Mark Shepanski
Executive Director, Operations - Site Leader at Sherpa Clinical Packaging: A PCI Pharma Services Company- Claim this Profile
Click to upgrade to our gold package
for the full feature experience.
Topline Score
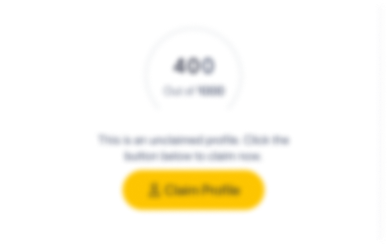
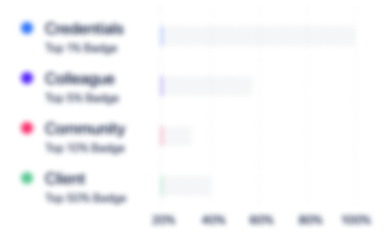
Bio


Experience
-
Sherpa Clinical Packaging: A PCI Pharma Services Company
-
United States
-
Pharmaceutical Manufacturing
-
1 - 100 Employee
-
Executive Director, Operations - Site Leader
-
Oct 2018 - Present
San Diego, CA
-
-
Senior Director of Quality
-
Jan 2017 - Oct 2018
San Diego, CA Responsible for the Quality functions at Sherpa Clinical Packaging. Sherpa provides clinical trial material management services for clinical studies phases I-IV, including packaging, labeling, distribution and returns/reconciliation, for pharmaceutical, biotechnology, medical device and dietary supplement companies. Sherpa specializes in labeling and packaging biologics and cold-chain logistics, but also handles solid-dose bottling. Directing the Quality functions.
-
-
Senior Director of Operations
-
Jan 2015 - Jan 2017
Greater San Diego Area Responsible for directing business operations including Materials Management and Production for Sherpa Clinical Packaging. I managed supply chain functions and personnel including: purchasing, receiving, inventory control, planning/scheduling, production control and shipping. I was focused on developing process improvements and capabilities that result in improved customer service, reduced cost, and increased efficiencies of personnel. I was responsible for managing ERP system and facility… Show more Responsible for directing business operations including Materials Management and Production for Sherpa Clinical Packaging. I managed supply chain functions and personnel including: purchasing, receiving, inventory control, planning/scheduling, production control and shipping. I was focused on developing process improvements and capabilities that result in improved customer service, reduced cost, and increased efficiencies of personnel. I was responsible for managing ERP system and facility infrastructure.
-
-
-
Quidel Corporation
-
United States
-
Medical Devices
-
1 - 100 Employee
-
Director, Quality Control
-
Aug 2009 - Jan 2015
• Develop Quality Control objectives for FDA and ISO 13485:2003 regulated medical device manufacturer. Collaborate with senior management team to integrate quality goals into corporate strategic plan. Support execution of strategic plan through manufacturing support operations, supplier management, internal audits, process improvement projects, product improvement and new product development projects. • Manage diverse group of 20 QC professionals to meet quality objectives in the… Show more • Develop Quality Control objectives for FDA and ISO 13485:2003 regulated medical device manufacturer. Collaborate with senior management team to integrate quality goals into corporate strategic plan. Support execution of strategic plan through manufacturing support operations, supplier management, internal audits, process improvement projects, product improvement and new product development projects. • Manage diverse group of 20 QC professionals to meet quality objectives in the administration of raw materials receiving inspection, in-process QC inspection, final product QC inspection, QC Chemistry, Customer Complaints, Stability Studies, Non-Conforming Materials, and Metrology. Effectively plan and manage an annual departmental budget exceeding $1M. • Direct and continuously improve quality systems associated with returned goods, corrective action, non-conforming materials, and inspection control plans. Identify and prioritize continuous improvement objectives. Direct resources and facilitate cross-functional groups to implement product and quality improvement initiatives.
-
-
Manager, Quality Control
-
Oct 2004 - Aug 2009
Managed 10 QC professionals to meet corporate quality objectives. Developed and managed annual departmental budget. Served Quality Assurance and Quality Engineering capacities when necessary. Achieved dramatic improvements in the performance of the QC Chemistry lab with regard to stability study system, complaint processing, and raw material testing. Manage QC Receiving Inspection area. Extensive experience in application Design Control system both as a new product development team member… Show more Managed 10 QC professionals to meet corporate quality objectives. Developed and managed annual departmental budget. Served Quality Assurance and Quality Engineering capacities when necessary. Achieved dramatic improvements in the performance of the QC Chemistry lab with regard to stability study system, complaint processing, and raw material testing. Manage QC Receiving Inspection area. Extensive experience in application Design Control system both as a new product development team member and as a stakeholder in the process. Oversee corporate Standards and Controls Program. Cooperatively lead corporate Herd Management program to manage goat, rabbit, and mouse herds that produce antibody raw materials for purification processes in manufacturing. Manage Senior Metrologist in overseeing corporate calibration program. Manage Final Product Inspection group. Lead and support multiple troubleshooting and investigation efforts to resolve manufacturing failures. Employ sound problem solving methodologies to identify root causes and implement effective, targeted corrective actions. Serve as internal auditor and member of external audit team. Participated as a Quality representative in third party audits including multiple ISO 13485:2003 recertification and surveillance audits, one USDA site inspection, and one FDA site inspection. Review and collaborate on many product, equipment, process, and software validations as a member and former chairperson of Validation Review Committee. Manage Non-Conforming Materials (NCMR) system. Responsible for the segregation, labeling, and disposition of all material identified as non-conforming. Chair Material Review Board (MRB) meetings to ensure material investigations are executed in a timely manner and appropriate material dispositions are made. Received three corporate Rising to Excellence Awards for contributions to successful corporate initiatives.
-
-
-
-
Manager, Process Development
-
2003 - 2004
• Responsible for analytical assay development and process improvement initiatives to enhance raw material characterization and achieve cost reductions by minimizing process/material variability. • Work on method development projects paved the way for the creation of a formal Analytical Methods Development Team which supports critical raw material characterization and qualification of QC standards.
-
-
Manager, Chemistry Manufacturing
-
2001 - 2003
• Managed up to seven production chemists in Protein Purification and Modification group. Improved process control, reduced scrap, led process scale-up projects, and improved efficiencies/process consistency resulting in increased product success rates. Implemented Lean Manufacturing principles in laboratory, set up Kanban systems, and lead Kaizen events. • Implemented multiple chromatography process improvements which resulted in elimination of product backorders due to technical… Show more • Managed up to seven production chemists in Protein Purification and Modification group. Improved process control, reduced scrap, led process scale-up projects, and improved efficiencies/process consistency resulting in increased product success rates. Implemented Lean Manufacturing principles in laboratory, set up Kanban systems, and lead Kaizen events. • Implemented multiple chromatography process improvements which resulted in elimination of product backorders due to technical failures.
-
-
-
-
Process Group Chemist
-
1998 - 2000
• Activities included performing ELISA assays, production scale protein purifications (affinity, ion-exchange, and size exclusion), antibody conjugations, and cell culture in support of H. pylori, fertility, and hCG product lines in a cGMP manufacturing environment. Implemented process scale up for cell culture, doubling output and presenting opportunity for next-generation product launch.
-
-
Education
-
Penn State University
BS, Biology, Vertebrate Physiology
Community
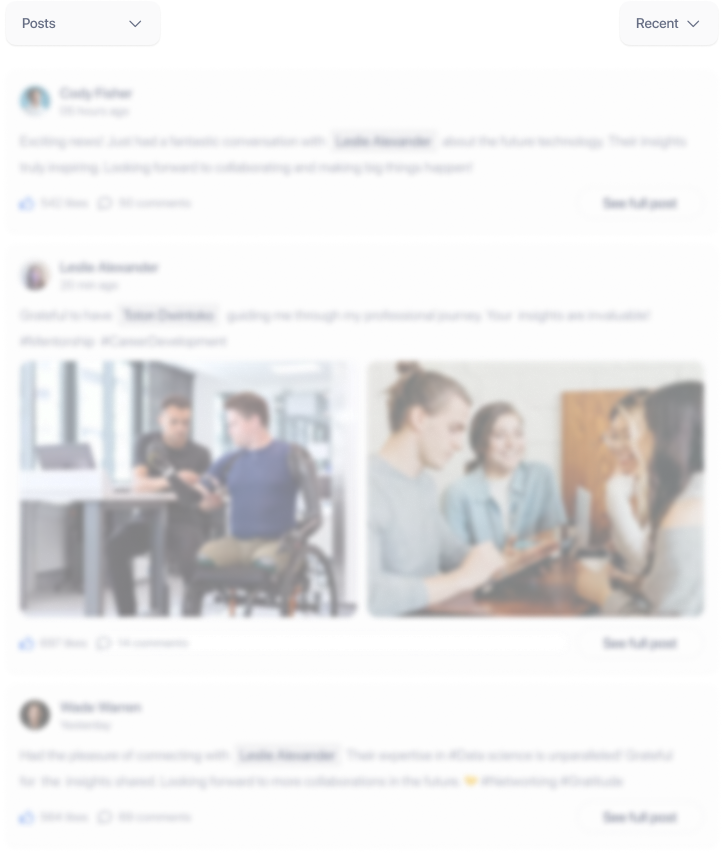