Mark Harper
Compliance Manager, Quality Assurance & Regulatory at Bridge to Life Ltd.- Claim this Profile
Click to upgrade to our gold package
for the full feature experience.
Topline Score
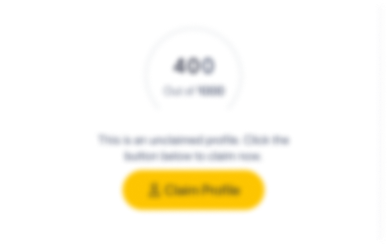
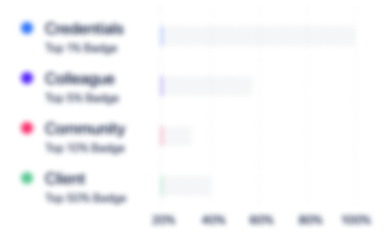
Bio


Experience
-
Bridge to Life Ltd.
-
United States
-
Biotechnology Research
-
1 - 100 Employee
-
Compliance Manager, Quality Assurance & Regulatory
-
Jun 2023 - Present
Illinois, United States
-
-
Director Quality Assurance Regulatory Affairs
-
Sep 2021 - Aug 2023
Wisconsin, United States
-
-
-
Spectrum Plastics Group, A DuPont Business
-
United States
-
Medical Equipment Manufacturing
-
300 - 400 Employee
-
Director Quality Systems
-
Aug 2021 - Sep 2021
-
-
Director Global Quality
-
Oct 2018 - Aug 2021
Sandy, Utah, United States
-
-
-
-
Director of Quality Assurance and Regulatory Affairs
-
Jul 2016 - Oct 2018
Kenosha WI •Directs the Quality Assurance and Regulatory Affairs processes as they relate to FDA regulations and ISO 13485 requirements, initiates and implements regulatory and quality improvement activities as appropriate, and raise the quality performance of the product lines. •Serves as the quality management representative •Educates and trains employees as to their impact in the Quality Management System •Ensure regulatory compliance and oversee the management of QC inspection, customer… Show more •Directs the Quality Assurance and Regulatory Affairs processes as they relate to FDA regulations and ISO 13485 requirements, initiates and implements regulatory and quality improvement activities as appropriate, and raise the quality performance of the product lines. •Serves as the quality management representative •Educates and trains employees as to their impact in the Quality Management System •Ensure regulatory compliance and oversee the management of QC inspection, customer complaint, CAPA and RMA processes •Manage 30+ quality, regulatory personnel •Supports concurrent engineering efforts by participating in design development projects representing regulatory, quality assurance, and the customer •Oversees development of procedures for process control, process improvement, testing and inspection •Establishes and implements metrics (process capability, control charts, measurement quality) for monitoring system effectiveness and to enable managers to make appropriate product quality decisions •Performs root-cause analysis and other problem solving activities to identify effective corrective actions and process improvements •Establishes collection and analysis systems of statistical data to predict trends that will affect improvement of product quality •Analyzes customers’ product specifications to establish efficient, cost-effective requirements for ease of manufacturing and reproducibility •Monitors vendor performance and the establishment of criteria and rating system for critical vendors •Oversees calibration and testing programs •Reports to management on quality issues, trends and losses •Establishes supplier quality requirements •Participates in internal and external quality audits •Interfaces with supplier and customer quality representatives concerning problems with quality, and assures that effective corrective action is implemented Show less
-
-
-
-
Senior Regulatory Affairs Manager
-
May 2016 - Jul 2016
Kenosha FDA Response and Remediation: Analyze observations, lead internal investigations to assess all affected processes, identify root causes of noncompliance, draft a comprehensive Corrective and Preventative Action (CAPA) plan, lead implementation and evaluate effectiveness, monitor, revise plan as needed and periodically submit objective evidence to FDA of effectiveness. • Prepare and provide oversight for submission dossier creation with respect to new products, renewals, product… Show more FDA Response and Remediation: Analyze observations, lead internal investigations to assess all affected processes, identify root causes of noncompliance, draft a comprehensive Corrective and Preventative Action (CAPA) plan, lead implementation and evaluate effectiveness, monitor, revise plan as needed and periodically submit objective evidence to FDA of effectiveness. • Prepare and provide oversight for submission dossier creation with respect to new products, renewals, product changes, advertising, and other licensing. • Interpret country regulations and provide regulatory insight plus guidance to support organizational objectives, to reduce risk and to drive regulatory compliance. • Develop and implement streamlined consistent processes for both new products and life cycle management. • Provides regulatory leadership to develop and sustain productive relationships with in-country business partners. • Monitor the external regulatory environmental changes and engage in shaping activities through industry association. • Maintain a positive relationship with health authorities through frequent and transparent dialogue. • Lead RA team and strengthen talent development for RA staff. Show less
-
-
-
GE HealthCare
-
United States
-
Hospitals and Health Care
-
700 & Above Employee
-
Senior Auditor (QMS)
-
Nov 2014 - Jan 2016
Waukesha WI As a member of GE Healthcare’s (GEHC’s) Global Quality Compliance (GQC) audit staff, I work with a global team to deliver GEHC’s Quality, Regulatory, Medical (QRM) audit program for Pharma, Medical Device, Clinical Research and Business Development interests. We plan, execute, report out and follow-up on comprehensive audits and reviews of compliance to GEHC procedures and country specific regulations and International standards to business and functional leadership. Key… Show more As a member of GE Healthcare’s (GEHC’s) Global Quality Compliance (GQC) audit staff, I work with a global team to deliver GEHC’s Quality, Regulatory, Medical (QRM) audit program for Pharma, Medical Device, Clinical Research and Business Development interests. We plan, execute, report out and follow-up on comprehensive audits and reviews of compliance to GEHC procedures and country specific regulations and International standards to business and functional leadership. Key responsibilities include: • Conduct reviews, perform audits and document findings for complex and unusual businesses • Provide follow up activities to ensure compliance with regulations and conformance with written and approved procedures • Provide direction on root cause, proactively assess risk, plan and execute audit deliverable's • Communicate audit results and recommendations • Provide leadership in driving improvement efforts • Interface with senior mgmt & external regulatory agencies during inspections, audits, investigations & report outs • Lead QRM personnel to identify compliance risk, develop action plans, report progress, and ensure closure • Provide specialist support during external audits or inspections and/or conduct technical/ombuds investigations in response to compliance concerns within QARA • Provide support to improvement or remediation QRM projects • Provide Subject Matter Expertise of quality systems, including 21CFR820, 803, 806, 210, 211, 50, 54 & 56, ISO 9001, ISO 13485 MDD, ANVISA, MHLW, CFDA
-
-
Global Quality Assurance Director - QMS
-
Apr 2012 - Jan 2015
Waukesha, WI •Responsible for the Global General Electric Healthcare Quality Management System (QMS) including Training, Translations, Document Control, Quality Data Review and Analytics across a combination of 80+ global GE Healthcare Design and manufacture locations. •Manage Global QMS change control, periodic reviews and deployment for QMS procedures, work instructions and training including master document source management. •Responsibilities include but not limited to the following: Initiating… Show more •Responsible for the Global General Electric Healthcare Quality Management System (QMS) including Training, Translations, Document Control, Quality Data Review and Analytics across a combination of 80+ global GE Healthcare Design and manufacture locations. •Manage Global QMS change control, periodic reviews and deployment for QMS procedures, work instructions and training including master document source management. •Responsibilities include but not limited to the following: Initiating and communicating document change control requests to executive leadership via DCAB management; Cross functional and multi-modality global document devlpmnt, iterative review, presentation to executive for approvals; Managing devlpmnt/revisions activities for training content and exams; Country specific translations; QMS Deplymnt and site implmnt, with effectivness evaluations. •Mnthly status: Global QMS deployment plan QMS document – Works in Progress; Risks to implementation; QMS wins and Actions; QMS change management metrics – Document throughput – English & translations; material Shipped Complete on Time (SCOT); Wing to Wing cycle times & Implementation (P50 & P95); Training status for QMS documents as well as Stand Alone Training for site’s needs; Global QMS training completion metrics. •Maintain QMS history of life cycle change based on requirements flow down from applicable business standards, regulations, and directives. •Conducts analysis of global metric data to provide comparison of prior periods, share insight/recommendations to strategic initiatives for imprvmnt. •Leads the Global QMS function by directly managing QMS team employees as well as indirectly managing virtual contributors ensuring compliant outcomes while coaching, teaching, and developing QA professionals at all levels. •Employees Performance Management experience (i.e. managing direct/indirect reports), including hiring, training, coaching and performance management activities for 8 full time reports.
-
-
QARA Sr. Site Leader
-
Jan 2009 - Apr 2012
Research Park Wauwatosa WI * Directing the site Quality Management System and 10 Direct reports, fully integrated with the GE Global QMS, including cross-functional and site specific processes, Management Representative for Quality at the site * Responsible for facility compliance covering voluntary, regulatory and company quality requirements and champion quality initiatives at all levels of the organization. * Oversee all quality related communications and training requirements for all site employees * Ensure… Show more * Directing the site Quality Management System and 10 Direct reports, fully integrated with the GE Global QMS, including cross-functional and site specific processes, Management Representative for Quality at the site * Responsible for facility compliance covering voluntary, regulatory and company quality requirements and champion quality initiatives at all levels of the organization. * Oversee all quality related communications and training requirements for all site employees * Ensure site audit readiness and host Quality system audits and inspections. * Oversee the Corrective action / Preventive action activities, complaint handling and Quality engineering while maintaining and improving all aspects of site quality planning * Reporting Quality system effectiveness and requirements to Management team, including preparing and executing facility Quality Management reviews * Drive the definitions of site quality objectives, metrics, reporting and operating mechanisms. * Participate in global initiatives to share best practices and leverage quality synergies. * Support local R&D programs and quality issue resolution.
-
-
Global Quality Systems Programs Manager
-
May 2005 - Jan 2009
Wauwatosa WI QMS Leadership role driving high quality expectations in a global environment, while accomplishing improvements to Quality Systems in Americas, Europe and Asia. Accomplished global FDA inspection leader and Subject Matter Expert. Unifying a World Class QMS with best practices. Proven history of global auditing QMS, special process and medical device products. Evaluating and communicating significant compliance risk to high-level business management. Analyzing technical documents,… Show more QMS Leadership role driving high quality expectations in a global environment, while accomplishing improvements to Quality Systems in Americas, Europe and Asia. Accomplished global FDA inspection leader and Subject Matter Expert. Unifying a World Class QMS with best practices. Proven history of global auditing QMS, special process and medical device products. Evaluating and communicating significant compliance risk to high-level business management. Analyzing technical documents, literature, protocols and design specifications for Class II & III medical devices. Responsible for assessing and development of quality system design and/or execution of compliance for specific sites covering voluntary, regulatory, company quality requirements. Design and execute communication and training related to quality system content and execution to site personnel. Developing and managing quality expectations for quality, engineering, manufacturing teams
-
-
-
Pemstar
-
Appliances, Electrical, and Electronics Manufacturing
-
1 - 100 Employee
-
FDA Compliance Manager
-
2002 - 2004
Rochester MN · Directed and Coordinated the Quality activities of Drug Coated Stent program to ensure compliance to Company QMS & FDA Regulatory Requirements were accomplished. · Responsible Medical Management representative for company related FDA compliance program. · Responsibility for Planning, Directing and Coordinating Quality activities as required for designated medical programs. · Lead developing and improving all quality and FDA compliance aspects of medical programs · Directly… Show more · Directed and Coordinated the Quality activities of Drug Coated Stent program to ensure compliance to Company QMS & FDA Regulatory Requirements were accomplished. · Responsible Medical Management representative for company related FDA compliance program. · Responsibility for Planning, Directing and Coordinating Quality activities as required for designated medical programs. · Lead developing and improving all quality and FDA compliance aspects of medical programs · Directly supervise 22 full time employees · Certified Quality Auditor
-
-
Program Manager
-
2003 - 2003
Rochester MN · Plan; direct and coordinate the business activities of Drug Coated Stent program to ensure goals and objectives are accomplished within prescribed time frame & funding parameters. · Review status reports prepared by program personnel and modified schedules or plans as required. · Establish Work plan and staffing for each phase of the program and arranged for recruitment or assignment of program personnel.
-
-
-
Natural Biologics, Inc.
-
United States
-
Biotechnology Research
-
1 - 100 Employee
-
Quality Assurance Manager
-
1997 - 2002
Albert Lea MN · Responsible management representative for company related FDA compliance program, 21 CFR parts 210 & 211. · Responsible for providing primary leadership in designing, leading, and directing all functions and aspects of the Quality Assurance Program. · Interpretation of quality philosophy to all personnel through training and Quality support. · Founded Internal and External audit program based upon 21 CFR requirements. · Directly supervise six full time employees. · Participate… Show more · Responsible management representative for company related FDA compliance program, 21 CFR parts 210 & 211. · Responsible for providing primary leadership in designing, leading, and directing all functions and aspects of the Quality Assurance Program. · Interpretation of quality philosophy to all personnel through training and Quality support. · Founded Internal and External audit program based upon 21 CFR requirements. · Directly supervise six full time employees. · Participate and maintain communication with the local FDA office, Annual amendments of regulatory submissions, new regulatory submissions, escort, and respond to external auditors.
-
-
Quality Control Manager
-
1996 - 1997
Austin MN · Responsible party for company related FDA compliance program · Project manager and lead auditor, direct supervision of seven 7 fulltime and 5 seasonal employees. · Managed procurement, validation, manufacturing, maintenance, and quality activities. · Designed Quality system upon 21 CFR, parts 210, 211 and ICH. · Development and execution of IOQ, process, and cleaning validation protocols. · Development of equipment and system SOPs for manufacturing and in-process sampling.
-
-
-
-
Quality Control Manager
-
1991 - 1996
Richmond, Virginia Area · Management responsibilities included but not limited to; responsibility for lab staff of 3, lab GC and other analytical equipment, yearly budget preparation, daily assignments and functions. · Provided QC support for manufacturing and the R&D lab. · Project lead for Pilot scale research and development projects for customers such as E.I. DuPont, PPG, Xerox, AT&T, Avon Rubber, Occidental chemical. · Provided customers on site technical service for production line problems.
-
-
Education
-
Cardinal Stritch University
MIS, Management Information Systems -
Virginia Commonwealth University
Business Administration
Community
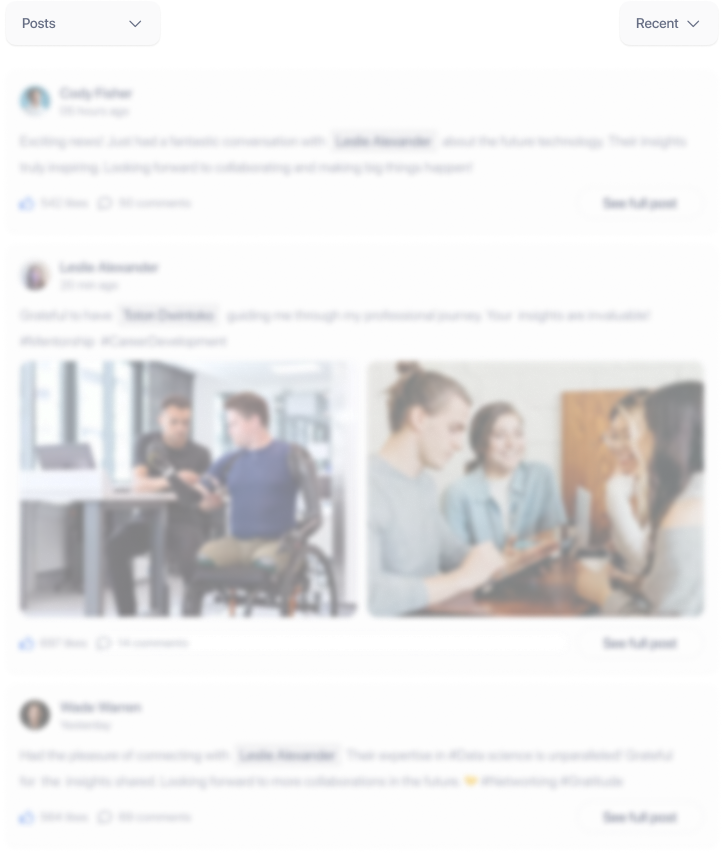