
Mario Rostant MBA
Supply Chain Coordinator at Trinidad Cement Limited- Claim this Profile
Click to upgrade to our gold package
for the full feature experience.
Topline Score
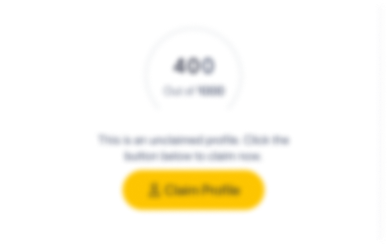
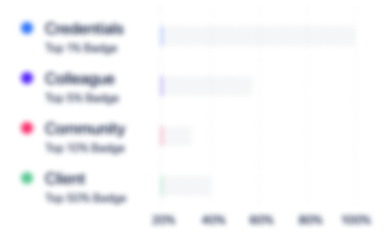
Bio


Experience
-
Trinidad Cement Limited
-
Wholesale Building Materials
-
100 - 200 Employee
-
Supply Chain Coordinator
-
Feb 2019 - Present
-
-
-
Stork, a Fluor company
-
Netherlands
-
Mechanical Or Industrial Engineering
-
700 & Above Employee
-
Access Team Lead
-
Aug 2017 - Nov 2018
-
-
-
SLB
-
United States
-
Technology, Information and Internet
-
700 & Above Employee
-
Materials Supervisor
-
Dec 2014 - Aug 2017
Main Objective is the Managing,Supervising and Coordinating all the Receiving, Storage and Distribution of all inventory, communicating with related personnel of the company while carrying accurate inventory. Main Objective is the Managing,Supervising and Coordinating all the Receiving, Storage and Distribution of all inventory, communicating with related personnel of the company while carrying accurate inventory.
-
-
-
-
Warehouse Leader
-
Mar 2014 - Oct 2014
Main Objective is the Managing,Supervising and Coordinating all the Distribution,Storage,Facilities and Logistics activities and related personnel of the company while carrying accurate inventory.Ensuring compliance, where products, parts, or supplies are shipped, distributed, or received in an efficient manner reducing, cost and lost prevention.Responsible for the management of warehouse(s) and plant(s) within the company.To report on distribution and logistical activities for operational management review purpose.Plan and coordinate distribution and trucking activities.Lead the implementation of quality and continuous improvement plans. Communicates with vendors, customers, carriers, brokers, agents etc..Ensures that Supervisors comply withrelated policies and procedures.Ensure that all arrangements are made for loading / offloading of cargo prior to arrival of container, vessel or truck.Coordinates the handling of import and export requirements. Ensure that a proper count of incoming stock is made and compared with the listed amounts on the shipping document / D.N. followed by a report to the Inventory personnel upon completion.Advice internal customer on stock levels, and movement.Manage and ensure that accurate monthly physical stock checks.where possible strive for real-time inventory management system at warehouse and mud plant.Ensure that stocks are stored in a safe and secure manner at all times.Ensure that damaged or written off stock is reported and approved by Management prior to any removal.Ensure that written off stock is disposed according to local EMA regulations.Ensure that materials are properly packaged prior to leaving the warehouse. Ensure appropriate approval and order for Delivery, also ensure that documentation is processed as quickly as possible to allow prompt invoicing.Ensure that all information is provided on the delivery notes.Report non-conformance of purchases of products or services with respect of approved vendor list.
-
-
Logistics Coordinator
-
Jan 2012 - Feb 2014
Main Objective is the Managing,Supervising and Coordinating all the Distribution,Storage,Facilities and Logistics activities and related personnel of the company while carrying accurate inventory.Ensuring compliance, where products, parts, or supplies are shipped, distributed, or received in an efficient manner reducing, cost and lost prevention.Responsible for the management of warehouse(s) and plant(s) within the company.To report on distribution and logistical activities for operational management review purpose.Plan and coordinate distribution and trucking activities.Lead the implementation of quality and continuous improvement plans. Communicates with vendors, customers, carriers, brokers, agents etc..Ensures that Supervisors comply withrelated policies and procedures.Ensure that all arrangements are made for loading / offloading of cargo prior to arrival of container, vessel or truck.Coordinates the handling of import and export requirements. Ensure that a proper count of incoming stock is made and compared with the listed amounts on the shipping document / D.N. followed by a report to the Inventory personnel upon completion.Advice internal customer on stock levels, and movement.Manage and ensure that accurate monthly physical stock checks.where possible strive for real-time inventory management system at warehouse and mud plant.Ensure that stocks are stored in a safe and secure manner at all times.Ensure that damaged or written off stock is reported and approved by Management prior to any removal.Ensure that written off stock is disposed according to local EMA regulations.Ensure that materials are properly packaged prior to leaving the warehouse. Ensure appropriate approval and order for Delivery, also ensure that documentation is processed as quickly as possible to allow prompt invoicing.Ensure that all information is provided on the delivery notes.Report non-conformance of purchases of products or services with respect of approved vendor list.
-
-
-
-
Senior Supply Chain Officer
-
Jan 2008 - Jan 2011
Daily supervision of staff to ensure functions is carried out in an efficient manner.Recommendation for performance evaluation (appraisals), staff training, work allocation and problem solving.Developed customized strategies providing high customer service and reduced cost.Developed record keeping procedures & manages appropriate department records in accordance with applicable regulations, policies and procedures.Assisted manager in the development of operating goals and objectives for the department, recommends, implements and administers methods and procedures to enhance operations.Co-ordinates the procurement process ensuring proper sourcing of, negotiation with and evaluation of suppliers. Approvals of purchase requisitions making sure all requirements are attached to requisitions, generating and printing of purchase orders.ContractsDaily Supervision of staff to ensure that functions are carried out in an efficient mannerRecommendation for performance evaluation (appraisals), staff training, work allocation and problem solving Leads the Supplier Pre-Qualification team, through which prospective suppliers are shortlisted.Generates the Invitation to Tender package in accordance with the SWRHA’s tendering policies and procedures. Participates in the Bid opening and documentation processEnsure, as part of the commercial bid evaluation team, that SWRHA’s Standard Operating Procedures are stringently adhered to.Generates goods and services contracts in accordance with either FIDIC Conditions of Contract or the SWRHA’s General Conditions of Contract.Developed and maintains a feedback system, ensuring that goods and services are received in a timely manner and that all pertinent information is disseminated to end users throughout the SWRHA.Assist in the annual budget planning process and regularly monitor expenditure.
-
-
Senior Supply Chain Officer
-
Jan 2007 - Jan 2008
InventoryDaily Supervision of staff to ensure that functions is carried out in an efficient mannerRecommendation for performance evaluation (appraisals), staff training, work allocation and problem solving Assist in Building a computerised inventory systemMaintained computerised inventory system by coordinating physical inventory process, minimun/maximum levels of stock, the count cycle, discrepancies and stock obsolescent Maintained the inventory database which includes catalogues for stock items and details of items. Daily supervision of staff to ensure function is carried out in an efficient manner, also typically include recommendation for performance evaluation, staff training, work allocation and problem solving.
-
-
-
-
Materials Specialist
-
Jan 2005 - Jan 2007
Responsible for the issuing of Purchase Orders goods & services were done in a timely manner and verifying price and delivery of all items, in compliance with company's policies and procedures.Ensured that stock and non-stock items were delivered as per delivery dates and that the warehouse was aware of receipts.Gave proper and astute feedback to customers as to the status of goods and services ordered.Invoicing of all goods and services before be delivered to customers.Monthly and weekly reports to managers and directors on the status of customers' orders.Updating of the computerised inventory system after periodic and annual stock counts.Assisting in periodic and annual stock counts.
-
-
-
-
Terminal Clerk
-
Jan 1998 - Jan 2005
assigned to the Stores Department for Heavy Equipment.Ensuring minimum/maximum levels for stock itemsRequisitioning of stock itemsIssuing and receiving of all goods and services, ensuring compliance to purchase ordersRotation of items when restocking warehouse shelves, ensuring that items do not cross it's shelf life date.Assisted in the stock count process by verifying items for the stock count teamsMaintained the computerised inventory system, ensuring physical quantities and system quantities match.
-
-
Education
-
Arthur Lok Jack Global School of Business, University of the West Indies
Master of Business Administration (MBA), International Trade Logistics and Porcurement -
Arthur Lol Jack Graduating School of Business
Masters of International Trade, Procurement and Logistics. -
Present Heriot Watt University
B.A
Community
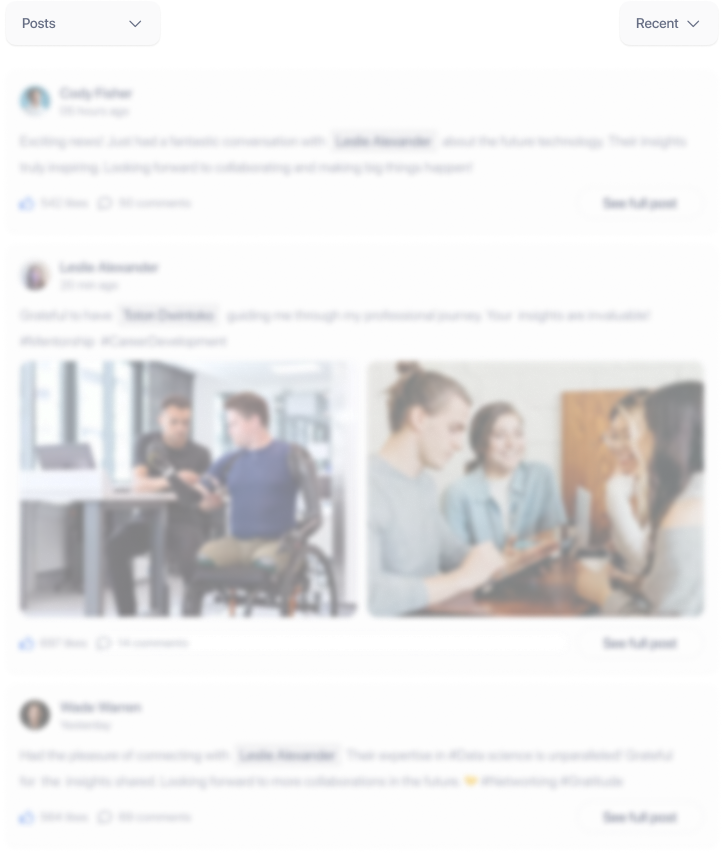