Mariel Urbina
Customer Service Representative at Packaging Solutions and Logistics- Claim this Profile
Click to upgrade to our gold package
for the full feature experience.
Topline Score
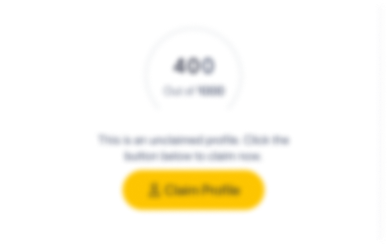
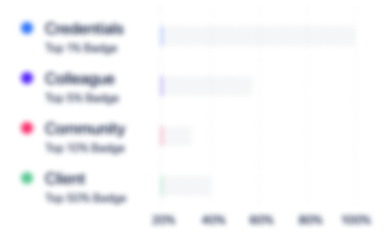
Bio


Experience
-
Packaging Solutions and Logistics
-
United States
-
Packaging and Containers Manufacturing
-
1 - 100 Employee
-
Customer Service Representative
-
May 2018 - Present
• Support to the quality department in the follow-up of customer complaints and quality problems. • Direct customer contact with special attention to their requirements at all levels. • Analysis and planning of material requirements (MRP’s), receipt and monitoring of purchase orders. • Quotation and development of PPAP (Production Part Approval Process) for the introduction of products and engineering changes. • Direct contact with suppliers. Achievements: • Reduction of excess inventory and prevention of late arrivals to the client, through daily analysis and monitoring
-
-
-
ZF Group
-
Germany
-
Motor Vehicle Manufacturing
-
700 & Above Employee
-
Customer Quality Assistant
-
Feb 2017 - May 2018
• Responsible for the coordination and follow-up of customer complaints: FORD, GM, FCA, AUDI and VW).• Management of customer service portals for the registration and monitoring of customer returns.• Verification of corrective actions implemented.• Receipt of invoices and monitoring payments from customers and / or suppliers.• Communicate reports of department's performance at management level: daily review of Scorecards, PPMs, customer deductions, costs and lots inspection status and 8D of all customersAchievements:• Directed the responses for 0km rejections and warranties of FORD, working with the departments involved to define the problem, identification of the root cause, and ensuring the implementation of corrective actions with the support of the tools: 8D, FMEA, Fishbone, 5 WHYS. The result was 90% of responses on time, avoiding costs for customer returns and maintaining the metrics in our Scorecard to maintain the Q1 certification.• Implement a Paynter Chart tool to track customer rejections and have the visibility of all rejects by customer, line, type of reject, status, etc. The result was an efficient system to complete responses to 95% of customer complaints, without exceeding the deadline.• Strengthen the budget control of the department, following up on expenses for lots inspection activities, customer rejects, rework and ensuring not exceeding the budget.
-
-
Customer Quality Intern
-
Mar 2015 - Feb 2018
• Chrysler and Ford warranty coordination and monitoring.• Responsible for auditing corrective and preventive actions.• Support in the use of 8D tools, FMEA, Pareto diagrams, Fishbone, 5Whys for root cause analysis of customer complaints.
-
-
Education
-
Universidad Autónoma de Tamaulipas
Environmental Health Safety Engineer
Community
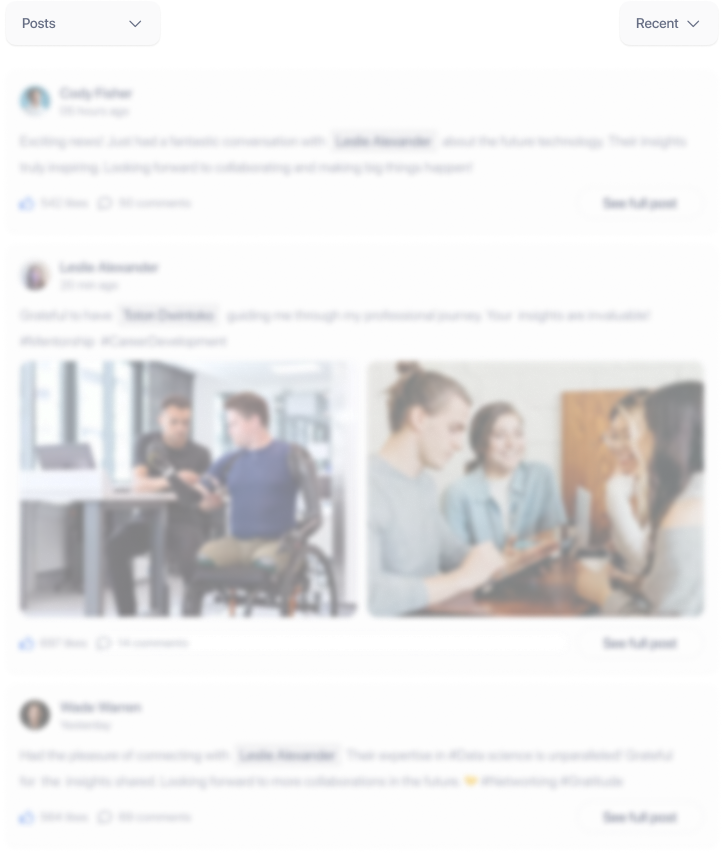