Mario Garcia
Vice President of Manufacturing at Velentium- Claim this Profile
Click to upgrade to our gold package
for the full feature experience.
-
Spanish -
-
English -
Topline Score
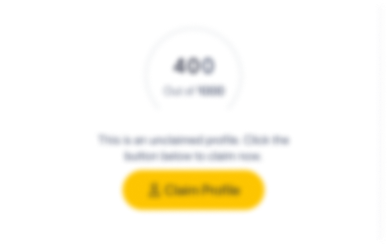
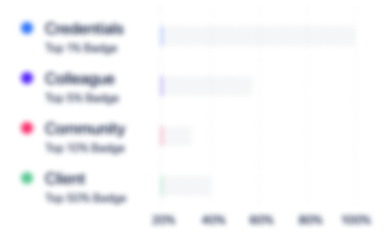
Bio
0
/5.0 / Based on 0 ratingsFilter reviews by:
Experience
-
Velentium
-
United States
-
Medical Equipment Manufacturing
-
1 - 100 Employee
-
Vice President of Manufacturing
-
Jan 2023 - Present
Velentium specializes in the end-to-end design, development, manufacturing and post-market support of therapeutic and diagnostic active medical devices. Our core competencies include active implantable medical devices, systems engineering, firmware & software, cybersecurity, mobile & cloud, electrical & mechanical engineering, human factors & usability, automated test systems, and CGMP manufacturing. Velentium specializes in the end-to-end design, development, manufacturing and post-market support of therapeutic and diagnostic active medical devices. Our core competencies include active implantable medical devices, systems engineering, firmware & software, cybersecurity, mobile & cloud, electrical & mechanical engineering, human factors & usability, automated test systems, and CGMP manufacturing.
-
-
-
CAPS® (Central Admixture Pharmacy Services, Inc.)
-
United States
-
Pharmaceutical Manufacturing
-
100 - 200 Employee
-
General Manager
-
Aug 2021 - Jan 2023
CAPS is a 503B central admixture pharmacy services. Products includes from daily delivery of custom parenteral nutrition solutions, to premixed Oxytocin bags, pre-filled anesthesia syringes, IV and epidural, drug delivery, pre-filled post-op pain pumps, or cardioplegia. Responsible for the Phoenix facility on Safety, Quality, Cost, Delivery, and People development. A facility of 250K SqFt with 200 employees under clean room class 7,8 & hoods class 5, using VHP (Vapor Hydrogen Peroxide) sterilization process in house. A low mix, high volume. Manufacturing Processes: Aseptic product, drug compounding, packaging and distribution. Show less
-
-
-
Avanos Medical
-
United States
-
Medical Equipment Manufacturing
-
700 & Above Employee
-
Plant Manager and Integration project leader
-
Dec 2018 - Jun 2021
Avanos is a medical technology company focused on delivering clinically superior breakthrough medical device solutions to improve patients’ quality of life. The company is comprised of two franchises – Pain Management and Chronic Care, under digestive, respiratory health and IV therapy products. Responsible for 2 manufacturing sites at Tucson AZ USA and Nogales MX from Dec 2018 to June 2021. FDA registered. Tucson: A facility of 140K SqFt manufacturing Operation and 400 employees with a high mix low volume, building medical devices for digestive health, Medical devices with drugs, pharmaceutical products, biological laboratory, and distribution center and warehouse. Sterile product controls. Nogales: A facility of 100K SqFt manufacturing operation with 1,200 employees with a high mix and high volume, building medical devices for Digestive and Respiratory heath. Sterile product controlsIntegration Project leader: Responsible to lead transfers site to site, coordinate full transfers by avoiding service disruption and getting saving benefits to the company. Main transfer was Oral Care product and 5X increase capacity into Nogales and transfers out of Tucson to Tijuana. Manufacturing processes: Avent at Tucson: Digestive devices and Kitting assembly including drugs, in-vitro diagnostic for ulcer detection, Radio nuclear pharmaceutical diagnostic, drug encapsulating and packaging, Chemical preparation and cup filling, Oral mouth cleaning kits, electronic servicing and assembly for nasal gastric feeding tube placement tracking device, direct distribution. Avent 1 Nogales: Enteral feeding G-tubes, accessories and kits, Nasogastric tubes, Endotracheal tubes, needles kits and trays, Jejunal tubes, Oral mouth cleaning kits. Show less
-
-
Plant Manager and Integration Project Leader
-
May 2016 - Dec 2018
Responsible for 2 manufacturing sites at Nogales MX from May 2016 to Dec 2018. FDA register. Avent 1 at Nogales: A facility of 100K SqFt manufacturing operation with 600 employees with a high mix and high volume, building medical devices for Digestive and Respiratory heath. Avent 2 at Nogales: A facility of 70K SqFt with 350 employees for plastic and silicon Molding machines plus extrusion with 45 Plastic molding machines and 15 silicon molding machines. ALP(Auto Liquid process) with RO system to produce vials. Integration Project leader: Responsible to lead transfers site to site, coordinate full transfers by avoiding service disruption and getting saving benefits to the company. Main transfer was Corpak facility (Nasogastric tubes) from Chicago to Nogales MX and several acquisitions of new molding machines and new molds to increase capacity. Manufacturing processes: Avent 1 Nogales: Enteral feeding G-tubes, accessories and kits, Nasogastric tubes, Endotracheal tubes, needles kits and trays, Jejunal tubes, Avent 2 Nogales: Molding process 45 machines from 28 Tons to 220 Tons, cold and hot runners; Liquid Molding for Silicon 15 machines; auto liquid process (ALP) with sterile saline water; extrusion process, microbiology laboratory, Tool room to fix molds in house. Show less
-
-
-
Lake Region Medical
-
Medical Equipment Manufacturing
-
400 - 500 Employee
-
Director of Operations
-
May 2011 - May 2016
A Medical device company dedicate to outsource product, offering service to design, develop and manufacture range from finished device systems Class I to III to hundreds of components. Manufacturing medical device in the markets of Electro physiology, Vascular access, Arthroscopy, Urology, Biopsy/drug delivery, Peripheral vascular, Laparoscopic and General surgery. Some of the main customers are St Jude, Medtronic, J&J, Cordis, BSC, Cr bard, Dendreon, Covidien, Bayer, Depuy Mitek, Conmed, Neurotherm, Stryker, Smith and Nephew, Synergetic, Intact, Bausch + Lomb, RyMed and KCI. Leading 2 manufacturing plants at Juarez MX plus a distribution center at ELP Texas from May/2011 to May/2016 and full P&L responsibility under high mix and low volume. FDA register. Juarez: 2 facilities of 160K SqFt with 1,000 employees, services include assembly of finish goods, manufacture of components and Molding process (13 Injection machines) as part of a vertical integration; including packaging, labeling and coordination for sterilization on ETO & Gamma. Manufacturing processes: Juarez: Diagnostic and therapeutic catheters, Laparoscopic trocars, breast biopsy devices, Biopsy forceps, Guidewires, Cartilage ablation devices, non-surgical permanent birth control implantable, embolic protection systems, Kidney stone retrieval catheter, Microwave Thermotherapy Catheter for Prostate, Neutral Fluid dispensing IV connectors, Negative pressure wound care Therapy, Hip and knee Arthroscopy shavers and burrs, Molding process and Over molding. ELP: Warehouse & distribution center of 20K SqFt, 10 employees for shipping and receiving, customs and delivery of FG. Show less
-
-
Business Unit Manager
-
Mar 2006 - May 2011
Interface directly with customers and sales reps to lead efforts for interdepartmental members to develop, improve, validate and sustain the existing products as well as support new transfers. Responsible for safety, fill rate, back orders, delivery on time, cost and quality of products in BU. proactively manage the risk associated with each project to achieve company goal and/or objectives and keeping the business with customers. Responsible to coordinate, present and explain the monthly metrics results with different customer for QBR as well as reviews and approves documentation to verify compliance of specifications, standards, procedures and FDA requirements. Support to generate quotes for customers related to validations, samples, Engineering testing, reworks, process and/or design changes requested by the customers. (NRE). Work along sales representatives to help customer needs and develop a plan to meet their requirements and/or needs. Maintain a good customer communications and credibility. Establishes goals and following up for all products in BU to improve the metrics such as scrap, labor variance, labor utilization, efficiencies, overtime, complaints, headcount, down time, capacity, safety & MRB. Experience in transfers of new product lines. Validation/ramp up/stabilization. Promotes teamwork and lean manufacturing techniques for continuous improvement to reduce waste.Main Accomplishments: EBITDA from 2008: 12.6%; 2009 24.2%; 2010 30.4%. Lead lean activities to save 6,700 Sqft on clean room. Successful lead in transfer of 2 production lines representing sales of $2.5M per year during 2006, support transfer Prolieve in 2007 representing $3.3M ; 2009 for 2 lines (Camplate & Medtronic) representing $4.5M per year; 2010 B&L representing $1.8M. During 2009 achieved 100% quality acceptance &100% on time delivery for S&N products. Implementation of Kanban system for FG. Reduction of 12.5% customer complaint (16 in 2008 to 14 complaints 2009), Show less
-
-
Engineering coordinator
-
Oct 2003 - Mar 2006
Management and leadership the efforts of the engineering team (4 process engineers/16 technicians) by tracking and following up tasks and projects assigned to be accomplished on time as well as the coordination of the preventive maintenance procedures. Responsible to coordinate all process engineering duties on BU by establishing goals to improve processes and/or equipment for current and new products. Direct responsible to develop and execute validations on new and current equipment and/or processes (generation of protocols, run validations, analyzes results and writing final report). Direct deal with customer (BSC-Boston Scientifics) for transfers, improvements, cost savings ($110K 2005), validations, new products introduction, complains and business status update for GBF product(Gastrointestinal & Pulmonary biopsy forceps) and Polypectomy snares. Responsible to built and validate brand new production lines and equipment to be transferred from Juarez to Costa Rica as well as lead transfers from USA to Juarez. Responsible to quote, buy, build and install new and/or equivalent equipments for company growth or capacity incensement as well as to justify expenses generated on each project. To review and approve documentation to verify the proper compliance on procedures, temporarily deviations, permanent changes, specifications, work instructions, routings and BOM’s. Show less
-
-
-
CR Bard
-
United States
-
Medical Equipment Manufacturing
-
700 & Above Employee
-
Sr Process Eng
-
Jan 2001 - Oct 2003
Responsible to validate new and existing machinery, tools and/or parts qualification from new supplier or mold changes. Identify and develop cost improvement by developing more cost effective methods for producing products implementing new equipment and/or automating processes. Over $ 300K on 2003 Continually upgrade and improve operations and performance of existing equipment and processes through redesign and enhancements. Analyze, justify and request capital budget for new projects. Responsible for PLC upgrade to Allen Bradley, software validations and programming changes. Implementation of a system that automatically collects data and parameters used in several machines into the facility and saved into the common net. Support plans of transitioning exiting processes to Davol’s Mexico operation from other Davol facilities. Responsible for development, implementation and maintenance of manufacturing procedures as well as the drawing up of operation procedures and visual aids. Resolve chronic production issues that affect production performance especially when issues require technical support. Complete studies of machinery capacity and method studies to improve manufacturing process in order to improve equipment and manpower utilization. Ensure that manufacturing processes and procedures comply with FDA regulations by completing the required process and equipment qualification studies. Responsible to implement corrective actions that resolve chronic production issues or possible customer complains. Continuous dealing with local and foreign suppliers. Show less
-
-
-
Delphi
-
United Kingdom
-
Motor Vehicle Manufacturing
-
700 & Above Employee
-
Process Engineer
-
Jan 2000 - Jan 2001
Development for new products and processes in transferences. Validate and release new equipment and machinery in transference projects. Active participation on the prototype runs and validations prior to send the equipment to México facility. Lean manufacturing systems implementation. Continuous improvement on processes and maintenance support. Coordination of new processes and following up until process is stable. Troubleshooting by using PFMEA, SMED and 8 D. Documentation control for all process parameters, procedures, changes and modification in machinery and/or spare parts. Show less
-
-
Education
-
Instituto Tecnologico de Chihuahua
Certified Bachelor of Science in Industrial Electronic Engineer., Major in Industrial Eng
Community
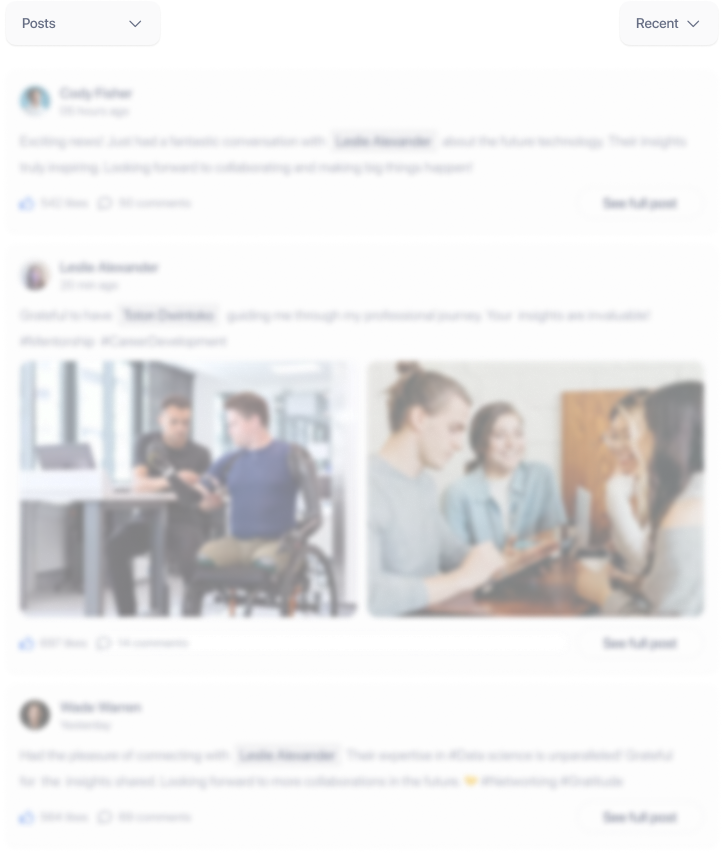