Mark Blatz
General Manager at CleanCare Linen- Claim this Profile
Click to upgrade to our gold package
for the full feature experience.
Topline Score
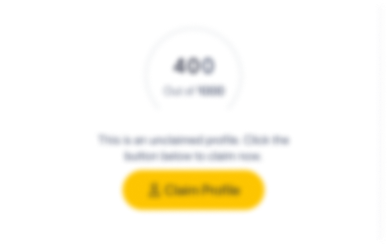
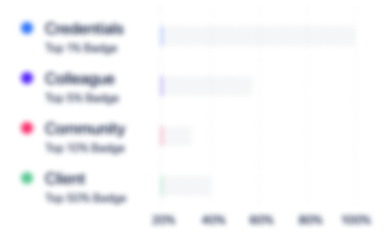
Bio


Experience
-
CleanCare Linen
-
United States
-
Hospitals and Health Care
-
1 - 100 Employee
-
General Manager
-
Mar 2021 - Present
Recruited to improve facility performance on key metrics, establish production process, develop corrective and predictive maintenance process, and provide accountability to the hourly and supervisory staff including; coaching, discipline, and performance development. Manage daily operations to achieve production throughput, safety performance, and customer service requirements while achieving budgetary commitments. Recruited to improve facility performance on key metrics, establish production process, develop corrective and predictive maintenance process, and provide accountability to the hourly and supervisory staff including; coaching, discipline, and performance development. Manage daily operations to achieve production throughput, safety performance, and customer service requirements while achieving budgetary commitments.
-
-
-
Airgas
-
United States
-
Chemical Manufacturing
-
700 & Above Employee
-
Plant Manager
-
Mar 2020 - Mar 2021
Recruited to facilitate the relocation of the distribution, warehouse, and production teams while maintaining productivity and service standards. Developing SOP's, facility security plans, safety programs, and communication tools for new facility. Implemented truck reconciliation process to provide an accurate representation of inventory for the retail team.Executed the relocation of the production and distribution functions to the newly built facility while absorbing 2 additional delivery areas and CDL drivers. Maintained customer service during furlough periods with 40% less staffing vs sales volume that was only down 9%
-
-
-
TruFoodMfg
-
United States
-
Food and Beverage Manufacturing
-
100 - 200 Employee
-
Plant Manager
-
Jan 2019 - Mar 2020
Recruited to improve facility performance on key metrics, establish production process, develop and implement 5S standards, develop corrective and predictive maintenance process, and provide accountability to the hourly and supervisory staff including; coaching, discipline, and performance development. Manage a roster of 270 plus employees. Manage daily operations to achieve OEE metrics, safety performance, schedule adherence, and customer service requirements while achieving budgetary commitments. Realized 5% or greater OEE improvement on 2 lines and 15% improvement on 1 lineRevitalized Redzone tool to improve communication and accuracy at all levels of the organizationEstablished daily production meetings to ensure all team members understand business metrics and performanceImplemented CMMS program to include PM process, parts tracking, inventory reconciliation, and maintenance utilization
-
-
-
-
Business Unit Manager
-
Jan 2018 - Jan 2019
Promoted to improve facility performance on key metrics and provide accountability to the hourly and supervisory staff including; coaching, discipline, and performance development. Manage a roster of 180 plus union employees, 1 warehouse manager, and 10 supervisory employees, including maintenance. Manage daily operations to achieve labeling requirements, safety performance, schedule adherence, customer service requirements, corrective maintenance, and preventative maintenance. Support production team through efficient direct labeling and Brite stacking process. Provide support for 22M cases of labeling to meet annual demandManage cost performance for $14M P&LLead cross functional team to achieve key KPI’s including OEE, Attainment, and customer fill rate
-
-
-
-
Operations Manager - Labeling and Distribution
-
Apr 2015 - Jan 2018
Recruited to improve facility performance on key metrics and provide accountability to the hourly and supervisory staff including; coaching, discipline, and performance development. Manage a roster of 170 plus union employees, 1 warehouse manager, and 9 supervisory employees. Manage daily operations to achieve labeling requirements, meet demand, and provide a high level of customer service. Provide support for 22M cases of labeling to meet annual demandEstablished daily/weekly/monthly down time tracking and analysis for all indirect and direct labeling linesLead daily respond and recover meeting as a collaborative effort with maintenance team to drive plant efficiency by reviewing down time, understanding root cause, and assigning ownership to resolve issuesImplemented daily/weekly inventory reconciliation process to reduce loss by more than $1M annuallyImproved 10.5oz labeling attainment by 17% through collaborative effort with frontline team, maintenance team, and supervisory teamAchieved line efficiency improvements 3 consecutive years
-
-
-
The Coca-Cola Company
-
United States
-
Food and Beverage Services
-
700 & Above Employee
-
Distribution Manager
-
Jan 2015 - Apr 2015
Manage daily activities of directing, controlling, and coordinating all phases of the distribution operation while maintaining delivery standards, efficiencies, and adhering to all regulatory requirements. Direct a staff of 6 supervisors and approximately 60 CDL drivers to maintain a high level of customer service to more than 6 thousand local customers and act as a liaison between the distribution center and sales management team. Realized 2% performance increase for department backhauls in a 3 month timeframe by implementing daily route review, supervisor route rides, and daily feedback process Improved DOT audit compliance from an internal rating of 46% to 87% by refocusing the leadership and frontline teamWorked with Here team to develop a strategy to increase staffing levels of CDL drivers through aggressive marketing plan
-
-
Warehouse Manager
-
Apr 2014 - Jan 2015
Manage a staff of more than 40 hourly union employees and 7 supervisors/clerks to maintain P&L, inventory, and productivity goals in a facility with more than 10M cases of local sales annually. Maintain high standards in safety, facility cleanliness, quality, and comply with regulatory guidelines. Provide a high level of customer service to internal and external customers by executing timely loading schedules. Successfully implemented ELS and facility optimization project to increase picking productivity by more than 10%.Optimized supervisor scheduling to provide 24 hour facility coverage and additional support/accountability to the frontline staff Improved inventory reconciliation process by eliminating daily cycle count process, implementing full daily warehouse counts, and requiring double blind counts for month end close
-
-
-
Bay Valley Foods
-
United States
-
Food and Beverage Manufacturing
-
400 - 500 Employee
-
Warehouse and Fleet Operations Manager
-
Feb 2011 - Apr 2014
Improve facility performance on key metrics and provide accountability to the hourly and supervisory staff including; coaching, discipline, and performance development. Foster an environment in which employees are motivated to deliver top performance. Manage daily operations to achieve loading requirements, meet demand, and provide a high level of customer service. Maintain list of 6 teamster drivers with a fleet of 6 tractors and 25 trailers to ensure all D.O.T. regulations are maintained and loads are delivered in a timely manner. Resolved load stability issues by implementing standard load patterns, dunnage and airbag requirements, and improved wrap methods to save $750K annually. Reduced staff headcount by 8 full-time employees through performance and feedback program to save $480K in support labor annually. Initiated Plant direct shipping program to eliminate $750K in freight costs by shipping directly from the production facility to the customer DC. Initiated facility wide recycling program to increase recycling income by $40K annually and reduce facility waste stream by 10%. Increased warehouse capacity by 25% with layout redesign and racking projects. Reduced teamster headcount by 2 full-time employees through performance management process to save $140K annually.Increased teamster runs per day to generate $40K in backhaul savings in 2012. Received award as a Load Bearing Member (LBM) of the organization in 2012.Selected as a member of the Leadership Development Program in June of 2013.
-
-
Distribution Center Manager
-
May 2010 - Feb 2011
Improve facility performance on key metrics and provide accountability to the hourly and supervisory staff including; coaching, discipline, and performance development. Coordinated facility closure with the supply chain, HR, and customer service teams while maintaining KPI performance. Implemented productivity tracking and feedback program for frontline employees that contributed to a 2% productivity increase. Improved loading process to reduce carrier downtime by 15% and save $90k in carrier detention pay.Drafted forklift maintenance requirements for 3rd party vendor that contributed $20K in savings to the bottom line. Trained hourly and supervisory teams on proper cleanliness and housekeeping standards to improve the overall appearance of the facility.
-
-
-
PepsiCo
-
United States
-
Food and Beverage Services
-
700 & Above Employee
-
Warehouse Manager
-
Apr 2007 - May 2010
Managed a staff of more than 50 hourly union employees and 7 supervisors to maintain P&L, inventory, and productivity goals in a facility with more than 40MM cases of production and 9MM cases of local sales annually. Maintained high standards in sanitation, safety, facility cleanliness, and complied with regulatory guidelines. Improved period inventory reconciliation process to save $95K in a six month period by implementing a daily respond and recover meeting and requiring double counts for month end closes. Improved truck loading accuracy to raise customer service levels which translated to 279K fewer cases cut in 2009 compared to prior year levels. Increased productivity levels 3% year over year through daily coaching and feedback process with the frontline employees. Recognized as a high potential employee and awarded a position in the employee mentor/mentee program.
-
-
Marketing Equipment Supervisor
-
Jan 2005 - Apr 2007
Scheduled and supervised vendor, fountain, and cooler installations and repairs for Western Pennsylvania in a service area that included over 13 thousand customers, 30 service technicians, and 50 thousand pieces of equipment. Reduced parts inventory through reorganization and consolidation of the parts room to save $75K annually. Improved average call response time by 3% and fixed right the first time by 5% by implementing coaching and feedback process to frontline employees.
-
-
Product Availability Supervisor
-
May 2003 - Jan 2005
Supervised and scheduled 42 union employees that efficiently loaded bulk, bay, and transport vehicles in a 15MM case distribution center and performed monthly safety training, facility audits, and period inventory counts. Improved loading productivity by 4% by conducting time studies and implementing productivity targets for the frontline staff. Developed pallet sorting and return process that added 10 thousand square feet of warehouse space to the facility and contributed to less downtime at the Johnstown production facility.
-
-
Checker
-
Jul 2001 - May 2003
Maintained inventory by checking route and bulk vehicles, logging and coordinating transport vehicles, and ensuring that product enters and exits the facility according to warehouse standards. Performed inspections on all vehicles entering and exiting the facility to hold the sales team accountable for breakage, rework, and out of date product. Reduced loading down time by setting up route loading area for the warehouse supervisor.
-
-
Weekend Merchandiser
-
Oct 2000 - Jul 2001
Maintained shelf space by utilizing point of purchase sales techniques and maintaining store merchandising and back room standards. Stocked store shelves, displays, and coolers with Pepsi product and worked with store management to gain display space throughout the account.
-
-
Education
-
Point Park College
Bachelor of Applied Science (BASc), Business Administration and Management, General
Community
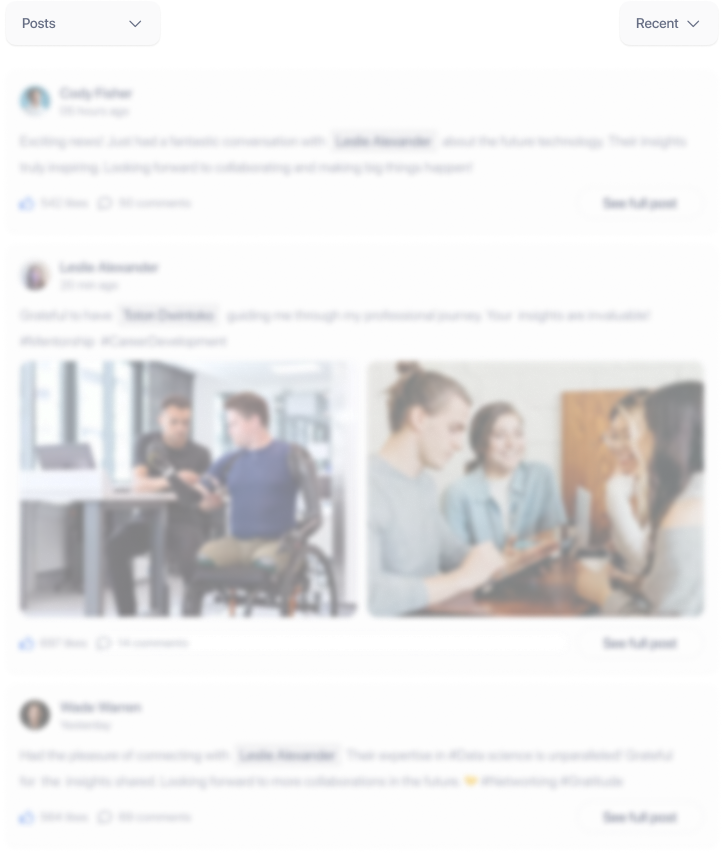