Mark Farrell
Vice President Operations, Waste Treatment at Wind River Environmental- Claim this Profile
Click to upgrade to our gold package
for the full feature experience.
Topline Score
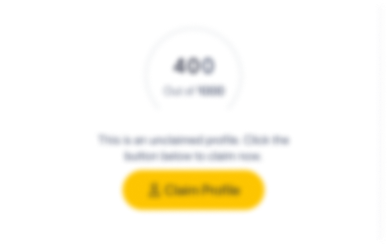
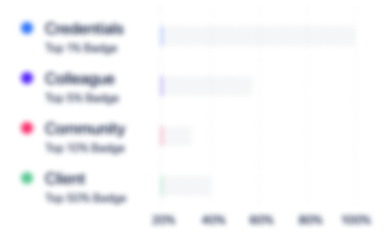
Bio

David Featherstonhaugh P.Eng.
I had the pleasure of working with Mark at Hydroxyl Systems. I can still remember the first words he said when he was approached by a colleague: "Hi, how can I help you?". And he truly meant it. Mark was always driven to make things better for clients, his colleagues, and from an engineering standpoint - designs/serviceability/reliability. He led by example. Those traits have carried forward throughout his career. He has a rare combination of technical, business and people skills that will benefit any organization.

Mark Forbes
I have no hesitation in recommending Mark. He is a highly skilled engineer and a brilliant manager of engineering teams. I worked closely with Mark for more than 10 years and found his honesty, integrity and trustworthiness be to unquestionable. He kept his staff highly motivated and delivered beyond expectation. Mark and I took on the largest project the company had ever undertaken, with Mark managing the delivery phase. It was delivered early, under budget and beyond the quality expectations of the client. This was the normal level of performance I came to expect of Mark and the team he managed in many subsequent projects. Mark Forbes

David Featherstonhaugh P.Eng.
I had the pleasure of working with Mark at Hydroxyl Systems. I can still remember the first words he said when he was approached by a colleague: "Hi, how can I help you?". And he truly meant it. Mark was always driven to make things better for clients, his colleagues, and from an engineering standpoint - designs/serviceability/reliability. He led by example. Those traits have carried forward throughout his career. He has a rare combination of technical, business and people skills that will benefit any organization.

Mark Forbes
I have no hesitation in recommending Mark. He is a highly skilled engineer and a brilliant manager of engineering teams. I worked closely with Mark for more than 10 years and found his honesty, integrity and trustworthiness be to unquestionable. He kept his staff highly motivated and delivered beyond expectation. Mark and I took on the largest project the company had ever undertaken, with Mark managing the delivery phase. It was delivered early, under budget and beyond the quality expectations of the client. This was the normal level of performance I came to expect of Mark and the team he managed in many subsequent projects. Mark Forbes

David Featherstonhaugh P.Eng.
I had the pleasure of working with Mark at Hydroxyl Systems. I can still remember the first words he said when he was approached by a colleague: "Hi, how can I help you?". And he truly meant it. Mark was always driven to make things better for clients, his colleagues, and from an engineering standpoint - designs/serviceability/reliability. He led by example. Those traits have carried forward throughout his career. He has a rare combination of technical, business and people skills that will benefit any organization.

Mark Forbes
I have no hesitation in recommending Mark. He is a highly skilled engineer and a brilliant manager of engineering teams. I worked closely with Mark for more than 10 years and found his honesty, integrity and trustworthiness be to unquestionable. He kept his staff highly motivated and delivered beyond expectation. Mark and I took on the largest project the company had ever undertaken, with Mark managing the delivery phase. It was delivered early, under budget and beyond the quality expectations of the client. This was the normal level of performance I came to expect of Mark and the team he managed in many subsequent projects. Mark Forbes

David Featherstonhaugh P.Eng.
I had the pleasure of working with Mark at Hydroxyl Systems. I can still remember the first words he said when he was approached by a colleague: "Hi, how can I help you?". And he truly meant it. Mark was always driven to make things better for clients, his colleagues, and from an engineering standpoint - designs/serviceability/reliability. He led by example. Those traits have carried forward throughout his career. He has a rare combination of technical, business and people skills that will benefit any organization.

Mark Forbes
I have no hesitation in recommending Mark. He is a highly skilled engineer and a brilliant manager of engineering teams. I worked closely with Mark for more than 10 years and found his honesty, integrity and trustworthiness be to unquestionable. He kept his staff highly motivated and delivered beyond expectation. Mark and I took on the largest project the company had ever undertaken, with Mark managing the delivery phase. It was delivered early, under budget and beyond the quality expectations of the client. This was the normal level of performance I came to expect of Mark and the team he managed in many subsequent projects. Mark Forbes

Credentials
-
Lean Six Sigma Black Belt
Six Sigma Global InstituteJan, 2018- Oct, 2024 -
Lean Six Sigma Yellow Belt
GoLeanSixSigma.comDec, 2017- Oct, 2024 -
Managing Safety Performance
Balmert ConsultingJan, 2016- Oct, 2024
Experience
-
Wind River Environmental
-
United States
-
Environmental Services
-
100 - 200 Employee
-
Vice President Operations, Waste Treatment
-
Jan 2018 - Present
-
-
-
Koch Membrane Systems
-
United States
-
Industrial Machinery Manufacturing
-
1 - 100 Employee
-
Chief Operating Officer / COO
-
Dec 2015 - Oct 2017
A subsidiary of privately owned Koch Industries providing Equipment, Systems and Services. Serving the global Food, Dairy, Beverage, Pharmaceutical, General Industrial, Automotive, Municipal & Industrial, Water & Wastewater Markets. • Lowered working capital; reduced operating expenses and cost of sales by >$12MM, increased gross profit. • P&L and global Sales & Marketing responsibility for >$40 MM Water & Wastewater business.• Established Manufacturing capabilities in North & South America, Europe, India, China, & Australia.• Additional operations managed that contributed to the favorable variances and increased profits; Project Management, Mechanical Design, Electrical Engineering, Procurement, Logistics, Warehousing, EH&S, Quoting and Estimating, Accounting, Information Technology, and Total Quality Management (TQM). Show less
-
-
Chairman & Managing Director Koch Membrane Systems GmbH - Board of Directors
-
Jan 2007 - Sep 2017
Koch International division. This division included the European, Process Engineering, Project Management, Field Services and two manufacturing facilities, membrane production and yarn braiding.
-
-
Vice President of Global Membrane Manufacturing & Systems Engineering
-
2012 - 2015
• Conceived and completed a number of multi-million-dollar CapEex investments globally, including the installation of additional capacity to support sales growth. Projects completed on time, on budget, improving quality, lowering Cost of Goods Sold (COGS) and supporting additional sales growth. CapEx investments combined totaled > $50MM.• Established a 120,000-sq. ft. assembly facility in a low cost global center. From green-field site selection, building design and layout, to full commission of the factory. Factory was built and in full production in seven months, 2 months ahead of schedule. Achieved >20% cost savings, improved efficiencies, and reduced scrap rates. • Developed and Managed Annual Engineering, Operations and Manufacturing department budgets totaling over $60MM. • Achieved annual budget reductions and favorable variances every year. • Optimized and expanded factories in USA, Germany, China and the Netherlands.• Consolidated one European factory from rented location in Europe into an owned facility the USA.• Led value engineering process for systems, equipment and products. Resulting in lower cost to fabricate, higher quality, quicker to install and commission, more compact, easier to service and operate systems, equipment and products. Reduced system, equipment and product costs by between 15% to 40%.• Rebuilt the company’s EH&S culture, resulting in 67% reduction in the Total Injury Rate (TIR) rate.• Operations included thousands of unique high-tech individual products, five different product families, and five different manufacturing facilities around the world. Show less
-
-
Director Systems Engineering
-
2000 - 2012
• Transitioned Systems fabrication from in-house fabrication to a 100% globally outsourced model, by establishing a network of System sub-contract fabricators worldwide. Providing Koch with the capability to be more competitive by building Systems at “local to the market” sub-contract partners, while maintaining consistency and required quality standards.• Implemented major improvements within global mechanical / electrical engineering, design, quoting and estimating, project management, contracts management, systems fabrication, delivery, installation, startup, and after sales technical services, while supporting a 600% growth in Systems Equipment Business at an increased gross margin. • Achieved total annual average, actual vs. estimate costs for all systems projects within +/-3% for 10 years in a row. • Increased direct absorption of Engineering Department hours to >85%. Show less
-
-
-
Hydroxyl Systems Inc.
-
Environmental Services
-
1 - 100 Employee
-
Engineering Services & Operations Manager
-
1997 - 2000
Established and directed all electrical engineering and in-house equipment fabrication. Secured, qualified, and managed all sub-contractor suppliers and fabricators. Developed the installation and commissioning, field services, remote monitoring, and after-sales residual revenue service business. Assumed responsibility, as lead Controls Engineer, for developing all PLC, HMI, and SCADA code. • Rapidly created and led complete Engineering, Fabrication, and Service teams to support and enable the company’s swift growth. Enabled the company to win and successfully deliver solutions for very high-profile customers, on some extremely environmentally sensitive and technically challenging sites. • Participated in all research and product development efforts. Ensured all available engineering experience in the application and operation of the advanced technologies and processes were considered for lessons learned and best practice; accelerated R&D and shortened scale-up and commercialization. • Ensured projects shipped on time and that customer technical support calls or complicated customer issues were resolved in a timely manner. Motivated working manager, who enjoyed applying his engineering skills and leading by example. Show less
-
-
-
Master Pave
-
United States
-
Construction
-
Construction Manager
-
1993 - 1997
-
-
-
Grinaker-LTA
-
South Africa
-
Construction
-
100 - 200 Employee
-
Site Engineer / (Intern then full time)
-
1988 - 1993
-
-
Education
-
Port Elizabeth Technikon
NHD, Civil Engineering -
Port Elizabeth Technikon
ND, Civil Engineering
Community
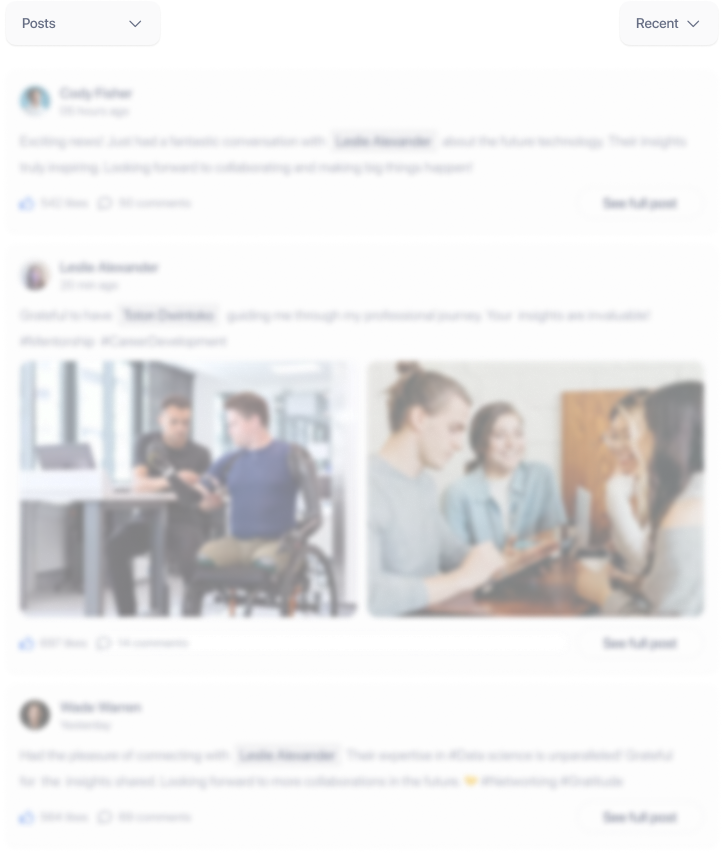