Marcelo Marsal
Project Manager at Rede D'Or- Claim this Profile
Click to upgrade to our gold package
for the full feature experience.
-
Português Native or bilingual proficiency
-
Inglês Full professional proficiency
Topline Score
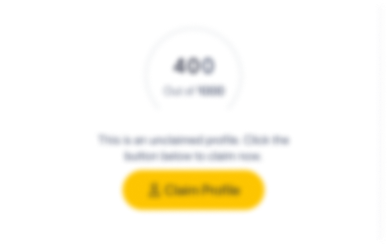
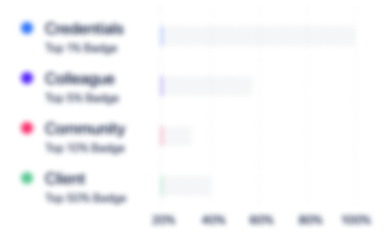
Bio

Renato Lopes Garrido
Ótimo profissional, com uma visão macro do negócio e buscando sempre atingir às necessidades do cliente e da companhia, exercendo um papel de líder que apoiava sua equipe e nos orientava para apresentarmos os melhores resultados. Obrigado Marcelo, pelos ensinamentos!

Luiz Mayer Rodrigues
O Marcelo é um professional muito competente, focado na resolução de conflitos e cumprimento de metas. Tem um bom humor e companheirismo contagiante, o que facilita muito as pressões diárias do trabalho. Com certeza é um professional competente para qualquer atividade que venha a fazer.

Renato Lopes Garrido
Ótimo profissional, com uma visão macro do negócio e buscando sempre atingir às necessidades do cliente e da companhia, exercendo um papel de líder que apoiava sua equipe e nos orientava para apresentarmos os melhores resultados. Obrigado Marcelo, pelos ensinamentos!

Luiz Mayer Rodrigues
O Marcelo é um professional muito competente, focado na resolução de conflitos e cumprimento de metas. Tem um bom humor e companheirismo contagiante, o que facilita muito as pressões diárias do trabalho. Com certeza é um professional competente para qualquer atividade que venha a fazer.

Renato Lopes Garrido
Ótimo profissional, com uma visão macro do negócio e buscando sempre atingir às necessidades do cliente e da companhia, exercendo um papel de líder que apoiava sua equipe e nos orientava para apresentarmos os melhores resultados. Obrigado Marcelo, pelos ensinamentos!

Luiz Mayer Rodrigues
O Marcelo é um professional muito competente, focado na resolução de conflitos e cumprimento de metas. Tem um bom humor e companheirismo contagiante, o que facilita muito as pressões diárias do trabalho. Com certeza é um professional competente para qualquer atividade que venha a fazer.

Renato Lopes Garrido
Ótimo profissional, com uma visão macro do negócio e buscando sempre atingir às necessidades do cliente e da companhia, exercendo um papel de líder que apoiava sua equipe e nos orientava para apresentarmos os melhores resultados. Obrigado Marcelo, pelos ensinamentos!

Luiz Mayer Rodrigues
O Marcelo é um professional muito competente, focado na resolução de conflitos e cumprimento de metas. Tem um bom humor e companheirismo contagiante, o que facilita muito as pressões diárias do trabalho. Com certeza é um professional competente para qualquer atividade que venha a fazer.

Credentials
-
Scrum Foundation Professional Certificate (SFPC)
CertiProf®Jan, 2019- Oct, 2024 -
Black Belt
Consumer Driven 6-SigmaJan, 2016- Oct, 2024 -
Green Belt
Consumer Driven 6-SigmaJan, 2014- Oct, 2024
Experience
-
Rede D'Or
-
Hospitals and Health Care
-
100 - 200 Employee
-
Project Manager
-
Aug 2022 - Present
-
-
-
Myra
-
Netherlands
-
Graphic Design
-
1 - 100 Employee
-
Project & Process Manager
-
Jan 2021 - Aug 2022
▪ Responsible for managing projects, monitoring the progress during all stages and acting as a focal point of contact for the client and internal areas. ▪ Coordinate the communication among other internal areas of the company, aiming at objectives achievement; ▪ Responsible for the implementation of Quality Operations (segments: Banking, Educational, Telecommunications, Technology, Transport and Retail.); ▪ Preparation of kick off presentations with the support areas, as well as project follow-up meetings with the board of directors; ▪ Systemic improvement and development Scrum Master, automation and development of new product features; ▪ Coordination of the new site implementation (approximately 3000 employees at the new location); ▪ Responsible for structuring and optimizing the processes, procedures, tools and discipline's manuals; ▪ Head of the Corporate Performance team leading actions with automations and solutions that bring significant gains to the business. Recognition Program 2021 – Myra Surpreende Show less
-
-
-
Randstad Brasil
-
Brazil
-
Human Resources Services
-
700 & Above Employee
-
Process Manager
-
Jun 2019 - Jan 2021
▪ Responsible for process standardization and continuous improvement of Inhouse Services solution customers, focusing on cost reduction (segments: automotive, food, pharmaceutical, cosmetic, logistics, health, etc.); ▪ Acting in the sales strategy of the business solution, presenting the concept and market differentials for the leadership of the potential customer; ▪ Mapping of critical points in new customers, to define a customized service model and subsequent follow-up; ▪ Implementation of new projects, being responsible for the delivery schedule, activities checklist, customer alignment meetings, manual of standardized processes and management of the implementation team; ▪ Commercial relationship with current customers, for fidelization and identification of new business opportunities; ▪ Definition and monitoring of KPI's, as well as an action plan when necessary; ▪ Periodic presentations and reports to headquarters located in the Netherlands. Show less
-
-
-
Ford Motor Company
-
United States
-
Motor Vehicle Manufacturing
-
700 & Above Employee
-
Project Coordinator
-
Oct 2017 - May 2019
• Coordinate all involved Areas (Engineering; Manufacturing; Material Planning and Logistics; Purchasing; Supplier Technical Assistance; Quality; and Plant) for the implementation of New Products Programs according to Ford metrics;• Assure that the Program Timing, Costs and Quality objectives are achieved;• Assure that all Equipment, Facilities & Tooling are available for the Build Phases;• Material Management in order to guarantee parts availability on time with required quality and resist for potential retrofits unless function or product safety is at risk;• Standardized process best practices and review them at each milestone;• Coordinate, record and maintain all Build Issues resolution;• Provide team feedback and continuous Launching improvement. Show less
-
-
Business and Strategic Planning Engineer
-
Sep 2015 - Oct 2017
Planning of future South America vehicle models including the timing development from the prototypes phases until the vehicle launches, including the quantity of pilot units and new models production acceleration curve, taking in consideration each plant patterns, cultures and others constrains.Develop the total cost of the new model launches considering staffing, quality actions, evaluation drives, tryout materials, travels, scraps and current model losses costs while identifying saving opportunities to achieve the company targets. Planning the new models training for the plant operators based on the vehicles new contents and working with the training suppliers to refine implement the training. Show less
-
-
Project Coordinator
-
Oct 2012 - Sep 2015
• Coordinate all involved Areas (Engineering; Manufacturing; Material Planning and Logistics; Purchasing; Supplier Technical Assistance; Quality; and Plant) for the implementation of New Products Programs according to Ford metrics;• Assure that the Program Timing, Costs and Quality objectives are achieved;• Assure that all Equipment, Facilities & Tooling are available for the Build Phases;• Material Management in order to guarantee parts availability on time with required quality and resist for potential retrofits unless function or product safety is at risk;• Standardized process best practices and review them at each milestone;• Coordinate, record and maintain all Build Issues resolution;• Provide team feedback and continuous Launching improvement. Show less
-
-
Project Engineer
-
Jul 2010 - Oct 2012
• Coordinate all involved Areas (Engineering; Manufacturing; Material Planning and Logistics; Purchasing; Supplier Technical Assistance; Quality; and Plant) for the implementation of New Products Programs according to Ford metrics;• Assure that the Program Timing, Costs and Quality objectives are achieved;• Assure that all Equipment, Facilities & Tooling are available for the Build Phases;• Material Management in order to guarantee parts availability on time with required quality and resist for potential retrofits unless function or product safety is at risk;• Standardized process best practices and review them at each milestone;• Coordinate, record and maintain all Build Issues resolution;• Provide team feedback and continuous Launching improvement. Show less
-
-
-
Volkswagen do Brasil
-
Brazil
-
Motor Vehicle Manufacturing
-
700 & Above Employee
-
Mechanical Engineering Trainee
-
Mar 2008 - Dec 2009
• Coordinating prevention and implementation of tools to decrease issues field; • Elaborating issues indicators; • Intern process planning; • Coordinating publications of Product Technical information; • Potential product failure analyzing; • Coordinating prevention and implementation of tools to decrease issues field; • Elaborating issues indicators; • Intern process planning; • Coordinating publications of Product Technical information; • Potential product failure analyzing;
-
-
Education
-
Fundação Getulio Vargas
Master of Business Administration on Engineering Project Management, Process & Project Management -
Centro Universitário da FEI
Mechanical Engineering with emphasis on automotive, Engenharia Mecânica
Community
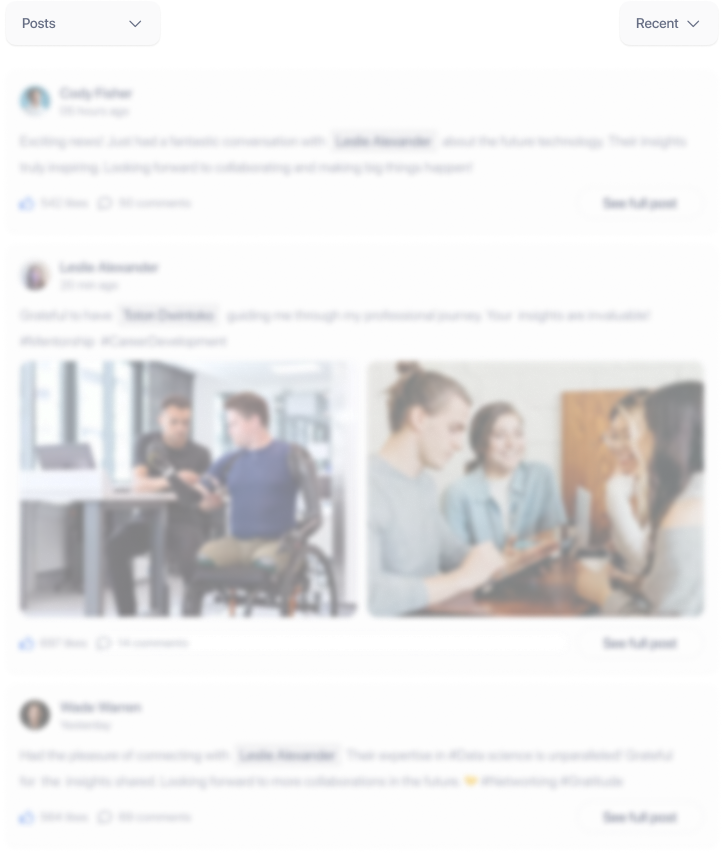