Mark Lusk
Quality Management - Systems Lead at Wabtec- Claim this Profile
Click to upgrade to our gold package
for the full feature experience.
Topline Score
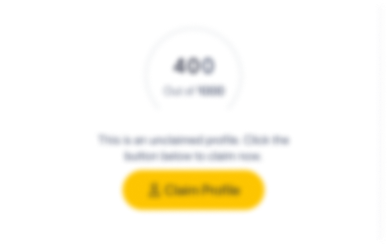
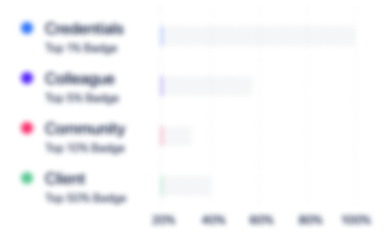
Bio
0
/5.0 / Based on 0 ratingsFilter reviews by:
Credentials
-
ASQ CQA
ASQ
Experience
-
Wabtec
-
Sweden
-
Railroad Equipment Manufacturing
-
100 - 200 Employee
-
Quality Management - Systems Lead
-
Apr 2023 - Present
Expand role to include Internal Quality System Auditing of Wabtec Manufacturing locations throughout North America. Also promote and Audit Special Processes and act as Subject Matter Expert for all Heat Treating activities.
-
-
Senior Manufacturing Quality Manager
-
Feb 2021 - Present
Managed a Quality Team to machine and assemble Electric Drive Systems and Control Groups for Off Highway Vehicle (OHV) Mining Trucks up to 400 Ton. Machined large forging and casting to become Wheel Drive Transmissions. Various large Vertical Turning Centers (VTC), Horizonal Boring Machines (HBM), Gear Cell, Tooth roughing, Induction Hardening, Grinding, CMM, Washing, Weld, Assembly. Responsibly for Gage Calibration, developing Procedures and Work Instructions to satisfy an ISO 9001 QMS. All aspects of employee development, goals and objectives, interview and hire. Show less
-
-
-
BENTELER Group
-
Austria
-
Motor Vehicle Manufacturing
-
700 & Above Employee
-
Manager of QA/QC
-
May 2019 - Jun 2020
Managed a Quality Assurance and Quality Control department in a heavy manufacturing environment, producing seamless steel tube in a 5-year-old state of the art Tube Mill. Product was Casing, Line Pipe and Mechanical Tubing. (ISO and API Certified). I was responsible for bringing knowledge acquired from decades of experience in multiple industries, delivering high quality products, minimizing waste, maximizing productivity. This is accomplished through proven Quality principles such as Continuous Improvement, Lean Six-Sigma, Corrective and Preventive Action programs, Risk assessments, Statistical Process Control and Process Capability studies. My primary goals are always to educate and facilitate projects that improve Key Performance Indicators, reduce all sources of variation, drive customer satisfaction metrics and sustain growth and profit. I bring concepts learned from the Automotive Industry such as FMEA (Failure Mode Effects Analysis), Kaizen, Value Stream Mapping, Lean and others. I am driven to teach and lead. I work closely with other departments to build or improve systems that drive out waste, expose variation and implement Corrective / Preventive Actions. (Mass Covid layoff) Show less
-
-
-
Dril-Quip
-
United States
-
Oil and Gas
-
700 & Above Employee
-
Quality Assurance Manager / Quality Systems Manager
-
Jan 2019 - May 2019
-
-
Global Quality Systems Manager
-
Oct 2013 - May 2019
Manage a Quality Systems department responsible for the Internal Audit Program, Corrective and Preventive Actions, Root Cause Analysis, Document Control - Distribution and Access. External Certification with API, VAM and A2LA. Transition to API Q1 9th Edition, developed new Quality Systems Manual and Conformity Matrix.
-
-
-
OneSubsea
-
United States
-
Oil and Gas
-
700 & Above Employee
-
Global Quality Manager, Subsea Manifolds Group
-
Dec 2012 - Oct 2013
Manage a Global network of Site QA Managers and Site QC Specialists supporting fabrication yards around the world, representing the largest Oil and Gas exploration projects on earth. (Virtual Manifold Group dissolved).
-
-
Project Quality Manager
-
May 2009 - Dec 2012
Managed the Quality activities at various sites around the world, supporting a large Subsea Project for the Gulf of Mexico. Developed Project Quality Manual, Project Quality Plans and provided an integral Quality interface between Client and Cameron.
-
-
-
Mahle
-
Germany
-
Motor Vehicle Manufacturing
-
700 & Above Employee
-
Quality Manager - Plant Metallurgist
-
Apr 2005 - Apr 2009
• Total Management responsibility over a 15 person Quality department which includes all Heat Treating and Inspection activities. Total plant is ~250 employees. • As Quality Manager I was part of an 8 person Plant Operating Committee (Staff) managing a $55M/Year, nonunion heavy manufacturing facility. • Product is heavy duty steel camshafts. Processes include Turning, Milling, Drilling, Carburizing, Straightening, Grinding, and super finishing for customer such as: Caterpillar, Cummins, Detroit Diesel, John Deere, Navistar and others. • My responsibilities include developing budgets, forecasts, strategic and capital planning, customer satisfaction, external PPM, supplier quality, over time, and other financial indicators. Accomplishments include reducing internal scrap from 5-6 % of sales to under 2%, reducing total quality costs from as high as 8% to under 4%. • Continuous Improvement activities include developing scrap data bases and paretos, modernizing the Metallurgical Lab capabilities, maintaining TS16949 registration and all Quality Management Systems that support it. • Heavily involved with implementing Lean principles, Kaizen, 5S, Visual Management, TPM, APQP and PPAP. Show less
-
-
-
GKN Driveline
-
France
-
Motor Vehicle Manufacturing
-
1 - 100 Employee
-
Plant Metallurgist
-
Nov 2000 - May 2005
• Total Management responsibility over an 8-person Metallurgical Lab providing plant wide support to all heat treating and welding activities. Tier 1 supplier to Toyota, Honda, Saturn, Ford, GM • Equipment includes ~20 multi station Induction Hardeners, some with robotic material handling. 2 Batch and 2 continuous gas carburizing furnaces for heat treating automotive driveline components. As Plant Metallurgist I was involved with all areas of material evaluation and selection as well as investigation of warranty returns and field failures. Mechanical Engineering and Quality Engineering responsibility for the Heat Treatment department. • I participated on many continuous improvement teams charged with reducing set-up times, variation and waste in all areas of manufacturing in focused Kaizen events. • Managed a Met Lab with state of the art sample preparation equipment, manual and automatic Vickers/Rockwell hardness testing equipment, full featured metallography, failure analysis, digital imaging and report generation. • Responsible for evaluation and selection of new equipment and developing systems to reduce turn around time on production inspections. • Developed extensive databases to consolidate set-up parameter information and inspection criteria for all Induction Hardening equipment as well as Metallurgical Heat Treat results. • As QS-9000 / TS16949 Coordinator I had extensive involvement with all Quality System activities, Internal auditing, management reviews and document control. Rewrote entire quality system, consolidated and reformatted all procedures and managed Web based access to all procedures and forms. Acted as Quality representative for all third party quality audits. Also provided auditing and document control advice to our ISO14001 efforts. (Plant closed) Show less
-
-
-
Teledyne Technologies Incorporated
-
United States
-
Technology, Information and Media
-
700 & Above Employee
-
Plant Metallurgist - Heat Treat Supervisor
-
Apr 2000 - Nov 2000
• Total Management responsibility for all Heat Treating and Plating operations. This included: Plating, Carburizing and Hardening of Aircraft Engine Components such as: Camshafts, Rocker Arms, and Gears. Gas Nitriding of Crankshafts, Cylinder Barrels and Gears. Copper, Bronze, Tin and Zinc plating of various engine parts including all cleaning, shot peening and blasting. • Conducted all training of furnace operators and had extensive hands on knowledge of all furnace equipment and processes. In addition, provided Lab support and performed failure analysis using SEM and other equipment. • Developed and wrote all Special Process Operating Procedures and Work Instructions for the Heat Treat department and provided support to the Quality areas for FAA compliance efforts. Show less
-
-
-
-
Plant Metallurgist
-
Dec 1994 - May 2000
• As Plant Metallurgist I was solely responsible for supervising 9 Heat Treat Lab Technicians and over $8M in heat-treat assets. My department heat-treated 6 million bearing cups per month out of 5 Surface Combustion twin rotary carburizing/carbonitriding furnaces. Dana Pottstown carburized 0.5 million journal crosses (Universal Joints) per month out of 7 Surface Combustion Super All-Case batch furnaces. Dana Pottstown Induction hardens many types of Yokes and Shafts off of numerous single/dual spindle induction scanners. • Responsible for all of the above heat treating activities. Included in these responsibilities were short & long term planning for furnace capacity, process monitoring, cost reductions, material selection and Quality Improvements. I developed extensive data acquisition programs to assess the statistical capability of key furnace characteristics. I also developed databases to associate heat treat results with furnace conditions and cycle times. I was involved in all aspects of employee empowerment and appraisals. I have been trained and am experienced with developing procedures and conducting internal auditing structured around ISO/QS-9000 including developing Process Control Plans, FMEA's, PPAP's, APQP and SPC development. • As heat treat supervisor I had extensive hands on experience with batch / continuous furnaces, electronic flow meters, computer controlled furnace parameters, Endothermic (Rx) generators, nitrogen and ammonia systems. All experience is focused around a high volume manufacturing environment driven by customer satisfaction and a world class Quality Product. Show less
-
-
-
Oregon Steel Mills
-
Mining
-
1 - 100 Employee
-
Metallurgist
-
Nov 1993 - Dec 1994
OSM Fontana produced wide plate for the structural, pressure vessel and line pipe markets. The Fontana mill specialized in high strength, high toughness, and thermal mechanically controlled rolled plate for use in Oil & Gas line pipe applications. (Left due to Plant closure) While there I: • Established an in house physical test lab resulting in a savings of $60,000/month in shipping and testing costs previously provided by an outside Lab. This includes all equipment acquisition, staffing, training and qualification of personnel. • Managed all aspects of the physical test lab. Supervised "Sample Preparers (Machinists) and Mechanical Testers" in preparing steel samples and conducting various mechanical testing necessary to certify mechanical properties to industry/customer specific requirements. • Provided technical expertise and services required to design, produce and market plate steel products. Services involved interaction and consulting with sales, production planning, operations, Quality Assurance and Technical Services in various divisions of the corporation, customers and any third party inspectors. • Specified steel chemistry, reheat parameters, controlled rolling parameters and conducted hold and release activities for all plates produced. • Performed statistical analysis of process data and physical results to determine mill capability for various structural, pressure vessels and line pipe orders. • Contributed in the self-assessment, internal auditing and procedure writing, which resulted in ISO 9002 registration. Show less
-
-
-
-
Plant Metallurgist
-
Apr 1991 - Nov 1993
DTP was a processor of Oil Country Tubular Goods, predominately for US Steel. The facility performs all necessary end finishing (forging/upsetting), heat treating (Quench and Temper, and Normalizing), Non-destructive inspection, threading and testing of API grade Tubing (Seamless & ERW) and Coupling Stock. Metallurgical: Provided all Metallurgical guidance in terms of heat treatment design practices, process control limits, furnace modifications, forging practices and all technical and computer support. Supervised the Metallurgical test lab; responsible for all physical testing and qualifying of pipe processed at DTP. This included all sample procurement, identification and milling; tensile testing, hardness testing and chemical analysis as required to validate conformance to specifications. Developed material databases and performed monthly capability evaluations to ensure mill capability. Performed all required Metallography and technical report writing for any customer concerns. Quality/Administrative: Employee/management interfacing (scheduling, evaluations, review boards etc.) Developed, managed and directed DTP's Quality System Program to satisfy API Q1 and ISO 9002 requirements. Wrote all Quality Control Procedures, Standard Operating Procedures, developed and standardized all forms used throughout the plant. Performed all responsibilities of the Lead Auditor and conducted all internal auditing. Technical: Developed data base applications for HR, payroll and QC departments, which greatly improved efficiency, flexibility and labor requirements over previous systems. Provided computer support plant wide; including all hardware and software diagnosis and maintenance, saving DTP down time, allowing the cancellation of service contracts and voiding the vacant system administrator's position. Show less
-
-
-
Algoma Steel Inc.
-
Canada
-
Mining
-
500 - 600 Employee
-
Product Metallurgist
-
Feb 1989 - Apr 1991
Provided a technical interface between the customer/sales and the seamless tube mill. All inquiries for tubing / casing / drill pipe and line pipe were routed through Product Metallurgy to be addressed for technical concerns. Customer specifications were reviewed, mill capability was determined and any extra costs or mill limitations were identified. Developed an extensive customer database allowing cross-referencing of specification requirements to mill capabilities. (Union / strike related layoff of young Engineers) Show less
-
-
-
The University of British Columbia
-
Canada
-
Higher Education
-
700 & Above Employee
-
Research Engineer
-
Jan 1988 - Feb 1989
Independently researched fabrication techniques for making high-temperature superconducting ceramic wires, coils, tubes and coatings. Manufactured powders from raw materials extruded and sintered superconducting powders into wires and coils. This work involved much material characterization and scanning electron microscopy. This contract research resulted in technical advancements in a very new field of research that aided CTF (Canadian Thin Films / MEG) in developing future plans to manufacture magnetic imaging equipment and their proprietary superconducting quantum interference devices (SQUIDS). The outcome of this research was the publication of one tech paper and presentation at an international physics conference. Show less
-
-
Education
-
The University of British Columbia / UBC
Bachelor of Applied Science (BASc), Metallurgical Engineering -
University of Victoria
Physics and Astronomy
Community
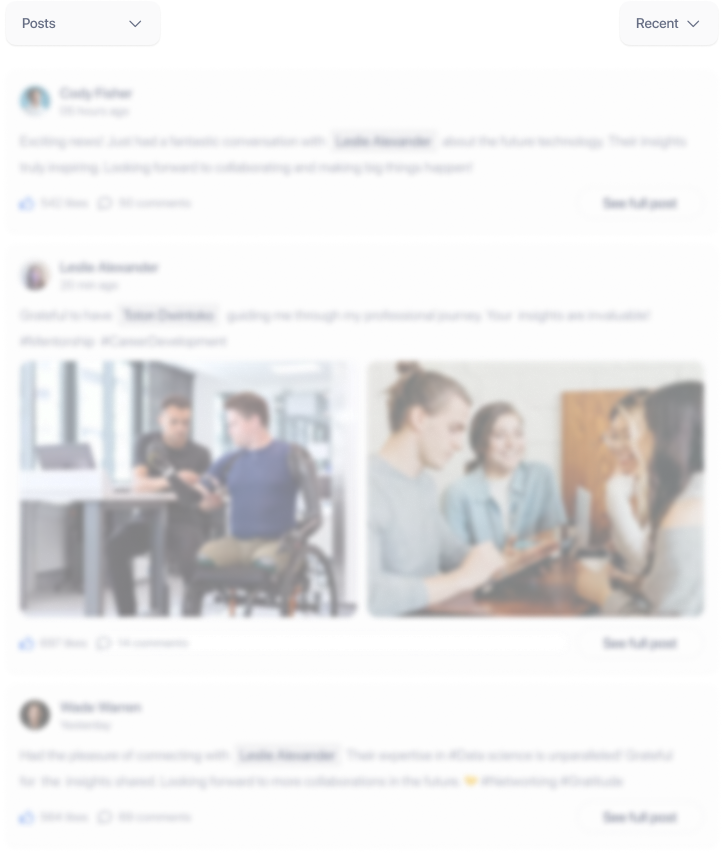