Maria Emilia Hurtado
Supplier Quality Manager at Vericor Power Systems LLC- Claim this Profile
Click to upgrade to our gold package
for the full feature experience.
Topline Score
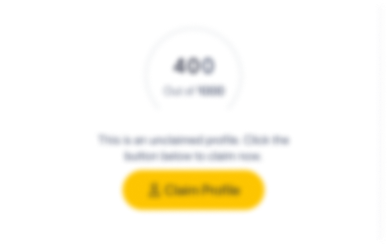
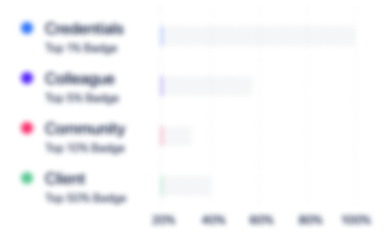
Bio

Eric Simon
I have been extremely lucky to have Emilia on my Quality team. Emilia is a driven and self-motivated Quality Engineering professional with disciplined, analytical technical skills and a Project Management approach to addressing risks and opportunities. Data driven, with a mindset of owning a given process, product, or business concern, her role model behavior energizes others around her to focus more on problem avoidance and less

Hector Cazares
Emilia is a very professional and emotive engineer in her job!. Able to plan and meet dates and always with that good enthusiasm that makes her unique. Excellent skills in drawing interpretation and carrying customer requirements to all levels in the organization she works for.

Eric Simon
I have been extremely lucky to have Emilia on my Quality team. Emilia is a driven and self-motivated Quality Engineering professional with disciplined, analytical technical skills and a Project Management approach to addressing risks and opportunities. Data driven, with a mindset of owning a given process, product, or business concern, her role model behavior energizes others around her to focus more on problem avoidance and less

Hector Cazares
Emilia is a very professional and emotive engineer in her job!. Able to plan and meet dates and always with that good enthusiasm that makes her unique. Excellent skills in drawing interpretation and carrying customer requirements to all levels in the organization she works for.

Eric Simon
I have been extremely lucky to have Emilia on my Quality team. Emilia is a driven and self-motivated Quality Engineering professional with disciplined, analytical technical skills and a Project Management approach to addressing risks and opportunities. Data driven, with a mindset of owning a given process, product, or business concern, her role model behavior energizes others around her to focus more on problem avoidance and less

Hector Cazares
Emilia is a very professional and emotive engineer in her job!. Able to plan and meet dates and always with that good enthusiasm that makes her unique. Excellent skills in drawing interpretation and carrying customer requirements to all levels in the organization she works for.

Eric Simon
I have been extremely lucky to have Emilia on my Quality team. Emilia is a driven and self-motivated Quality Engineering professional with disciplined, analytical technical skills and a Project Management approach to addressing risks and opportunities. Data driven, with a mindset of owning a given process, product, or business concern, her role model behavior energizes others around her to focus more on problem avoidance and less

Hector Cazares
Emilia is a very professional and emotive engineer in her job!. Able to plan and meet dates and always with that good enthusiasm that makes her unique. Excellent skills in drawing interpretation and carrying customer requirements to all levels in the organization she works for.

Experience
-
Vericor Power Systems LLC
-
United States
-
Machinery Manufacturing
-
1 - 100 Employee
-
Supplier Quality Manager
-
Sep 2021 - Present
-
-
-
Hussmann
-
United States
-
Retail Groceries
-
700 & Above Employee
-
Sr. Supplier Quality Engineer
-
Jun 2014 - Aug 2021
• Monitor and track the corrective/preventive action system for all suppliers, driving them to identify solid root cause analysis and establish corrective actions using solving problem tools (8D’s, 5Whys, A3, Fishbone) Issue SCAR’s in the system. Work directly with sourcing manager to manage new suppliers certifications and/or approvals using Supplier Quality Manual tools using the PPAP elements Responsible to maintain and keep MRB, work with purchasing to obtain RMA’s as part of Score Cards Constantly reviewing supplier Score Cards (Supplier KPI’s, PPM, on-time delivery, late supplier 8D responses) and working directly with corporative on critical Supplier evaluation needs by performing on site supplier audits. Lead problem-solving activities as required for customer related with vendors. Coordination of cross functional teams such a Design engineering/manufacturing/supply chain/quality to resolve vendor issues on the manufacturing floor. Work with New Product Development (NPD) team on APQP activities that include suppliers and quality assurance on all the product phases. Actively working with corporate quality measurements providing data analysis for improvement from stablished processes such a VOC, COPQ, LPA’s, QMS. Develop processes on manufacturing lines that include proper handle of material to eliminate waste, increase product quality, productivity and cost using tools such a as Six Sigma, statistical process control, value analysis, FMEA, and lean. Continuous improvement activities. Change Management Coordinator: Review and address risk of proposed changes affecting the factory manufacturing areas. Responsible to provide quality documentation to comply with NOM for products ship to Mexico Train new personnel in the quality system and ISO requirements. Perform and schedule internal ISO audits in order to meet the established schedule. ISO 9001:2015 Lead Auditor, responsible for QMS. Show less
-
-
-
ElringKlinger
-
Germany
-
Motor Vehicle Manufacturing
-
700 & Above Employee
-
Quality Engineer
-
Jan 2013 - Jul 2014
Handle customer complaints using problem solving techniques 8Ds, 5 whys , fishbone deep drill. Maintain customers websites Covisint. PPAP coordinator for new products and current process changes. Experience with Ford, Chrysler, GM, Hyundai. Etc. On charge of Gages calibration and or certification. Review and approve supplier’s PPAP and or corrective actions. Coordinate on site audits. Internal ISOTS 16949 auditor. Responsible of supervise Early Launch Containment documentation and activities such a tally sheets, clean points with customer and review containment exit criteria. Show less
-
-
-
Parkway Products, LLC
-
United States
-
Plastics Manufacturing
-
100 - 200 Employee
-
Quality Engineer
-
Aug 2011 - Dec 2012
-
-
-
Nifco America Corp.
-
United States
-
Motor Vehicle Manufacturing
-
300 - 400 Employee
-
Quality Manager
-
Jul 2008 - Dec 2009
Responsible to lead quality engineers activities, customer service QE, engineers for QA, ISO9000 coordinator, calibration and training department. Handle customer claim and visit & audit, track customer quality issue and complain, coordinate engineers to submit 8D /5Why to customers. Follow up corporate's rule to manage RMA and keep its levels between monthly goals Work with engineering and lead QA team to support miscellaneous: package's transfer / qualification / production ramp-up healthily to meeting business introduction requirement. Lead QA team to achieves high quality and low PPM. Review and be part of the sign off APQP phases and deliverables, and new or changes introduced to ensure build-in quality of all products/packages. Experience in Design and process FMEA's, Process controls, Capability and process analysis OEE and part approval PPAP. Able to coordinate the maintenance of QS9000 and manage the system to move towards ISOTS16949 and Ford Q1 standards as well as QSB audits from GM. Perform customer satisfaction survey (External/internal), investigate the root cause if the objectives are not achieved and find method to overcome the problem. Experience working with Honda, Nissan, Ford, GM, BMW systems and quality requirements. Show less
-
-
-
-
Senior Program Engineer
-
Jan 2002 - Jan 2008
Jan. 2008 Lead activities during a new product launch to meet timeline, quality and financial goals at the Manufacturing Plant.Control program budget according to goals and requirements.Lead prototype and process validation builds at the manufacturing plant and develop feasibility reports.Review/Develop DFMEAs and Develop/Maintain PFMEAs. Establish actions to reduce potential failure modes.Coordination, review and support DVP&Rs and PVP&Rs testing for new products validationInitiate corrective actions when problems which impact quality are identified.Preparation of VAVE (Value Analysis and Value Engineering) projects for product and process. Product and Process capability analysis. Support to sales department on the quotation process for new programs or Eng. Changes.Develop/Maintain Control Plans, Process Flows, Layouts, Manufacturing Instructions and Key characteristics matrix for the new products and Eng. Changes.Responsible to release and control the BOM of the new products in the company system.Lead on the equipment/machine tools acquisition including purchasing process, validation at the suppliers in Poland, USA, Canada and Mexico; training and production assistance in the products launch phase. Show less
-
-
Quality Engineer
-
Jan 2001 - Jan 2002
Use of statistical techniques for customer to support special product characteristicsAssist in the qualification of new equipment for new products by doing audits, calculation of Cpk, PPk and line certification.Drawing analysis, PSW, Process Audits , Control Plan & Special Characteristics matrix documents provided to the team for PPAP documentation.
-
-
-
-
Engineering Coordinator
-
Jun 1997 - Jan 2000
Lead engineering teams to meet flawless launch goals for laundry products harness. Ensure efficiency at the lines working with the engineers to provide metrics and tools for productivity. Plan for supplier support of new program ramp up plans Customer contact as required to support program information needs. Served as liaison between system users and technical support group. Lead engineering teams to meet flawless launch goals for laundry products harness. Ensure efficiency at the lines working with the engineers to provide metrics and tools for productivity. Plan for supplier support of new program ramp up plans Customer contact as required to support program information needs. Served as liaison between system users and technical support group.
-
-
-
-
Resident Engineer
-
Jun 1996 - Jun 1997
Resident in the USA in Iowa State, in the company FRIGIDAIRE LAUNDRY PRODUCTS (Electrocomponente´s customer) solving quality and shipment Plan for supplier support of new program ramp up plans. Contact with customer service for issues related with delivery. Active participation for new programs while been design over the facility. Supervision of line auditors to ensure QC for the products and report to top management monthly results. Resident in the USA in Iowa State, in the company FRIGIDAIRE LAUNDRY PRODUCTS (Electrocomponente´s customer) solving quality and shipment Plan for supplier support of new program ramp up plans. Contact with customer service for issues related with delivery. Active participation for new programs while been design over the facility. Supervision of line auditors to ensure QC for the products and report to top management monthly results.
-
-
Education
-
INSTITUTO TECNOLOGICO DE CHIHUAHUA, MEX
Bachelor of Science, Electrical Industrial Engineering
Community
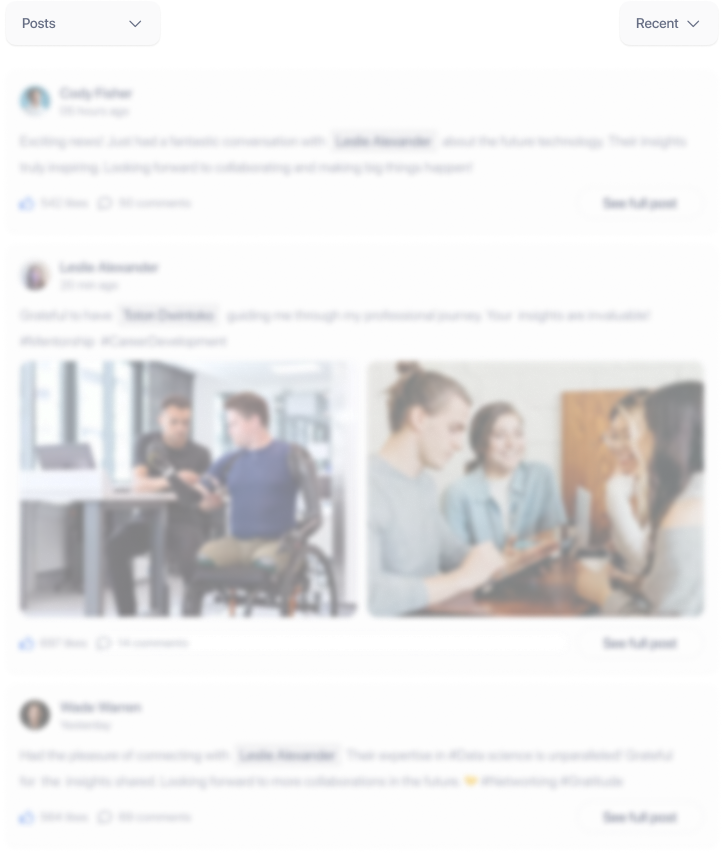