Maria Aparecida Araújo (Lila), PRINCE2
Global Manufacturing Systems Deployment Lead - Associate Director at Takeda in Deutschland- Claim this Profile
Click to upgrade to our gold package
for the full feature experience.
-
English -
-
Spanish -
Topline Score
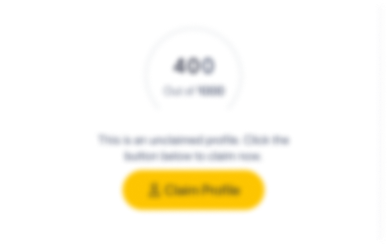
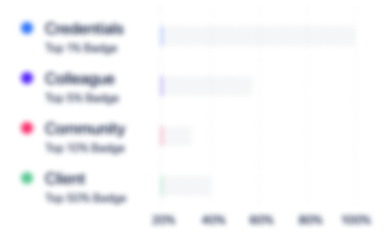
Bio

Daniela Silva
Trabalhar com Lila é algo excepcional e maravilhoso. Ela foi minha mestre e minha professora em Qualificação. Lila é uma profisional dedicada, criteriosa, brava e engajada nos projetos no qual se envolve e vai até o fim. Se cheguei onde estou devo muito a ela..É uma excelente profissional, além de ser uma grande amiga.

Daniela Silva
Trabalhar com Lila é algo excepcional e maravilhoso. Ela foi minha mestre e minha professora em Qualificação. Lila é uma profisional dedicada, criteriosa, brava e engajada nos projetos no qual se envolve e vai até o fim. Se cheguei onde estou devo muito a ela..É uma excelente profissional, além de ser uma grande amiga.

Daniela Silva
Trabalhar com Lila é algo excepcional e maravilhoso. Ela foi minha mestre e minha professora em Qualificação. Lila é uma profisional dedicada, criteriosa, brava e engajada nos projetos no qual se envolve e vai até o fim. Se cheguei onde estou devo muito a ela..É uma excelente profissional, além de ser uma grande amiga.

Daniela Silva
Trabalhar com Lila é algo excepcional e maravilhoso. Ela foi minha mestre e minha professora em Qualificação. Lila é uma profisional dedicada, criteriosa, brava e engajada nos projetos no qual se envolve e vai até o fim. Se cheguei onde estou devo muito a ela..É uma excelente profissional, além de ser uma grande amiga.

Experience
-
Takeda in Deutschland
-
Germany
-
Pharmaceutical Manufacturing
-
300 - 400 Employee
-
Global Manufacturing Systems Deployment Lead - Associate Director
-
Jun 2021 - Present
-
-
-
Takeda GmbH
-
Austria
-
Pharmaceutical Manufacturing
-
1 - 100 Employee
-
Global Manufacturing Systems Deployment Lead
-
Jan 2020 - Jun 2021
-
-
-
-
Global Project Manager - Internal sites lead
-
Nov 2016 - Jan 2020
Manage all aspects for implementation of Track&Trace system on the sites according to Program Strategy.Maintain process to ensure Project management documentation, reports and plans are relevant, accurate and complete, including update the schedule, take minutes, track issues and action items, produce reports, follow-up open issues and other similar tasks.Empower sites Project managers that relevant activities, deliverables and milestones are defined, implemented and monitored. Support site project managers to develop detail scope of each line and develop overall resources and activity plan in cooperation with vendors. Ensure & validate that site PMs maintain detailed project plan for all project initiativesEstablishing a new role for overall global serialization coordination and a local super-user and coordinator for trouble shootingProvide assistance to maintain and update the project management framework and disciplines necessary to support the Serialization Global program lead.Assist and advise leaders, managers and team to the best use of project management disciplines and approaches with a fast-paced, high tech environment.
-
-
Project Coordinator
-
Aug 2014 - Oct 2016
Responsible for portfolio management of CAPEX engineering projects.Project Manager of Serialization T&& project.
-
-
-
Novartis
-
Switzerland
-
Pharmaceutical Manufacturing
-
700 & Above Employee
-
Technology Transfer Project Manager
-
Oct 2013 - May 2014
Management of Technology Transfer Project of Meningococical C Vaccine from Novartis to FUNED (Minas Gerais Government Institute). Management of Technology Transfer Project of Meningococical C Vaccine from Novartis to FUNED (Minas Gerais Government Institute).
-
-
-
-
Project Manager
-
2011 - Jul 2013
Management of Conceptual Design, Basic Design and planning of the Construction, Installation, Commissioning, Qualification and Handover of upgrade project for fermentation of a production plant for NN in Montes Claros – MG.Responsible for Conceptual Design and Basic Design of a Warehouse in NN Araucaria - PR.Key person on Brazil responsible for standardization of procedures related to project management in NP Brazil and to establish NP operations in Brazil.Support on preparation of technical and commercial proposals.Responsible for implementation of Quality Management System.
-
-
-
Kop do Brasil
-
Brazil
-
Pharmaceutical Manufacturing
-
1 - 100 Employee
-
Project Manager
-
2007 - Nov 2011
FURP Management of commissioning, training, technical documentation, startup, IQ and OQ of complete pharmaceutical systems for solids and sterile: granulation; drying; micronization; blending; washing and drying systems for bins; tablet press; tablet coating; blister machine; automatic system for manipulation/filtration/CIP of sterile; laminar flows and pass through; autoclaves; washing/sterilization/depyrogenation of components/filling/stoppering of sterile; ampoules review; purified water; water for injection; clean steam; cold storage; sampling and weighing systems. Verification of user requirement specification compliance and report elaboration in order to obtain the final system acceptance term regarding financial issues.Interface management between manufacturer and customer in order to obtain the executive project for the installation of the above systems.FAT execution of foreign equipment: product handling and transportation systems with bins, lifting, washing and drying equipment.Avon CosmeticsDefinition of the company validation structure, elaboration of validation master plan, elaboration of validation procedures and performance of training to employees.Process mapping, critical analysis, procedure elaboration and training in Change Control Management.Process mapping, procedure elaboration and training in User Requirements Specification and Risk Analysis.Cases execution of User Requirement Specification and Risk Analysis for weighing system, auxiliary containers, votator, powder area, weighing area, case packers, flexible line, dedicated line for brightness rollete, hot fill line, cream and plastics lines, mobile vessels, cream and liquid manipulation, roll on line, checkweighers, crimping line and purified water.
-
-
-
Eurofarma
-
Pharmaceutical Manufacturing
-
700 & Above Employee
-
Project Coordinator
-
2006 - 2007
Responsible for interfaces coordination across departments in order to have the startup of the first building of the Industrial Complex in Itapevi for medicines production (Solids, Liquids, Creams and Sterile). The pharmaceutical processes involved were: weighing; drying; micronization; blending; tableting; automatic system for manipulation/filtration/CIP of sterile; automatic system for manipulation/CIP/transferring of liquids and creams; laminar flows and pass through; autoclaves; washing/sterilization/filling/stoppering of sterile; ampoules review; secondary and primary packaging; purified water; water for injection; pure steam; process air; computerized systems and HVAC.Identification of the needs for the plant startup, such as: construction; installation; commissioning; systems and equipment qualification; process adaptation; process validation, cleaning validation and methods validation.Preparation of time schedule for the factory startup and follow-up on it.Technical support for validation, quality assurance and quality control departments related to the cGMP prerequisites for the factory startup and preparation for the audits.Coordination of validation activities performed by subcontractors.Preparation and presentation of project status for the project time, the process owners and the board.
-
-
-
Novo Nordisk
-
Denmark
-
Pharmaceutical Manufacturing
-
700 & Above Employee
-
Project Quality Manager/Validation Specialist
-
2004 - 2006
Validation Specialist, responsible for promotion of the compliance and harmonization process of Montes Claros site through pursuing proper and balanced quality in all Validation Pharmaceutical Process to related business activities. The activities were related to a factory for Insulin production and the pharmaceutical processes involved were: API; weighting; automatic system for manipulation/filtration/CIP/ZIP of sterile; laminar flows and pass troughs; autoclaves; washing/sterilization/filling/stoppering of sterile; secondary packaging; purified water; water for injection; pure steam; process air; cleanrooms; HVAC; computerized systems, etc.Black Belt, responsible for managing Lean Six Sigma Projects related to optimization in Quality Assurance Processes in Novo Nordisk.Responsible for the Validation Committee.Quality Manager, responsible for the Quality department during the construction of new plant built in Montes Claros. Having as main tasks the implementation and management of all Validation, Factory Acceptance Tests, Commissioning and Quality activities for the following systems, where applicable: cleanrooms; HVAC; BMS; access control; FMS; compressed air; cold storage; cold water; hot water; chilled water; steam; potable water; electrical systems; effluents treatment. Including the responsibility for the budget, KPI’s and the resources to perform these activities.International experience with validation strategies and project definition. Including part time developing project activities at NN Headquarter in Denmark.Support to national and international audits for GMP certification.Member of the failure investigation committee.
-
-
-
Altana Pharma
-
Pharmaceutical Manufacturing
-
1 - 100 Employee
-
Validation Supervisor
-
1998 - 2004
Responsible for the Qualification Department. The activities were related to a factory for Solids, Liquids and Creams production and the pharmaceutical processes involved were: weighing; blending; granulation; drying by fluidized bed; drying by microwave; tablet press; tablet coating; blister machine; encapsulation; automatic system for manipulation and transference of liquids and creams; primary and secondary packaging of solids, liquids and creams; purified water; process air; nitrogen; HVAC; automatic warehouse system and quality control equipment.Implementation of Computer System Validation working structure, having the integration among the Information Technology department and the System Users departments, training and management of all projects related to the Computer System Validation as the main responsibilities.Support to national and international audits for GMP certification.Implementation of process equipment, systems and cleanrooms qualification structure to qualify the new plant built in Jaguariúna, including the coordination of a group to perform these activities. All productive equipment, HVAC systems, cleanrooms, purified water, nitrogen and process air systems were qualified.Coordination of Equipment and Systems Qualification performed by subcontractors during the construction phase.Execution of Factory Acceptance Tests (FAT) of national and foreign equipment: blister line, liquids and drops filling line and autoclave.Startup of new production lines: blister line and liquids and drops filling line.Implementation of the plant Instrument Calibration Management System, including instrument Tag numbering system and calibration of all critical instruments.Responsible for the budget, KPI’s and the resources to perform all calibration and qualification.Responsible for Engineering Technical File.Participation in the implementation of SAP Maintenance Module.Member of the failure investigation committee.
-
-
Education
-
Ohio University
Master of Business Administration (MBA) -
Fundação Getulio Vargas
Master of Business Administration (MBA), Project Management -
Universidade de São Paulo
Post degree, Business Administration and Management, General -
Faculdades Oswaldo Cruz
Bachelor of Engineering (BEng), Engineering Chemistry
Community
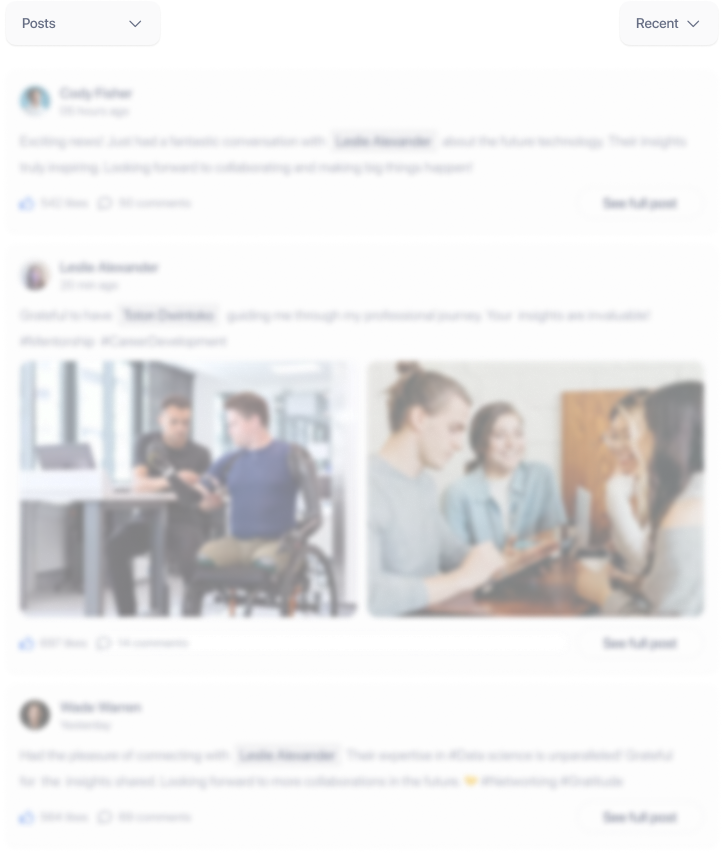