturing planning, supplier purchase orders and engineering specifications to meet contract compliance regulations. • Instructed vendors or contractors on quality guidelines, safety procedures, testing procedures and ways to eliminate deficiencies. • Determined root cause of deviations and non-conforming results and implemented appropriate corrective and preventive actions throughout product development process. • Monitored KPIs to proactively address bottlenecks and quality issues. • Developed training materials, SOPs and work instructions to supplement new team member onboarding. • Participated in available trainings to improve the program TPM (Total Productive Maintenance). Show less
-
-
Education
-
Griffith College Dublin
Posgraduate Diploma, Global Brand Managment -
Universidad Tecmilenio
Master in Business Administration with Productivity and Quality, Quality Control -
Universidad Tecmilenio
Industrial Engineer, Business Administration and Management, General
Community
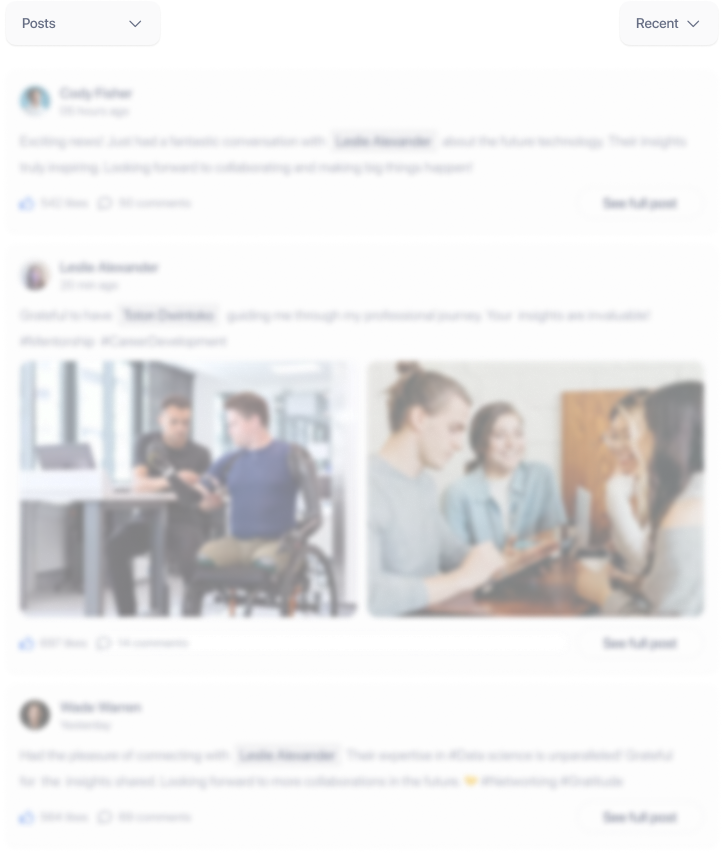