Marina Garcia CEng MIChemE
Senior Process Engineer at Worley- Claim this Profile
Click to upgrade to our gold package
for the full feature experience.
-
English Full professional proficiency
-
French Professional working proficiency
-
Vasco Native or bilingual proficiency
-
Catalán Elementary proficiency
-
German Elementary proficiency
-
Spanish Native or bilingual proficiency
Topline Score
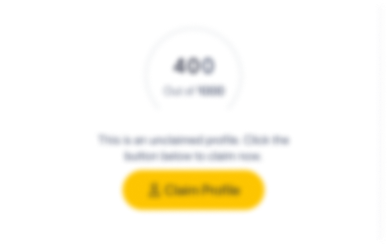
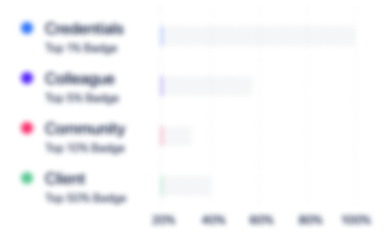
Bio


Credentials
-
International Project Management
Rochester Institute of TechnologyOct, 2017- Oct, 2024 -
Hazards Identificacion techniques
Institution of Chemical Engineers (IChemE)Aug, 2017- Oct, 2024 -
Drinking Water Treatment
Delft University of TechnologyMar, 2017- Oct, 2024 -
Treatment of Urban Sewage
Delft University of TechnologyMar, 2017- Oct, 2024 -
Layers Of Protection Analysis (LOPA)
HSE Science and Research CenterJul, 2016- Oct, 2024 -
Best Practices for Project Management Success
Rochester Institute of TechnologyMay, 2017- Oct, 2024 -
Project Management Life Cycle
Rochester Institute of TechnologyJan, 2017- Oct, 2024 -
MOOC Fundamentals of Six-Sigma: Quality Engineering and Management
Technische Universität MünchenJun, 2016- Oct, 2024 -
MOOC Sustainable Mobility 2
IFP SchoolNov, 2015- Oct, 2024 -
GESTION DE PROJET
MOOC Gestion de projetSep, 2015- Oct, 2024 -
MOOC Oil & Gas Achievement Certificate
IFP SchoolJun, 2015- Oct, 2024 -
edX Honor Code Certificate for Introduction to Oil Country Tubular Goods (OCTG)
edX -
edX Honor Code Certificate for Introduction to Running Pipe in Oil and Gas Wells
edX
Experience
-
Worley
-
Brazil
-
Business Consulting and Services
-
700 & Above Employee
-
Senior Process Engineer
-
Oct 2022 - Present
-
-
-
Tata Chemicals Europe
-
United Kingdom
-
Chemical Manufacturing
-
1 - 100 Employee
-
Process Engineer
-
Jul 2019 - Feb 2022
Senior Process Engineer working with a multidisciplinary team in the Project Department. I was in charge of designing a new Sodium Bicarbonate Plant (575tn/day) including the utilities systems. Also I supervised and led the process design and hazard studies of the biggest Carbon Capture Plant of the UK The plant is capable of capturing and producing up to 40,000 tonnes a year of CO2 to reduce TCE's carbon emissions by 11 %. And I supported the plant teams in the resolution of technical operational problems.
-
-
-
ProLogical Ltd
-
Wincham, Cheshire, United Kingdom
-
Senior Process Engineer & Project Manager
-
Jun 2017 - Jul 2019
Senior process engineer for a top tier COMAH site. Key responsabilities included as the responsible Process Engineer at HAZOP and LOPAs, conducting sizing calculations, close out safety critical corrective actions, update P&IDs. My role involved leading a multidisciplinary team as well as liasing with operations personnel, external contractors and relevant stakeholders. I managed the scope, time and quality of multiple ongoing projects(£15M), as well as I supervised young engineer's work. Senior process engineer for a top tier COMAH site. Key responsabilities included as the responsible Process Engineer at HAZOP and LOPAs, conducting sizing calculations, close out safety critical corrective actions, update P&IDs. My role involved leading a multidisciplinary team as well as liasing with operations personnel, external contractors and relevant stakeholders. I managed the scope, time and quality of multiple ongoing projects(£15M), as well as I supervised young engineer's work.
-
-
-
C-Tech Innovation
-
United Kingdom
-
Industrial Machinery Manufacturing
-
1 - 100 Employee
-
Engineering Consultant
-
Apr 2017 - May 2017
Responsible for the process design of the cryogenic filling station for a Hydrogen cell based airplane. I managed the design of a multi-unit pilot plant to simulate the performance of one hydrogen cell and multiple hydrogen cells according with different flight conditions (humidity, pressure, temperature,...). Responsible for the process design of the cryogenic filling station for a Hydrogen cell based airplane. I managed the design of a multi-unit pilot plant to simulate the performance of one hydrogen cell and multiple hydrogen cells according with different flight conditions (humidity, pressure, temperature,...).
-
-
-
MALONEY METALCRAFT LTD
-
Oil and Gas
-
1 - 100 Employee
-
Process Engineer
-
Apr 2014 - Oct 2016
Process Engineer with responsibility for the process design of oil & gas treatment packages during conceptual, front end through to as-built design stage working as a member of the Engineering Department and also providing technical support to Sales Department reviewing client specifications and clarifications. I am responsible for sizing of equipment, lines and relief valves, completing equipment data sheets, relief valve sizing, using Hysys for material balances and writing descriptions of operation, control narratives and operating manuals. Developing P&IDs and PFDs. Attending meeting with client and suppliers, including HAZOP’s. Projects include: • 2-3 phases separators • Fuel Gas Units • Gas dehydration with TEG • Produced Water Treatment Unit • Amine Units • Gas dehydration with solid desiccant
-
-
-
BioWayste
-
Brixworth
-
Process Engineer
-
Nov 2013 - Feb 2014
Process engineer working on all round engineering support of High Rate Anaerobic Digestion plant across all phases of the project cycle from conceptual design to commissioning of the plant. Using high rate AD to treat waste effluents from different sectors (Beverage and Food) to provide green energy and helping the reduction of CO2. I was in charge of £2M new AD project from the basic engineering to the detail engineering and from sizing the equipment and lines to the procurement of them. The effluent flowrate was about 40,000-ton p.a. The modular AD plant was built on its seven-acre site, with six high rate reactors with CHP engines which provided to the company with 75% of its electricity usage, all generated from waste products being tinkered from site. Also, I contributed in the optimization of AD plant. The company was handling around 1.5 tons of COD/day from the liquid waste stream and a further 4 tons of COD from the macerated fruit peelings. This biogas supplied a total of around 200 kW of electricity back to the factory for use in the 24/7 production process. Heat recovered from the CHP engines was used to maintain the anaerobic digesters at their optimum 38°C. At full capacity, the plant was capable of handling nearly 7 tons of COD/day. The waste volume was reduced by 80%.
-
-
-
Pell Frischmann
-
United Kingdom
-
Civil Engineering
-
400 - 500 Employee
-
Chemical Process Engineer
-
Nov 2012 - Nov 2013
I worked in a R&D Plant specialized in water treatment technology using AOP (advanced oxidation processes). My task included the operation of different test rigs and the design of them on a large scale. I also responsible for testing the products of the trials to optimize the operation conditions to obtain the target of the client, Main activities and responsibilities: - Operation and building test rings and pilot plant in the Water Treatment using AOP technology: o Catalytic Wet Air Oxidation Plant, o UV-Ozone Plant and o Ceramic High Membrane Microfiltration Plant. - Chemical analysis, e.g.: Chemical Oxygen Demand (COD) with Hach Method, precipitations, titrations, Gas Chromatography analysis... - Input into design documents including, operating manual, proposals, reports ... - Production of process design documentation including mass and heat balance, PFD’s, P&IDs, process description, schedules, datasheets, utility consumption,... - Experience with HAZOP and Risk Assessment - Experience in working abroad, e.g.: Siemens Energy (WI, US)
-
-
-
INERCO
-
Spain
-
Engineering Services
-
300 - 400 Employee
-
Process Engineer
-
Apr 2011 - Mar 2012
In this role, I was responsible for sizing of equipment, lines and relief valves, completing equipment data sheets. Developing the material heat balances and writing descriptions of operation, control narratives and operating manuals and technical support on various projects for Petrochemical companies, i.e. UBE Corporation, Repsol Refinery/Petrochemical... Main activities and responsibilities: - Experience in optimization and revamping of existing process: Equipment sizing, Hydraulic calculation, Pump and Control valve sizing - Undertaking detailed CAPEX modeling. - Ensure equipment design, manufacturing, and installation complies with relevant safety standards and regulations - Negotiate, co-ordinate and control suppliers to optimize technology, operational performance and minimize cost and develop a supply chain, which provides the most effective solution I fully participated in the design and purchase-procurement of the equipment for a new plant of PCD (Polycarbonate Diol). The production capacity of this new plant was of 3,000-ton p.a. I also was responsible for the design of 6,000 m3 of Cyclohexanone and 6,000 m3 of Acid sulphuric storage and its fire protection system for the new plant of PCD.
-
-
-
Pontificia Universidad Católica de Chile
-
Higher Education
-
700 & Above Employee
-
Researcher
-
Mar 2010 - Sep 2010
As R&D Engineer my responsibility was the design and the optimization of an air flat photobioreactor to study the productivity of H. Pluvialis microalgae. This type of microalgae is used as biomass to obtain biodiesel. I carried out a series of experimental design to establish the best hydrodynamic performance model for three different volumes of air flat photobioreactors. My research work, “ Hydrodynamic characterization and scale-up of flat air lift photobioreactor (PBR) for cultivation of Haematococcus Pluvialis”, involved a series of trials designed to evaluate the mixing time (tm), the hold up (ε), the mass transfer coefficient (kLa) as a function of the superficial gas velocity (UG). The trials were performed in both a two-phase system (tap water and atmospheric air) and three phase system (air, culture medium and cells). The hydrodynamic characteristics were evaluated using a combination of the following conditions: types of the diffuser (rigid and flexible), an average of bubble size and for a gas flow rate. Several analysis were carried in different reactor volumes. I also evaluated the possibility of growing the microalgae Haematococcus Pluvialis CONC – 023 in this type of bioreactor The efficiency of the microalgae growth was tested as per bioreactor geometry: the relation between the downcomer-to-riser cross-sectional area ratio (Ad/Ar) and the system volume (as per length of the weir). Due to the promising results I achieved the university continued the research and eventually scaled up to a 200-liter volume reactor.
-
-
-
LRGP I Laboratoire Réactions et Génie des Procédés
-
France
-
Chemical Manufacturing
-
1 - 100 Employee
-
Researcher
-
Sep 2008 - Sep 2009
In 2008-2009 I also obtained a Postgraduate on Génie des Procédés in ENSIC-INPL (Nancy, France), one of the seven best engineering schools in France. My research was about ionic liquids as green solvents for the petrochemical industry. As a result I was part of the following article published: “Study of Ether, Alcohol or Cyano Functionalized Ionic Liquids Using Inverse Gas Chromatography”, submitted to theJournal of Chemical and Engineering Data in 2010. In 2008-2009 I also obtained a Postgraduate on Génie des Procédés in ENSIC-INPL (Nancy, France), one of the seven best engineering schools in France. My research was about ionic liquids as green solvents for the petrochemical industry. As a result I was part of the following article published: “Study of Ether, Alcohol or Cyano Functionalized Ionic Liquids Using Inverse Gas Chromatography”, submitted to theJournal of Chemical and Engineering Data in 2010.
-
-
-
Cray Valley Iberica (TOTAL)
-
Miranda de Ebro, Burgos
-
Process Engineer
-
Mar 2007 - Nov 2007
As Process Graduate, I worked for the Project Department given assistance for four different projects as a result of an increment of production capacity. The company, a petrochemical plant of epoxy resins and unsaturated polyesters, increased its productivity up to 40,000 tons p.a. I was responsible for sizing of equipment, lines, completing equipment data sheets and writing descriptions of operation. Developing P&IDs and PFDs. Projects include: • Regenerated Thermal-Oxidizer system • Centralized Vacuum system • Sub-Cooled water system • Optimization of the Distillation Unit • Optimization of Water Treatment system I was responsible for the design of a COV treatment unit to comply with the Directive 1999/13/EC the limitation of emissions of volatile organic compounds due to the use of organic solvent in certain activities and installations. I collected samples of the vent points on the site and I analyzed them to define the heat and mass balance and the process flow diagram. I researched the best process technology for the company and I contacted different suppliers. I designed a Regenerated Thermal-Oxidizer system with a capacity of 8,000Nm3/h. The total cost of the project was 0.5M€.
-
-
Education
-
Universitat Rovira i Virgili
Master Engineering degree (M.Eng), Chemical and Process Engineering -
Rochester Institute of Technology
Master's degree, Project Management -
ENSIC
Master of Engineering (M.Eng.), Mechanic, Energy, Processes and Products -
Universidad del País Vasco/Euskal Herriko Unibertsitatea
Bachelor of Engineering (B.Eng.), Industrial Engineering, specialized in Chemist Industries
Community
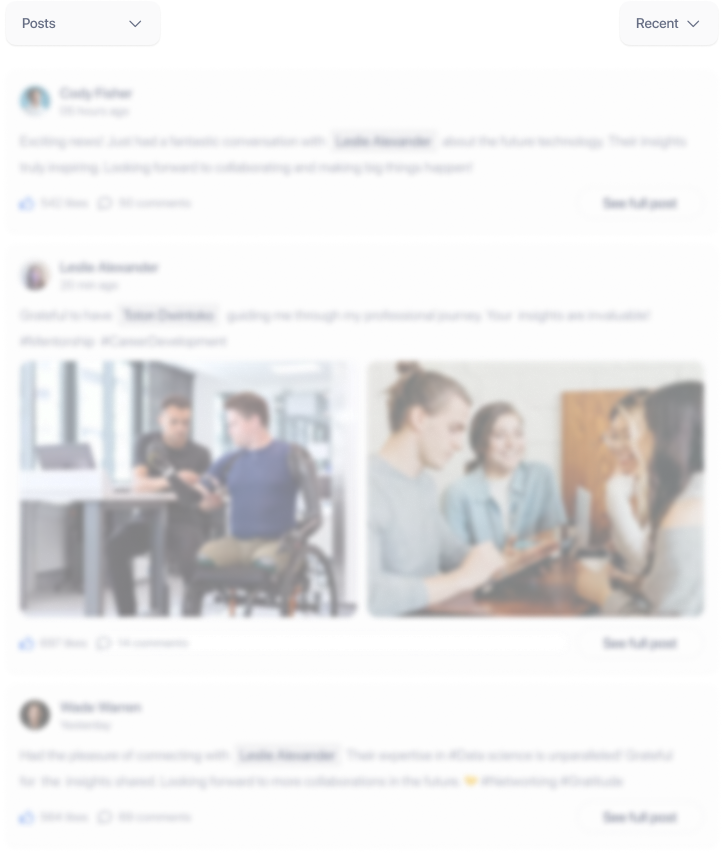