Mark Endo
Site Quality Manager at Pharmachem Laboratories, Inc.- Claim this Profile
Click to upgrade to our gold package
for the full feature experience.
Topline Score
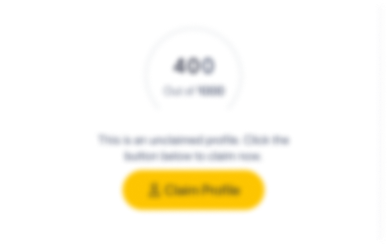
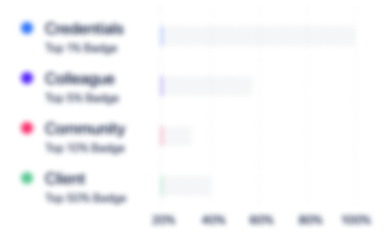
Bio


Experience
-
Pharmachem Laboratories, Inc.
-
United States
-
Health, Wellness & Fitness
-
1 - 100 Employee
-
Site Quality Manager
-
Jun 2021 - Present
-
-
-
-
Director Of QA
-
Nov 2019 - Jun 2021
-
-
-
Global Health Industries
-
United States
-
Wellness and Fitness Services
-
1 - 100 Employee
-
Assistant Quality Manager
-
Mar 2016 - Nov 2019
-
-
-
Catheter Connections, Inc.
-
United States
-
Medical Equipment Manufacturing
-
1 - 100 Employee
-
Director of Quality Assurance
-
Apr 2014 - Jan 2016
Manage and maintain QMS ensuring compliance to FDA 21 CFR 820 regulations. Performed annual management review meetings. Manage and supervise document control system. Perform training for document updates within the Quality Management system Perform internal / supplier audits ensuring compliance to internal procedures and 21 CFR 820. Review and approve inspection reports on incoming materials and final assemblies. Implementation of new materials into current medical device. Manage CAPA, SCAR, NCMR and Customer Feedback processes. Manage FMEA for user, process and product design. Write justifications / rationale for NCMR’s, CAPA’s, Customer Complaints. Manage routine LAL and VDmax Dose Audits for product lines. Review and approve production work orders, document change orders, NCMR’s Assist with 510(k) submission for changes in indications for use. Write letter to file for product changes in design and material. Obtain Certificates to Foreign Government and authentications from US Department of State to get product into foreign markets. Worked directly with Australian TGA to get product into Australia. Worked with Regulatory Affairs to change CE mark for changing component materials and indications for use, Worked with marketing to create product label, IFU’s and packaging. Show less
-
-
-
SINTX Technologies
-
United States
-
Biotechnology Research
-
1 - 100 Employee
-
Quality Assurance Manager
-
Jun 2005 - Apr 2014
Highly involved with cross functional team (PD, R&D, Mktg, Mfg, RA) to successfully bring a new material from idea to implantable medical device. Implemented and managed the company document control system (PDM). Managed and performed internal, DHF, and supplier audits ensuring compliance to FDA 21 CFR 820 and ISO 13485 regulations as well as to internal procedures. Directly involved in FDA and BSI Notified Body audits Directed and managed CAPA and Customer Feedback Processes. Wrote justifications for NCMR’s, CAPA’s, Customer Feedbacks, etc. Perform Design, Process and User FMEA . Directed biocompatibility testing for new material for spinal implants. Directed cleaning and steam sterilization validations for surgical instrument systems. Directed gamma sterilization validations and dose audits, cleaning and packaging validations for sterile implants. Reviewed and approved equipment qualifications, production work orders, document change orders, NCMR’s. Participated in annual Management Review Meetings. Worked with Regulatory Affairs in compiling Technical File for CE. Worked with vendor to implement software for Quality Management System. Show less
-
-
-
ICU Medical
-
United States
-
Medical Equipment Manufacturing
-
700 & Above Employee
-
Validation Microbiologist
-
Apr 2003 - Jun 2005
Responsible for validation of laboratory equipment (FT-IR, Melt Flow Indexer, GC, Biolog, refrigerators, incubators) ensuring 21CFR Part 11 Compliance, all used to support final release of materials and final product. Managed microchallenges for annual qualifications, validation of a process challenge and master device, and validation of a low gas weight cycle for EtO sterilization, and for the steam sterilizer. Managed production of material used to validate EtO sterilization cycles. Managed radiation sterilization quarterly dose audits. Also involved with dose setting of new product. Maintaining compliance with ANSI/AAMI/ISO guidelines. Actively involved in formal investigations for EtO residual failures, sterilization cycle excursions, and particulate contamination, and determining corrective and preventive actions. Actively involved in recommending and implementing improvements, and developing cost reductions for the laboratory and facility. Involved in risk analysis for sterilization processes, laboratory equipment and procedures. Provide capital request justifications for the purchase of laboratory equipment. Involved in corporate, internal, and FDA audits. Other duties include laboratory testing (FT-IR, GC, sterility, pyrogen) on incoming materials used to manufacture medical devices and on final product for customer release. Other responsibilities include writing NCMR's, justifications, preparation of laboratory reports, revising and implementing plant BOP’s, problem solving, and employee training. Show less
-
-
-
-
Research Assistant II
-
Aug 2000 - Jan 2003
Worked under the direction of senior scientists in assay and method development for the Somata high throughput screening system. Managed the operation and maintenance of automated laboratory instruments including the MultiMek , TANGO, & Matrix 96/384 tip automated pipettors, Molecular Devices & Acquest Plate Reader, Festo robotic arm, and CCD fluorescence camera used in the Somata high throughput screening of protein and chemical libraries. Worked with engineers in solving problems associated with the automated laboratory equipment and instrumentation. Communicate with suppliers in the development of product to be used in assay and method development. Other duties also include performing molecular biological tests such as PCR, DNA preparation and quantitation, gel electrophoresis, DNA transfections, transductions, fluorescence and absorbance assays Responsible for performing data analysis and generating reports for presentation to other business units for project coordination. Also responsible for developing SOP's used for employee training. Show less
-
-
-
Abbott
-
United States
-
Hospitals and Health Care
-
700 & Above Employee
-
Biological Quality Assurance
-
May 1998 - Aug 2000
Managed the qualification of laboratory refrigerators and incubators used to store materials and reagents used for product release testing. Managed microchallenges for annual qualification of EtO sterilization cycles. Managed quarterly AAMI dose audits on product for radiation sterilization. Managed the environmental monitoring program for class 100,000 manufacturing clean rooms. Conducted study for replacement and implementation of a new process challenge device to be used for product release. Coordinate, implement, and execute testing procedures such as pyrogen, APTT, particulate, sterility testing, inhibition testing, environmental monitoring, bioburden, maintaining ATCC stock cultures, and media preparation) in accordance with established BOP’s, Performed laboratory investigations, deviations, preparation of laboratory reports, revised and implemented plant BOP’s, problem solving, and employee training. Show less
-
-
-
-
Laboratory Technician
-
Aug 1997 - May 1998
Performed DNA/RFLP analysis on transgenic plants and animals, which included hybridizing radioactive P32 to DNA probes, performing PCR, and operating the 377 DNA sequencer. Managed projects from creation to final product by marketing the RFLP test procedure to potential customers. Coordinated projects between business units to ensure timely completion and delivery of test results. Communicated with existing customers on project status. Implemented and revised standard operating procedures and actively involved in employee training. Prepared and loaded agarose gels, performed southern transfers, data entry, and reagent preparation. Worked with and disposed of hazardous materials. Show less
-
-
Education
-
Weber State University
Bachelor of Science (B.S.), Microbiology, General
Community
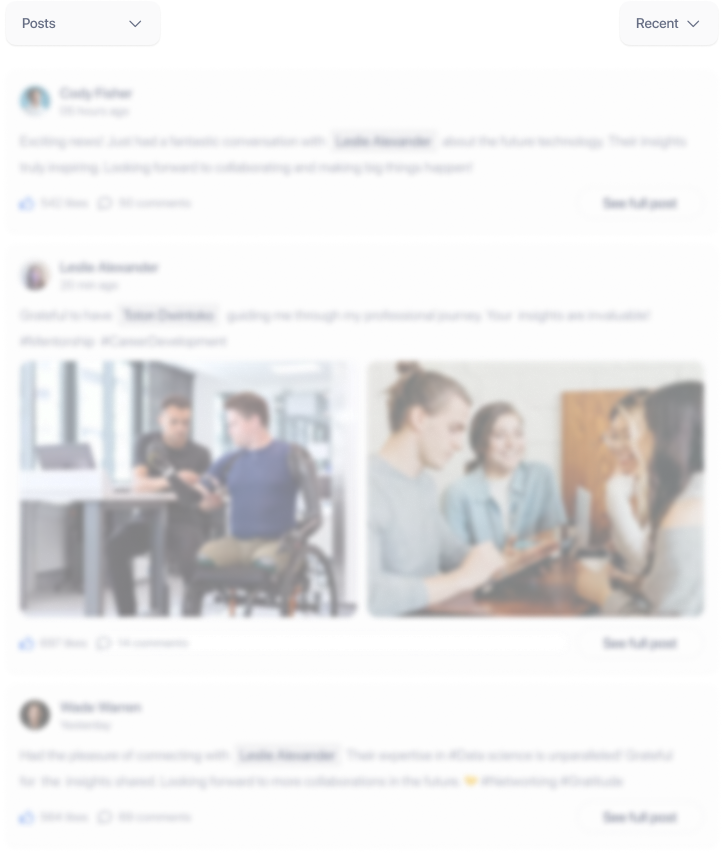