Marco Quintana
Plant manager at Vitromex S.A de C.V.- Claim this Profile
Click to upgrade to our gold package
for the full feature experience.
-
English Full professional proficiency
-
Spanish Native or bilingual proficiency
Topline Score
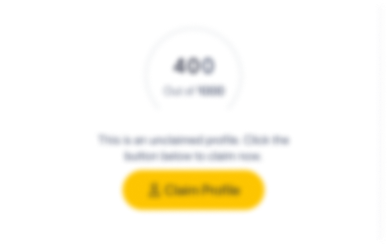
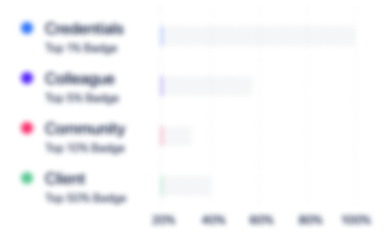
Bio

Sergio Morales Venegas
Marco se ha caratcerizado por un liderazgo nato y disponibilidad para solucionar problemas de una manera objetiva y eficaz. Se ha caracterizado por ser una persona en la que puedes confiar en cualquier situación. Su capacidad para crear un excelente ambiente de trabajo está probada a través de todos los años de llevo laborando con él. Cuenta con una más que probada experiencia en su campo la cual el ha permitido formar a otros líderes y profesionales en la empresa. Me es grato recomendar a Marco por su profesionalismo y ofrecer siempre la mejor actitud a quienes han tenido la oportunidad de aprender siempre algo de él. Sergio M

Sergio Escalante
Marco is a smart and analytic person, he always offer a solution for the issues that you could have and give the 360ª perspective. Always is trying to get the answer for problems, getting the ideas of the team consolidating this information to have the best for the situation. As coworker he offers the support to resolve situations, as boss give a guide to make your job as best as you can.

Sergio Morales Venegas
Marco se ha caratcerizado por un liderazgo nato y disponibilidad para solucionar problemas de una manera objetiva y eficaz. Se ha caracterizado por ser una persona en la que puedes confiar en cualquier situación. Su capacidad para crear un excelente ambiente de trabajo está probada a través de todos los años de llevo laborando con él. Cuenta con una más que probada experiencia en su campo la cual el ha permitido formar a otros líderes y profesionales en la empresa. Me es grato recomendar a Marco por su profesionalismo y ofrecer siempre la mejor actitud a quienes han tenido la oportunidad de aprender siempre algo de él. Sergio M

Sergio Escalante
Marco is a smart and analytic person, he always offer a solution for the issues that you could have and give the 360ª perspective. Always is trying to get the answer for problems, getting the ideas of the team consolidating this information to have the best for the situation. As coworker he offers the support to resolve situations, as boss give a guide to make your job as best as you can.

Sergio Morales Venegas
Marco se ha caratcerizado por un liderazgo nato y disponibilidad para solucionar problemas de una manera objetiva y eficaz. Se ha caracterizado por ser una persona en la que puedes confiar en cualquier situación. Su capacidad para crear un excelente ambiente de trabajo está probada a través de todos los años de llevo laborando con él. Cuenta con una más que probada experiencia en su campo la cual el ha permitido formar a otros líderes y profesionales en la empresa. Me es grato recomendar a Marco por su profesionalismo y ofrecer siempre la mejor actitud a quienes han tenido la oportunidad de aprender siempre algo de él. Sergio M

Sergio Escalante
Marco is a smart and analytic person, he always offer a solution for the issues that you could have and give the 360ª perspective. Always is trying to get the answer for problems, getting the ideas of the team consolidating this information to have the best for the situation. As coworker he offers the support to resolve situations, as boss give a guide to make your job as best as you can.

Sergio Morales Venegas
Marco se ha caratcerizado por un liderazgo nato y disponibilidad para solucionar problemas de una manera objetiva y eficaz. Se ha caracterizado por ser una persona en la que puedes confiar en cualquier situación. Su capacidad para crear un excelente ambiente de trabajo está probada a través de todos los años de llevo laborando con él. Cuenta con una más que probada experiencia en su campo la cual el ha permitido formar a otros líderes y profesionales en la empresa. Me es grato recomendar a Marco por su profesionalismo y ofrecer siempre la mejor actitud a quienes han tenido la oportunidad de aprender siempre algo de él. Sergio M

Sergio Escalante
Marco is a smart and analytic person, he always offer a solution for the issues that you could have and give the 360ª perspective. Always is trying to get the answer for problems, getting the ideas of the team consolidating this information to have the best for the situation. As coworker he offers the support to resolve situations, as boss give a guide to make your job as best as you can.

Credentials
-
Aerospace internal auditor AS9100 D
Bureau Veritas GroupJul, 2017- Oct, 2024 -
wiring, stripping and crimping trainer
Zodiac AerospaceSep, 2008- Oct, 2024
Experience
-
Vitromex S.A de C.V.
-
Glass, Ceramics and Concrete Manufacturing
-
1 - 100 Employee
-
Plant manager
-
Sep 2021 - Present
-
-
-
Safran
-
France
-
Aviation and Aerospace Component Manufacturing
-
700 & Above Employee
-
Senior Program Manager
-
Apr 2019 - Aug 2021
- In charge of the Chihuahua programs department with two programs managers in charge.- Monitoring and controlling all programs of the division for Chihuahua site focus in profitability, improvement, customer satisfaction and costs in manufacture products such as harnesses, conduits, special processes, etc.- To work directly with Sales departments on Quotations, negotiations and contracts review to ensure the success of the programs.- Direct support on new projects, transfers and new business in the company being the link between Sales and operations.- Support all programs with analysis in configuration management, sales, Quality, communication, production and risk management plans.- Negotiations in engineering changes, demand changes and development management to follow up with customers for the non recurring changes, E&O, claims, etc.- Develop the overall plan / schedule based on strategies and objectives defined by the PMO working as a link between the headquarters and Chihuahua site.- Focus in KPI's and results of the company.- Actively Interface with customer during all stages of program transfer, quotation, production rate assessments and program milestone reviews.- Support customer’s onsite visit at the Chihuahua facility as primary contact.- Review contractual requirements and work with sales on the reviews.- Flag changes in internal processes to highlight the commitment and resources needed to sustain the customers’ satisfaction.- Results and objectives presentations to top management and customers in weekly and monthly basis.- Suggest changes where mutually beneficial to the customer and us.• Program management course (PM fundamentals & Leadership essentials) 21 hrs training* SAFRAN PROMPT 16 hrs training.* PMP classroom certification Grey campus* PMP live online training 35 hrs
-
-
Program Manager
-
Apr 2017 - Apr 2019
• Develop the overall plan / schedule based on strategies and objectives defined by the PMO.• Work with engineering, operations, QA, and sales to maintain the status of all deliveries, and manage resource allocation to best match our capabilities with the customers’ expectations• Provide to the PMO and project team with weekly updates, at a minimum, of status vs. plan and vs. changes in customer status and expectations, including functional design, costs, scope, pricing, content, changes, delivery, documentation, and supplier performances.• Actively Interface with customer during all stages of program transfer, quotation, production rate assessments and program milestone reviews.• Support customer’s onsite visit at the Chihuahua facility• Review contractual requirements and identify areas needing special treatment to achieve them.• Flag changes in internal processes to highlight the commitment and resources needed to sustain the customers’ satisfaction.• Suggest changes where mutually beneficial to the customer and us.• Establish a clear understanding of the Statement of Work throughout both the customers’ organization and our internal organization.• Flag changes in the Statement of Work requiring contractual modifications.• Program management course (PM fundamentals & Leadership essentials)• Program Manager supervisor in charge of two program managers.• Supervisor of Inside sales department (4 people) focus in customer demand follow up. • Follow order from placement to delivery. • Verify order for accurate price, parts and quantity. • Determines and keeps records of sales order status, shipping dates, availability and back orders. • Complete and maintains sales order file. • Complete Contract Review form for all orders and quotes and insures the appropriate signatures are received Training:* Personal leadership (dao)* Team leadership (dao)* Project management (Safran university)
-
-
-
Zodiac Aerospace
-
France
-
Aviation and Aerospace Component Manufacturing
-
700 & Above Employee
-
Production Manager
-
Sep 2015 - Mar 2017
The Production Manager at Zodiac Aerospace manufacturing facility will perform the daily operations of the plant to ensure reliability and consistency on the production line including, but not limited to, the following departments such as aerospace harnesses, conduit assemblies, Welding, bending, special processes and surface treatments.This role will manage/lead a team of hourly production employees to meet/exceed production, efficiency, productivity, safety & quality goals while maintaining positive employee relations.
-
-
Product Transfer Manager
-
Sep 2012 - Mar 2016
- Responsible for the product transfer between companies of the same Division and the transition of new products to the company from external customers. Development of the program and product in terms of production, quality, engineering, materials, logistic, costs, headcount and delivery at the first production. - Administration of all the product transfers from Tunisia, England, France, Canada, USA and México.- Completed transfers from different type of processes (welding, bending, harnesses, conduits and special processes.)- Transfers achieved of different customers (UTAS, EATON, HONEYWELL, ZODIAC, etc.)- Identify the potential products to be transfer from different sites, analyzing logistic, costs, savings, risks, etc.- Define scope of work and introduce transfer plan to the management for approval.- Define, prepare and analyse the tooling, layout, training, headcount and raw material involved in the new transfer.- Leader teams from both sites of different departments to accomplish the proper transfer of the product.- Responsible to obtain, manage and provide all the information of the transfer (documentation, purchase orders, bill of materials, engineering documents, etc.)- Identify and complete the layout for the new product.- Ensure the raw material, components and training material for the transfer.- Train the new personnel involved in the transfer (Manufacturing engineer, planner, quality engineer, assemblers, etc.)- Hire the headcount need to accomplish the transfer.- Define the production transition between the two sites Using ramp-up / Ramp-down, ensuring the delivery on time of the product to the customer.Doing business fairly course.
-
-
Senior Manufacturing Engineer
-
Nov 2010 - Sep 2012
- Harness process management in 7 different areas for Boeing, Embraer, Dash 8, Gulfstream, CRJ, Labinal, etc as customers. - Achieving the certification and approval of each customer. Transferring each area in charge from different facilities. - Visual factory implementation, Tools and accessories design to support manufacture operations, Making and/or modifying operation instructions, process flow improvement, changing and updating the plant layouts.- In charge of the train for each operator and supervisor of the different harnesses areas, focus in drawing and document interpretations, wiring knowledge, special process - Aerospace internal auditor.- Production lines support and process engineering department. - Control and maintenance of special equipment and tooling like stripping tools, crimping tools, laser marked, label printers, etc. - Certified trainer for IPC 620, BAC and D6 documentation for different customer requirements.- Implementation of the AS9100 Rev C, Nadcap, DGAC, Boeing certifications.- In charge of implementation and maintenance of the TPM, 5’S, Kaizen, Gemba, VSM, lean, engineering changes, process capacity analysis. - Courses: Aerospace internal auditor, Gemba academy, 5’s. Lean manufacturing, VSM, transfer process expert.
-
-
Manufacturing Engineer
-
Sep 2008 - Nov 2010
- Responsible for production lines KPIs & documentation: Work instructions, Visual Aids and Control Plans- Responsible to attend and follow actions for Internal/External Audits.- In charge of Productivity scrap reduction project. Accountable to Lead the solution of Quality issues.- Internal Auditor for AS 9100, 5's and PDCA - Responsible of create and update documentation like: visual aids, dashboards, work Instructions & travelers-Layout design for new and existing products & Manufacturing leader for Kaizen projects.- Validation of manufacturing tooling & line balancing, - Development of Scrap and efficiency projects focus.- Root causes analysis and reports (8D’ methodology), from customer complains.- Ishikawa diagram, SCARs, 5 Why's, empowerment, teamwork, leadership etc.- Main technical support for customer requirements.- Quotation of new products and Engineering Changes.- In charge of translate customer requirements, into BOM´s, work instructions, and travelers.- Transfer plan developments for new products.- Follow up of Engineering Changes.
-
-
-
-
Senior Production Supervisor
-
Oct 2006 - Sep 2008
Managing different departments involves in the mixed, press and enamel lines. In charge of 30 enamel operators, one mixed supervisor, four mechanical and 4 electronic technician, two press machine technicians, five quality inspectors and one quality supervisor. Control and follow up of chemical mixed, production lines and maintenance of all the equipment involved in the process. Making and/or modifying work instructions, flow charts and process sheets New tools implementation, engineering changes, cycle times, process capacity analysis, work load balancing. New products development, designed and standardized the production process. Daily activities of quality control, workshops, 5’s methodology. Improvement of process flow, internal audits and direct management contact for results. Control and monitoring of direct suppliers, raw material control and audits to direct suppliers. Customer direct dealing for complaints and forecast demand.
-
-
-
Grupo Bafar
-
Mexico
-
Food Production
-
700 & Above Employee
-
Production supervisor
-
Jun 2004 - Jul 2006
Supervising the complete selection and packaging department on third shift. 50 people on the area. Implementation of manufacturing specifications, Flow chart, achieves the production rate, increasing the efficiency and reduction of the manpower. Contribution to achieve the ISO 9000 and 9001 for the first time in the company, standardizing the process, documentation and the quality in the product. Management of final product in packaging and shipment area Control of Inventory for raw material and final product. Bafar University counselor. Courses: 5’s, lean manufacturing, supervisor of excellence,
-
-
Education
-
Instituto Tecnologico de Chihuahua II
Industrial Engineering, Manufacturing Engineering
Community
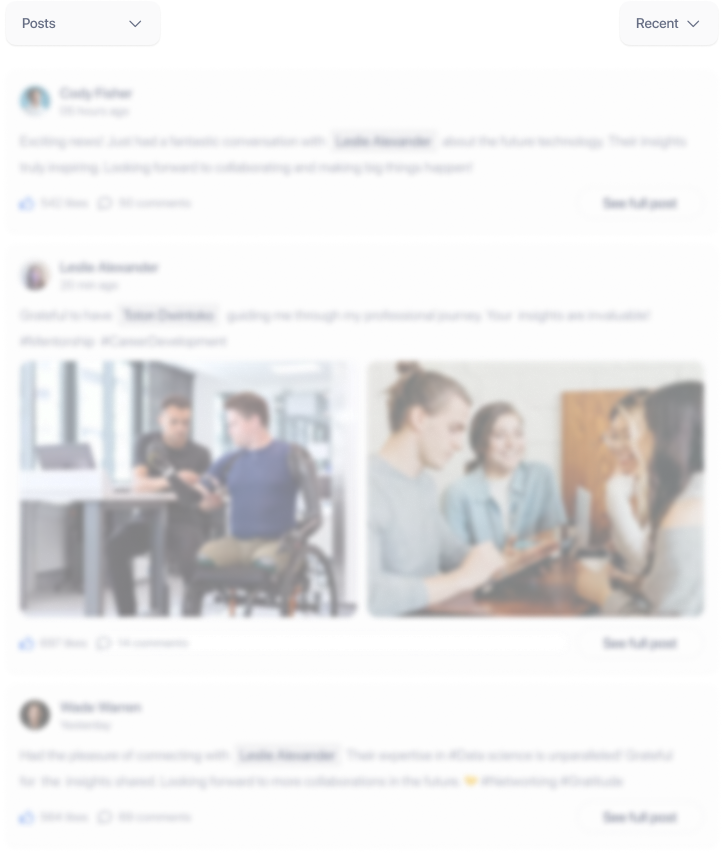