
Marissa Vitug
Manager, Order Management at Wiwynn Mexico SA de CV- Claim this Profile
Click to upgrade to our gold package
for the full feature experience.
Topline Score
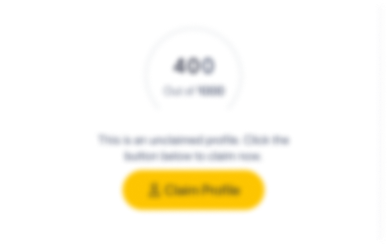
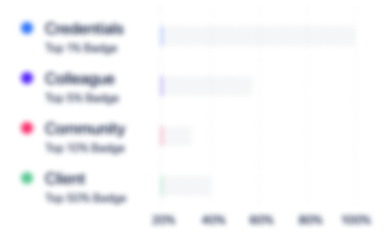
Bio


Experience
-
Wiwynn
-
Taiwan
-
IT Services and IT Consulting
-
500 - 600 Employee
-
Manager, Order Management
-
May 2019 - Present
• Forecasting, capacity planning to compute the expected products to build and ship, trailer load planning to ensure trailers are planned and at a maximum load.• Directs and manages demand execution, production and shipment priorities with Planning and Logistics team.• Communicates with headquarters in resolving issues related to material shortages, order priorities and formulating efficiency to satisfy customer’s needs and expectations, hitting monthly revenue targets and business goals.• Ensures the timely and successful delivery of the products to Data Centers according to customer’s forecasts and priorities.• Interface directly with customers, including (Data Center) site survey and assessment.
-
-
-
-
Purchasing Manager
-
Sep 2018 - Apr 2019
• Responsible for the management of a large group of purchasing personnel and ensures the team is performing at a high level of efficiency and exercising due diligence at all times.• Provided a strong and motivating leadership to all Purchasing personnel to maximize efficiencies and performance through coaching, trainings, workshop and performance evaluation.• Responsible for the execution of the purchasing process related to raw materials and test equipment as needed in NPI and mass production, supplier onboarding, both direct and VMI vendors.• Strategically identify alternative source, components and delivery strategy to support the production and critical business needs.• Oversaw the development and implementation of purchasing strategies and initiatives for LMHV (Low Mix High Volume), HMLV (High Mix Low Volume) and highly complex products of eleven business units and four manufacturing plants.• Collaborated with central team to formulate and provide solutions to purchasing and system issues, bringing both global and regional functional expertise and best practices - Order lead time reduction, MOQ reduction, inventory and cost reduction, system bug, process alignment, automating manual processes and tasks as possible.• Monitored suppliers performance metrics such as delivery performance, adherence to procurement policies, customer support and services.• Collaborated closely with Planning team on PO rescheduling/cancellation and inventory management for both on-site and VMI hub locations to increase inventory turns.• Collaborated with Logistics team and suppliers on exploring every possibility to at least minimize the impact of Section 301 tariffs for raw materials that are made in China.
-
-
-
-
Supply Chain Manager / Account Management Manager
-
Mar 2015 - Sep 2018
• Led a complex customer requirements and business models of one of the world’s biggest appliance makers.• Provided strategic leadership and direction to Order Management and Procurement team.• Oversaw and resolved escalated issues arising from customer forecast, order management, inventory management, shipments/deliveries, payments, PPV’s and data management.• Secured adequate inventory levels of raw materials and manufactured parts are monitored and maintained to meet customer’s demand and sales plan, avoid slow moving items, obsolescence and minimize cost.• Developed and enhanced supply chain processes, both process and risk management, to ensure the operation is equipped to be successful in current and future business.• Ensures all supplies are secured for production use and the biggest detractors to hitting target are eliminated to meet short and long-term priorities and sales plans. • Reviewed and highlighted contract/supply agreement clauses or business terms that need to be negotiated.• Customer relations specifically to manage day-to-day interaction and communication with customers empowering customer service at all levels of the supply chain and fulfillment, identifying and anticipating the needs of customer that are aligned with the best practices and interest of the company.
-
-
-
-
Supply Chain Director
-
Feb 2010 - Mar 2015
• Oversaw all aspects of global business strategy, fulfillment and order management, supply chain management and operations, material supply, manufacturing and shipment optimization, process improvement, strategic inventory management, local sourcing, VMI (Vendor Managed Inventory)/JIT (Just In Time) solutions, commercial/liability/inventory claims, component sales and project cost, inbound and outbound freight cost reduction, BOM cost reduction and NPI of the world’s leading Multinational Corporations –BlackBerry, Mattel, Ecobee and Cognitive Systems.• Administered best service and solutions to meet business and customers’ expectation.• Provided supply chain expertise to optimize systems and processes, both internal and external, to management team and customers, driving a more flexible supply chain such as EDI, web service solutions and other analytics report automation.• Utilized benchmarking techniques and trend analysis to ensure supply chain strategy is aligned to customers’ and Wistron’s standards.
-
-
Fulfillment Manager
-
Aug 2003 - Jan 2010
• Responsible for managing the entire production planning for Acer, IBM, Lenovo and Fujitsu Siemens which includes demand, MRP, material supply, production capacity, on-site and hub inventories, order fulfillment, shipment, payment, project development and DOA/RMA.• Administered the team for worldwide account management to ensure timely possession of information and materials for smooth production.• Managed the forecast from customers worldwide and execute strategic sales plans.• Involved at all stages of production development – from NPI (New Product Introduction) to volume/mass production.• Worked with PM, RD, EE, PCC and CFE for production, quality and engineering issues.• Estimated and analyzed the monthly sales revenue, Margin Report, shipments and demand hit rate.• Maintained the lowest possible liability of inventory and reducing risk for both company and the customer.• Maintained business relationship with customers and other vendors to facilitate the supply of raw materials in a timely manner. • Interfaced with customers and manufacturing team to build up rapport and resolve issues as the business requires.
-
-
-
Wistron InfoComm Philippines Corporation
-
Philippines
-
Appliances, Electrical, and Electronics Manufacturing
-
1 - 100 Employee
-
Fulfillment Specialist
-
Jun 1999 - Jul 2003
• Responsible for managing forecast, planning, order management and shipment of Acer, IBM and Fujitsu Siemens.• Drove daily production activities and instructions to manufacturing team on customer requirements and process improvements with effective communication and leadership.• Reviewed and evaluated sales forecasts, financial reports and tracked inventories, both raw materials and finished products (notebook/laptop).• Established and implemented operational procedures. • Responsible for managing forecast, planning, order management and shipment of Acer, IBM and Fujitsu Siemens.• Drove daily production activities and instructions to manufacturing team on customer requirements and process improvements with effective communication and leadership.• Reviewed and evaluated sales forecasts, financial reports and tracked inventories, both raw materials and finished products (notebook/laptop).• Established and implemented operational procedures.
-
-
Community
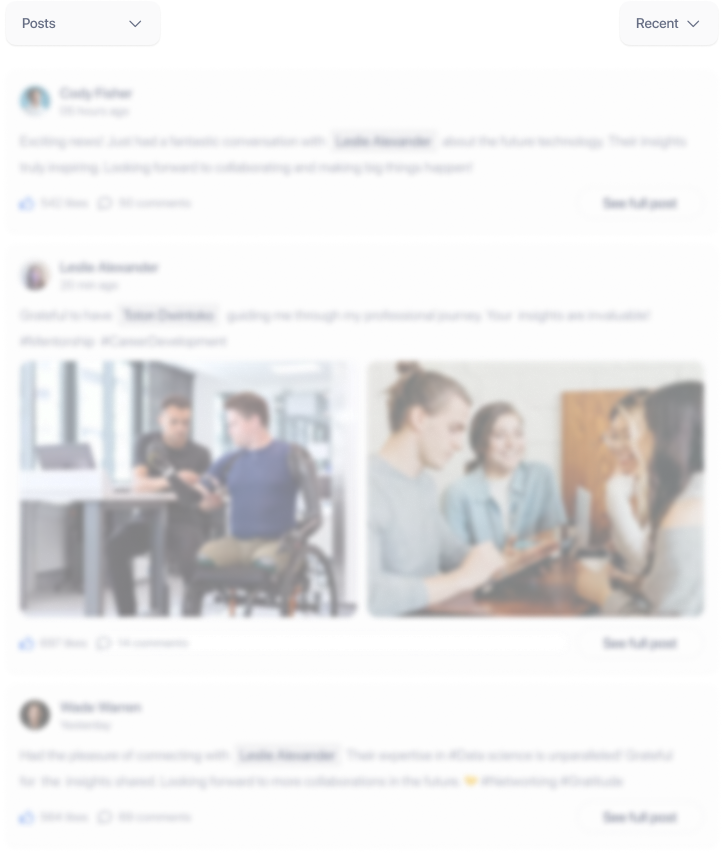