José M Hernández
Supplier Quality Sr Manager at Keurig Dr Pepper Inc.- Claim this Profile
Click to upgrade to our gold package
for the full feature experience.
-
English Professional working proficiency
-
Spanish Native or bilingual proficiency
Topline Score
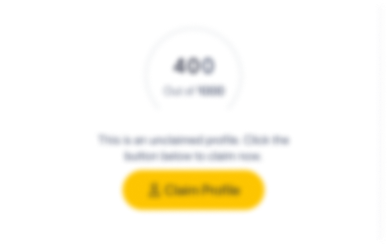
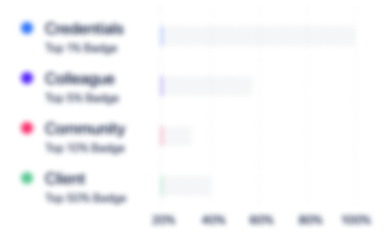
Bio

Ivan Jileta
I know Manuel for the last +15 years. He is an extraordinary quality leader, making an impact in each organization or program that he is involved. Manuel’s empathy to his team members and customers, in addition to his technical knowledge; making him a unique positive force.

Gregory Menn
Manuel is an effective, results-oriented professional, with proactive approach to developing and implementing effective quality procedures and methods. He has a strong background in manufacturing processes, Quality systems, ISO standards, and NPD and AQP tools. Detail oriented, hands on engineer with a strong analytical, statistical, and problem solving background. Team player with high ethical and professional standards. Highly recommended.

Ivan Jileta
I know Manuel for the last +15 years. He is an extraordinary quality leader, making an impact in each organization or program that he is involved. Manuel’s empathy to his team members and customers, in addition to his technical knowledge; making him a unique positive force.

Gregory Menn
Manuel is an effective, results-oriented professional, with proactive approach to developing and implementing effective quality procedures and methods. He has a strong background in manufacturing processes, Quality systems, ISO standards, and NPD and AQP tools. Detail oriented, hands on engineer with a strong analytical, statistical, and problem solving background. Team player with high ethical and professional standards. Highly recommended.

Ivan Jileta
I know Manuel for the last +15 years. He is an extraordinary quality leader, making an impact in each organization or program that he is involved. Manuel’s empathy to his team members and customers, in addition to his technical knowledge; making him a unique positive force.

Gregory Menn
Manuel is an effective, results-oriented professional, with proactive approach to developing and implementing effective quality procedures and methods. He has a strong background in manufacturing processes, Quality systems, ISO standards, and NPD and AQP tools. Detail oriented, hands on engineer with a strong analytical, statistical, and problem solving background. Team player with high ethical and professional standards. Highly recommended.

Ivan Jileta
I know Manuel for the last +15 years. He is an extraordinary quality leader, making an impact in each organization or program that he is involved. Manuel’s empathy to his team members and customers, in addition to his technical knowledge; making him a unique positive force.

Gregory Menn
Manuel is an effective, results-oriented professional, with proactive approach to developing and implementing effective quality procedures and methods. He has a strong background in manufacturing processes, Quality systems, ISO standards, and NPD and AQP tools. Detail oriented, hands on engineer with a strong analytical, statistical, and problem solving background. Team player with high ethical and professional standards. Highly recommended.
0
/5.0 / Based on 0 ratingsFilter reviews by:
Experience
-
Keurig Dr Pepper Inc.
-
United States
-
Food and Beverage Services
-
700 & Above Employee
-
Supplier Quality Sr Manager
-
Aug 2022 - Present
-
-
-
Flex
-
Paraguay
-
Advertising Services
-
Quality Manager
-
Jan 2021 - Jul 2022
Assess trends and publish departmental metrics in compliance with KPI’s. Maintaining Quality systems continuous improvement programs status tracked and reported in monthly basis. Quality team follow up to achieve established goals and objectives related to implementing, sustaining and improvement of effective and efficient Quality systems and Customers KPI’s. Ensure compliance to product requirements, international and external regulatory requirements, and guidelines. Oversee quality staff in quality management principles and procedures training. Coach the team in determine root cause (8D process) of quality problems and implement effective and timely resolutions. Deployment and execution of supplier performance product quality in alignment with business initiatives and priorities. Oversee development of supplier evaluation and selection process, and Production Part Approval Process (PPAP). Ensure procedures, systems, and processes effectively meet quality (Customers) requirements and business needs for product manufacturing. Company representative for customer audits and host management review meetings. Oversee internal audits. Show less
-
-
-
Interplex
-
Singapore
-
Appliances, Electrical, and Electronics Manufacturing
-
700 & Above Employee
-
Quality Manager
-
Nov 2019 - Jul 2020
Implementation of the ISO9001, IATF 16949 and ISO14001 systems. Serve as management representative for QMS. Identify opportunities to improve processes, and perform customer and regulator external audits. Implement, report and improve quality of KPI’s, including internal/external corrective actions, 8D’s, internal/external PPM, scrap, supplier quality and CoPQ. Ensure customer satisfaction, and product and process quality. Supervise calibration process, Quality Engineering department, Metrology and Document Control. Provide support for new product introduction activities, and facilitate communication between Quality and other departments. Show less
-
-
America's Regional Quality Manager
-
Mar 2019 - Nov 2019
Management support for ISO 9001, IATF 16949, VDA 6.3, ISO13485 and ISO14001 systems. COPQ improvement plan support. Improve Customer perception. Improvement plans support towards zero escapes.
-
-
Quality Manager
-
Jun 2015 - Mar 2019
Serve as management representative for ISO9001, IATF 16949, ISO 13485 and ISO14001 systems. Identify opportunities to improve processes, and perform customer and regulator external audits. Implement, report and improve quality of KPI’s, including internal/external corrective actions, 8D’s, internal/external PPM, scrap, supplier quality and CoPQ. Ensure customer satisfaction, and product and process quality. Supervise calibration process, Quality Engineering department, Metrology and Document Control. Provide support for new product introduction activities, and facilitate communication between Quality and other departments.Achievements Increased customer satisfaction levels by reaching 0 customer incidents with one of the largest automotive customers. Show less
-
-
Quality Manager
-
Jul 2011 - May 2015
Executed customer and regulatory external audits. Managed ISO 9001, ISO TS 16949, ISO 13485 and ISO 14001 systems. Monitored, followed up and identified opportunities to improve various KPIs. Successfully reduced customer complaints by increasing quality control measures. Oversaw product and process quality, calibrations, quality engineering and document control. Collaborated with Materials team to improve purchasing process and selection suppliers
-
-
-
VOIT Automotive GmbH
-
Germany
-
Motor Vehicle Manufacturing
-
1 - 100 Employee
-
Senior Quality Engineer, Oct 2010 – July 2011
-
Oct 2010 - Jul 2011
Handled all customer satisfaction issues throughout the company, including Continental, Brose and TRW. Complied with all quality indicators, corrective actions, 8D’s, PPAP’s and AMEF. Produced reports regarding quality activities and processes. Directed development of improvement plans for business objectives with management teams. Identified cost reduction opportunities using Lean Manufacturing and Lean Six Sigma strategies. Utilized statistical tools, such as SPC, ANOVA and DOE, to analyze data. Show less
-
-
-
-
Senior Engineer/Lead Auditor for Quality Systems, Acting Quality Manager,
-
Sep 2003 - Oct 2010
Filled in for Quality Manager in his absence. Oversaw one supervisor, four technicians and 16 quality auditors. Coordinated with team to complete product and process audits. Evaluated, selected, approved and developed vendors. Served as lead auditor for the Quality, Environmental, Health and Systems. Directed and organized internal audit programs.
-
-
Painting Process Coordinator/Acting Supervisor
-
Jul 2001 - Sep 2003
Controlled production resources and coordinated service areas in the painting plant. Managed al process and quality engineering activities. Analyzed and developed solutions to reduce production variances. Consistently met all production programs and financial indicators.
-
-
Senior Quality Engineer
-
Aug 1995 - Jul 2001
Developed quality plans and visual aids. Employed SPC, AMEF and ANOVA statistical tools. Designed experiments and performed process capability analyses. Coordinated response and follow up for corrective actions. Managed the quality system for the paint process to ensure compliance with established standards. Participated in projects involving injection molding, sub-assemblies and paint.
-
-
Education
-
Universidad de Guadalajara
Master of Business Administration (MBA), Business Administration and Management, General -
Centro de Enseñanza Técnica Industrial
Bachelor's degree, Industrial Engineer with minor in Instrumentation and Process Control -
Universidad Tecmilenio
Master Business Administration and Finance, Finance and Financial Management Services
Community
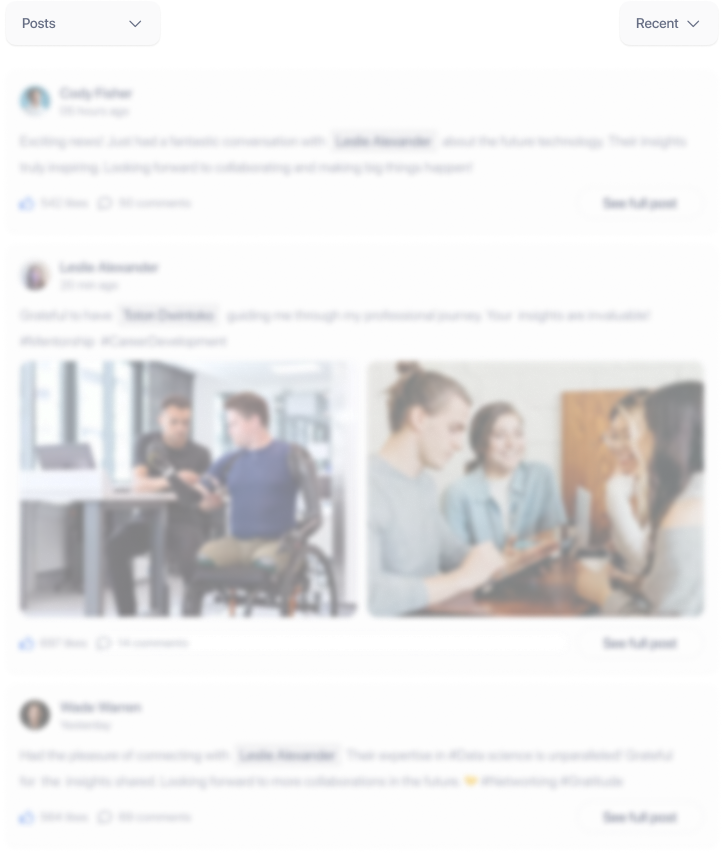