Mark Pincince
Sr. Lean Advisor at FTE Performance Consulting, Inc.- Claim this Profile
Click to upgrade to our gold package
for the full feature experience.
Topline Score
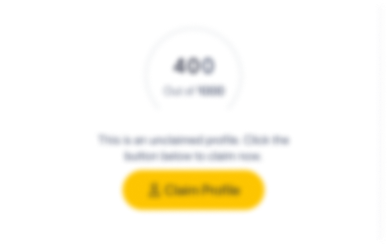
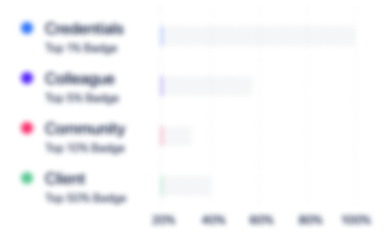
Bio


Experience
-
FTE Performance Consulting, Inc.
-
United States
-
Business Consulting and Services
-
1 - 100 Employee
-
Sr. Lean Advisor
-
Apr 2018 - Present
Various projects including: Process Stream Mapping, improvements identified, adjusted resources to rapidly respond to customer requirements. Various plant assessments, implemented standardized work, visual management/status at a glance techniques, identifly and implement process improvements for quality, productivity, and customer satisfaction. Reduced lead time through the elimination of waste. Projects to implement team concept techniques, team meetings, business plan deployment boards with status tracking, and drove communications between shifts.
-
-
-
General Motors
-
United States
-
Motor Vehicle Manufacturing
-
700 & Above Employee
-
Retired from GM
-
May 2016 - Present
-
-
Shift Leader General Assembly
-
Jun 2015 - May 2016
Responsible for daily operations of Trim Department in General Assembly. Successful build out of the Chevy Equinox and early launch of the Cadillac XT5. Improved throughput in General Assembly. Focused on Workstation readiness, quality, throughput, and standardized work for launch.
-
-
Plant Manager - CCA Product Distribution Center
-
Apr 2008 - May 2015
Responsible for operating 405,000 sq. ft. Product Distribution Center (PDC) with 44,000 part numbers and 120 total employees. Provided overnight delivery service to 450 customers shipping 23,000 lines per day. Consistent and sustained high performance regarding customer satisfaction, quality, productivity, and cost. Implemented the Global Manufacturing System (GMS) in a PDC warehouse.
-
-
Manager Global Lean Warehouse Operations
-
Feb 2006 - Apr 2008
Responsible for maintaining and improving common processes at template PDC facilities. Assigned as a Lean Coach to Operations Regional Directors to identify and eliminate waste, improve quality, productivity, and profitability. Implement the Global Manufacturing System (GMS) throughout the region (US).
-
-
Manager Lansing Liaison Office
-
Dec 2003 - Feb 2006
Developed and managed a two year "Lean" training program for high potential employees. The office was located at the Lansing Grand River Assembly plant that had fully implemented GM's Global Manufacturing System (GMS). Program was developed and based upon a learn, teach, and implement philosophy. Developed employees for placement in manufacturing leadership assignments.
-
-
GMS Advisor
-
May 2002 - Dec 2003
Responsible for the implementation of GMS principles and elements at a brown field facility to support the launch of the Chevrolet SSR. Was the People Involvement Champion and led the training and implementation for this principle. Led implementation of team concept by clearly defining roles, responsibilities and skill set requirements. Conducted GMS shop floor training for all levels of plant leadership.
-
-
Sr. Lean Manufacturing Advisor
-
Jun 2000 - May 2002
Two year Lean Manufacturing developmental Assignment at NUMMI (GM/Toyota joint venture) to obtain a working knowledge of the Toyota Production System. The primary focus of the assignment was to learn, teach and implement Lean principles. Led customized workshops for GM Leadership and Manufacturing Launch Teams. Worked as a Lean Consultant in various industries. Performed on-site assessments, developed improvement plans, and implemented Lean Principles. Significant improvements in employee engagement, standardized work, quality and cost were achieved.
-
-
Project Manager OTD (Order to Delivery)
-
Sep 1999 - Jun 2000
Truck Project Team member working on strategies to expedite "sold orders" through the scheduling system and assembly plant build process to reduce vehicle assembly lead times for customers.
-
-
Industrial Engineering Supervisor
-
Nov 1997 - Sep 1999
Responsible for General Assembly planning and execution of line speed, model changes, productivity improvements and manpower targets. Also, responsible for indirect labor, ergonomics, plant layout and throughput simulation studies. Led training of workforce in standardized work, scrolling, waste elimination, and job set-up's.
-
-
Supervisor of Industrial Engineering / Competitive Manufacturing
-
Oct 1994 - Nov 1997
Responsible for managing resident Industrial Engineering teams implementing lean manufacturing concepts including quality Andon, material pull systems and workplace organization (5S) at full-size truck assembly plants. Coordinated the advanced Industrial Engineering activities for the Arlington Assembly plant conversion (car to truck) including competitive benchmarking and headcount target development.
-
-
Sr. Project Engineer
-
Oct 1991 - Oct 1994
Worked on manufacturing team for the GMT-600 full size van program. Worked with product engineers to develop components designs to support Design for Manufacturability (DFM) for both the Suppliers and the Assembly Plant. Assessed Suppliers manufacturing capability, documented their costs, analyzed their bids, and tracked engineering changes. Worked on set up of the engine line and glass installation processes at Wentzville Assembly.
-
-
Sr. Industrial Engineer
-
Sep 1989 - Oct 1991
Responsible for conducting detailed analysis of component suppliers manufacturing plants and processes. Worked as a Supplier Cost Engineer and technical advisor supporting the GM Purchasing Organization. Analyzed and documented Suppliers' manufacturing costs including material, labor, burden, selling/general administrative expense and profit utilizing activity based costing techniques. Provided specific recommendations to eliminate waste, improve throughput and reduce cost resulting in renegotiated component prices.
-
-
Industrial Manufacturing Engineer
-
Apr 1986 - Sep 1989
Plant Industrial Engineer. Applied "theory of Constraints" techniques to significantly increase capacity and thoughput at the plant.
-
-
Industrial Engineer
-
Jun 1985 - Apr 1986
-
-
Education
-
The University of Texas at Arlington
BS Industrial Engineering -
Central Michigan University
Master’s Degree, Administration
Community
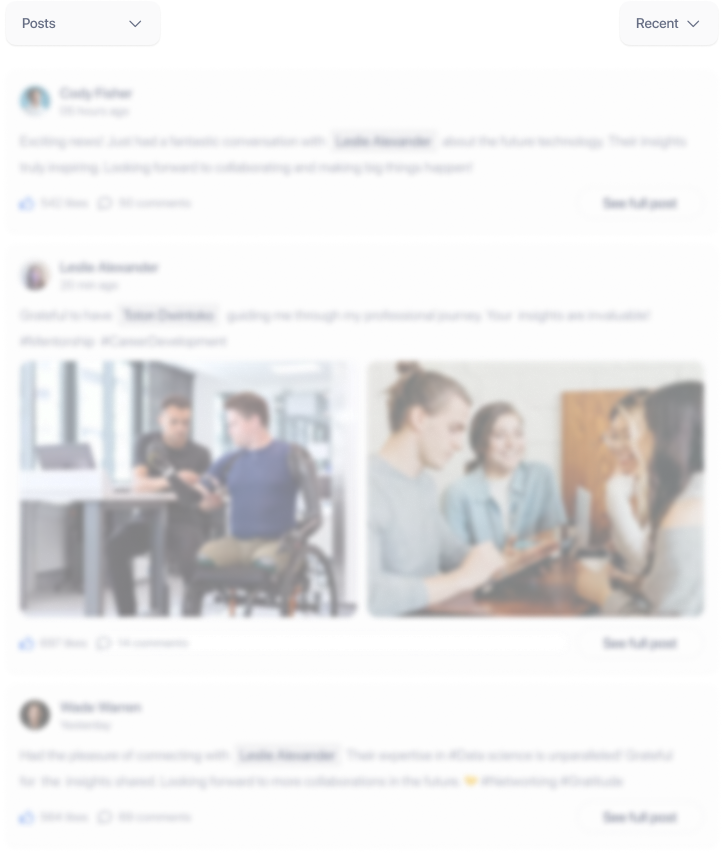