Marc Rottink
Senior Vice President Global Supply Chain at Smith+Nephew- Claim this Profile
Click to upgrade to our gold package
for the full feature experience.
-
German -
-
English -
-
Dutch -
Topline Score
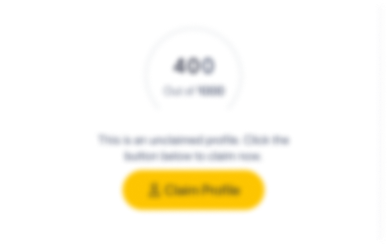
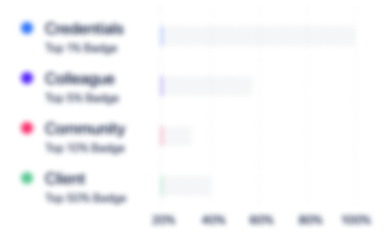
Bio
0
/5.0 / Based on 0 ratingsFilter reviews by:
Experience
-
Smith+Nephew
-
United Kingdom
-
Medical Equipment Manufacturing
-
700 & Above Employee
-
Senior Vice President Global Supply Chain
-
Apr 2022 - Present
-
-
-
Medtronic
-
United States
-
Medical Equipment Manufacturing
-
700 & Above Employee
-
VP of Operations Cranial Spine Technologies
-
Mar 2021 - Apr 2022
- Responsible for Operations and Supply Chain for Cranial and Spine technology product portfolio- Main focus areas are product development, sourcing, manufacturing process design and delivery, Supply Chain Management (Integrated Business Planning) & inventory Management - Key portfolio dimensions: ~$5B revenue, 45K SKU's, ~20 product launches annually, $700M inventory and $600M of capital assets- Key challenges and deliverables in the role are increasing our speed of innovation (product launch cycle time, optimizing our asset and inventory burden through technology, develop and implement next generation product delivery offerings to differentiate Medtronic in the market place
-
-
VP Supply Chain RTG
-
Apr 2017 - Feb 2021
- Heading up Global Supply Chain for Neuro Science portfolio- Total turnover value through Supply Chain is approx. 8.3B$- Total directly managed inventory responsibility is 1B$, 85K SKU’s and managing $900M of assets (surgery instruments)- Span of control: approx. 160 employees split over 5 locations- End to end Supply Chain responsible: IBP, Contract Manufacturing Supplier management, Master Scheduling and planning, field warehousing & Distribution, final mile & network planning- Key challenges in role: Optimizing inventory (~$250M) and ~$80M of assets in 5 years through transformational programs (Implemented Order to Cash in US), SKU’s rationalization, standardizing field inventory tools and management processes, standardized master production scheduling and production planning in 19 RTG Medtronic Manufacturing sites, Transforming S&OP to IBP, leading program with Sales and Marketing to drive to “one number”
-
-
-
Xerox
-
United States
-
Business Consulting and Services
-
700 & Above Employee
-
Vice President Technology Supply Chain
-
Sep 2014 - Apr 2017
- Heading up Supply Chain in North America & Latin America- Total turnover value through Supply Chain is approx. 4.5B$- Total annual Supply Chain spend is approx. 295M$- Total Managed inventory value is approx. 350M$- Span of control: approx. 1000 employees split over 8 locations within the US- End to end Supply Chain responsible: S&OP, vendor management and planning, inbound supply chain, central warehousing, order desk, field warehousing (including service logistics), end customer delivery & Reverse Supply Chain- Key deliverables and challenges in the role: o Transform the Supply chain and define differentiated solutions that are tailored to the way Xerox goes to Market o Reduce the Supply Chain cost base and its efficiency (by means of partnering, right-shoring and by offering level of service options that fit the gross margins that our Xerox GTM channels can afford) o Set up and drive asset utilisation programs that maximise Xerox return on assets (2nd life equipment, re-use for Service parts, etc) o Develop and roll out cultural and skill change programs for Xerox supply chain employees for development towards the skills and behaviours needed to serve our business
-
-
Vice President Manufacturing & Supply Chain
-
Feb 2013 - Aug 2014
- End responsible (Algemeen Directeur) for Manufacturing & Supply Chain in Europe, MEA, Russia and India, reporting to President Xerox Europe- Total turnover is approx. 2.3B$- Total annual Supply Chain spend is approx. 279M$- Total Managed inventory value is approx. 300M$- Resp. for approx. 1000 employees split over 3 locations: Venray (Netherlands), Dundalk (Ireland) and Uxbridge (UK)- End to end Supply Chain responsible: S&OP, warehousing, order desk, in-country warehousing, end customer delivery, reverse Supply Chain- Manufacturing is mainly focussed on toner and packaging of toner, Supply Chain function is end to end and are for both product as well as Service Logistics (spare parts and toner to end users)- Main accountabilities and challenges in the role: o Transform the Supply chain into differentiated solutions that are priced in a differentiated way o Reduce the Supply Chain cost base with 20% in 3 years (by outsourcing, offshoring to Far East & implementing differentiated solutions that are affordable) o Migrate traditional toner manufacturing to adaptive toner manufacturing including postponement production strategies o Set up of a Pan-European Reverse Supply Chain to ensure asset maximisation for off lease equipment (2nd life, asset strip, etc)
-
-
Manager Corporate Procurement Third Party Equipment
-
Nov 2011 - Mar 2013
- Leading a team of procurement Managers focussed on the procurement of OEM products (mainly printers, Multi function devices & finishing equipment) that Xerox buys from Third Party Vendors across the globe- Total procurement spend value is $200M- Leading cross functional & organisational projects/ initiatives that support improvement of Supply Chain performance (VMI, Supplier compliance management & Supply Chain cost down projects)- Leading Xerox's challenge in Europe to get our Supplier base on Global contracts: Today each European country has separate contracts with same suppliers. This leads to sub-optimisation
-
-
Manager Equipment Supply Chain (Eastern Hemsiphere)
-
Sep 2006 - Nov 2011
Leading a Supply Chain operation for Office equipment & supplies in Europe, MEA & CEE (mainly related to supply chain management activities such as order management, inventory management, service & supplies management)Responsible for negotiating sales forecasts with marketing & sales (S&OP process), purchasing of equipment (mostly via OEM suppliers), Order management & fulfilment, Inventory management, service & returns)Managing LSP’s on warehousing, light manufacturing, order fulfilment & outbound logisticsLeading & participating in productivity & value chain projects like Vendor Managed Inventory, Direct ship to developing markets, Global alignment of the Xerox corporate Supply chain and shortening our cash to cash cycle Annual turn over going through is approximately $1.2BAccountable for an operational spend/ budget of $25MInventory value is approximately $40M (12 turns yearly)
-
-
Manager S&OP Equipment
-
Apr 2004 - Aug 2006
Responsible for the demand forecasting process for copying-& printing equipment, for Europe, MEAand CEEMaintain relationships & agree demand outlooks with marketing & sales operations within Xerox that meet service level and revenue requirements and at the same time optimises the amount of cash invested in inventory holding (balance between cost and service level) Responsible for the inventory holding of purchased equipment and manage the inventory towards optimum levelsManaged Transition process whereby I moved the entire S&OP department from the west to the East of the UK
-
-
Operations Manager Spare parts Logistics Centre
-
May 1999 - Mar 2004
Leading a two shift spares parts warehouse operation of 150 people and a returns channel operation of 50 peopleResponsible for the pick, pack, distribution & returns process of spare Parts within Europe, CEE & MEAResponsible for the return operation, handling the field returns of used machines and consumablesLead and participated in (productivity) projects and IT system change projects that affected operationLiase with internal customers within the European Xerox service officesOperational LSP management on outbound truncking and outsourced pre-pack and storage activities
-
-
-
DHL
-
Germany
-
Transportation, Logistics, Supply Chain and Storage
-
700 & Above Employee
-
Human Resources Manager
-
May 1996 - Apr 1999
- Development en implementation of de-central Human Resources policy like people development, training, recruitment, Management development, absence policy - Reorganising Van Gend & Loos Eindhoven, where 80 jobs were made redundant - Development en implementation of de-central Human Resources policy like people development, training, recruitment, Management development, absence policy - Reorganising Van Gend & Loos Eindhoven, where 80 jobs were made redundant
-
-
Education
-
HU University of Applied Sciences Utrecht (Hogeschool Utrecht)
Business, Logistics & Business administration -
VLM/ NIVE
Supply Chain Management, Logistics & Supply Chain -
Hogeschool van Arnhem en Nijmegen (HAN)
BA, Human Resources Management
Community
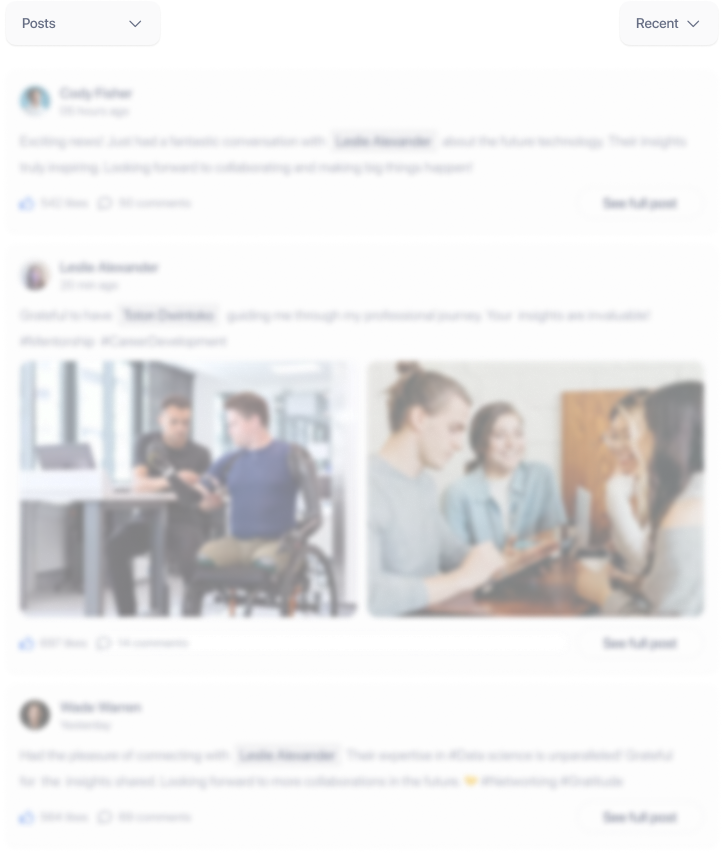