Marcos Mora
VP of Operational Excellence at MN8 Energy- Claim this Profile
Click to upgrade to our gold package
for the full feature experience.
-
Spanish Native or bilingual proficiency
Topline Score
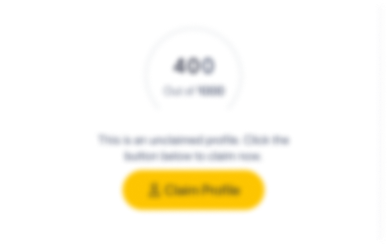
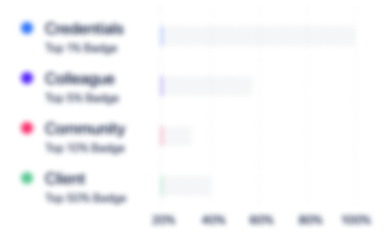
Bio

Barry Brock
I worked with Marcos on the Volt Launch at the GM Hamtramck Plant. Marcos was the go-to guy on the Volt Launch. Marcos used his motivation and technical skills to help make the Volt launch successful. Marcos built relationships along with building quality into each car. He was a key leader of the launch. Marcos was well liked at GM and has major accomplishments here. He made things happen.

Barry Brock
I worked with Marcos on the Volt Launch at the GM Hamtramck Plant. Marcos was the go-to guy on the Volt Launch. Marcos used his motivation and technical skills to help make the Volt launch successful. Marcos built relationships along with building quality into each car. He was a key leader of the launch. Marcos was well liked at GM and has major accomplishments here. He made things happen.

Barry Brock
I worked with Marcos on the Volt Launch at the GM Hamtramck Plant. Marcos was the go-to guy on the Volt Launch. Marcos used his motivation and technical skills to help make the Volt launch successful. Marcos built relationships along with building quality into each car. He was a key leader of the launch. Marcos was well liked at GM and has major accomplishments here. He made things happen.

Barry Brock
I worked with Marcos on the Volt Launch at the GM Hamtramck Plant. Marcos was the go-to guy on the Volt Launch. Marcos used his motivation and technical skills to help make the Volt launch successful. Marcos built relationships along with building quality into each car. He was a key leader of the launch. Marcos was well liked at GM and has major accomplishments here. He made things happen.

Credentials
-
Project Management Professional
Project Management InstituteDec, 2015- Nov, 2024 -
Change Leader
ignitemJun, 2015- Nov, 2024 -
Six Sigma Black Belt
ASQ -
Six Sigma Master Black Belt
Florida Power & Light
Experience
-
MN8 Energy
-
Spain
-
Renewable Energy Semiconductor Manufacturing
-
100 - 200 Employee
-
VP of Operational Excellence
-
Apr 2023 - Present
-
-
-
NextEra Energy, Inc.
-
United States
-
Utilities
-
700 & Above Employee
-
Executive Director of Development
-
Jul 2020 - Apr 2023
-
-
Director of Development
-
Jun 2018 - Jul 2020
-
-
Manager, Corporate Operational Excellence
-
Apr 2013 - Jun 2018
- Lead Strategic, Multi-Business Unit Quality projects aimed at improving company-wide operational performance. - Lead Quality Deployment initiatives to drive and sustain a continuous improvement culture across the organization. - Increase organizational capabilities in the areas of Lean, Six Sigma, Analytical Problem Solving and Process Management via ongoing project execution, support, mentoring and training.
-
-
Lead Quality & Process Project Manager
-
2010 - Apr 2013
- Lead Quality Deployment initiatives to drive and sustain continuous improvement across the organization. - Increase organizational capabilities in the areas of Lean, Six Sigma, Analytical Problem Solving and Process Management via ongoing project execution, support, mentoring and training.
-
-
-
General Motors
-
United States
-
Motor Vehicle Manufacturing
-
700 & Above Employee
-
Sr. Manufacturing Project Engineer
-
2004 - 2010
- Lead cross-functional team activities to achieve the flawless launch of a new vehicle program. - Development of General Assembly Launch plans and implementation in production. - Facilitate integration and issue resolution process between different departments, cross-functional teams and assembly plant; often reconciling conflicting objectives from different areas. - Documentation of issues and driving timely resolution. - Tracking of Manufacturing Investment while identifying and… Show more - Lead cross-functional team activities to achieve the flawless launch of a new vehicle program. - Development of General Assembly Launch plans and implementation in production. - Facilitate integration and issue resolution process between different departments, cross-functional teams and assembly plant; often reconciling conflicting objectives from different areas. - Documentation of issues and driving timely resolution. - Tracking of Manufacturing Investment while identifying and pursuing cost reduction potentials to ensure successful project execution (on time and on budget).
-
-
Sr. Manufacturing Engineer
-
2000 - 2004
- Multi-plant, multi-program technical support for manufacturing processes and assembly verification equipment and software. - Liaison between manufacturing plants and product development teams. - Analysis of Product Design Changes and impact to manufacturing process and cost. - Definition of Bill of Process (BOP) and Manufacturing requirements. - Validation of Test Software and Equipment prior to installation at manufacturing facilities. - Development and roll-out of Lean… Show more - Multi-plant, multi-program technical support for manufacturing processes and assembly verification equipment and software. - Liaison between manufacturing plants and product development teams. - Analysis of Product Design Changes and impact to manufacturing process and cost. - Definition of Bill of Process (BOP) and Manufacturing requirements. - Validation of Test Software and Equipment prior to installation at manufacturing facilities. - Development and roll-out of Lean thinking initiatives within a global organization.
-
-
-
-
Sr. Quality Engineer
-
1998 - 2000
- Leadership experience – directly supervised a team of Quality Auditors. - Troubleshooting and Problem Analysis, Continuous Improvement and leading Task Force Teams to drive issue resolution upstream in the process (Build In-Station Quality). - Implementation of Quality driven culture and initiatives in the manufacturing process to ensure meeting quality objectives during regular operations and sustain them during the introduction of new vehicle models to the assembly plant process.
-
-
Production Supervisor
-
1997 - 1998
- Successfully Leading and motivating teams to achieve departmental and organizational goals (Safety, Quality and Throughput). - Leadership Experience: directly supervised teams in a workers union environment. - Achievement of Safety, Quality, Throughput and other departmental goals. - Expertise with personnel training on Industrial Safety, Lean Manufacturing, Self-Inspection and Quality principles and requirements. Also definition, documentation, implementation and follow-up of Best… Show more - Successfully Leading and motivating teams to achieve departmental and organizational goals (Safety, Quality and Throughput). - Leadership Experience: directly supervised teams in a workers union environment. - Achievement of Safety, Quality, Throughput and other departmental goals. - Expertise with personnel training on Industrial Safety, Lean Manufacturing, Self-Inspection and Quality principles and requirements. Also definition, documentation, implementation and follow-up of Best Practices for these areas. - Needs Detection and Resource Distribution in a Production Facility. - Sense of Urgency and Decision-Making. - Optimization of cycle-time, manpower and equipment utilization. - Tooling, Equipment and Machinery Vendor/Supplier interface and inspection/buy-off. - Experience with Assembly Plant Processes and Culture – Electrical/Mechanical components & systems.
-
-
Education
-
Indiana University - Kelley School of Business
Master's, Strategic Management -
Universidad de Carabobo
Bachelor's, Industrial Engineering
Community
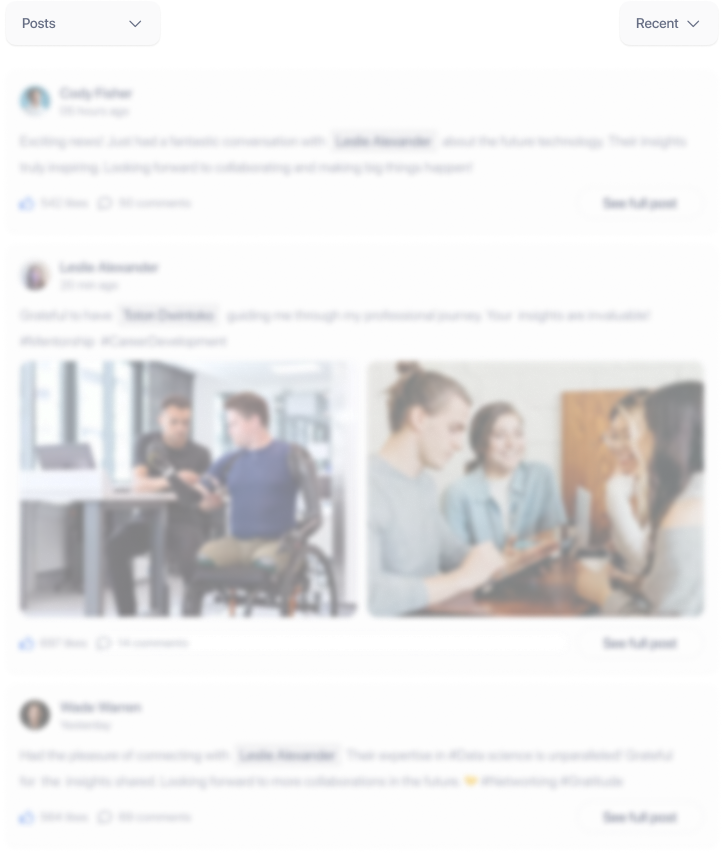