Miguel Arredondo
Operations Consultant at Mexico Operations & Supply Chain Problem Solving- Claim this Profile
Click to upgrade to our gold package
for the full feature experience.
-
Spanish Native or bilingual proficiency
-
English Native or bilingual proficiency
Topline Score
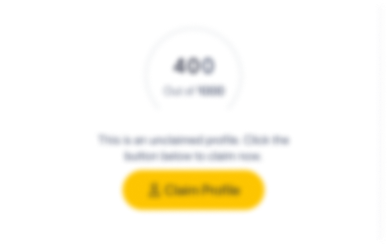
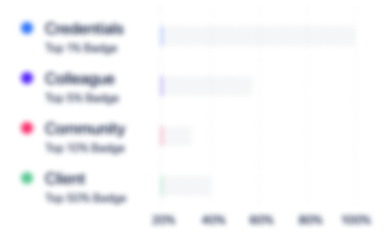
Bio

Gilberto Garcia
I had the opportunity to work with Miguel in my time at Methode Monterrey, his plant supply 85% of the plastic and paint components to my plant, in the beginning his plant has a lot of quality and delivery opportunities, but Miguel and his team was able to turnaround the plant perfomance by implemented the right strategies and systems. Miguel is a strong leader and great team player with a lot of experience and will be an excellent addition to any organization.

Miguel Mata
Tuve la oportunidad de trabajar con Miguel Arredondo, su liderazgo y enfoque a resultados son su principal característica. Logra integrar su equipo de trabajo y conectar con todos los niveles su cargo, logrando siempre compromiso y excelente desempeño. Su capacidad para tomar decisiones es fundamental. Miguel Arredondo es una persona que recomiendo ampliamente por sus capacidades y su habilidades.

Cesar Fernando Carreon Fuantos
Tuve la oportunidad de trabajar directamente para el Ingeniero Arredondo y sin duda su orientación a resultados y su liderazgo nos llevó a todo el equipo a tener mejoras en cuanto a reducción de scrap y mejorar el margen y la productividad de nuestros proyectos tanto en producción como en lanzamiento, lo recomiendo ampliamente como un excelente lider y formador de equipos.

Gilberto Garcia
I had the opportunity to work with Miguel in my time at Methode Monterrey, his plant supply 85% of the plastic and paint components to my plant, in the beginning his plant has a lot of quality and delivery opportunities, but Miguel and his team was able to turnaround the plant perfomance by implemented the right strategies and systems. Miguel is a strong leader and great team player with a lot of experience and will be an excellent addition to any organization.

Miguel Mata
Tuve la oportunidad de trabajar con Miguel Arredondo, su liderazgo y enfoque a resultados son su principal característica. Logra integrar su equipo de trabajo y conectar con todos los niveles su cargo, logrando siempre compromiso y excelente desempeño. Su capacidad para tomar decisiones es fundamental. Miguel Arredondo es una persona que recomiendo ampliamente por sus capacidades y su habilidades.

Cesar Fernando Carreon Fuantos
Tuve la oportunidad de trabajar directamente para el Ingeniero Arredondo y sin duda su orientación a resultados y su liderazgo nos llevó a todo el equipo a tener mejoras en cuanto a reducción de scrap y mejorar el margen y la productividad de nuestros proyectos tanto en producción como en lanzamiento, lo recomiendo ampliamente como un excelente lider y formador de equipos.

Gilberto Garcia
I had the opportunity to work with Miguel in my time at Methode Monterrey, his plant supply 85% of the plastic and paint components to my plant, in the beginning his plant has a lot of quality and delivery opportunities, but Miguel and his team was able to turnaround the plant perfomance by implemented the right strategies and systems. Miguel is a strong leader and great team player with a lot of experience and will be an excellent addition to any organization.

Miguel Mata
Tuve la oportunidad de trabajar con Miguel Arredondo, su liderazgo y enfoque a resultados son su principal característica. Logra integrar su equipo de trabajo y conectar con todos los niveles su cargo, logrando siempre compromiso y excelente desempeño. Su capacidad para tomar decisiones es fundamental. Miguel Arredondo es una persona que recomiendo ampliamente por sus capacidades y su habilidades.

Cesar Fernando Carreon Fuantos
Tuve la oportunidad de trabajar directamente para el Ingeniero Arredondo y sin duda su orientación a resultados y su liderazgo nos llevó a todo el equipo a tener mejoras en cuanto a reducción de scrap y mejorar el margen y la productividad de nuestros proyectos tanto en producción como en lanzamiento, lo recomiendo ampliamente como un excelente lider y formador de equipos.

Gilberto Garcia
I had the opportunity to work with Miguel in my time at Methode Monterrey, his plant supply 85% of the plastic and paint components to my plant, in the beginning his plant has a lot of quality and delivery opportunities, but Miguel and his team was able to turnaround the plant perfomance by implemented the right strategies and systems. Miguel is a strong leader and great team player with a lot of experience and will be an excellent addition to any organization.

Miguel Mata
Tuve la oportunidad de trabajar con Miguel Arredondo, su liderazgo y enfoque a resultados son su principal característica. Logra integrar su equipo de trabajo y conectar con todos los niveles su cargo, logrando siempre compromiso y excelente desempeño. Su capacidad para tomar decisiones es fundamental. Miguel Arredondo es una persona que recomiendo ampliamente por sus capacidades y su habilidades.

Cesar Fernando Carreon Fuantos
Tuve la oportunidad de trabajar directamente para el Ingeniero Arredondo y sin duda su orientación a resultados y su liderazgo nos llevó a todo el equipo a tener mejoras en cuanto a reducción de scrap y mejorar el margen y la productividad de nuestros proyectos tanto en producción como en lanzamiento, lo recomiendo ampliamente como un excelente lider y formador de equipos.

Credentials
-
Project Management
Harvard Business Publishing EducationFeb, 2022- Nov, 2024 -
PMP® PMBOK Training Course
HoneywellApr, 2006- Nov, 2024 -
Lean Six Sigma Black Belt Training
Stream Technologies @ HoneywellNov, 2005- Nov, 2024 -
Management Skills
ICAMI Centro de Formación y Perfeccionamiento DirectivoJun, 2001- Nov, 2024 -
Global Management
University of PhoenixApr, 1999- Nov, 2024
Experience
-
Mexico Operations & Supply Chain Problem Solving
-
Mexico
-
Operations Consulting
-
1 - 100 Employee
-
Operations Consultant
-
Jan 2012 - Present
* Subject Matter Expert Consulting on Supply Chain definition, Nearshoring – related matters: Assessment, Development. RFQ Assistance. (MX + US, 1/12 – Current) * 2021 Remote & Onsite Freelance Consulting, surveys, follow-up reports and feedback for Kearney, IPS Services, others. * Training Sr Instructor for Solma Soluciones. o Tijuana (´15): On-site Operations Assessment at an acquisition target for a Customized D2C Sportswear Manufacturer; follow-up roadmap to improve operational performance (Cost & Lead-Time to Customer Orders) and support growth plan. o Miami FL (’12), Working with Materials Manager, implemented ERP, prioritized Production Planning and Scheduling, improving machine utilization; and eliminating past-due backlog at an Engineered Plastic Components Manufacturer. * Sr Operations Consultant, Ambe Engineering (Automotive Consultants): o Bajío: Operational and System Assessment at Automotive Electric Motor Tier 1. ID’d Cost Reductions o Mexico City: Operational Assessment at Truck Fuel Tank Manufacturer. Identified Process, Cost Reduction Opportunities. o Saltillo: Heavy Truck Fluid Transfer Tier 1 Supply Chain issues, lacking standard work and frequent quality escapes. Traced to weak APQP and a poorly executed US transfer. Assisted on OEM Audit, recommended and helped with Corrective Actions. Show less
-
-
-
ISGO MANUFACTURING
-
Mexico
-
Plastics Manufacturing
-
1 - 100 Employee
-
Director for New Business & Projects
-
Sep 2021 - Present
* Special Projects related to profitability and future growth. * Focused on profitability in light of Volatile 2021 environment: Achieved $800K+ in cost recovery so far. * Tier 1 Status at Stellantis, 2022 National Exporters' Award
-
-
Director of Operations
-
Dec 2018 - Oct 2021
P&L responsible for 4 business units, while supporting aggressive Sales growth (40%) to US$90M, supported by $8M+ CapEx investments. Standardized key Processes to Support a Market-Centric reorganization. o Central Tool: New stand-alone unit after purchasing and consolidating a Canadian toolmaker. Work on Business Plan.o MTY: Restructure (staff replaced) to align with expected business. 30% Reduction in Labor Costs & idle equipment. o SLP: Realigned organization for efficiency. Achieved PO Supplier of the Year, Audi Tier 1 Status. o Puebla: Plant Start-Up with key OEM program. o Customers: Audi, GM; Most Auto T1s; for GM, Daimler, Ford, VW-Audi, Tesla, BMW, Nissan, Toyota, Honda, Rivian, CAT. Show less
-
-
-
NORMA Group
-
Germany
-
Industrial Machinery Manufacturing
-
700 & Above Employee
-
Plant Manager
-
Sep 2017 - May 2018
• ~400 people growing plant with complex Culture issues in Quality, Service, PM, CapEx allocation and Customers (Ford, FCA, BMW, VW, Daimler, Volvo and other Tier 1s) • Brought 9 different NPI programs back on schedule (out of 30+), addressing Program Management shorts. • Finalized a troubled Connectors BU transfer, starting new Injection Molding and Extrusion processes. • ~400 people growing plant with complex Culture issues in Quality, Service, PM, CapEx allocation and Customers (Ford, FCA, BMW, VW, Daimler, Volvo and other Tier 1s) • Brought 9 different NPI programs back on schedule (out of 30+), addressing Program Management shorts. • Finalized a troubled Connectors BU transfer, starting new Injection Molding and Extrusion processes.
-
-
-
MMI Engineered Solutions
-
Motor Vehicle Manufacturing
-
1 - 100 Employee
-
Plant Manager
-
Jan 2016 - Sep 2017
• Green Field to First Shipment in 10.5 months for a high-growth Private Company’s first international expansion; Navistar, Paccar. • Green Field to First Shipment in 10.5 months for a high-growth Private Company’s first international expansion; Navistar, Paccar.
-
-
-
Inteva Products
-
United States
-
Motor Vehicle Manufacturing
-
700 & Above Employee
-
Injection Molding Manager
-
Aug 2014 - Jan 2016
• Preventive Maintenance + Troubleshooting = Scrap -30% (98.8% Yield), OEE +12%; Mold C/O to 47 mins, Expenses cut 12%. • Scope: 360 people, 40 presses (up to 3000T) @ 92% Capacity; for GM, Daimler, Paccar, Navistar, VW, Tesla. • Preventive Maintenance + Troubleshooting = Scrap -30% (98.8% Yield), OEE +12%; Mold C/O to 47 mins, Expenses cut 12%. • Scope: 360 people, 40 presses (up to 3000T) @ 92% Capacity; for GM, Daimler, Paccar, Navistar, VW, Tesla.
-
-
-
Methode Electronics
-
United States
-
Appliances, Electrical, and Electronics Manufacturing
-
700 & Above Employee
-
Plant Manager
-
Aug 2013 - Feb 2014
• Executed on “Flying Pigs” Turnaround Plan returning to profitability in 7 months after 4 years in the red. • OEE: +13%; ePPMs -92%, iPPMs -77%; Scrap -35%; Mold Change-Over (SMED) -75%; DOS -17%; ISO/TS-16949 certification on 1st try. Scope: 3 Focus Factories, 2 buildings (130K ft2); ~700 people, 60 IM Cells (25-750T) + 4 Paint Lines + Assembly for Methode Electronics (Ford, GM), Electrolux, LG, GE-Mabe, Schneider • Executed on “Flying Pigs” Turnaround Plan returning to profitability in 7 months after 4 years in the red. • OEE: +13%; ePPMs -92%, iPPMs -77%; Scrap -35%; Mold Change-Over (SMED) -75%; DOS -17%; ISO/TS-16949 certification on 1st try. Scope: 3 Focus Factories, 2 buildings (130K ft2); ~700 people, 60 IM Cells (25-750T) + 4 Paint Lines + Assembly for Methode Electronics (Ford, GM), Electrolux, LG, GE-Mabe, Schneider
-
-
-
Nidec Leroy-Somer
-
France
-
Appliances, Electrical, and Electronics Manufacturing
-
700 & Above Employee
-
Plant Manager
-
Mar 2013 - Aug 2013
• Customer focus to win new business (CAT, Generac) 94% OTD, ePPMs -60%; restarted 12 late programs, Downtime -50% • Customer focus to win new business (CAT, Generac) 94% OTD, ePPMs -60%; restarted 12 late programs, Downtime -50%
-
-
-
TydenBrooks
-
United States
-
Transportation, Logistics, Supply Chain and Storage
-
100 - 200 Employee
-
General Manager
-
May 2012 - Mar 2013
• Improved Profitability by 34% at a plant that carried 75% of EBITDA for a P/E -owned Company ($36M Sales, 235 people) by realigning organizational roles to focus on KPIs and Customers + Lean Tools (OEE (40% to 82%) + other Lean tools. • Focus on transaction integrity + ERP Process alignment Inventory Accuracy (40% to 90%+ in 3 mos) + No Losses ($1m/ yr). • Reduced Cost of Poor Quality by 30% through processes like MRB, Defect Triggers and effective Corrective Action. • Improved Profitability by 34% at a plant that carried 75% of EBITDA for a P/E -owned Company ($36M Sales, 235 people) by realigning organizational roles to focus on KPIs and Customers + Lean Tools (OEE (40% to 82%) + other Lean tools. • Focus on transaction integrity + ERP Process alignment Inventory Accuracy (40% to 90%+ in 3 mos) + No Losses ($1m/ yr). • Reduced Cost of Poor Quality by 30% through processes like MRB, Defect Triggers and effective Corrective Action.
-
-
-
Lite-On Mobile Mechanical
-
Appliances, Electrical, and Electronics Manufacturing
-
100 - 200 Employee
-
General Manager
-
May 2006 - Aug 2012
• 180K sqft 1,200 ppl, Mold + Paint + Assembly + US legal entity. • Ops: Used of Lean-6Sigma tools to achieve major gains in a state-of-the-art operation 25% overall cost reduction, Cut Inventory by >50%, 21 DOS. • Sales: Designed, executed plan to leverage capabilities, broaden Customer-Base and improve Margins. 2011 Sales: $5M $12M (PO) expanding into Automotive, Industrial, Appliances, Consumer markets. • Hired as Plant Engineering Manager (Plant Startup, Maintenance, Automation); then Paint Workshop Mgr) where we took quality to 6-Sigma Level, and fixed output to 500K pcs/wk. Promoted to Ops Manager (Molding + Paint + Assembly), implemented OEE. Show less
-
-
-
Honeywell
-
United States
-
Appliances, Electrical, and Electronics Manufacturing
-
700 & Above Employee
-
Regional Commodity Manager
-
May 2004 - May 2006
• Program Management + Supplier Development Role for Aerospace Product Transfers: Using a Supplier Capability vs a Part Spec Matrix, my 2 Program Managers and I achieved 18% average savings in over 100 Part Numbers. • Program Management + Supplier Development Role for Aerospace Product Transfers: Using a Supplier Capability vs a Part Spec Matrix, my 2 Program Managers and I achieved 18% average savings in over 100 Part Numbers.
-
-
-
Novares Group
-
France
-
Motor Vehicle Manufacturing
-
700 & Above Employee
-
Engineering Manager
-
Sep 2002 - Mar 2004
• Successfully led all Engineering functions (Product, Process (IM, Paint, Deco), Industrial, RFQ, NPI, CapEx) for 9 programs. • Customers: Pioneer Audio (Ford), Visteon (Ford, Jaguar), TRW (Dodge, Jeep). • Successfully led all Engineering functions (Product, Process (IM, Paint, Deco), Industrial, RFQ, NPI, CapEx) for 9 programs. • Customers: Pioneer Audio (Ford), Visteon (Ford, Jaguar), TRW (Dodge, Jeep).
-
-
-
Outokumpu
-
Finland
-
Mining
-
700 & Above Employee
-
Plant Manager
-
Sep 2000 - Sep 2002
Full P&L responsibility for small site. Used Lean, Visual Factory to eliminate backlog, increase Output by 165%, Productivity by 79%. Full P&L responsibility for small site. Used Lean, Visual Factory to eliminate backlog, increase Output by 165%, Productivity by 79%.
-
-
-
Thomas & Betts a member of the ABB Group
-
United States
-
Appliances, Electrical, and Electronics Manufacturing
-
1 - 100 Employee
-
Engineering & Maintenance, Eng & QA Mgr
-
Sep 1999 - Sep 2000
• Zamak Injection Process, leading a team of 24. Clean up KPI’s traceability. Overhaul QA Manual for ISO Recertification and better data analysis. Redefined Roles and Systemic approach under “project driven organization” focus. • PPMs down 50%; CoPQ halved to 2.6%; Customer Response times down from 1 week to 8 hours); Maintenance Headcount cut (35 people) with Service up. • Zamak Injection Process, leading a team of 24. Clean up KPI’s traceability. Overhaul QA Manual for ISO Recertification and better data analysis. Redefined Roles and Systemic approach under “project driven organization” focus. • PPMs down 50%; CoPQ halved to 2.6%; Customer Response times down from 1 week to 8 hours); Maintenance Headcount cut (35 people) with Service up.
-
-
-
Mattel, Inc.
-
United States
-
Manufacturing
-
700 & Above Employee
-
Plant Engineering Representative / Product Engineer
-
Jun 1992 - Sep 1999
• HQ-based Plant - Product Development Team Liaison (PM role) ; Transfers Support (US, MX, EU). Led 8 wk (10%) time –to-market improvement with >95% On-Time Production Start Ups. • Previous Roles at the Plant: (6/92 - 12/96): Product Development Engineer, Packaging Engineer. • HQ-based Plant - Product Development Team Liaison (PM role) ; Transfers Support (US, MX, EU). Led 8 wk (10%) time –to-market improvement with >95% On-Time Production Start Ups. • Previous Roles at the Plant: (6/92 - 12/96): Product Development Engineer, Packaging Engineer.
-
-
Education
-
Universidad de Monterrey
Bachelor of Arts (BA), Industrial Design -
ThePower Business School
Executive MBA, Business and Entrepreneurship
Community
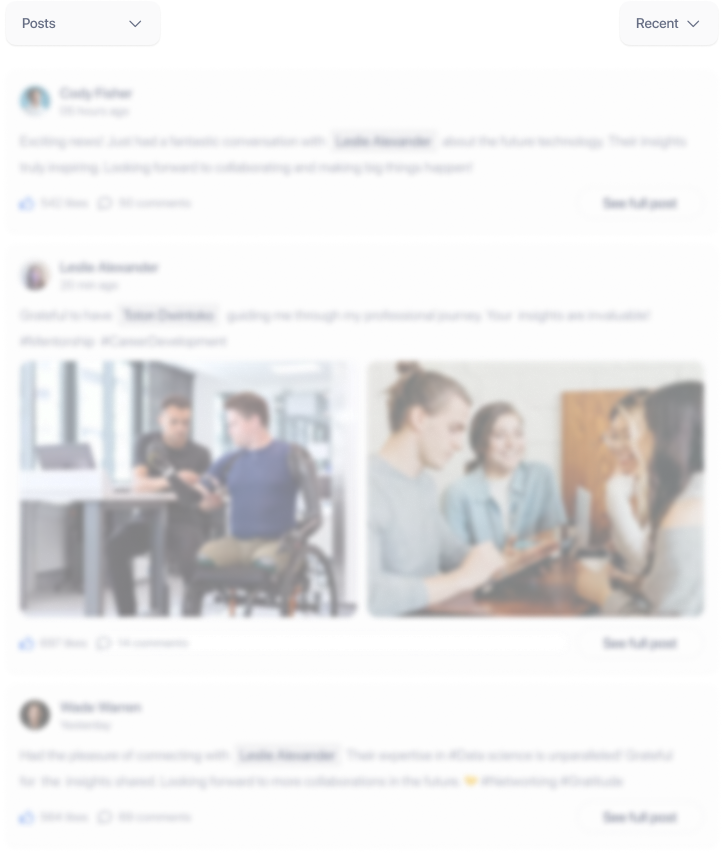