Mario Sanchez
General Manager at KC Jones Plating Company- Claim this Profile
Click to upgrade to our gold package
for the full feature experience.
Topline Score
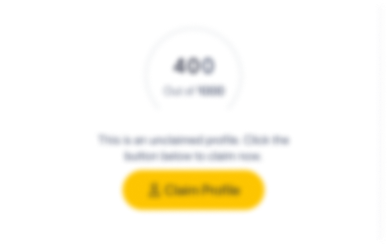
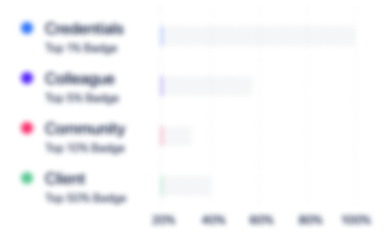
Bio
0
/5.0 / Based on 0 ratingsFilter reviews by:
Experience
-
KC Jones Plating Company
-
United States
-
Motor Vehicle Manufacturing
-
1 - 100 Employee
-
General Manager
-
May 2023 - Present
-
-
-
Martinrea International
-
Canada
-
Automotive
-
700 & Above Employee
-
Sr. Operations Manager HPDC (AGM)
-
Nov 2020 - Jul 2022
** Automotive Aluminum Business Unit ** TIER 1, Biggest Automotive Aluminum Engine Blocks in America & Transmission Housings Die Casting Industry located at Queretaro Mexico, with +750 Employees. Under my responsibility 2 operations plants one for Die casting high pressure (HPDC) with 11 die casting machines between 2500 and 4400 Tons. Machining operations with 65 CNC´s Machine, most of these line all automatized processes. Machined and cast 4 & 6 Cylinders Engine Blocks & Transmission Housing & Aluminum Suspension. Under my responsibility 2 operations plants one for Die casting and the other one for machining. Drives overall operational excellence through the application of LEAN, KAISENS and JISHUKENS good practices events. Increased operating income from 5% to 19% in just 6 Months. Oversee operational metrics to ensure KPIS are in line with targets thru the daily followed of SQDCP OPEX Methodology. Responsible for all P&L management plant, created annual budget and assure all member of the team follow up as well as other financial goals included the saving programs plan. Leading one of the biggest OPEX saving program with a potential saving of 1.15 Millions of Dlls in 1 year, Results 1.35 Million of Dlls during at the end of 12 Months, Project exceeded the expectation. Recommended improvements based to my previous experience in machining equipment’s and manufacturing methods that support process optimizations. Weekly result reports presented to the TOP corporative level. Eliminated Back Log to CERO with 4 of our main customers, (FORD, FCA, NISSAN and DAIMLER). Achieved ZERO accidents on 2021 providing strong leadership over safety programs ensuring the adherence to the rules and workspace policies optimized areas and processes. Show less
-
-
-
UTC Aerospace Systems
-
United States
-
Aviation and Aerospace Component Manufacturing
-
700 & Above Employee
-
Maintenance & Facilities Associate Director
-
Feb 2017 - Nov 2020
** Aerostructure División** Biggest Aerospace Company located at Mexicali Campus Site, with +1000 employees. Responsible for 2 Buildings with 3 Operations Business with 1,350,000 SQ FT. Reporting to Operation Mexico Director, main customers Boeing, Airbus, Bombardier, Embraer, Mitsubishi Regional Jets, etc. Reporting directly to my 4 Maintenance Managers (2 for facilities and other 2 for equipment’s) across the 3 sites, 137 total people under my structure between technicians, Engineers, Supervisors, Team Leaders, and external services. Critical equipment’s categorizations A, B & C, definition of critical spare parts and KPI´s for it. World Class Maintenance KPI´s (MTTR, MTBF, %Availability) and TPM program Implementation. % Availability = 98.5%, MTTR= 2.5 Hrs, MTBF= 245 Hrs., Results until August 2017, improving 6% of % Availability Vs 2016 on critical equipment’s. Leadership event ¨Spare Parts¨saving achieved by $875 K dlls. Installation of 210 new solar panels including an innovative device ¨Solar Smart flower¨, producing 89,500 Kilowatts Hour each Year. Won an award to be a Leader in environmental stewardship receiving the Gold-Level LEED Certification (Leadership in Energy and Environmental Design). CAPEX equipment & facility responsible. Leading a SMED as part of a Global Kaizen event at Singapore, reducing from 318 Minutes to 36 mins, 89% of reduction total savings with just 6 lathes, savings of 165K Dlls. annually. ACE Associate Certification Achieved. Show less
-
-
-
ZF Group
-
Germany
-
Motor Vehicle Manufacturing
-
700 & Above Employee
-
-
Jan 2016 - Feb 2017
** Safety Automotive Braking & Mechanisms División **TIER 1 Plant, One of the largest global automotive plant in the world located at Queretaro facility, with + 1500 Employees.Responsible for Zinc, Zn Ni Plating and E-Coat Paint Processes Responsible for the 2 largest automatized plating machine in America, 23 bars per hour rate production with 110 people reporting directly and indirectly to myself including Maintenance, Facility, Production, Engineering, Quality, Safety, Materials, Lean, including Main leaders. 27 M plating pieces produced annually between Zinc & Zn Ni and 10.2 M of E-Coat.Analyzed production cost and inventories to establish areas of improvement, always achieving the production goals, quality and cost objectives.Improve OEE from 65% to 87% at the end of Jan.2017.Development & Implementation of LEAN OPEX daily track system in the floor to monitoring the performance of all operations reviewing main KIP´s on all departments SQDCP.Ensure the right talent and capabilities be in place to meet strategic objectives, developing the current talent to have ready now the next talent backupsScrap reduction rate at 63% Vs 2015, at the end of 2016 in 1 year, annual savings $585 K dlls.Saving Projects thru Six Sigma methodology ZF & TRW for 1.038 M Dlls achieved. Show less
-
-
-
Jun 2014 - Jan 2016
** Automotive Braking Systems / Machining Areas, CNC´s & Metalworking Processes **OEM Plan, Responsible of machining operations at plants I & II with 77 production lines with 2,193,000 SQ FT between 2 plants.Reporting with Plant manager, our main Customers, Ford, Fiat, Honda, Toyota, VW, Mercedes Benz, GM, Audi, BMW, Mazda, Nissan, etc.596 People under my responsibility including all 10, Managers (2 of Production, 3 of Maintenance including Facilities, Quality, Lean, Materials, Safety, Projects, and 2 Leader of HRBO and FABO. Development & Implementation of daily track system in the floor to monitoring the performance of all operations reviewing main KIP´s on all departments (Safety, Quality, Deliveries, Inventories, Sales, Past Dues, Expenses, Production, Turnover & absenteeism, Etc.), 4 meeting total to cover 24 hours operations.Control and management of operations budget of $ 53,256,375 Dlls. Annually.Implementation of Critical issues quick meeting that as to be resolved into the 8 hours to activate the escalation process. Implementation of weekly workshops, Kaisen, SMED, QOS, programs activated across all plant to increase performance based on weekly data.Monitoring as daily basic P&L to keeping under budget.Implementation of weekly cross audits LPA´s to keep alive the program as well GEMBA walks per lines. PCC, QOS, LPA´s and LOTO Programs implementation. Won first safety leadership award to achieve more than 5 million of hour’s man without lost time incidents completing 1.5 years with Zero accidents.Achieved Quality Ford Q1 Award.OEE & Scrap Achieved records numbers from 2014 to the end of 2015, OEE from 68% to 79% .Saving Over time expenses on Maintenance department from 2650 Hours Monthly to Zero, (Annual OT Savings 540 KDlls.)Over time 35% of DL and headcount 8% reductions at plants level in general improving OEE.SMT expenses reduction 7% Vs 2013 Budget and keeping under control.Past due reduction from 375 Kdlls Monthly to 14K Show less
-
-
-
-
Operation Business Unit Manager
-
Dec 2012 - Jun 2014
**Automotive Lightweight & Commercial Division / Metalworking Processes** Dana Cardane´s Plant is the biggest Mexican operations with 180M of sales, with 760 employees. Responsible for production, maintenance, safety, projects and engineering departments. 24/7 Metal & Mechanic processes, 55 production lines including assembly lines. Under my responsibility 5 Maintenance & Production Leaders, 25 Engineers to support all operation and management about 276 people between technicians, custodians, Metal workers, operators, production supervisors, team leaders and external services. Reporting with plant manager. Production Efficiency & Delivery improvement of 69% to 92%, improving processes. Jishukens and (Work shops) leading obtaining saving of $1,475,635 dlls. Annually. Facility area responsible of 1,237,096 Sq.Fts. and control of 2072 equipment across all factory. Control and management of maintenance and production budget of $ 23,826,125 Dlls. Annually. Maintenance & Production expenses savings programs in charge, 5% Vs 2012, results 7% as Close to December 2013. Achieved 2.6 Million Employee hours without lost time incidents & 555 days without a L.T.I. Down Time, PM, LOTO, Electrical Safe Program, Guarding Machine and TPM programs responsible. Maintenance Down time reduction of 1.28% (2012) to 0.87% as close to December 2013, Goal (1%). % Availability = 98.9%, MTTR= 4.2 Hrs, MTBF= 167 Hrs., Results until Julio 2014. Implementation of total down time cost per maintenance as a KPI. Leading the implementation & standardization Maintenance new KPI´s (MTTR, MTBF, % Availability, OEE, Etc) of 11 plants in Mexico. Show less
-
-
-
-
Maintenance Manager
-
Jun 2010 - Dec 2012
**Automotive & Packaging Moulding Foam Processes** Responsible of building 175,550 Sq.Fts, process equipment’s and new projects. 24/7 Foam molding machines and assembly lines running. Responsible of all building & equipment production, 3 plants, 3 shifts, 45 technicians including set-ups and mold setters. QMC, Down Time, OEE, PM and TPM programs responsible. Leading several projects by Lean techniques CIP, 8D´s, 5´S, 7W´s, SMED LOTO implementation program, guarding machines and electrical safe programs. Leading down time program. (Reduction from 11% (2010) to 1.5 % YTD 2012, Goal 2%. Weekly Monitoring of Maintenance Metrics (PM Achievement and Efficiency, Etc). Implementation and control of Maintenance Software’s, Data Logger, Keep Track and Bear Track. General utilities daily monitoring and control, Gas LP consumption saving controlling boilers (Results 578 K Dlls from Jan thru Dec 2012, Water Savings 275 K Dlls and Electricity 334 K Dlls. Maintenance down time reduction from 4.5 % to 1.2% (Goal 2%). Maintenance Over time reduction 45% Vs 2010. Scrap reduction from 1.5% to 0.6% Vs 2010 (Goal 0.9%) by Poka-Yokes, Travel to Taiwan, Canada, Chicago, Michigan, Atlanta, etc. to validated new equipment and processes to be moved to Mexico. Project managements for $786,897 US Dlls done in one year Show less
-
-
-
-
Maintenance Leader / Automation Engineer
-
Jan 2001 - May 2010
**Appliance Components & Motor Fabrication and Assembly plant** Responsible of all production equipments including forklifts, tool-crib, tool-room, cafeteria and all 712,850 Sq.Ft of building, reporting myself directly to Engineer Director. Under my supervision all technicians and janitorial personnel 32 total including, 8 Engineers. Lay out changes across all factory to install new assemblies line transferred from USA to Mexico. Modification of tooling equipments, fixtures and work station design. Purchase and inventory control of all MRO parts and some MRP. Purchased of new equipments to replace obsolete. Accounts Managements. In charge of EMS "Energy Saving Program" (Green Spirit). Results Savings 2009 Vs 2008; Electricity 18% (577,175 KWH), Natural Gas 13% (14,795 M3), Water 7% (870 M3) Total savings $60,743 Dlls. Over time Maintenance reduction of 45% to 8% on the first year. Leading EMS "Indirect Expenses Team".Saving 2009 Vs 2008, -24%- ($102,458 Dlls.) Responsible to keep multimillionaire automation equipments working. Show less
-
-
-
-
Maintenance & Manufacturing Engineer
-
Jan 1997 - Jan 2001
**Electrical Motor Division** In charge of Building & Equipment maintenance areas 3 shifts, 35 Techs. Develop and follow the annual preventive maintenance program. Relocation of all plant 5 to plant 1. Travel to AltaVista to transfer complete lines to Mexico. Travel to England for a month to check up a new equipments and training. Travel to North Carolina and Fort Wayne to validated new equipments. Documentation, control and manufacturing of test prototypes. Poise production lines, BOM managements and procedures plan. Received equipment training for two months in Charlotte N.C. Equipment installations and provide training of new production lines. Show less
-
-
-
-
Maintenance General Supervisor
-
Jan 1990 - Jan 1997
**Automotive Harnesses Division** In charge of 18 technicians that supported all maintenance areas. Analysis of Maintenance down time and preventive solutions. Planning and development of preventive maintenance and corrective. Continuous improvement, poke-yokes, Quick change, SMED. Etc. Maintaining Tool-Crib inventory control, functional and a low cost. Implementation and development of the automated system Main Saver; to control all maintenance, tool-crib, tool-room, tools, and purchases. Show less
-
-
Education
-
CETYS Universidad
Diploma of Education, EMOTIONAL INTELLIGENCE -
CETYS Universidad
SIX SIGMA BLACK BELT, Accounting and Finance -
CETYS Universidad
Diploma of Education, High Management Direction -
Universidad Autónoma de Chihuahua
Master of Business Administration - MBA -, Finance, General -
Universidad Autónoma de Ciudad Juárez
Bachelor of Engineering - BE, Electrician
Community
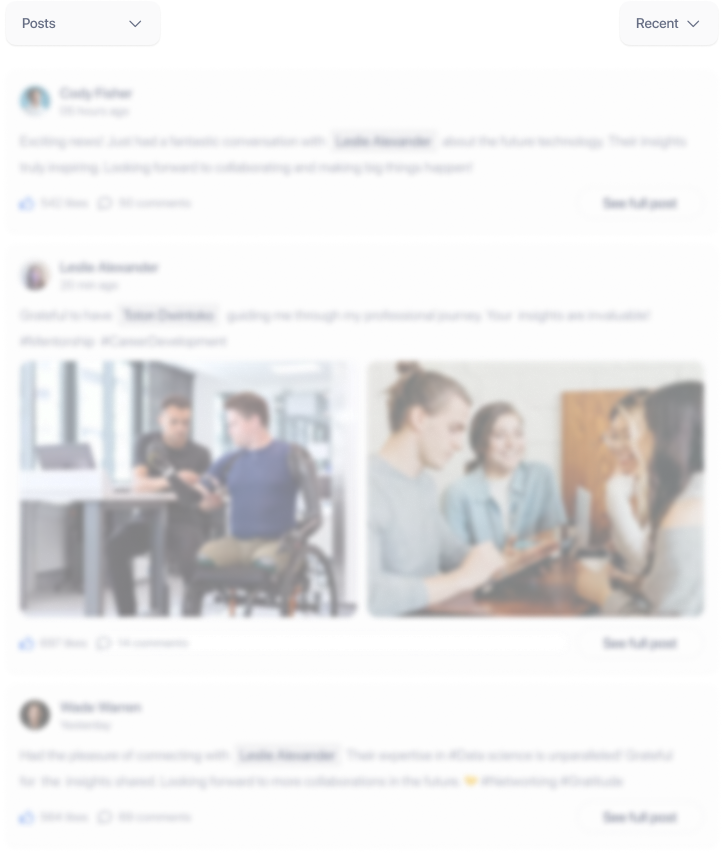